In the dynamic realm of industrial engineering, precision reigns supreme, and safety is an unequivocal priority. Think of pressure relief valves as crucial unreplaced components, always ready to step in to relieve excess pressure when excess pressure exceeds set limits. These unsung heroes, interchangeably known as safety valves, safety relief valves, or relief valves, play a pivotal role in averting potential damage caused by excessive pressure. From chemical plants to power generation facilities, these safety relief valves are typically installed to control pressure and ensure the well-being of machinery and prevent the high risk of catastrophic failure. As we embark on this journey to unravel the intricacies behind pressure relief valves and their specific applications, we delve into their crucial roles and the precise design that goes into each unit, proudly crafted by industry leaders like THINKTANK.
Functionality of Safety Relief Valves
At THINKTANK, we recognize the fundamental purpose of a safety relief valve (SRV) in industrial systems. As a professional manufacturer, we focus on creating SRVs that effectively serve this purpose, which includes:
1. Preventing Overpressure
The primary role of our SRVs is to protect equipment and systems from excessive pressure build-up. This is crucial to prevent the risk of equipment failure, rupture, or even explosions that can occur due to overpressure.
2. Ensuring Safety and Compliance
Our SRVs are designed to ensure the safety of the plant, its workforce, and the environment. They are a critical component for complying with industry safety standards and regulations, helping to avoid hazardous incidents.
3. Maintaining System Integrity
By automatically releasing excess pressure, SRVs help in maintaining the operational integrity of systems. This is vital for the continuous and efficient operation of various industrial processes.
4. Cost-Effective Operation
By preventing damage caused by overpressure, our SRVs help industries avoid costly downtime and repairs. This makes them a cost-effective solution for maintaining long-term operational stability.
5. Customization for Specific Applications
We understand that different industries have varied requirements for pressure management. Therefore, we offer customized SRVs tailored to meet the specific needs of these applications, ensuring optimal performance and safety.
6. Diverse Industrial Sectors
Safety relief valves find indispensable applications across various industries, acting as crucial linchpins in maintaining system safety. From chemical plants and power generation facilities to refineries and pipelines, these valves ensure optimal performance by relieving excess pressure. Whether safeguarding against thermal expansion, chemical reactions, or cooling system failures, pressure safety valves are the unsung heroes that foster a harmonious balance in pressurized systems. Their role extends to protecting pressure vessels, process valves, and other critical components, making them a vital component in ensuring a safe and efficient operation.
Importance of Safety Relief Valves
In the world of industrial safety, safety relief valve stand as pressure regulator, designed to automatically release excess pressure and prevent catastrophic events. These valves play a pivotal role in protecting life, property, and the environment by offering the last means of reducing system pressure. Operating within specified set pressure limits, they act as a fail-safe, crucial for averting potential damage caused by excessive pressure. Think of safety relief valves as silent protectors, ensuring system stability and preventing disruptions. As essential components, they uphold a delicate equilibrium, fostering a safe environment where operations unfold seamlessly. In various industrial sectors, these valves are indispensable, safeguarding against excessive pressure and contributing to overall plant safety.
Plant Safety Chronicles
Ensuring facility and employee safety is a plant manager’s top priority. Safety valves, whether spring-loaded or pilot-operated, play diverse roles in chemical plants, power generation, and other industrial settings. They act as the linchpins, upholding the delicate equilibrium of safety and reliability in the dynamic realm of industrial engineering. Operating within specified set pressure limits, these valves contribute to the prevention of disasters by promptly and fully opening to release excess pressure. In the plant safety chronicles, we delve into the plant manager’s responsibility, the diverse roles of safety valves, and the comparison between spring-loaded and pilot-operated PRVs in maintaining a safe industrial environment.
Selection and Maintenance of Safety Relief Valve
Choosing the right pressure safety valve involves considering factors such as media type (air, gas, steam, liquid), set pressure, and capacity required for the application. This selection process ensures the valve functions optimally, providing safety in various industrial setups. Additionally, safety valve maintenance is vital for long-term reliability. Regular inspections, testing, and adherence to maintenance schedules are crucial to ensure that safety valves operate effectively when needed. In this section, we explore the key factors to consider during the selection of safety valves and the pivotal role of maintenance in ensuring their ongoing reliability. You can follow THINKTANK’s engineer to step by step maintenance your safety relief valve.
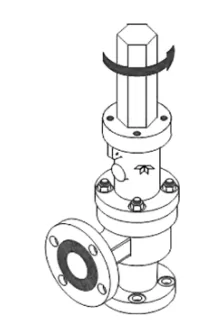
Step 1: Remove the cap and cap washers
To start, remove the cap and cap washers, if there are any. If the valve has a lifting lever device, take off the lifting lever assembly.
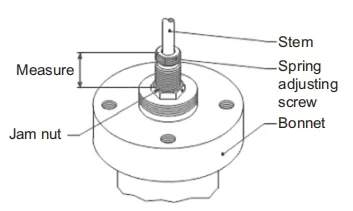
Step 2: Unscrewing the adjusting screw to relax the spring
Before unscrewing the adjusting screw to relax the spring, it’s a good idea to measure the precise position of the spring adjusting screw for future reference. This will ensure that the valve can be retested and reset accurately after reassembly.
