Flow control is an integral part of all industries, such as in chemical plants, power stations, food factories, dyeing and finishing plants, or other factories, flow control is an essential part of process control. Flow controls meanings to control of the flow rate of the medium in an adjustable range according to the process requirements. For example, flow control may be utilized in the chemical industry to manage the flow of liquids between tanks or reactors during the manufacturing process. In an oil and gas plant, flow control may be used to control the flow of fluids through pipelines or to measure the amount of oil or gas being extracted.
Usually, this function is required flow control valves, which regulate the capacity of the fluid or gas in the pipeline and ensure smooth and safe operation. In this article, we will explore the different types of flow control valves, their applications, and the common problems associated with their use.
Introduction of Flow Control Valve
Flow control valves play a key role in regulating the flow of fluids and gases through pipelines, and if you walk into a plant, you can find flow control valves everywhere in the equipment, and they ensure that processes run efficiently and safely. Flow control valves can be found in a variety of industries such as textile mills, water treatment plants, chemical plants, refineries, and power plants. These valves offer several benefits, including improved process efficiency, precise control, reduced energy consumption, and enhanced safety measures.
Types of Flow Controls
1. Globe Valves
Globe valves are used for regulating fluid flow and can be found in various configurations, such as on/off globe control valves, single-seated globe control valves, double-seated control globe valves, 3-way globe control valves, and y-type globe valves.
2. Ball Valves
Ball valves offer excellent shut-off capabilities and are commonly used in applications where tight sealing is required.
3. Butterfly Valves
Butterfly valves are designed for controlling the flow of fluids in pipelines and are known for their compact design and ease of operation.
4. Check Valves
Check valves prevent fluid flow in the reverse direction, ensuring that processes run smoothly and efficiently.
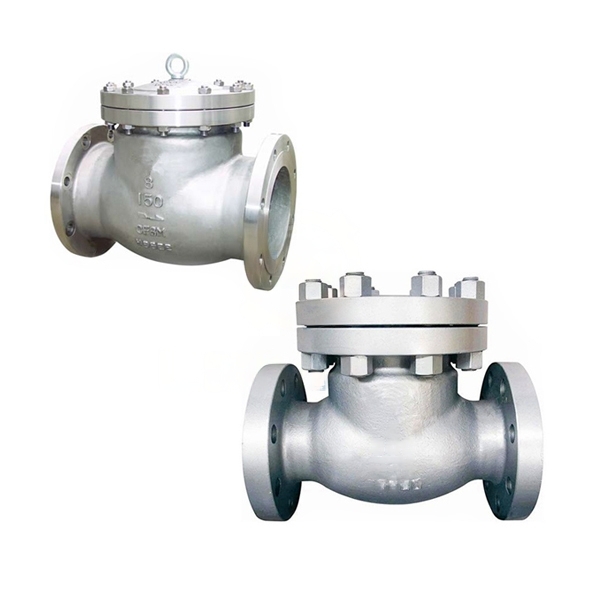
5. Automatic Recirculation Valves (ARVs)
ARVs protect pumps from damage by maintaining a minimum flow rate even when the demand for fluid decreases.
6. Diaphragm Valves
Diaphragm valves use a flexible diaphragm to control fluid flow, making them suitable for use in sanitary applications or with abrasive and corrosive materials.
7. Pinch Valves
Pinch valves are designed to control the flow of fluids or gases in pipelines by pinching a flexible tube or sleeve. They are often used in industries such as wastewater treatment, mining, and food processing.
8. Pressure Reducing Valves
Pressure reducing valves regulate the pressure of a fluid or gas by reducing it to a specific set point.
9. Control Valves with Actuators
Valves such as pneumatic angle type control valves and electric temperature control valves are equipped with actuators to enable remote or automated control of fluid flow.
Flow Controls Applications
Flow control valves are used in various industries and applications, including:
- Water Treatment: Valves like hydraulic check valves and flow control valves are essential in wastewater treatment processes to ensure proper flow regulation and prevent contamination.
- Power Plants: In power plants, high-pressure control valves and steam pressure reducing valves help maintain safe and efficient operations by controlling the flow of steam and other fluids.
- Oil and Gas: Flow control valves, such as gas pressure regulating valves and natural gas pressure regulators, are crucial for managing the flow of oil and gas through pipelines and ensuring safe transportation.
- Chemical Processing: In chemical processing plants, valves like non-slam check valves, globe valves, butterfly valves, and arc valves are used to control the flow of corrosive and hazardous chemicals, ensuring safety and process efficiency.
- Food and Beverage: The food and beverage industry relies on valves such as diaphragm valves and pinch valves for sanitary flow control during processing and packaging operations.
