What is an Axial Flow in the Check Valve?
Axial flow in the check valve means the fluid or gas flowing parallel to the axis. It is an axial flow shuttle structure design, and the disc assembly with spring has cushioning and anti-vibration functions. When the medium flows downstream, it will push open the disc and the fluid through the body via axial flow channel circulation. And the spring here has a cushion effect to avoid the impact vibration between the disc and the body when a standard check valve opens. When the medium flows in the opposite direction, the disc closes very quickly, and the disc and the valve seat are tight fitted to cut off the fluid from the reverse flow direction.
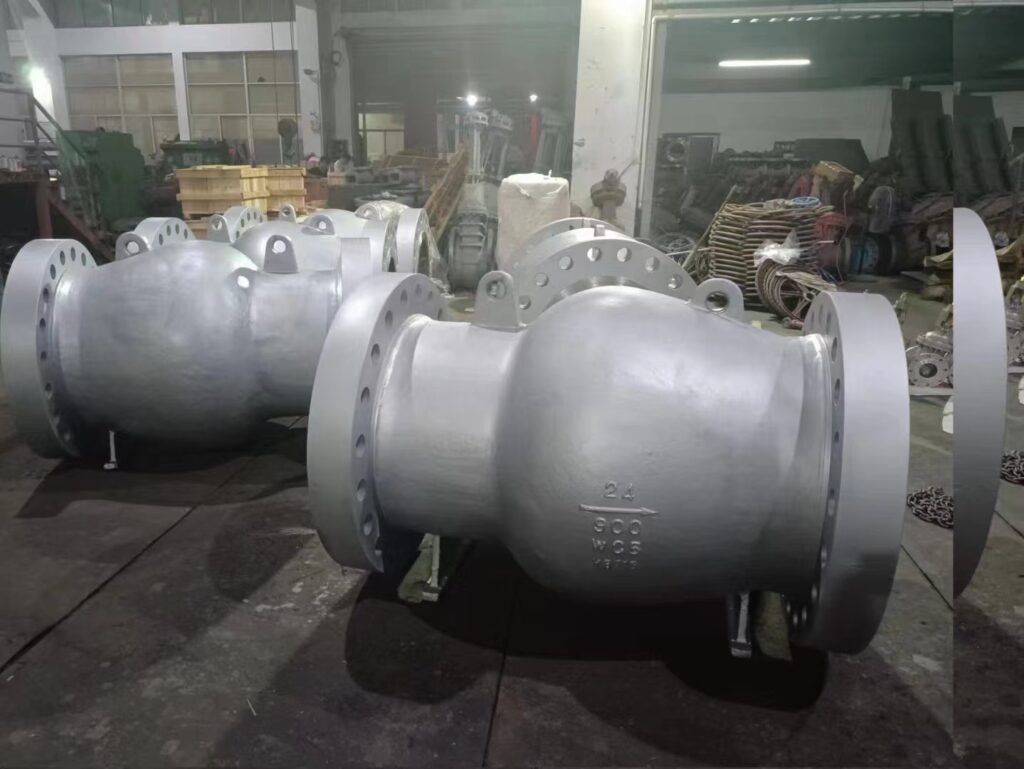
The axial flow check valves have a fast response and silent non-slam issue against pressure surge or damage from water hammer and are particularly designed for fast-reversing systems where backflow is a regular crisis.
What is Flow Check Valve?
An axial flow check valve is a kind of silent check valve. The check valve is driven by the medium itself and automatically opens and closes the valve disc. Generally, it is used to prevent the backflow of fluid or gases. A flow check valve can be called a one-way valve, non-return valve, backflow valve, backstop valve, and back pressure valve. An axial flow check valve has been a popular industrial valve since 2008. This valve has the function of the general check valve and is designed with a shock-absorbing spring, combined metal seat, and soft seat structure, which is easy for end-user maintenance on site.
The axial flow check valve adopts a particular sealing structure. Whether the downstream pressure is high or low, the valve is permanently closed tightly and has excellent shutoff performance. It overcomes the disadvantage of the lack of shutoff performance of the general check valve at low back pressure. THINKTANK produced an axial flow check valve that has a unique axial flow shuttle structure. It has the advantages of small flow resistance, significant flow coefficient, compact design, etc. It is the best valve for oil and gas gathering and transmission pipeline systems, especially for the outlet of oil transmission pumps.
Typical Application
- Water hammer prevention system
- Pump discharge application
- Cooling water systems(Ethylene, LNG)
- Waterworks & transmission systems
- Potable & raw water
- Transmission pipeline compressor discharge
- LNG compressor train
- Multiphase pumping
- Subsea pump and flowline application
Introduction to Non-Slam Nozzle Check Valves
A nozzle check valve also is a kind of non-slam or silent check valve, which is designed as a self-actualizing device and responds in a piping system to either pressure or flow changes. The main purpose of a non-slam check valve is to restrict or shut off the flow in the reverse flow direction. The important thing is that the normal position of a nozzle check valve is a valve close position with silent and non-slam closing action.
Why Use Non-Slam Nozzle Check Valve?
