As a valve engineer, company executive, international valve brand agent, or valve purchasing manager, understanding the intricacies of valve bodies is essential for making informed decisions in your field. At Shanghai Thinktank Process Management Co., Ltd, our THINKTANK brand is dedicated to providing high-quality valve solutions for a variety of applications. In this comprehensive guide, we will delve into the critical aspects of valve bodies, exploring their types, functions, and applications, tailored specifically for industry professionals and decision-makers like you.
What are Valve Bodies
Valve bodies are the primary components of valves, responsible for regulating the flow of fluids within a pipeline. They function as the housing for internal components such as the stem, disc, and seat. Valve bodies are critical in ensuring the proper operation and sealing of a valve, thereby maintaining control over the flow, pressure, and temperature of fluids within various industrial systems.
Types of Valve Bodies
Valve bodies can be categorized into several types based on their design and the way they control fluid flow. Some of the most common types include:
Two-Way Valve Bodies
Two-way valve bodies are designed with two ports – an inlet and an outlet – for fluid to enter and exit. They are used to control the flow of fluids in a simple, direct linear way, making them suitable for various applications, including isolation and throttling.
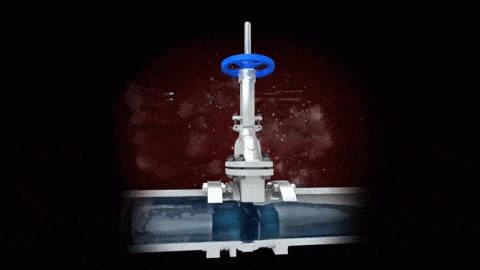
Three-Way Valve Bodies
Three-way valve bodies feature three ports that facilitate the transmission, mixing, or diverting of fluids. They are commonly used in systems that require precise control over fluid flow, such as heating, ventilation, and air conditioning (HVAC) systems.
Four-Way Valve Bodies
Four-way valve bodies have four ports that allow for more complex fluid flow control. They are often employed as plug valves or ball valves, in systems requiring the simultaneous control of multiple fluid paths, such as hydraulic systems and pneumatic systems.
Materials Used in Valve Body Construction
Valve bodies are made from a variety of materials, each with unique characteristics and suitability for specific applications. Some of the most commonly used materials include:
Cast Iron
Known for its durability and cost-effectiveness, cast iron is a popular choice for valve bodies in low-pressure applications.
Ductile Iron
This material offers improved strength and toughness compared to cast iron, making it suitable for higher-pressure applications.
Stainless Steel
With excellent corrosion resistance and high strength, stainless steel is a preferred material for valve bodies in corrosive environments or high-pressure systems.
Bronze
Bronze valve bodies are commonly used in marine applications due to their resistance to seawater corrosion.
Plastic
Lightweight and corrosion-resistant, plastic valve bodies are often utilized in applications where chemical resistance is a priority.
Applications of Valve Bodies
Valve bodies are integral components of various industrial systems, playing a vital role in controlling fluid flow. Some common applications include:
Oil and Gas Industry
Valve bodies are used to regulate the flow of crude oil, natural gas, and other fluids within refineries and pipelines.
Chemical Processing
In chemical plants, valve bodies control the flow of various chemicals and solutions through a piping system, ensuring safe and efficient processing.
Power Generation
Valve bodies are essential in power plants, where they regulate the flow of steam, water, and other fluids vital to the generation of electricity.
Water and Wastewater Treatment
In water and wastewater treatment facilities, valve bodies help regulate the flow of water and various treatment chemicals, ensuring the efficient operation of the treatment process.
HVAC Systems
Valve bodies are crucial components in heating, ventilation, and air conditioning systems, where they control the flow of air and water to maintain optimal temperature and humidity levels.
Food and Beverage Industry
In food and beverage processing plants, valve bodies and piping are used to control the flow of ingredients, cleaning solutions, and finished products, ensuring hygiene and efficiency.
Pharmaceutical Industry
Valve bodies play a vital role in the pharmaceutical industry, where they help maintain sterile environments and control the flow of chemicals and solutions during the manufacturing process.