Common Questions For Flow Controls
1. How do I select the right flow control valve for my application?
To select the right flow control valve for your applications, we need to consider many processing parameters, which include type of fluid or gas, operation temperature, operation pressure, desired flow rate, pressure drop, or differential pressure, control method, mode of operation and the desired level of control accuracy. Correct sizing not only reduces unnecessary downtime for maintenance for the end user, but also greatly accelerates productivity and accuracy. You can ask for a free consultation with THINKTANK to ensure the right selection.
2. What are the differences between manual and automated flow control valves?
Manual flow control valves require manual adjustment to regulate fluid flow, while automatic valves require the use of actuators such as pneumatic or electric to control fluid flow, via remote signals, or to adjust the valve position according to specific control parameters. You can find these different valves in the following pictures.
Automatic valves are suitable for applications that require precise control, remote operation, or integration with control systems. In modern industry, automatic valves are being used more and more widely in production processes, not only to improve the efficiency of production, precise control, and greater energy savings.
3. How do I maintain flow control valves?
Proper routine maintenance job of flow control valves includes periodic inspections for shell leaks, inner leaks, seals, signals, correct actuator action, and routine valve cleaning and lubrication. In addition, we should replace worn or damaged parts as needed to ensure optimum performance and extend the life of the flow control valve. The end-users need to follow the manufacturer’s guidelines and recommended maintenance schedule, which is essential to maintain valve efficiency and prevent unexpected failures. If you don’t have the manual book or maintenance book in hand, you can contact the equipment factory to ask them to send it again. Every single valve from THINKTANK will have a 100% test and inspection before shipment, ensuring the reliable quality of flow control valves. You can surely no worries about the quality and service.
4. How do flow control valves affect energy efficiency?
Flow control valves provide precise control of the flow of fluid or gas in a system. The change of flow or pressure after the valve is controlled by the flow area of the valve core through which the fluid or gas passes. Flow control valves can improve industrial energy efficiency mainly through three aspects.
One is to reduce unnecessary energy consumption due to system pressure drop.
We know that when fluid or gas passes through a pipeline or system without a flow control valve, the flow will pass elbows to change direction in the pipeline, or generate friction with the pipeline wall and other reasons, so it will cause a pressure drop in the entire system, because the loss of fluid energy. The pressure drop not only causes energy loss but also wasted a lot of energy and power.
Flow control valves can help reduce pressure drops by regulating the flow capacity, and make sure fluid or gas passes through the system at a consistent pressure. By maintaining a certain pressure value, no need for much energy is required running the entire processing system.
The second is to improve the control of fluid or gas flow in the system.
Flow control valves can ensure that only the required amount of fluid or gas is used at any given time, precisely controlling the flow parameter value, which prevents overuse and wasted energy, resulting in significant energy savings.
Third, flow control valves can help improve energy efficiency by increasing the overall efficiency of the system.
For example, if a flow control valve works in an HVAC system, it can regulate the flow of water through heating and cooling circuits, maintaining the desired temperature and improving energy efficiency while optimizing heat transfer. It’s more and more important for end-users save costs during production efficiency. Standing for the customer position to thinking of the market is very valve manufacturer need to be consideration.
5. What is meant by flow control?
Flow control is the process of regulating the flow capacity or volume of a fluid, gas, or steam in a piping system. It involves the use of flow control valves and other devices to manage the flow of the medium to achieve the desired output. Welcome to choose THINKTANK as your reliable partner of flow control valves.
6. What is an example of flow control?
We can list 3 types of different valves to achieve flow controls.
- If using pressure reducing valve to control flow, it regulates the flow of fluid to reduce the downstream pressure range to a desired value.
- If using pneumatic globe type control valve to control flow capacity, the input signals from the controller can directly regulate the valve opening to the precision flow rate needed.
- If using flow level control valve, through the height of the liquid level ball, the opening level of the valve is mechanically controlled.
7. How does flow control system work?
Flow control systems are designed to modulate the process flow rate/capacity of fluids or gases in an industrial system. Based on different applications and types of flow control systems on-site, the operating principles may vary in design.
Generally, a standard flow control system consists of 4 key components.
- Flow Control Valve: Flow control valve is the final component to directly control the pressure or flow rate, in case to meet the desired value in the system. There are many types of flow control valves, such as ball type, butterfly type, globe type, needle type and plug type etc. These valves can be operated by pneumatic actuator, electric actuator, or handle/handwheel.
- Flow Sensors: Flow sensors are used to measure the flow of fluid or gas through a system. Usually, when the flow sensors collect the data from the processing, it will send it to the controller, and the controller will according to the value release a signal to the flow control valve, in case to maintain the desired flow rate by the valve opening or positioning.
- Controllers: Based on the above paragraph, we know the controller is responsible for receiving feedback from the flow sensor and adjusting the opening of the flow control valve as needed. Controllers can use proportional control algorithms to ensure consistent flow, even in the face of changing pressure, temperature, or flow rate, it also can immediately respond. If you need assistance with your application, please just feel free to contact us for a free consultation.