The primary function of a non-slam nozzle check valve is to prevent the water hammer and closing rapidly without slamming. When flow is reversed in a pipeline, it will cause hydraulic shock waves to pass through the valve, it also called the water hammer phenomenon. The water hammer can cause damage to the equipment in the pipeline, so we must prevent this phenomenon. So selecting the right non-slam nozzle check valve is the best way to prevent damage from occurring and causing serious issues at the site when the valve is in a fully closed position during reverse flowing through.
The Working Principle of Axial Flow Check Valves
An axial flow check valve is a kind of non-slam check valve, when the valve closes it won’t have a slamming phenomenon, and there are no excess pressure spikes are generated. Aixa flow check valve is simply designed with spring-loaded and a single low-mass valve disc that enables fast response, and dynamic reaction to the reduction in flow. The working principle is easy to understand, when the disc of the axial flow check valve is opening, the force of the single disc and spring is balanced that resulting in uniform flow.
When the pressure difference between the upstream and downstream of the valve exceeds the crack pressure of the spring, the obturator moves and allows flow. With the venturi design that the flow area of the valve steadily decreases to the seat diameter, and the reduced flow area increases the dynamic pressure and reduces the static pressure, allowing the valve to open fully and quickly. The spring is selected to allow the disc to open fully and stabilize on its backstop under normal flow conditions.
When the flow rate is significantly reduced, the spring responds in advance to the force of the reduced flow.
Standards for Axial Flow Check Valves
Here is the list of standards for an axial flow check valve, it’s very important for your selection.
Standard | Description | Supplier of Certificate |
ASME B16.34 | Applies to new construction and covers pressure-temperature ratings, dimensions, tolerances, materials, nondestructive examination requirements, testing and marking for the cast, forged, and fabricated flanged, threaded, and welding end and wafer or flangeless valves of steel, nickel-base alloys, and other alloys. | American Society of Mechanical Engineers (ASME) |
ASME B16.10 | Covers face-to-face and end-to-end dimensions of straightway valves and center-to-face and center-to-end dimensions of angle valves. | ASME |
API 598 EN 12266-1, 2 | Defines inspection, examination, supplementary examinations, and pressure test requirements for resilient-seated, nonmetallic-seated (e.g., ceramic), and metal-to-metal-seated valves of the gate, globe, plug, ball, check, and butterfly types. | American Petroleum Institute (API) |
ISO 5208 | Defines examinations and tests that a valve manufacturer needs to act upon in order to establish the integrity of the pressure boundary of an industrial metallic valve and to verify the degree of valve closure tightness and the structural adequacy of its closure mechanism. | International Organization for Standardization |
API 6D | API Specification 6D is an adoption of ISO 14313: 1999, Petroleum and Natural Gas Industries-Pipeline Transportation Systems-Pipeline Valves. This international standard specifies requirements and gives recommendations for the design, manufacturing, testing, and documentation of ball valves, check valves, gate valves, and plug valves for application in pipeline systems. | API |
Axial Flow Check Valve Manufacturers
Mokveld (Netherlands)
Mokveld is a Netherlands industrial valve brand, which has over 100 years of experience in the gas, oil, and water industry with expert knowledge, and it has advanced engineered valve systems for critical control and safety applications.
Sizes: 2″ – 84″
Rating class: ASME 150 – 2500
DFT (USA)
DFT is a famous brand of nozzle check valves, and it is formerly known as Durable Fluid Technology. DFT has been making in-line check valves and severe service control valves for over 70 years. It started with a customer’s need for a small metal-seated check valve that could be installed in any position while providing a tight shut-off.
CRANE (USA)
Crane is a USA brand that is focused on chemPharma & Energy designs and manufactures highly industrial valves, such as check valves, plug valves, ball valves, butterfly valves, and so on. For nozzle type and non-slam check valve, it is called brand NOZ-CHEK, this nozzle check valve is specially designed for fast reversing systems where backflow is a constant concern. Typical applications include gas transmission, power generation, petro-chemical / chemical processing, hydrocarbon processing, and water transmission.
Sizes: 2″ – 84″
Rating class: Class 150 – 4500
NOREVA GmbH (Germany)
Size range: 1” – 10” (DN 25 – DN 250)
Pressure Class: ASME 150 – ASME 4500
THINKTANK (China)
THINKTANK is a new brand compared with the above international brands, but its advantage is cost-effective and reliable quality, which means the end-users, engineering&contractor don’t have to pay high costs for axial non-slam check valves but still have a stable performance.
