Pressure relief valves are required to relieve pressure under widely varying conditions. These valves play a pivotal role, in ensuring the maintenance of balance between optimal functionality and potential risks. However, like any mechanical component, pressure relief valves undergo wear and tear over time that may lead to a pressure valve failure, raising a crucial question: How often should these components be replaced to maintain peak performance?
In this blog, we explore the factors that govern the replacement frequency of pressure relief valves. From signs of wear and industry guidelines to the consequences of neglect and the best practices for replacement, join us on a journey to unravel the secrets of maintaining a robust and reliable safety infrastructure.
Signs of Pressure Relief Valve Wear
In the lifecycle of pressure relief valves, wear is an inevitable companion, silently influencing their performance. Identifying the signs of wear becomes crucial to ensure these essential components are replaced at the right time.
Leakage and Drips
A noticeable increase in leakage or drips around the pressure relief valve could indicate wear, compromising its effectiveness in managing excess pressure.
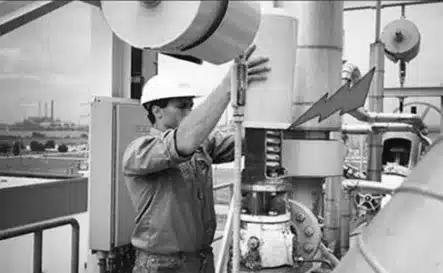
Corrosion and Rust
External signs of corrosion or rust on the valve body may signify deterioration, impacting its structural integrity.
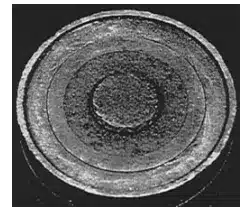
Inconsistent Operation
If the valve operates erratically or fails to open and close smoothly during tests, it might be a sign of a malfunctioning pressure relief valve with internal wear.
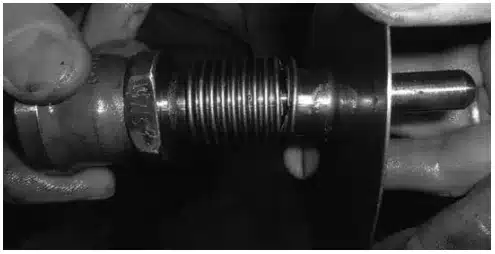
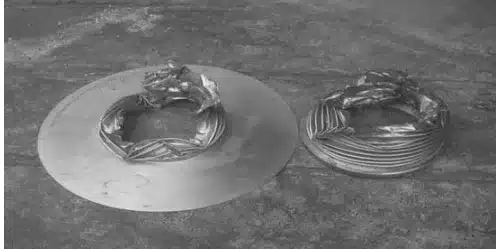
Reduced Performance
A decline in the valve’s performance, such as insufficient pressure relief or delayed response, is a clear indicator of wear and tear.
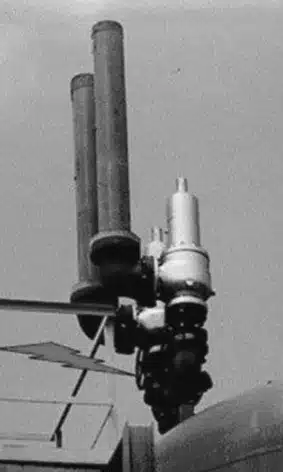
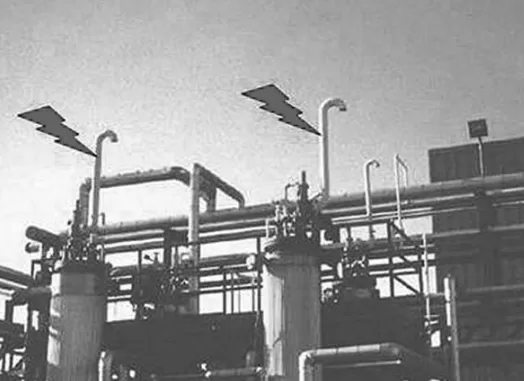
Visual Inspection
Any visible deformities, cracks, or abnormalities on the valve’s surfaces.
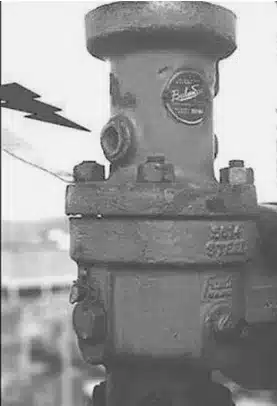
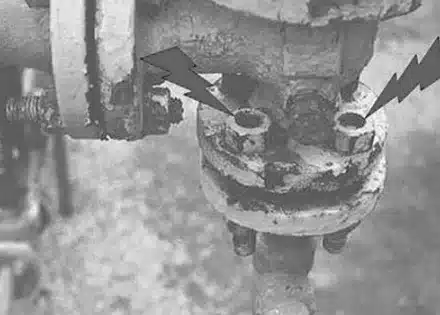
Fluid Residue
The presence of fluid residue around the valve seat or discharge outlet could suggest wear and compromise the seal.
Vibration and Noise
Unusual vibrations or noise during valve operation may point to internal components experiencing wear and needing attention.
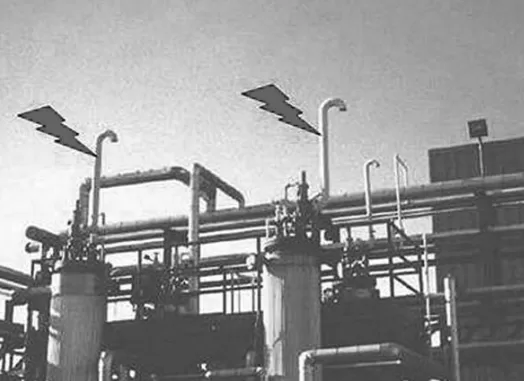
By recognizing these signs, operators can proactively address wear issues and ensure the continued reliability of pressure relief valves in safeguarding industrial processes.