- Pipes: Pipes in the flow control systems are designed to move fluid or gas through the system, it’s very common to see them everywhere in the factory. From a source like a storage tank to the destination, such as an industrial process. There are many standards for pipes, make sure it is right for the customer required, and also pay more attention to the standards of pipe flange, and match flanges for flanges of flow control valves.
8. What is the best control of flow?
We need to based on a variety of processing parameters to design the best control of flow solution for customers. Deeply knowing the specific requirements of the system running is very important for professional valve manufacturers, like THINKTANK. It will help us to design and provide precision and control systems for the desired levels as users need.
Here we will introduce the most 4 simple control of flow type systems for your reference.
1. Proportional Control
This type of flow control adjusts the flow rate in proportion to changes in the input signal, such as 4-20mA, 0-10V, or 3-15psi signal. For example, if the input signal is 50%, the response flow rate of the control valve is just adjusted to 50% of the maximum capacity. Proportional control is often used for the high level of accuracy of control systems.
2. On/Off Control
In an on/off control system, the flow control valve is either fully open or fully closed based on the input signal. This type of control is less precise than proportional control but can be simpler and less expensive to implement.
3. PID Control
PID control is a type of proportional control that also takes into account the integral and derivative components of the input signal. The proportional component adjusts the flow rate in proportion to changes in the input signal, while the integral and derivative components help to reduce the “overshoot” and “undershoot” that can occur with proportional control. PID control can offer a good balance of precision and simplicity.
4. Flow Limiting Devices
Flow limiting devices are passive devices (such as orifices, flow nozzles, and ventures) that are designed to limit the flow rate of a fluid or gas. These devices can be effective in applications where a fixed flow rate is required and no active control is necessary.
Ultimately, the best control of flow for a particular application will depend on the unique requirements of the system and will take into account factors such as precision, accuracy, cost, and ease of use. A qualified engineer or technician can help to determine the optimal flow control solution based on these factors.
9. What are the 3 types of control flow?
The three types of control flow in computer programming are:
1. Sequential Control Flow
This type of control flow is the simplest and most straightforward. Programs with sequential control flow execute one instruction after the next, in the order that they are written. There is no branching or looping, and each instruction is executed exactly once.
2. Selection Control Flow
In selection control flow, a program chooses between two or more paths based on some condition. This is typically accomplished using if-else statements, which allow the program to execute one block of code if a condition is true, and another block of code if the condition is false. Switch statements are another example of selection control flow, allowing programs to choose between multiple options based on the value of a variable.
3. Iteration Control Flow
Iteration control flow involves repeating a block of code multiple times, either a fixed number of times or until a certain condition is met. This is typically accomplished using loops, such as while loops or for loops, that allow the program to execute a block of code multiple times with different input values.
These three types of control flow are fundamental to most programming languages, and mastering their use is essential to becoming a skilled programmer. By combining sequential, selection, and iteration control flows, programmers can create complex systems that can perform a wide range of tasks.
10. What are the two types of flow control?
The two types of flow control are open-loop and closed-loop control. Open-loop control is a non-feedback system where the output is not used to regulate the input, while closed-loop control is a feedback system where the output is used to regulate the input to maintain a desired output.
11. When should I use flow control?
Flow control should be used when it is necessary to regulate the flow rate or volume of a fluid, gas, or steam to achieve a desired output. It is commonly used in industrial processes, such as chemical and petrochemical plants, food and beverage production, and water treatment facilities. Here are 4 conditions you may consider for using flow control in programming.
- You want your program to respond differently based on certain conditions or events. For example, you might use an if statement to output a different message to the user depending on whether their input meets certain criteria.
- You want your program to execute certain values repeatedly until a certain condition is met. This is typically done using loops, which allow you to run a block of code multiple times with different input values.
- You want to handle errors or unexpected events in your program. This can be done using exception handling, which allows you to catch and handle different types of program errors, such as invalid input or data type errors.
- You want to optimize the efficiency of your code. By using flow control constructs such as loops or switch statements, you can reduce the amount of code you need to write and make your code more efficient by avoiding unnecessary computations or operations.
12. Where is flow control needed?
Flow control is needed in any application where the flow rate or volume of a fluid, gas, or steam needs to be regulated. It is used in various industries, including oil and gas, power generation, water and wastewater treatment, and food and beverage production.
13. What is flow control used to prevent?
Flow control is used to prevent a range of issues, such as overpressure, overheating, cavitation, erosion, and water hammer, which can cause damage to piping systems, valves, and other components.
14. What is the benefit of flow control?
The benefits of flow control include improved efficiency, accuracy, and reliability in controlling the flow rate or volume of a fluid, gas, or steam. It can also reduce operating costs, improve product quality, and enhance safety by preventing damage to piping systems and components.
15. What are the reasons for flow control?
The reasons for flow control vary depending on the specific application and requirements. Some common reasons include ensuring safety and reliability, improving efficiency and accuracy, meeting regulatory requirements, and enhancing product quality.