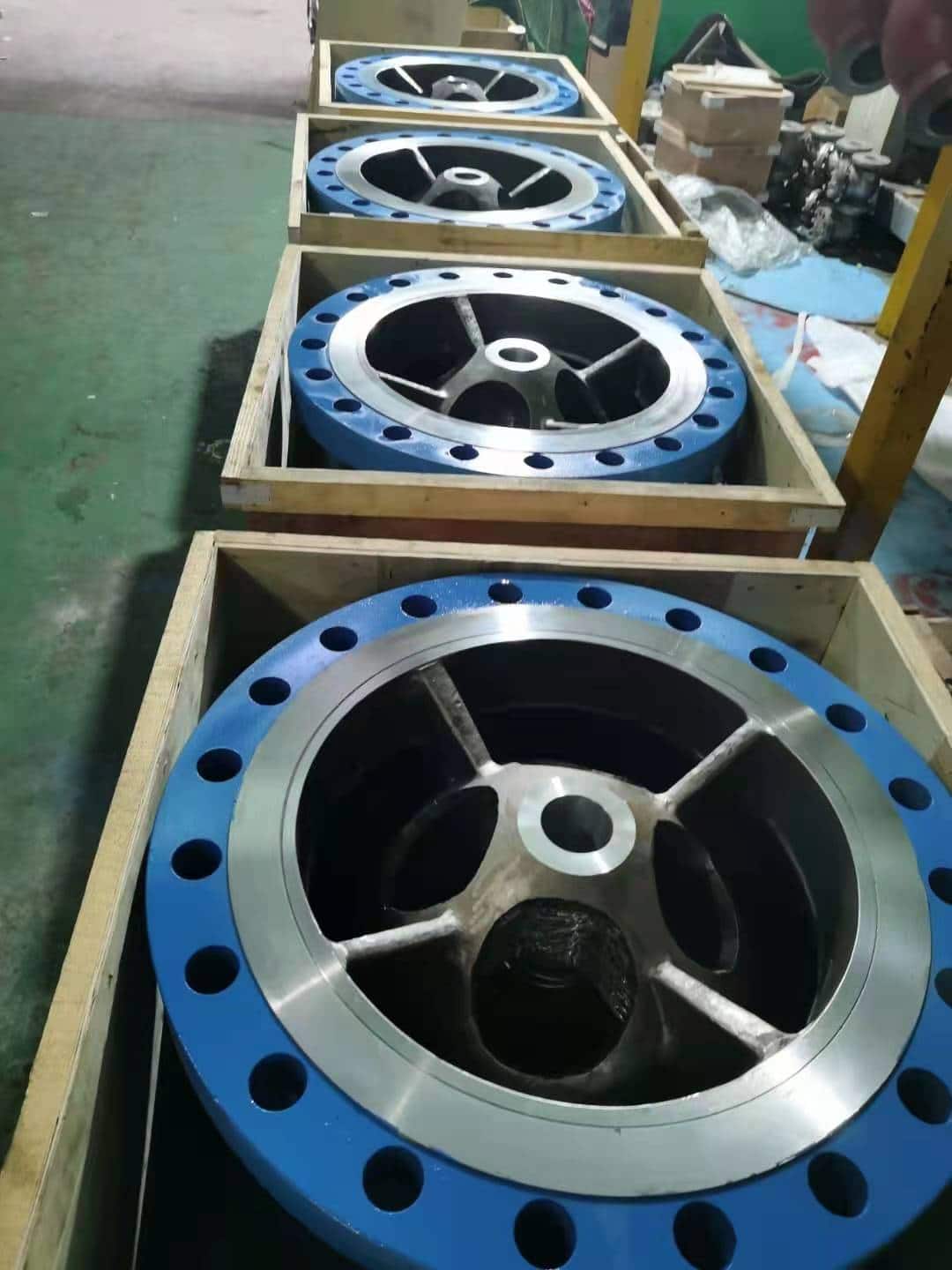
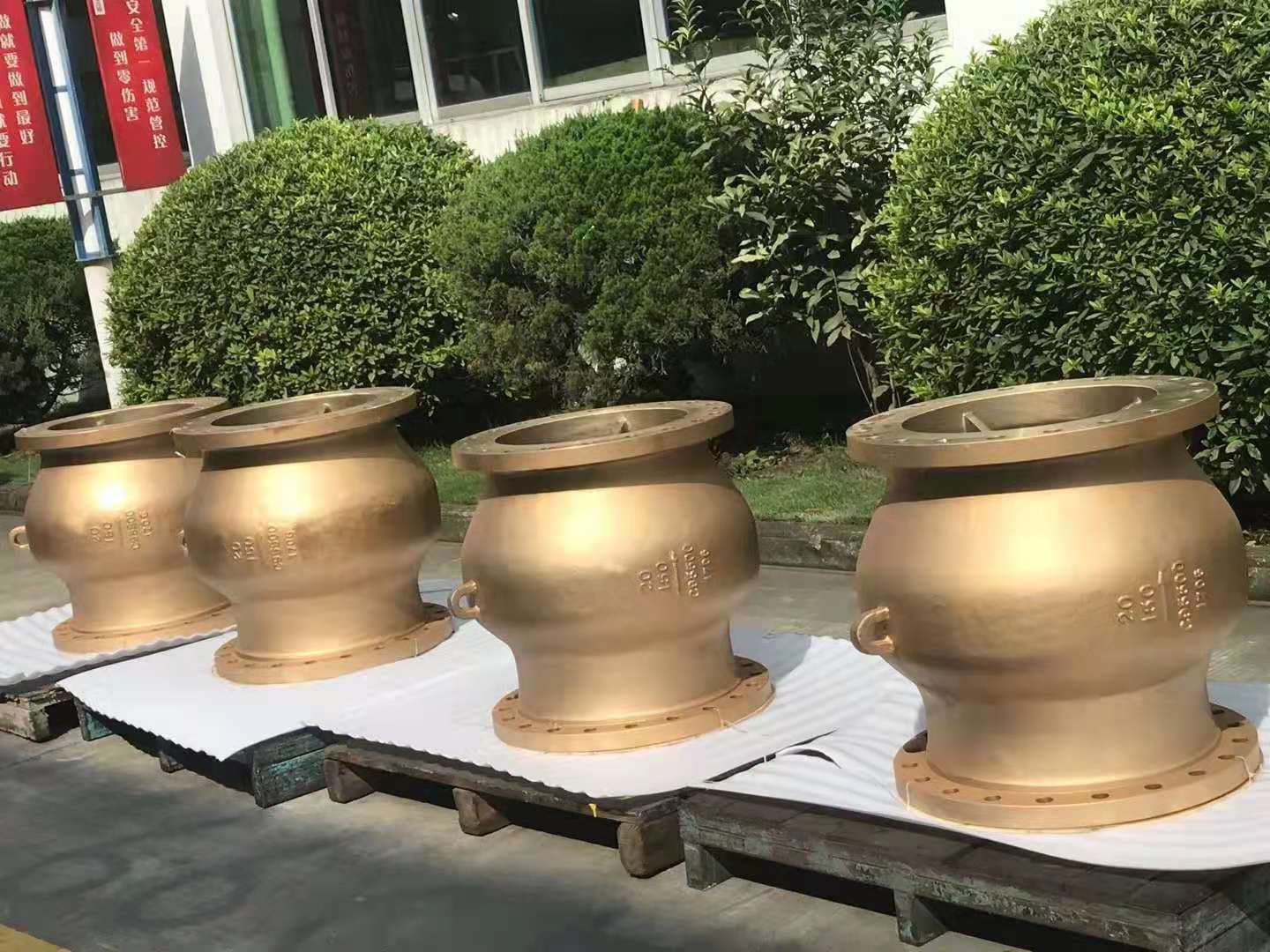
Axial Check Valve Installation
The components of the piping system include pumps, valves, compressors, elbows, bends, and reducers, and it will cause turbulence in the flow stream. In case to improve the service time of an axial flow check valve, you need to install it in accordance with best industrial practice, which means we need to keep enough distance from the