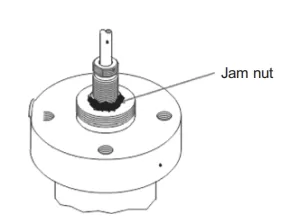
Step 3: Remove the jam nut
First, loosen and remove the spring adjusting screw to relax the spring. Remember to firmly hold the stem and bonnet while loosening the screw, as the spring is still compressed.

Step 4: Loosen the body/bonnet nuts and remove the bonnet.
Be cautious when lifting the car hood since the spring and spindle can easily detach and fall away.
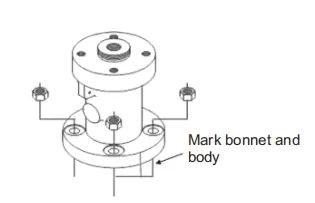
Step 5: Inspect the bonnet
Inspect the bonnet for any damage. Remember to mark both the body and the bonnet to serve as reference points during reassembly. It is crucial to reassemble the valve exactly as it was originally manufactured to ensure proper alignment of the internals, which is essential for optimal valve operation.
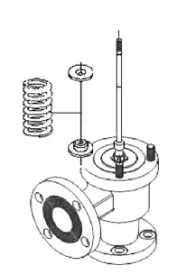
Step 6: Remove the spring, spring washers and bonnet gasket.
The spring and its washers usually come as a set. Each spring has its own set of washers. If you change the spring, make sure to replace the washers too. Keep in mind that spring washers may not always be swapped between opposite ends of the same spring.
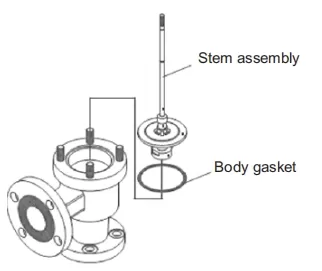
Step 7: Inspect the spring and spring washers
Please check the spring for corrosion or cracks. Ensure that the coating on the spring is still intact. Inspect the spring washers for any unusual damage.
Always replace the bonnet gasket with a new one and never reuse it.
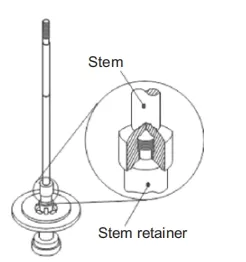
Step 8: Remove the stem assembly
Remove the stem assembly and check to see that the stem is not damaged by galling or deformation.
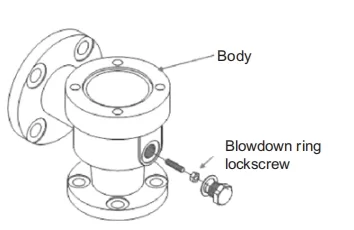
Step 9: Remove the blowdown ring lockscrew from the body
Make sure to remove the blowdown ring from the nozzle. Remember the number of turns it takes to unscrew the nozzle ring, so you can put it back in the same position when you assemble the valve again. This step is crucial because on small test benches with limited capacity, it is not possible to adjust the blowdown.
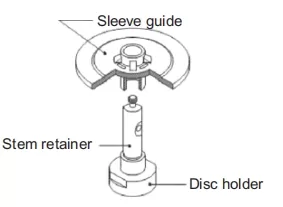
Step 10: Lift the sleeve guide off the stem retainer
If you’re dealing with a bellows valve, make sure to remove the bellows at this stage as well. If certain parts are hard to remove because they’ve been affected by corrosive substances or foreign materials, you might need to soak them in an appropriate solvent for a period of time.
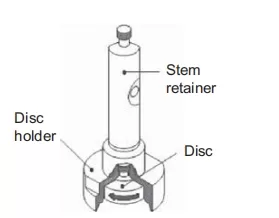
Step 11: Remove the disc from the disc holder
Depending on the design, this can be a bit inconvenient. Some designs feature holes on the top of the disc holder that allow you to push the disc out, while others require the use of a screwdriver to release the disc. Another type has a lockscrew in the middle of the disc that can be loosened to remove it. Regardless of the design, be careful not to harm the disc or its surface, unless you intend to replace it entirely. Make sure you’re familiar with the disc removal process, or consult the manufacturer’s instructions.
If the disc is not severely damaged, it can be lapped using a professional lapping machine. Otherwise, it can be done manually, as explained below. It’s important to note that a disc has limitations in terms of repairability. The material removed during lapping may impact the tolerances in the valve and, potentially, the set pressure.
After performing the necessary maintenance tasks, be sure to reassemble the valve precisely as it was originally manufactured. Proper alignment of the internal components is crucial for the valve to function well.
If you come across any questions while conducting the maintenance work, feel free to reach out to the engineer from THINKTANK. They will be available to help you with your specific application.
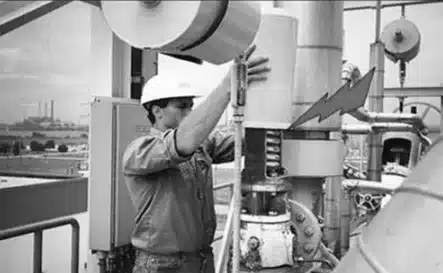
Summary
In essence, the purpose of our safety relief valves at THINKTANK is to act as a critical safeguard against overpressure, ensuring the safety, reliability, and efficiency of industrial operations. to learn more about pressure relief valve or pressure safety valve please visit our blog posts.