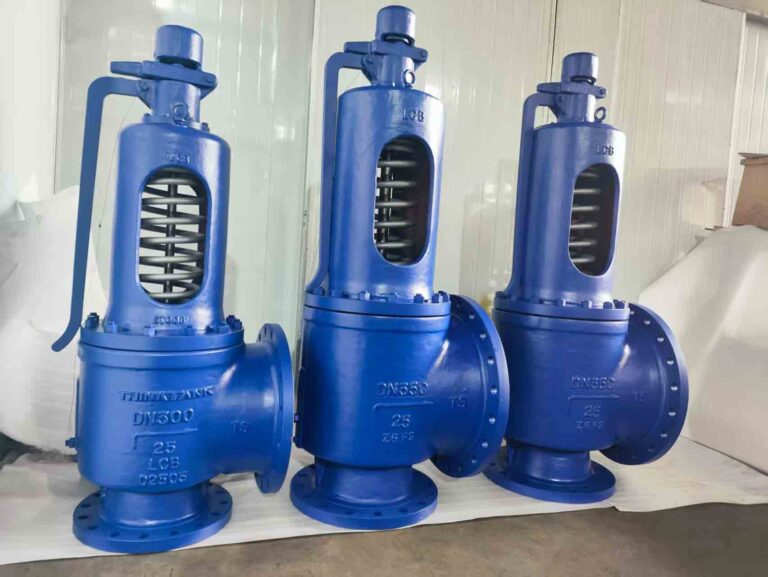
Throttle globe valves use a linear motion to move a closure into and out of the valve seat, with the valve body being a spherical chamber. They are designed to control process flow, pressure, or temperature when combined with an actuator assembly. A cage or retainer-style design is used in many single-seat bodies to hold the seat seal, provide plug guiding, and give a method for determining the flow characteristics of a specific valve. Single-seat globe valve bodies with cage or retainer structure may also easily adjust flow characteristics by changing the trim, enabling decreased capacity flow, noise reduction, or decreasing or eliminating cavitation.
The China valve industry has been rapidly expanding, offering a wide range of high-quality products for various applications. When it comes to sourcing top-grade valves, partnering with a reputable valve manufacturer in China guarantees access to cutting-edge technology and competitive pricing.
A globe valve is a type of valve used to regulate the flow of fluid in a pipeline. It works by using a movable disc or plug that can be raised or lowered within the valve body to control the flow of fluid. Here’s a step-by-step explanation of how a globe valve works:
1. The main components of a globe valve include the valve body, bonnet, stem, disc or plug, and seat ring.
2. When the valve is in the closed position, the disc or plug is seated against the seat ring, creating a tight seal that prevents the flow of fluid through the valve.
3. To open the valve, the handwheel or actuator is turned, which rotates the stem. The stem is connected to the disc or plug, so when the stem is rotated, it lifts the disc or plug away from the seat ring.
4. As the disc or plug is lifted, an opening is created between the disc and the seat ring, allowing fluid to flow through the valve.
5. The flow rate of the fluid can be regulated by adjusting the position of the disc or plug. The more the disc or plug is lifted, the larger the opening, and the greater the flow rate.
6. To close the valve, the handwheel or actuator is turned in the opposite direction, lowering the disc or plug back onto the seat ring, stopping the flow of fluid.
Globe valves provide users exceptional performance and reliability and come in a range of sizes from DN15 to DN900. They can assist in meeting a variety of application demands, from general to severe, small size to big size, hot temperature to cold temperature.
Different kinds of bonnets are offered to handle various application temperatures. To protect packing materials when the valve is used in highly hot or cold situations, this principally includes basic bonnets and optional extension bonnets.
For situations where the packing system must keep fugitive emission concentrations below environmental requirements, there are additional specific packing arrangements.
Boiler and main steam vents and drains, fuel oil systems, feedwater or chemical feed systems, turbine lubrication oil systems, and cooling water systems are just a few of the many places where globe valves are used.
Globe valves can be equipped with either balanced or unbalanced valve plugs. Balanced plugs permit equal process pressure above and below the valve plug, with the normal flow down through the seat ring. Unbalanced valve plugs are solid with no through the hole, and flow is typically upward via the seat ring.
There are various ways to guide the plug in globe valves, the most popular of which are cage guided and post-guided. Cage-guided assemblies come in both balanced and unbalanced plug configurations. This method of guiding employs the outside diameter of the plug to touch the inside diameter of the cage, which provides excellent plug stability and alignment but necessitates extremely tight tolerances between the plug and cage. The seat retainer is used in place of the retainer in the post-guided assembly. The seat retainer has a guide cage that guides the post on the plug. Because this method provides for an unobstructed flow route around the plug, the back-guided trim is better appropriate for viscous and unclean fluids.