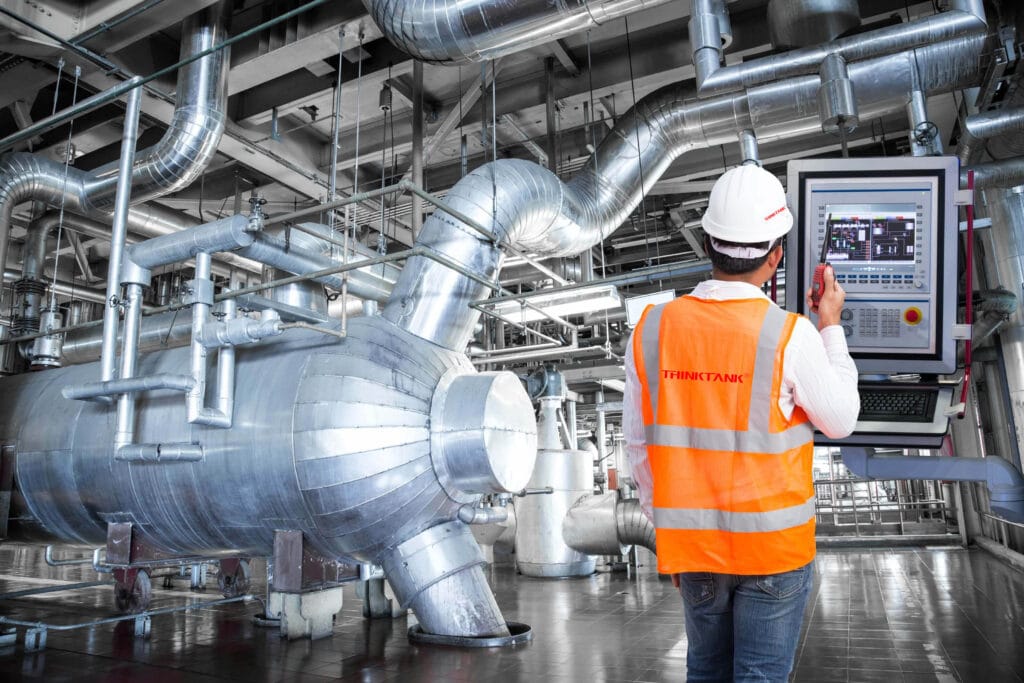
Choosing the Right Valve Body with THINKTANK
As an industry professional or decision-maker, selecting the appropriate valve body for your application involves considering several factors, such as:
1. Flow Control Requirements
Determine the type of flow control needed for your application, including isolation, throttling, mixing, or diverting.
Types of Flow Control
There are several types of flow control that can be achieved using valves:
- Isolation: Valves used for isolation purposes, like gate valves and ball valves, provide a tight shutoff to stop fluid flow in a system when needed.
- Throttling: Throttling valves, such as globe valves and control valves, regulate the flow of fluid by adjusting the opening in the valve. This allows for precise control over flow rates and pressure drops.
- Mixing and Diverting: Some valves, like three-way and four-way ball valves, are designed to mix or divert fluid flow between multiple ports. These valves can control the flow of fluids in different directions, depending on the system requirements.
- Pressure Regulation: Pressure regulating valves, like pressure relief valves and pressure reducing valves, maintain a set pressure in a system by releasing excess pressure or reducing the incoming pressure to a desired level.
- Check (Non-Return): Check valves allow fluid to flow in one direction and prevent backflow, ensuring that the fluid moves through the system in the intended direction.
2. Operating Conditions
Evaluate the pressure, temperature, and flow rates the valve body will be subjected to during operation.
Temperature
The temperature of the fluid and the operating environment can significantly impact a valve’s performance and material selection. High temperatures can cause some materials to weaken or lose their elasticity, while low temperatures can make them brittle. When selecting a valve, consider the following temperature-related factors.
- Material Compatibility: Ensure that the valve body, internal components, and sealing materials can withstand the operating temperature range of your system without compromising performance or safety.
- Thermal Expansion: Account for potential thermal expansion and contraction of valve components and the pipeline, which can affect the valve’s sealing and overall performance.
- Temperature Cycling: If your system experiences frequent temperature fluctuations, choose a valve designed to withstand temperature cycling without causing premature wear or failure.
Pressure
Pressure is another crucial operating condition that influences valve selection. Valves must be capable of handling the system’s maximum pressure and potential pressure fluctuations without leakage or damage. Consider the following pressure-related factors.
- Pressure Rating: Choose a valve with a pressure rating that meets or exceeds your system’s maximum operating pressure. Pressure ratings are often designated as Class (e.g., Class 150, Class 300), or as PN (Pressure Nominal) numbers.
