We know control valves are like the ‘final control element’ in the process of the industry. The main function of the control valve is to regulate the flow capacity or downstream pressure of a fluid. The control valves are usually installed with an actuator(pneumatic actuator, electric actuator, or gear handwheel actuator etc), positioner, handwheel, solenoid valve, limit switch, or other accessories.
different valves
Different types of valves are used in a variety of industries and applications to shut off, regulate and control the flow, pressure, and direction of fluids and gases, such as gate valves, globe valves, ball valves, check valves(spring return valves), butterfly valves, and other valves. There are hundreds of different valve types in industrial pipelines and equipment, also made of different materials, such as stainless steel bodies, special alloy bodies, carbon steel bodies, cast iron bodies, brass bodies, and others.
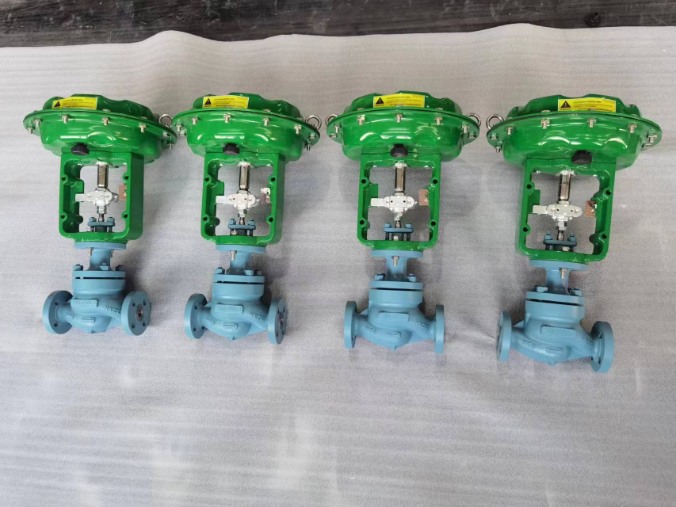
THINKTANK has more than 30 years of experience in valve manufacturing, and our control valves have been highly recognized by customers after time tested.
The most common control valves in industrial process loop include:
- Globe-type control valves
- Angle-type control valves
- Butterfly-type control valves
- Diaphragm-type control valves
- Ball/Plug type control valves
Globe Type Control Valves
Pneumatic globe control valves are widely used for control systems with precise regulation qualities. Their characteristics can be customized by the condition, and it can be safe and reliable handling of high differential pressure. For high-pressure drop applications, we use a multi-stage design to relieve the outlet pressure and also with low-noise internals. The globe control valves required low actuator forces but can achieve low leakage and even complete tightness function. Also no worry with the high switching cycle on the site. Of course, the control valves have disadvantages such as large install space and low flow capacity.
Advantage | Disadvantage |
Globe (Unbalanced) : 1. Large Range 2. Good Shutoff | 1. Unbalanced Forces 2. High-Pressure Loss |
Globe (Balanced): 1. High Capacity 2. Large Range 3. Balanced Forces | 1. Poor Shutoff 2. High-Pressure Loss |
The globe control valve assembly of two main components, valve, and actuator.
Valve | Actuator |
Body (2-way, 3-way) | Actuator Power Unit (Electric, Pneumatic) |
Bonnet | Actuator Stem |
Trim | Yoke & Coupling |
Recommended brand of globe control valves: FISHER, FLOWSERVE, SAMSON, ARCA, THINKTANK, KOSO
Recommended brand of valve positioners: SIEMENS, ABB, ROTORK(YTC).
Valve Body
- The globe control valve gets its name from its spherical shape. According to the ports of the valve body, it includes 2-way Flow Control, 3-way Mixing, 3-way Diverting type.
- Size: 1/2” to 36”
- Nominal Pressure: 150LB to 2500LB
- Material: Carbon Steel, Stainless Steel, Duplex, Alloy
Valve Characteristics
- Linear
- Equal percentage
- Quick opening
The globe control valve can meet capacity demands from 0.001 CV up to 12,000 Cv.