Globe valves can be linear, equal percentage, or quick opening and can satisfy capacity demands from 0.001 Cv up to 12,000 Cv through a variety of trims with various flow characteristics.
Additionally, there are specialty trims that may be used in clean or unclean applications to stop noise and cavitation problems.
A globe valve can be opened, closed, or adjusted to the desired flow rate. Valves can be manipulated either manually or mechanically.
As an example, the petroleum sector uses globe valves because they have several benefits.
Globe valves are often used in control and isolation systems. This motion is straightforwardly linear. Since this is the case, it can quickly allow or restrict fluid flow. It makes for a secure seal. This is why globe valves are commonly utilized in the petroleum industry.
A gate valve’s closing element is a plate or disk like a “gate” that is parallel to the plane of the valve seat.
The globe valve’s closing part, known as the “plug,” travels perpendicular to the plane of the valve seat.
Globe valves have a high capacity for throttling, but gate valves are not employed for throttling. Gate valves are ideal for isolation, whereas globe valves are ideal for regulating or throttling.
Globe and gate valves are the most common types of valves in the industry, each having its own unique functions and design features. Below, we highlight the key distinctions between globe valves and gate valves:
Globe Valve | Gate Valve |
---|---|
Used to Open, Close, or Control the Fluid | Only Used to Open or Close the Fluid |
High-pressure Drop | Low-Pressure Drop |
Single-Way Direction | Bidirectional Valve |
Complicated Design | Simple Design |
High Maintenance Costs | Easy Maintenance |
Expensive than Gate Valves Based on Same Size and Material | Lower Cost than Globe Valve |
Complex Design & Struction | Simple Design |
For newbies, the gate valve may be very similar to the globe valve. But if you take close look at these two different valves, you will find the gate valve is much simple, a gate/disc you can see at the top of the valve body. When the gate valve is opened, the gate/disc will upward action, and complete on the top part of the bonnet, and the body becomes hollow.
But for the globe valve, the plug and seat are complete inners of the valve body. The design permits impediments that help the globe valve in its primary function of throttling and providing positive shut-off. Additionally, the design allows for variations in flow rate and direction, which can lead to a high-pressure drop.
When compared to a gate valve, a globe valve cannot close tightly. Pipeline gate valves provide a tight shut-off feature. Gate valves are utilized upstream of globe valves due to their tight shut-off abilities. This gate and globe valve combination may have been visible at the discharge pipe of a pump.
A globe valve needs more torque to operate. This higher power consumption for globe valves is also taken into account when constructing automated and motorized valve actuators.
When gate valves are used to regulate flow, we witness noise, vibration, and seat/disk damage, so gate valves were not designed to regulate flow. In the event that a gate valve is unavailable, a globe valve might be utilized to stop and start the flow. Generally speaking, a gate valve is only utilized for isolating fluid. As designs exist for both directions of flow, a gate valve can be utilized in either direction.
The opening and closing geometry of the valve disc/plug and seat also differ between globe valve and gate valve.
Globe valves can be maintained in place, while almost all gate valves need to be removed from the piping system in order to make repairs for leakage problems.
A gate valve will bind and be impossible to open against a large differential pressure, while a globe valve can. The seat will score and leak if you attempt to open against high differential pressure.
The gate valve is perfect for uses where low-pressure losses are essential. It is a multidirectional valve. The globe works best in settings where large pressure variations are not a concern. Globe valve only has one direction, and you will see an arrow mark on the body to show the flow direction.
Gate valves are linear valves that belong to the family of shutoff valves. The gate valve is widely used to isolate media because its wedge-shaped disc can effectively shut off fluid. This type of valve is suitable for applications requiring a tight seal. For thicker and more viscous fluids, the knife gate valve is the best choice.
Since there is no blockage in the media flow path, gate valves only cause minor pressure drops. The valve opens by the upward movement of the gate disc. It closes by lowering the disc to connect with the seats. The disc of a gate valve can be shaped as a wedge, a knife, or a parallel plane.
The gate valve is not utilized to control the flow of media, although having considerable throttling capacity. Due to the thinness of its disc, it might get misaligned from its seat as a result of media vibration. Its service life is shortened and harm is caused by this situation. The gate valve should completely open or fully close when in operation to increase the lifespan of the valve.