turbulence source that makes the valve is in fully developed flow. The following figures are the best practice installation for nozzle non-slam axial flow check valves.
Horizontal Flow Installation
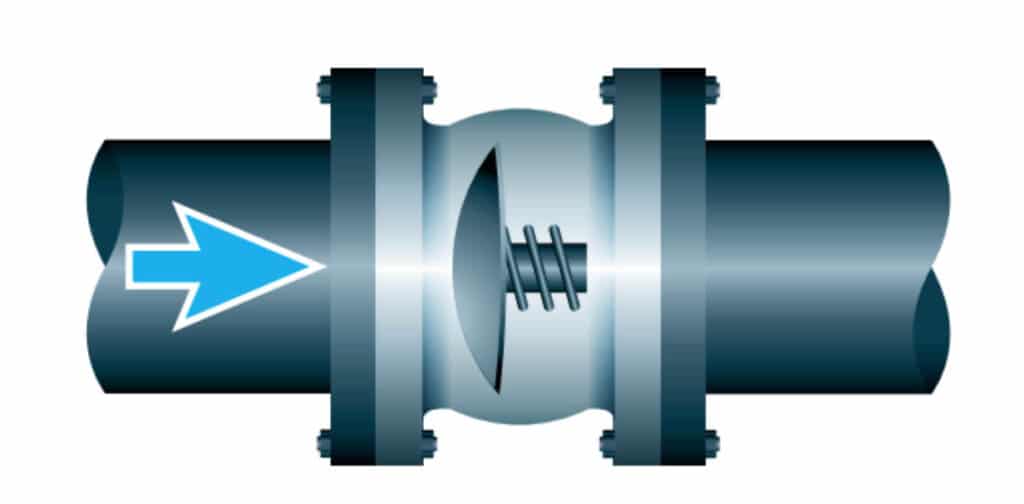
Vertical Flow Installation
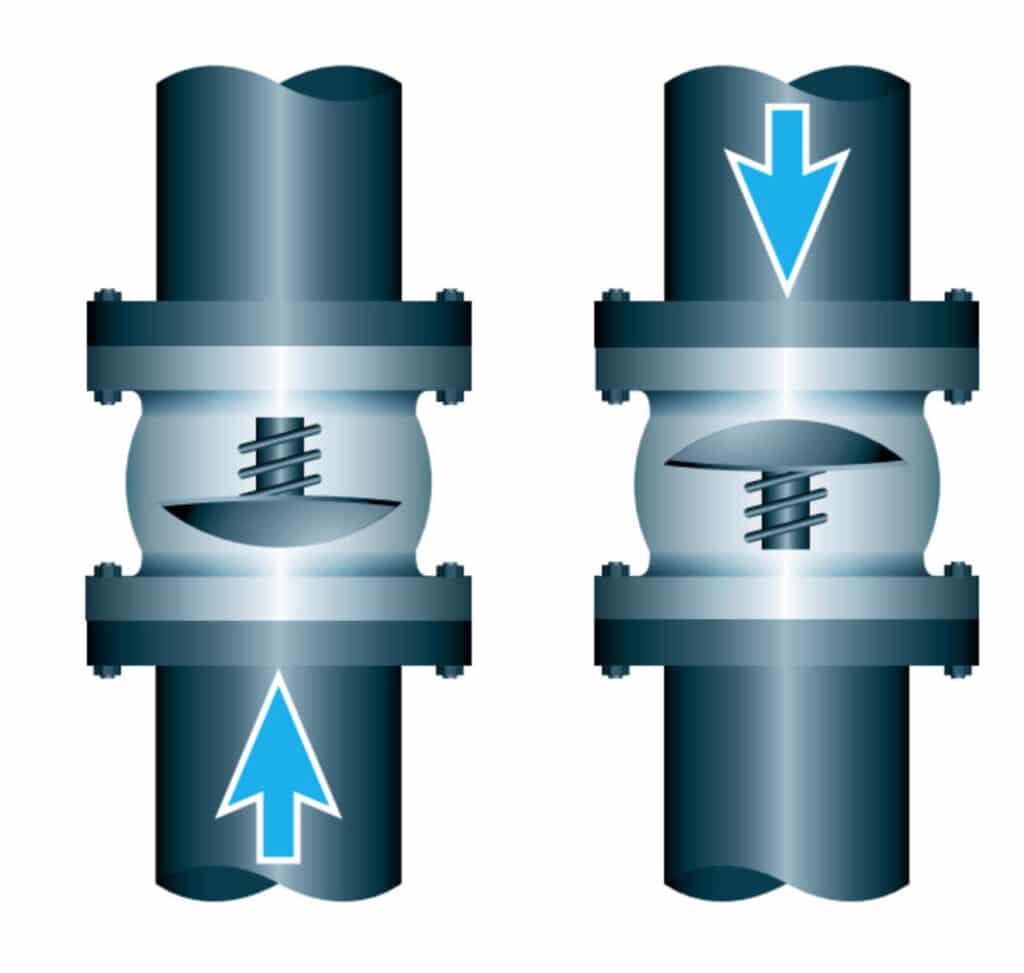
Non-slam axial flow checks are also suitable for vertical flow up and down. But it requires more process conditions for selection and sizing, so if your