- Pressure Drop: Evaluate the expected pressure drop across the valve, as excessive pressure drops can negatively impact the system’s efficiency and performance.
- Pressure Surges: In systems that may experience pressure surges or fluctuations, select a valve designed to handle such conditions without compromising safety or performance.
Flow Rate
Flow rate requirements must also be considered when selecting a valve. The valve size, design, and flow characteristics can impact the overall efficiency and effectiveness of your system. Keep the following flow rate factors in mind.
- Valve Size: Select a valve size that provides the desired flow rate with minimal pressure losses. An oversized valve can lead to poor control and increased wear, while an undersized valve can cause excessive pressure losses and reduced flow capacity.
- Flow Characteristics: Evaluate the valve’s inherent and installed flow characteristics, which describe how the valve’s flow capacity changes as it opens and closes. Choose a valve with flow characteristics that suit your application’s requirements for precise flow control and system stability.
- Cavitation and Flashing: In some systems, high flow velocities and pressure drops can cause cavitation or flashing, leading to damage and reduced valve performance. Select a valve designed to minimize these effects or consider using specialized anti-cavitation or noise-reducing trims.
By carefully considering the operating conditions of temperature, pressure, and flow rate, with THINKTANK’s expert assistance, you can select the most suitable valve for your system, ensuring optimal performance, reliability, and safety.
3. Material Compatibility
Ensure the valve body material is compatible with the fluid it will handle, considering factors like corrosion resistance, chemical compatibility, and temperature resistance.
4. Size and Connection Type
Select a valve size or body that matches your pipeline size and is compatible with existing connection types. At THINKTANK, we can customize any size which customers needed.
Various valve connection types are used to join valves to pipelines or other equipment in a system. Here is a list of common valve connection types.
Flanged Connections
Flanged connections involve bolting two flanges together, with a gasket between them to create a seal. Flanges come in different sizes, pressure ratings, and face types, such as raised face, flat face, and ring-type joint.
Threaded Connections
Threaded connections use male and female threads to join valves and pipelines. These connections are common in smaller valve sizes and are typically used for low to medium pressure applications. Threaded connections can be NPT (National Pipe Thread), BSPT (British Standard Pipe Thread), or other standardized thread types.
Socket Weld Connections
Socket weld connections involve inserting the pipe into a valve’s socket and then welding them together. This connection type is generally used for small-sized valves and in high-pressure, high-temperature applications.
Butt Weld Connections
Butt weld connections join a valve and pipe by welding their beveled ends together. This type of connection is often used for larger valves and high-pressure, high-temperature applications, as it provides a strong, leak-proof seal.
Compression Fittings
Compression fittings use a ferrule or an O-ring to create a tight seal between the valve and pipe. These connections are typically used in smaller valve sizes and lower-pressure applications, such as instrumentation and gas lines.
Union Connections
Union connections allow for easy disconnection and reconnection of valves and pipes. They consist of a male and female end, which are joined using a union nut. This connection type is used in applications where frequent maintenance or replacement is necessary.
Wafer and Lug Connections
These connection types are commonly used for butterfly valves. Wafer connections are sandwiched between two flanges, while lug connections have lugs that are bolted to the flanges. Both types provide easy installation and removal of the valve from the pipeline.
These are some of the common valve connection types used in various industries and applications. The selection of the appropriate connection type depends on factors such as valve size, pressure and temperature requirements, and ease of installation and maintenance.
Maintenance and Accessibility
Consider the quality, ease of maintenance, and accessibility of the valve body within your system, as this may impact overall efficiency and longevity.
What are the different types of valves in the valve body
The term “valve body” refers to the main component or housing of a valve that contains the internal parts responsible for regulating fluid flow. However, if you are looking for information about the different types of valves that utilize valve bodies, here are some common types:
Gate Valves
These valves are designed for on/off control and are used primarily for isolation purposes. They feature a wedge-shaped disc that moves vertically to control the flow of fluid.
Globe Valves
Globe valves are used for throttling and flow regulation. They consist of a movable disc or plug that can be raised or lowered to control the fluid flow.
Ball Valves
Ball valves use a spherical ball with a hole through its center to control fluid flow. They are popular for their quick operation and tight sealing capabilities.
Butterfly Valves
These valves have a disc mounted on a rotating shaft to control fluid flow. Butterfly valves are known for their compact design and low-pressure drop.