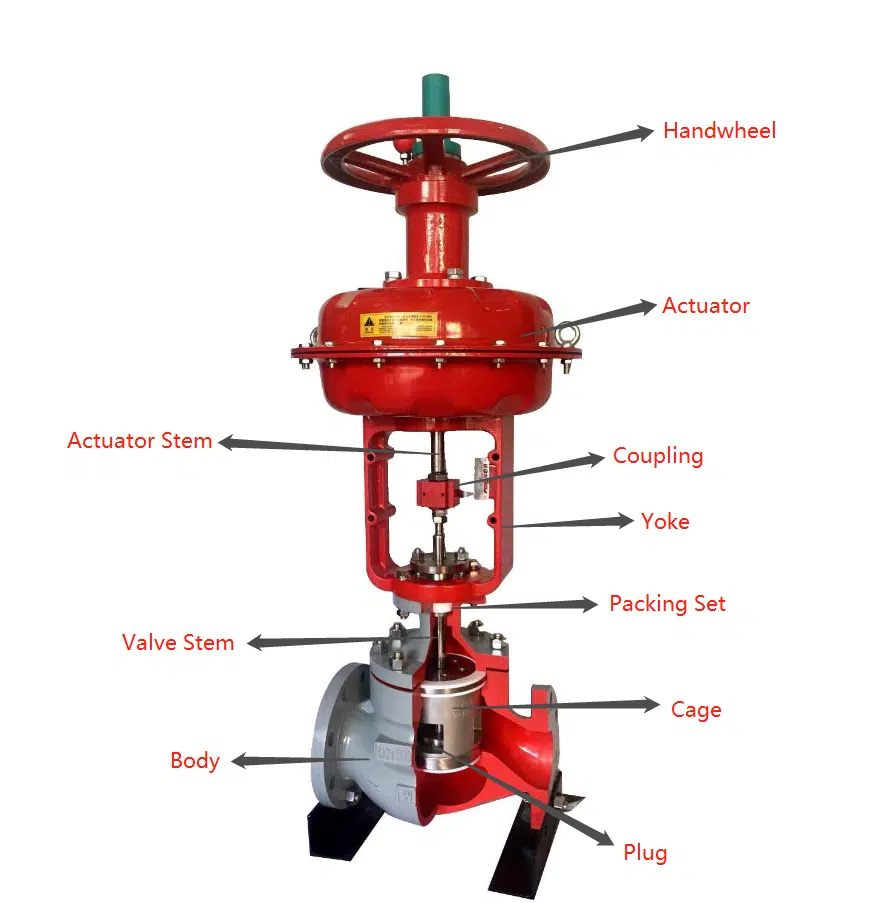
Valve Plug
- Balanced plug
The balanced port allows equal process pressure above and below the valve plug and typically flows downward through the seat ring.
- Unbalanced plug
The unbalanced plugs are solid, have no through holes, and typically flow upward through the seat ring.