application needs vertical flow installation, please feel free to contact THINKTANK’s representative for consulting.
Sufficient Distance for Axial Flow Check Valve
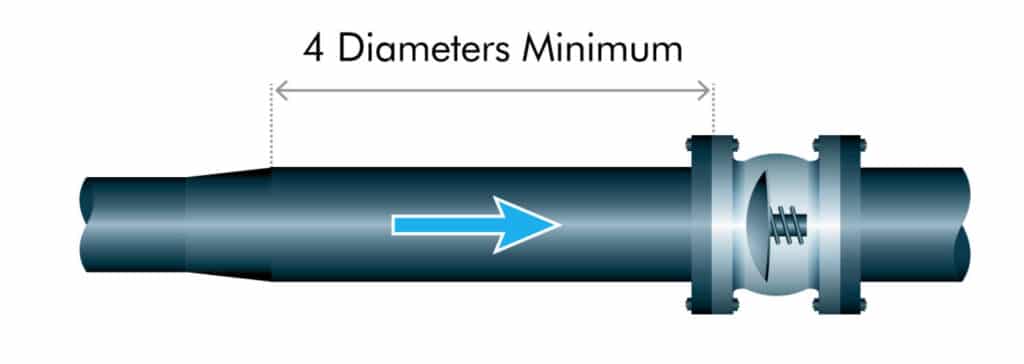
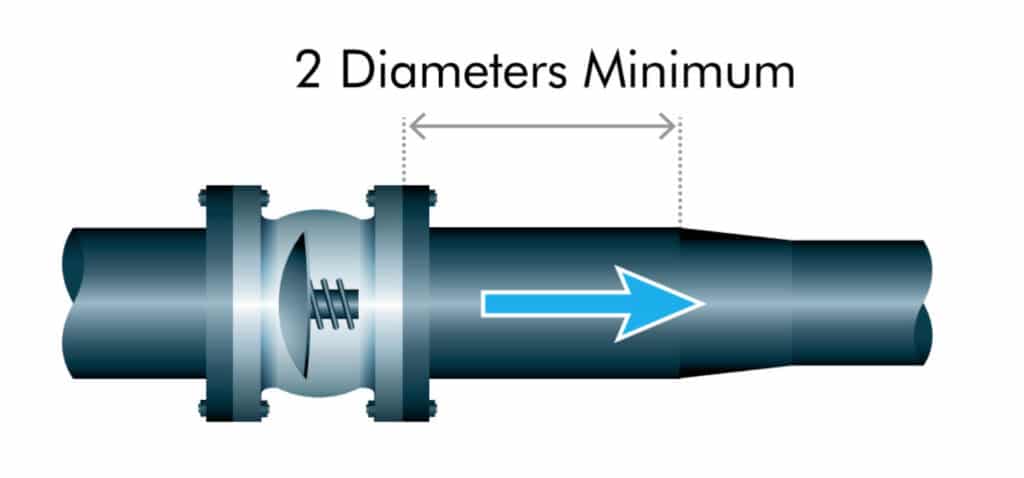
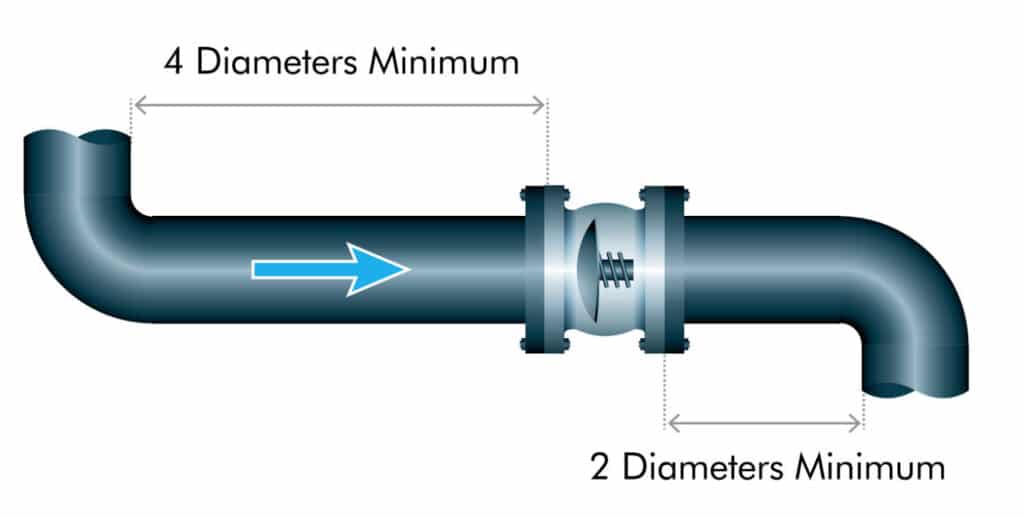
To ensure turbulence is minimized, the axial flow check valve needs to be at least 4 diameters distance to downstream of a reducer or expander, so that to make sure flow at the valve is fully developed.