Factors Influencing Replacement Frequency
understanding the factors that decide replacement frequency for the pressure relief valves is crucial. From operating conditions and system criticality to manufacturer recommendations and technological advances, these variables play a pivotal role in planning an effective and proactive maintenance strategy. Let’s explore each elements to ensure the continued reliability of our safety infrastructure.
- Operating Conditions: Harsh or extreme operating conditions, such as high temperatures or corrosive environments, may accelerate wear and necessitate more frequent replacements of the pressure relief valves.
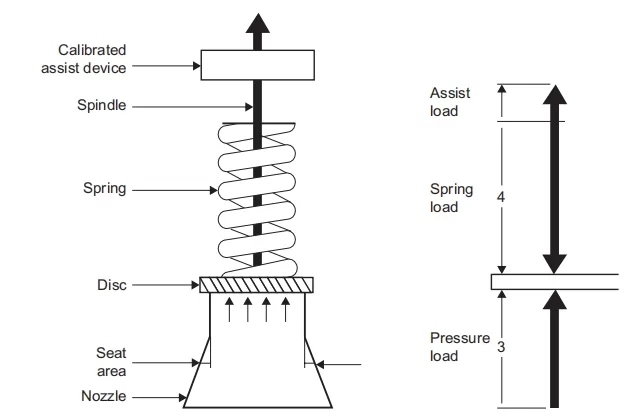
- System Criticality: The criticality of the system the relief valve protects influences replacement frequency. Vital systems may require more frequent evaluations and replacements.
- Type of Application: Different applications have varied demands on pressure relief valves. Applications with frequent pressure fluctuations may require more frequent replacements.
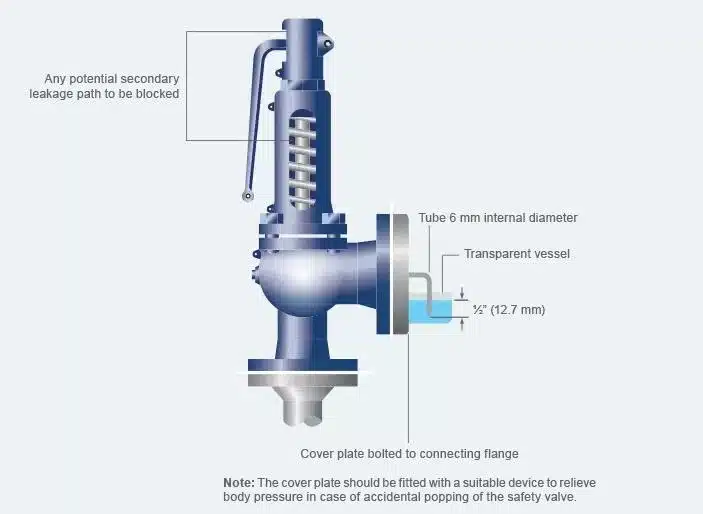
The frequency of replacing pressure relief valves (PRVs)
The frequency of replacing pressure relief valves (PRVs) depends on various factors including the valve’s operating conditions, the nature of the medium it controls, the valve’s design and material, and the regulatory standards applicable to your specific industry and geographic location. There is no universal interval for replacement as it can vary significantly based on these factors. However, here are some general guidelines:
1. Manufacturer’s Recommendations:
Always refer to the manufacturer’s guidelines first. Manufacturers provide specific intervals or conditions under which their valves should be replaced or serviced.
2. Regulatory Requirements:
Different industries and regions have specific regulations governing the inspection, maintenance, and replacement of PRVs. For instance, in certain high-risk industries, such as petrochemicals or power generation, the regulations may be more strict.
3. Service History and Conditions:
The history of the valve’s operation, including the frequency of actuation, exposure to corrosive materials, and operating pressures and temperatures, can affect its lifespan. Valves in harsher conditions may require more frequent replacement.
4. Routine Inspections and Maintenance:
Regular inspections can help determine if the pressure relief valves are functioning properly. Signs of wear, corrosion, leakage, or damage are indicators that the valve may need to be replaced.
5. Testing Results:
Pressure relief valve testing should be done periodically to ensure they open and close at the correct set pressures. If a valve fails these tests, it may need to be serviced or replaced.
6. Industry-Specific Guidelines:
Some industries have specific guidelines for PRV replacement. For example, in the boiler industry, safety valves might have specific replacement intervals based on usage and inspection results.
7. Type of PRV:
The design and material of the PRV also influence its lifespan. Some materials and designs are more robust and can last longer under certain conditions.
8. Incident-Driven Replacement:
If there has been a system overpressure event or a significant process upset, it’s wise to inspect and possibly replace the PRVs involved, as these events can cause unseen damage to the valve.
9. Technological Upgrades:
Advancements in valve technology might also justify replacement of older valves even if they are still functional, especially if safety, efficiency, or regulatory compliance can be significantly improved.
Summary
In conclusion, the decision to replace a Pressure relief valve or safety relief valves, should be based on a combination of the manufacturer’s recommendations, regulatory requirements, inspection and test results, and the operational history of the valve. Regular maintenance and inspection are key to ensuring the proper functioning and safety of PRVs in any system. Should you have any questions, please do not hesitate to contact the sales representative at THINTKANK.