Each type of valve is represented by a different symbol. The globe valve is denoted by the symbol:
Here is what makes a globe valve different from a ball valve:
Globe Valve | Ball Valve |
---|---|
Best suited for controlling, opening, and closing flows | Excellent for opening and closing services |
Utilizes a plug to open, close, and control flow | A ball is used to open and close the flow |
The valve’s plug and stem move in a straight line | This valve’s ball and stem move in rotary |
High-pressure drop | Low-pressure drop |
Linear motion valve | Rotary motion valve |
Globe valves are control valves that are used to control, start, and stop the flow of media through a pipe. They feature a spherical body shape the appearance; on the inside, a plug fits on the end of a threaded rotating stem that is upward and downward to control media flow. Globe valves are a type of linear motion valve, which indicates that the valve mechanism moves in a straight line.
Globe valves provide a tight seal with minimum leakage, making them a great choice in high-pressure industrial pipe systems.
Gate valves are excellent for applications requiring tight shutoff or isolation. In the half-open state, gate valves cannot withstand a strong flow of media and are thus not utilized to regulate flow. They are utilized in industrial oil and gas pipe systems, water systems, and maritime sectors.
As a leading Control valve, globe valve and China filter valve manufacturer, our company is dedicated to providing innovative and reliable solutions to meet your filtration needs.
Globe valves can alternatively be referred to as throttling valves or throttle trip valves.
Throttle Trip Valves are a single, highly reliable valve assembly that can control flow and shut off in an emergency. The throttling valve controls the flow of steam and gas in large, high-pressure pipelines, like the main steam line for a high-pressure turbine or the gas supply line for a turboexpander. As trip valves, they add a crucial level of safety to these uses without the cost of a separate trip valve. When manually or automatically tripped, the valves quickly stop the flow of water to protect expensive equipment.
Advantages
When the throttle trip valve is opened, the pressure on the main disc is released by a pilot valve inside the valve. The seal-welded seat ring fits tightly to the body and has an expansion groove to keep the seating face from distorting. Gaskets of the flexitallic type seal well at all cover joints. The yoke and latching assembly are made to be easy to adjust while it is in use. To save space and enable the use of smaller operators, venturi seats can be offered in high-pressure applications. For direct connections to steam turbines, valves can be made with either welded ends or ANSI flange connections.
A needle valve is used to precisely regulate the flow of clean gases or liquids. Smooth flow control is achieved by gradual changes to the stem and plunger. The needle valves often feature a small flow capacity and a large pressure drop. Standard needle valve port diameters range from DN2 to 12 mm(1/8″ to 2″). A needle valve’s most typical application is to regulate gas flow, such as propane in a tank. Need valve is a kind of globe valve.
China oil cylinder valve manufacturers are known for their expertise in producing durable and efficient valves that can withstand demanding conditions in the oil and gas sector.
China manufacturers have made significant strides in recent years, becoming key players in the global market by delivering high-quality products at competitive prices. Investing in the right pneumatic components is essential for maintaining optimal efficiency and longevity in your pneumatic systems.
Our extensive selection of pneumatic accessories ensures seamless integration and enhanced performance in your pneumatic systems.
With robust design and precision engineering, pneumatic cylinders play a crucial role in translating compressed air into linear motion for various industrial applications
A pneumatic on/off valve is used for tight closing applications for liquids, gases, and vapors. It has standard options such as temperature extensions and metal bellows seals.
As this control valve is designed according to the modular assembly principle, so it can be assembled with a pneumatic actuator and an option with a handwheel, it also can be equipped with other accessories, such as limit switches, solenoid valve, and so on.
Features & Benefits
Modulating type control valves include single-seated control valves, double-seated control valves, angle type control valves, cage guided control valves, and so on.
For example, cage guided type balanced trim, movement balanced ring, fission labyrinth type standard cage, optional movement seal ring, high strength structure. The 510D series is the most pointed control valve in the high differential pressure operating mode, has used the labyrinth type valve cage, has the characteristic which multistage falls pressure, the multilayered labyrinth gasket type valve can reduce the fluid noise and eliminate cavitation as well as the multi-hole cage valve. Moreover, reduces the volume greatly, the trim in the valve is interchangeable between the HCB series control valve with the HSC series Cage Guided control valve.
A self-acting control valve is also known as a self-operated pressure regulator, which doesn’t need any auxiliary power to drive the valve, the self-acting control valve through the medium energy to operate the valve itself, that’s why it is called self-acting or self-operated. A self-operated control valve can realize the adjustment of temperature, pressure, differential pressure, flow rate, and other parameters. It has the characteristics of simple structure, low price, reliable action, and so on. It is suitable for occasions where flow rate changes are small, adjustment accuracy is not high, or instrument air/power supply is difficult.