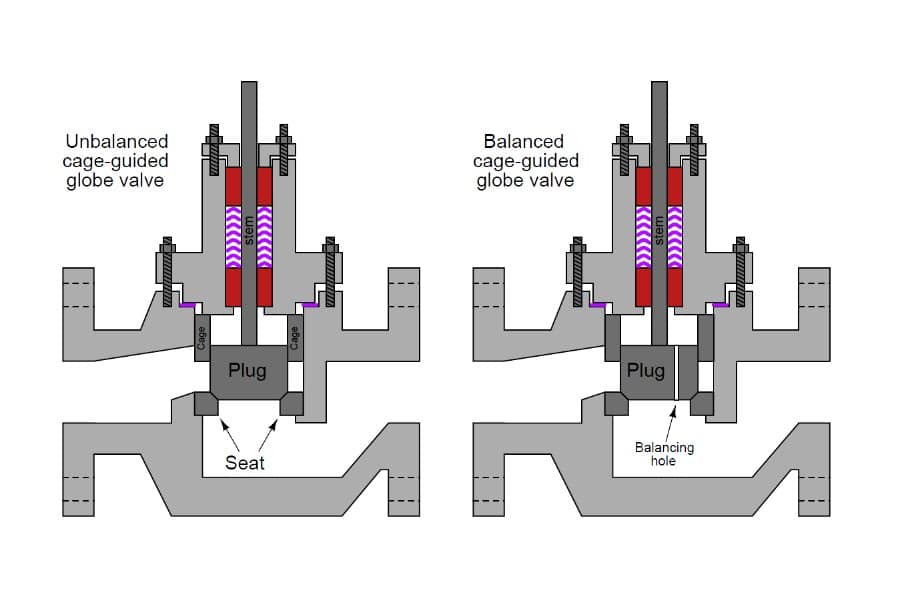
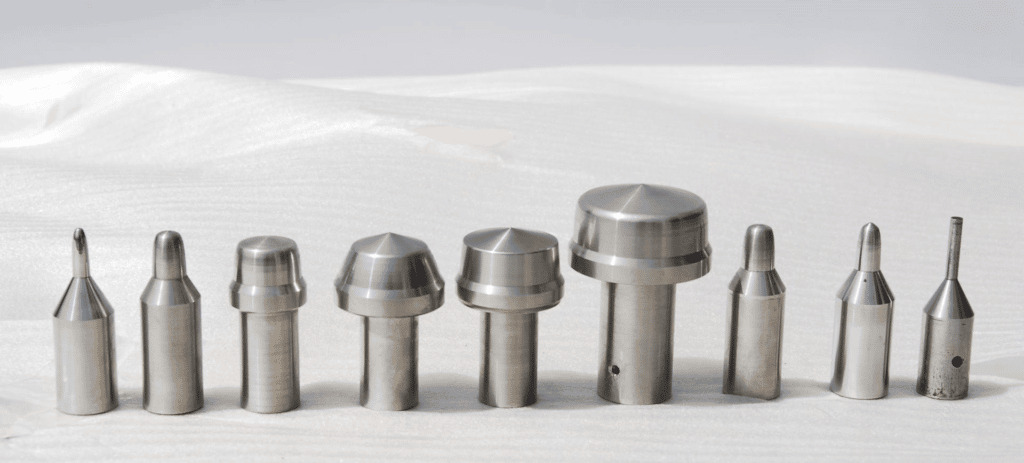
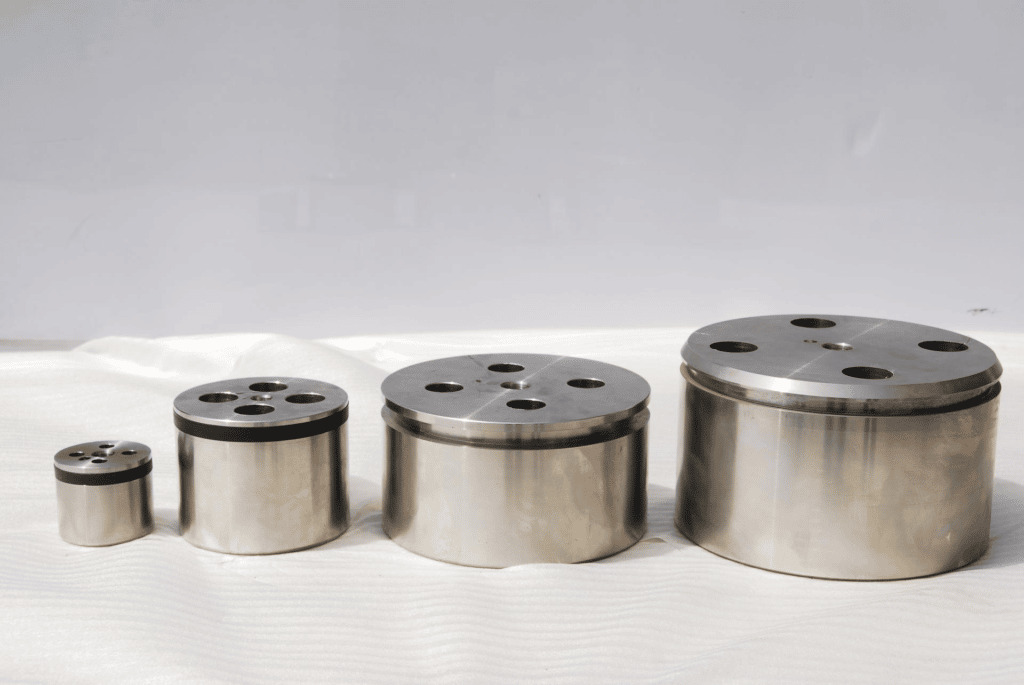
Bonnet
- Standard, plain bonnet (-17 to 230°C)
- Extension type I (-45 to -17°C and 230 to 566°C)
- Bellows
- Cryogenic bonnet
Integral cast type (-100 to -45°C)
Welded type (-196 to -100°C)
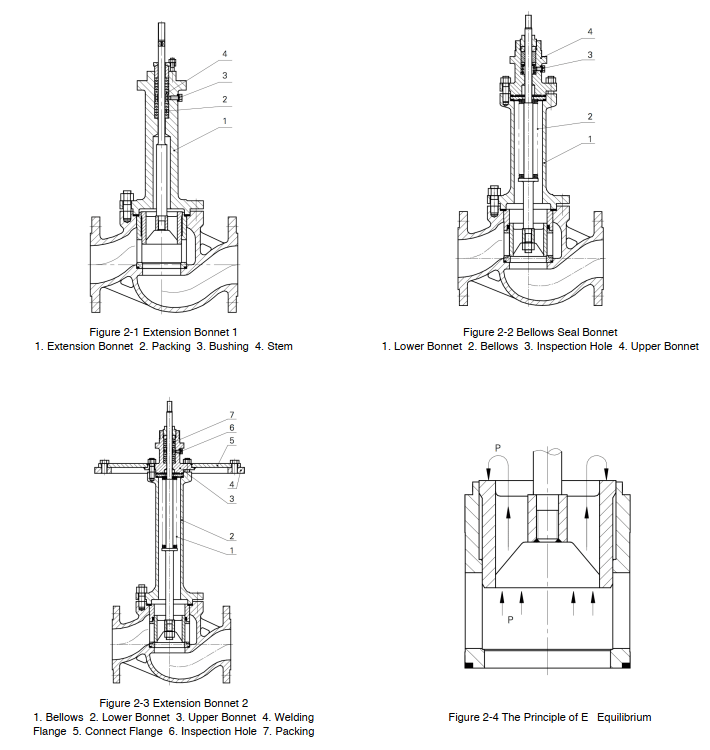
Trim
The selection of trims with different flow characteristics allows the globe control valves to be linear, equal percentage, or quick opening, so they can meet the capacity requirements from 0.001 Cv to 12,000 Cv.
Special valve trims are also available, which are designed to prevent noise and cavitation problems in cleaning and pollution applications.