Check Valves
Check valves that allow fluid flow in one direction and prevent backflow. They use various mechanisms like swing, lift, or tilting disc designs to achieve this functionality.
Plug Valves
Plug valves use a cylindrical or conical plug with a hole through its center to control fluid flow. They are suitable for applications requiring low-pressure drop and minimal fluid trapping.
Diaphragm Valves
These valves use a flexible diaphragm to control fluid flow. Diaphragm valves are commonly used in applications where tight sealing and purity are essential, such as in the pharmaceutical and food industries.
Needle Valve
Needle valves are designed for precise flow control in low-flow applications. They feature a long, tapered needle that can be adjusted to control the flow rate accurately.
These are some of the common types of valves that utilize valve bodies in their construction. Each valve type has unique characteristics and is suited for specific applications, flow control requirements, and operating conditions.
What is A105 body material?
A105 is a material specification for carbon steel forgings used in components like valve bodies, flanges, and fittings. This material is designated by the American Society for Testing and Materials (ASTM) under the standard ASTM A105. A105 is suitable for high-temperature and high-pressure applications due to its excellent mechanical properties.
A105 carbon steel is primarily composed of iron, with a small percentage of carbon and other alloying elements such as manganese, phosphorus, sulfur, and silicon. The carbon content in A105 provides strength and hardness, while the other elements contribute to the material’s overall toughness, ductility, and weldability.
A105 valve bodies are commonly used in the oil and gas industry, power plants, and other high-pressure, high-temperature applications. This material provides good resistance to wear and fatigue, making it a reliable choice for components subjected to demanding operating conditions.
What is WCB material for valves?
WCB is a material specification for cast carbon steel used in valve components like valve bodies, flanges, and fittings. This material is designated by the American Society for Testing and Materials (ASTM) under the standard ASTM A216 Grade WCB. WCB cast carbon steel is suitable for a variety of applications, particularly in moderate to high temperatures and pressures.
The primary constituents of WCB material are iron and carbon, with smaller amounts of alloying elements such as manganese, silicon, sulfur, and phosphorus. The combination of these elements provides WCB with a balance of strength, toughness, and ductility, making it an ideal material for valve components.
Valve bodies made from WCB material are commonly used in industries such as oil and gas, power generation, chemical processing, and water treatment. The WCB material provides good mechanical properties and resistance to wear, making it suitable for demanding environments and a wide range of operating conditions.
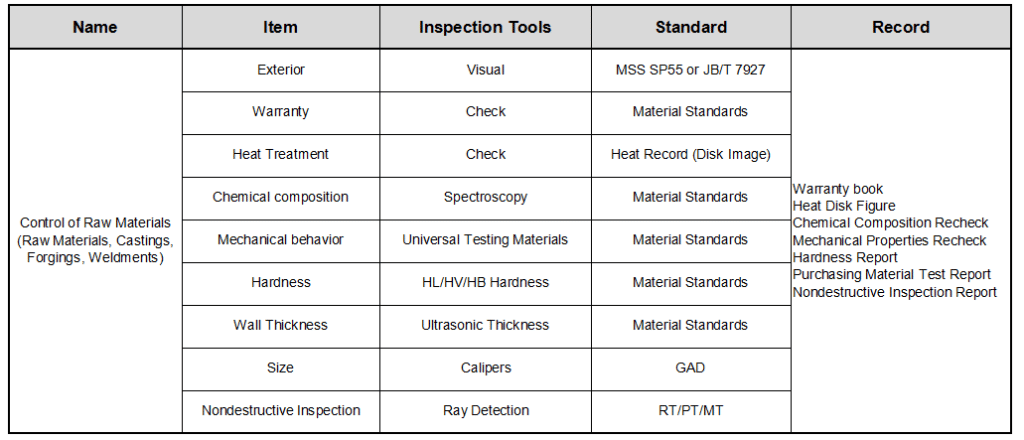
Conclusion
Valve bodies are critical components in various industrial systems, responsible for controlling the flow of fluids in pipelines and ensuring the efficient operation of numerous processes. Understanding the types, materials, and applications of valve bodies is essential for selecting the right valve body for your specific needs. By considering factors such as flow control requirements, operating conditions, material compatibility, size, and connection type, you can make an informed decision and optimize the performance of your system.
With THINKTANK’s comprehensive range of valve solutions, you can rest assured that you’re choosing quality products backed by industry expertise. For different types of control valves, please click this post.