Nominal Pressure PN of Control Valves Less Than 1.6MPa
Nominal Pressure PN of Control Valves Range 2.5 to 6.4MPa
Nominal Pressure PN of Control Valves Range 10.0 to 80.0MPa
Pneumatic top guided single-seated angle control Valve applied with an unbalanced plug, this top guided single seated angle control valve requires a large actuator output force. The size is reduced by incorporating a fine designed multi-spring diaphragm actuator. This series is a good application for slurry polymer crystallization and high-temperature fluid as the pressure balanced structure is not used here.
510D Model is adopted cage guided type balanced trim, movement balanced ring, fission labyrinth type standard cage, optional movement seal ring, high strength structure. The 510D series is the most pointed control valve in the high differential pressure operating mode, has used the labyrinth type valve cage, has the characteristic which multistage falls pressure, the multilayered labyrinth gasket type valve can reduce the fluid noise and eliminate cavitation as well as the multi-hole cage valve. Moreover, reduces the volume greatly, the trim in the valve is interchangeable between the HCB series control valve with the HSC series Cage Guided control valve.
A manual control valve uses a handwheel or handles to operate the valve, it is also called a blowdown valve.
Electric globe type control valves use electric or motorized actuators to drive the control valve to open, close, or regulate fluid flow.
In this type, the flow of the fluid is modified by the closure member in rotary motion. Rotary motion valves are of three types.
Normally the industrial process is by open-loop control or closed-loop control to maintain the desired data such as flow capacity, pressure, or temperature.
Generally, the open-loop control system that controls action only depends on the input signal without its output response.
The closed-loop control system that controls action depends on both of input signal and a feedback signal from the valve controllers.
Operator controls the process variable p2 via remote adjuster
Operator controls the process variable p2 an a closed-loop
Controlling system: Controller and actuator
Controlled system: Final control element, pump, pipeline, heating system, etc.
Input signal: It is the signal from the control room/operator controls to the valve positioner.
Output signal: It is the signal from the valve positioner then feedback to the control system.
Pneumatic globe type control valves: Globe valve, actuator, valve positioner, air filter regulator.
Actuator: It is the device to provides the power to activate the valves.
Steam control valves with pneumatic actuators are widely used for industrial processes, such as sugar mills, power plants, chemical industry, oil, and gas.
Usually, it is assembled with E/P or P/P valve positioner to receive an input signal from the controller room, 4-20mA or 3-15psi.
Description
The multi-spring membrane pneumatic actuators of P/R type are applied for control operation of control valves and other positioning elements in automatic industrial systems. There are two following design options of the actuator:
– Direct action (air – advances the stem)
– Reverse action (air – retracts the stem)
Features
( a) Direct-acting( PZMA)
1. Up diaphragm castings 2. Diaphragm
3. Diaphragm plate 4. Spring
5. Down diaphragm castings 6. Actuator stem
7. Yoke 8. Adjust nut 9. Travel indicator
( b) Reverse-acting ( PZMB)
1. Up diaphragm castings 2. Diaphragm
3. Diaphragm plate 4. Spring
5. Down diaphragm castings 6. Actuator stem
7. Yoke 8. Adjust nut 9. Travel indicator
Model TT-667 actuator is a reverse-acting, spring-opposed diaphragm actuator. The actuator positions the valve plug in response to varying pneumatic loading pressure on the actuator diaphragm.
Description
Our Model TT-667 diaphragm actuator with a single spring is 100% to replace Fisher 667 actuators, which are designed to ensure stable on/off or throttling operation of the control valve. These spring-balanced membrane actuators respond to the pneumatic output signal of the controller or valve positioner to determine the position of the valve plug. 667 diaphragm actuator is a reverse-acting.
Specifications:
It could be a single-seated, double-seated, cage-guided, top-guided globe type trim design for the industrial engineering process. The control valve body assembly with a pneumatic actuator to modulate or shut off downstream pressure, flow rate, or temperature.
Three ways control valves are service for diverting or mixing service. The pneumatic actuator is designed as a rubber diaphragm with multi-springs, or piston/cylinder type pneumatic actuator with single-acting or double-acting.
We are looking for valuable brand customers with long-term cooperation. Only with high-quality quality and service can bring our customers more market share and stable business.
Avoid your inquiry is delay response, please enter your WhatsApp/Wechat/Skype along with the message, so we can contact you at the very first time.
We will reply you within 24 hours. If for urgent case, please add WhatsApp: +86 185 1656 9221, or WeChat: +86 199 2125 0077. or call +86 189 5813 8289 directly.
Just leave your name, email, and simple message or requirements, We will contact you within 1 hour.
WhatsApp: +86 199 2125 0077
Skype ID: sowell85
Wechat ID: +86 199 2125 0077
We will reply you within 24 hours. If for urgent case, please add WhatsApp: +86 199 2125 0077, or WeChat: +86 199 2125 0077. Or call +86 189 5813 8289 directly.