Valve Actuator
- Electronic actuator
- Motorized actuator
- Diaphragm pneumatic actuator
- Piston type pneumatic actuator
- Cylinder type pneumatic actuator
- Electro-hydraulic actuator
Valve Positioner
Electro-pneumatic positioner (E/P or I/P)
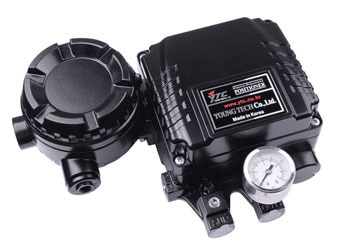
Pneumatic-pneumatic positioner (P/P)
Smart positioner (Digital positioner)
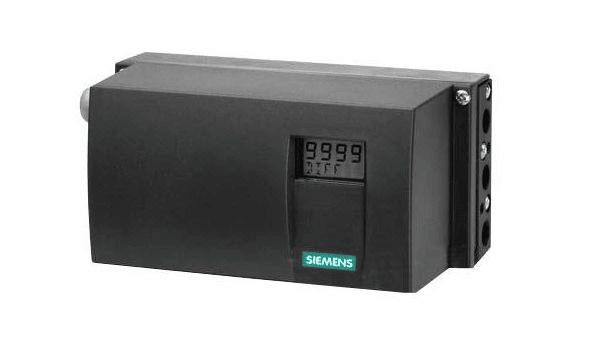
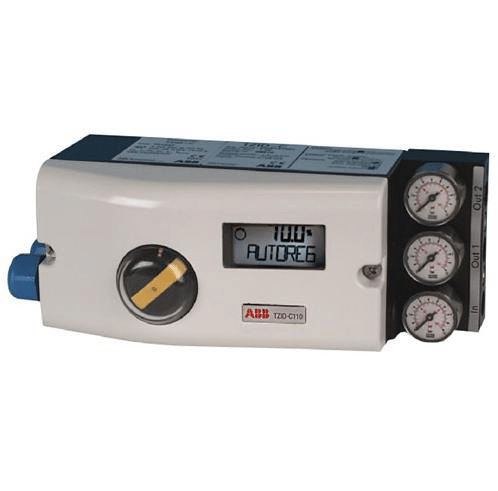
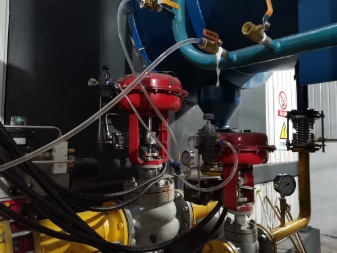
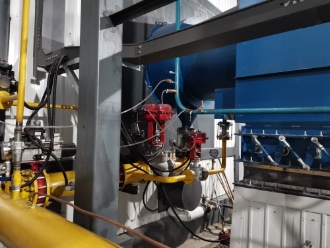
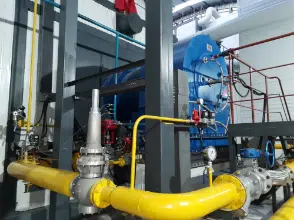
Angle Type Control Valves
Angle control valve design the inlet and outlet are perpendicular to each other. It uses linear motion to move the closure part in and out of the base surface. Angle control valves are usually used for boiler feedwater and heater blowdown services, and in piping systems where space is limited and piping valves can also be used as elbows. The valve can adopt a cage structure or an extended outlet connection, restricted internals, or outlet linings to reduce corrosion, flashing, or cavitation damage.
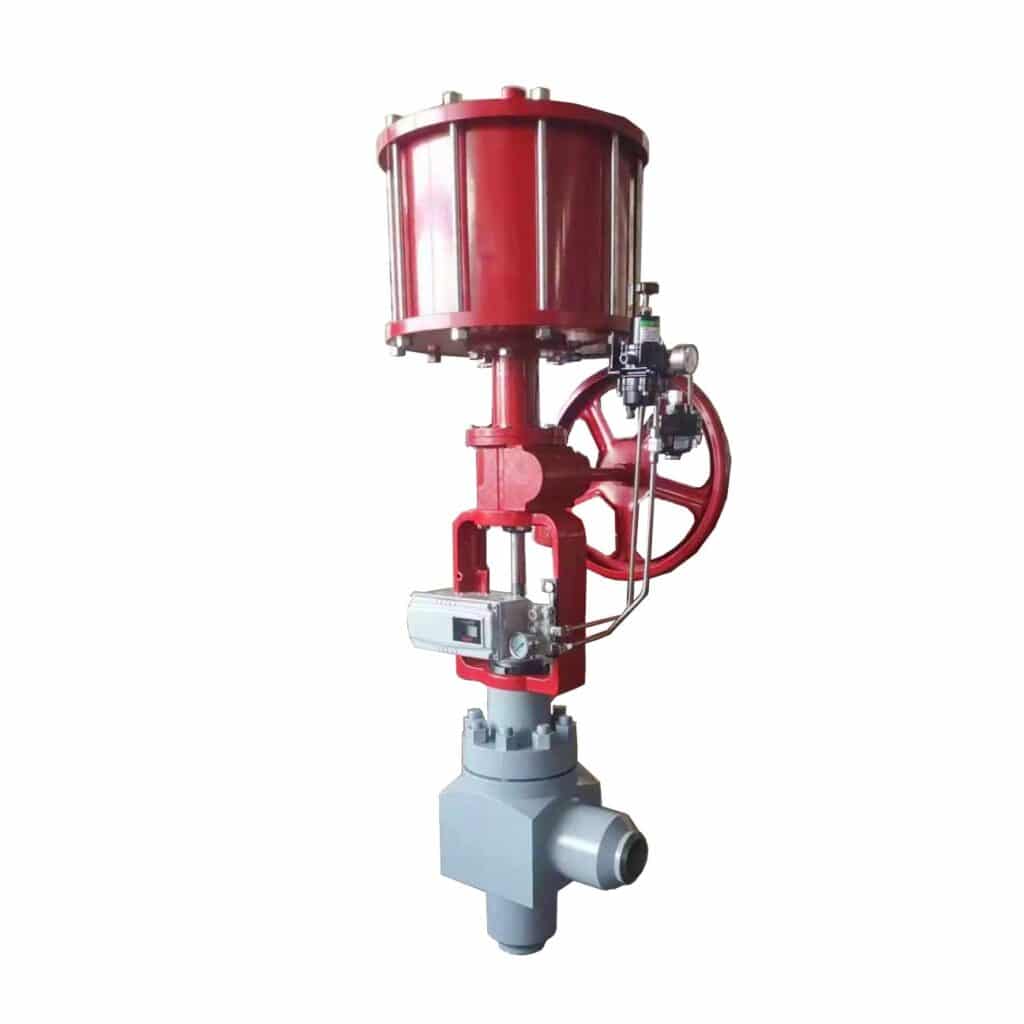
Valve Actuator
- Electronic actuator
- Motorized actuator
- Diaphragm pneumatic actuator
- Piston type pneumatic actuator
- Cylinder type pneumatic actuator
- Electro-hydraulic actuator