To avoid causing choked flow that makes the valve only partially open, we should install an axial check valve at least 2 diameters distance to upstream of a reducer or bend.
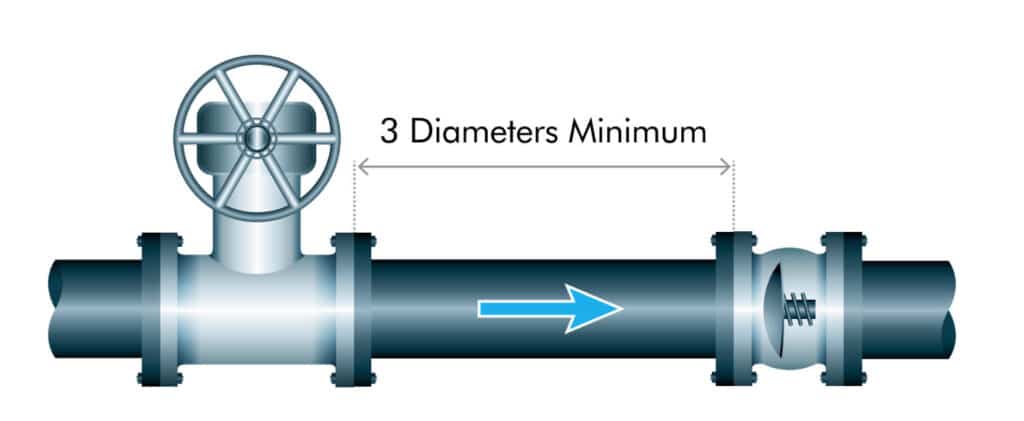
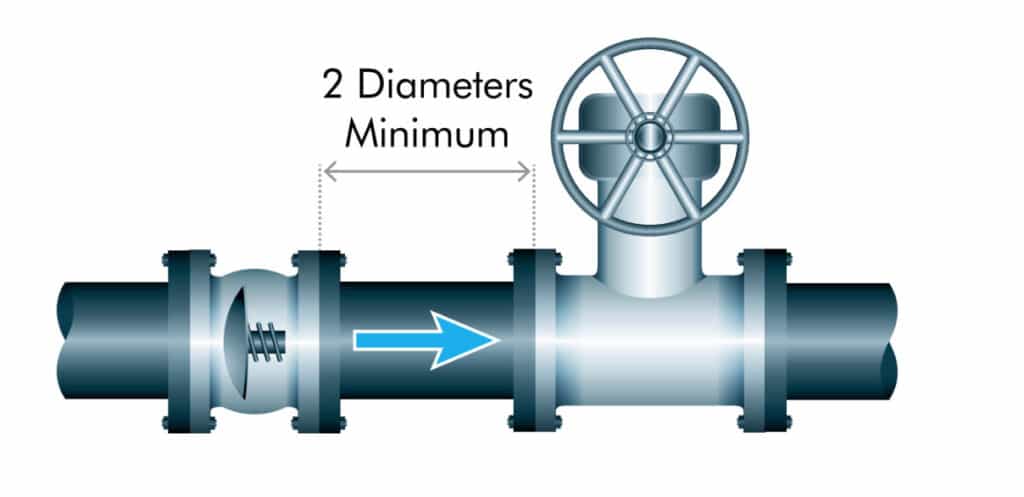
If the axial flow check valve is installed close to a throttling valve, we should be installed at least 3 diameters downstream, or 2 times of diameters upstream.