Butterfly Type Control Valves
When we talk about butterfly control valves, we generally refer to high-performance butterfly valves (double eccentric butterfly valves) and triple eccentric butterfly valves (triple offset butterfly valves).
In most applications, butterfly valves can replace other types of control valves because they provide the same basic functions, but often have more safety features and better performance. Using butterfly valves in your application can reduce maintenance requirements, improve the accuracy of flow control, and reduce the risk of disasters such as leakage. Butterfly control valves are also used to control water treatment plants because they provide the best seal and can withstand water pressure. Especially in large-diameter pipelines, the use of butterfly control valves is cost-effective.
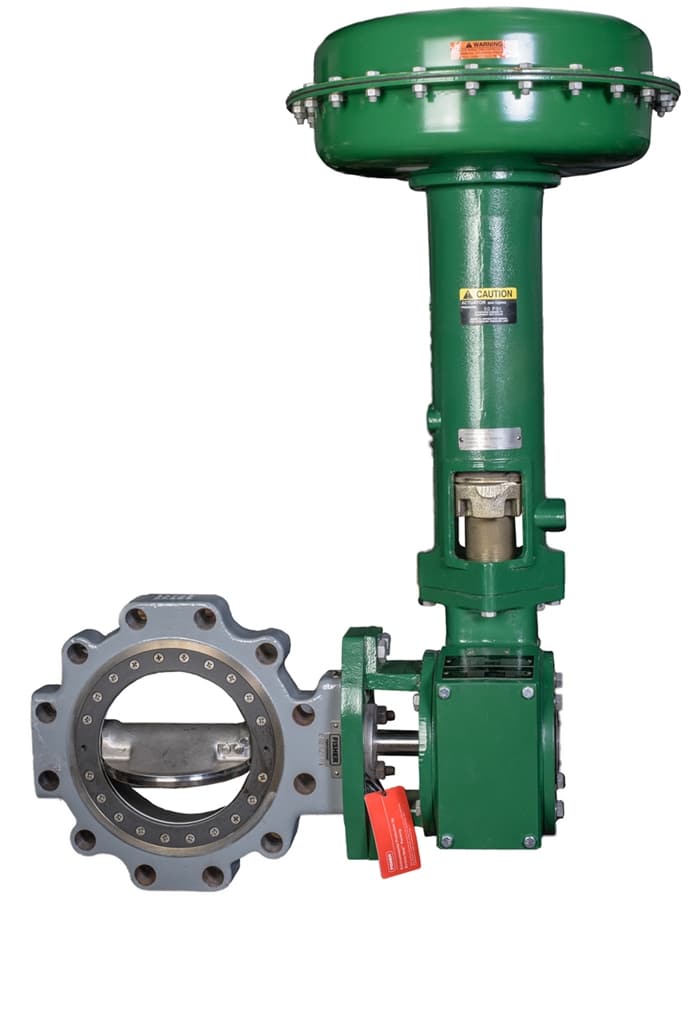
Advantage | Disadvantage |
1. High Capacity 2. Low-pressure Loss 3. Slurry applications | 1. High Torque 2. Large Deadband 3. Affects Flow-Through Limited Range (i.e. 0-60%) 4. Tight Shutoff Requires Special Seat Material |
Diaphragm Type Control Valves
The diaphragm type control valves consist of three main components: the body, the diaphragm, and the actuator.