Free PDF of Axial Flow Check Valve Catalogue
If you are looking for a details introduction to the axial flow check valve, here is the catalogue you can free download.
Typical Applications for Axial Check Valves
Although axial non-slam check valves can be used for a variety of applications, in a growing number of niche industries, these valves are used primarily in the following areas:
Chemical & Pharmaceutical Industry
- Chlorine gas
- Phosphine
- Aromatics
- Polymers
- Acids
- Air separation
- Corrosive substances
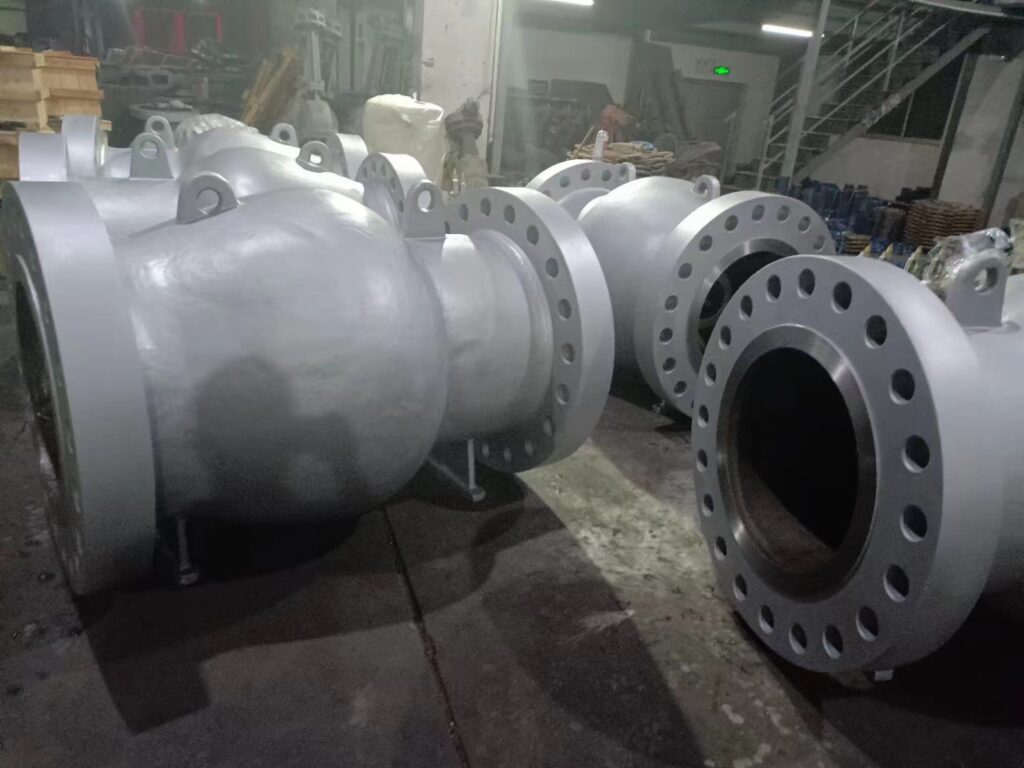
Power Plant
- Steam
- Condensate
- Boiler feed pumps
- Cooling tower
- Service water recirculator
- River Water Intake
- Renewable energy
Refining & Petrochemical
- Hydrogen
- Cracking
- Steam
- Crude oil
- Ethylene
- Propylene
- Steam
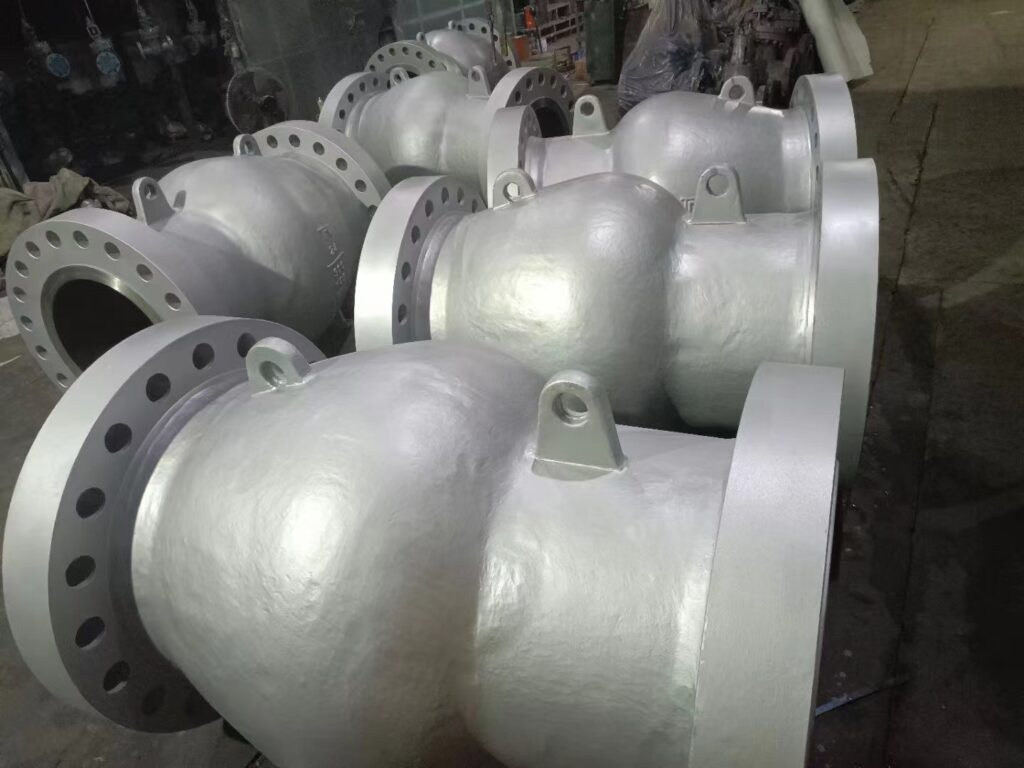
Oil & Gas
- Regasification
- Liquefaction
- Centrifugal compressor discharge
- Firewater piping
- Oil/steam separation
- Steam and CO₂ Injection
- Oil and gas gathering systems
In Conclusion
Non-slam silence nozzle check valves are widespread in many industrial processes. THINKTANK manufactures a large diameter axial flow check valve with a floating valve disc design that can automatically compensate for errors caused by installation and wear in use to ensure that the sealing surface fits tight and improve the shutoff performance. Please do not hesitate to contact us if you have any questions or comments.
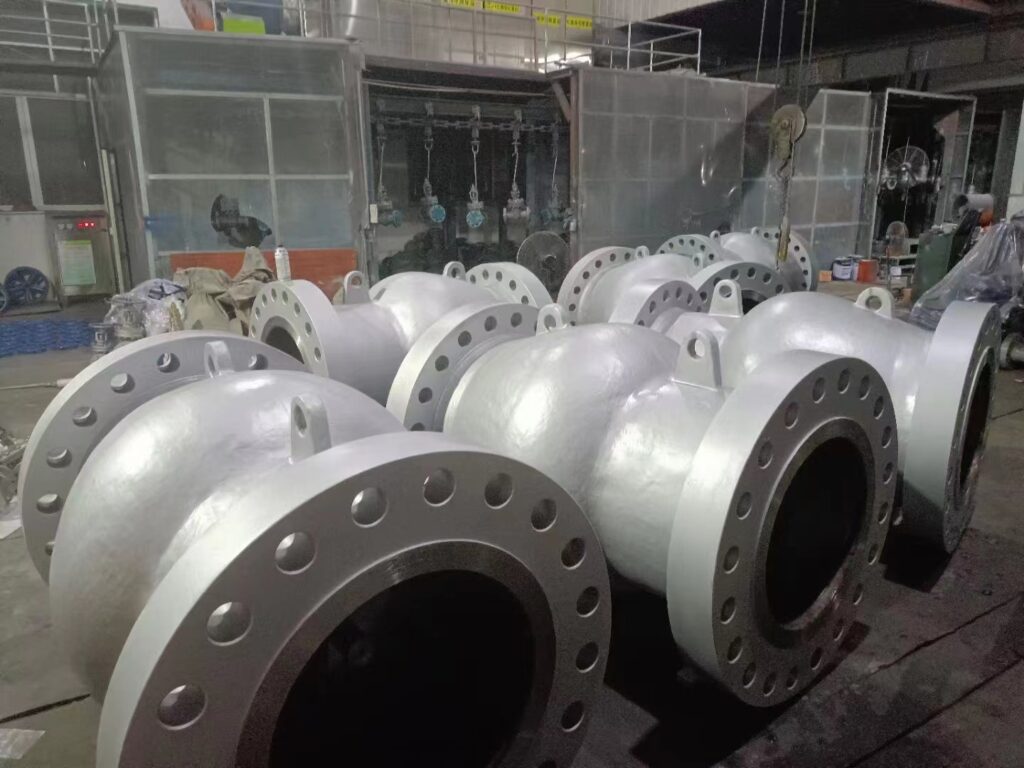