The diaphragm is a dynamic component that restricts or isolates the flow of the medium. The original valve design includes a “weir” on the valve body, the medium flows through the weir and the diaphragm seals. A straight-through (or full-bore) design was introduced to handle solid particles. Both designs can utilize a variety of different diaphragm and liner materials.
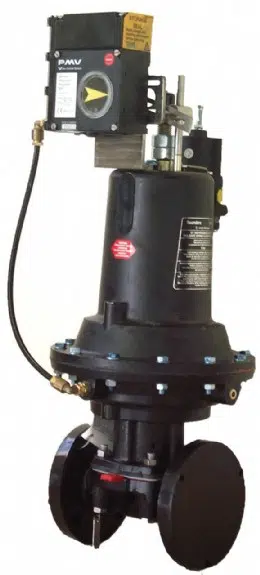
Advantage | Disadvantage |
1. Slurry Applications 2. Corrosion Resistant Materials | 1. Short Diaphragm Life 2. Limited Pressure and Temperature 3. Small Range |
Ball Type Control Valves
The V-Port or segmented ball is the most common type for ball control valves. Ball valves are widely used in fluid systems in many industries due to their low cost, durability, and excellent closing performance. Similar to butterfly valves, they are not as effective in flow control applications that require high precision and control sensitivity. One of the reasons is that the ball valve requires high torque to open and close, which prevents the operator from making fine adjustments. There is also a certain gap between the stem and the ball, which makes it difficult to find a specific flow rate suitable for fluid control applications.
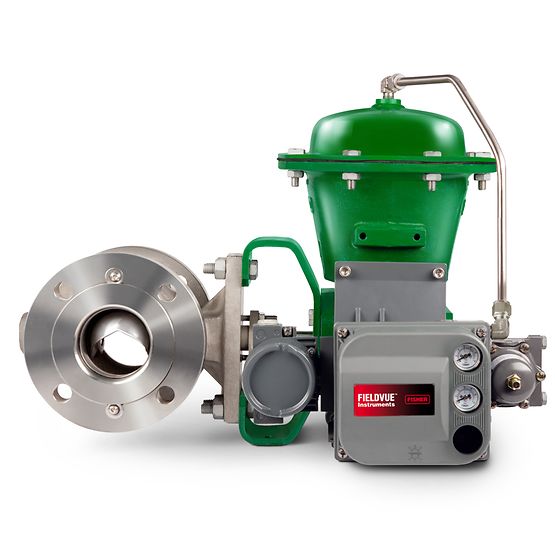
Advantage | Disadvantage |
1. High Capacity 2. Tight Shutoff | 1. Moderate Pressure Drop Applications 2. Tends to Plug (Except Segmented Ball Valve) |