In today’s industrial landscape, efficient control of fluid flow is crucial for operational success. A key component in this process is the valve, a device used to regulate, direct, or control the flow of a fluid by opening, closing, or partially obstructing fluid flow. Among the various types of valves available, pneumatically operated valves have carved a niche for themselves due to their numerous advantages. These valves, which use air pressure for operation, are known for their safety, s, and energy efficiency. In this blog post, we delve into the world of pneumatically operated valves, exploring their benefits, wide-ranging applications, and tips for selecting the right valve for your needs. We, THINKTANK Control Valve, a trusted provider of high-quality pneumatically air operated valves throughout, designed to meet the diverse requirements of various industries.
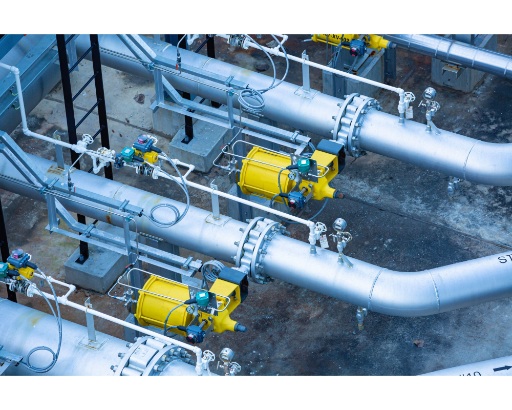
The importance of valves in industrial processes
Valves are an indispensable part of any industrial process. They serve several crucial functions that ensure the smooth, safe, and efficient running of operations across a wide range of industries. Here’s why they are so important:
Flow Control
The primary function of a valve is to control fluid flow. This can be achieved by starting, stopping, or modulating the flow, allowing precise control over process quantities like flow rate and pressure.
Safety
Valves play a critical role in maintaining safety in industrial processes. For instance, safety or relief valves prevent equipment damage by releasing pressure when it exceeds a set limit. This function is particularly vital in industries such as oil and gas, power generation, and chemical processing, where overpressure can lead to catastrophic failures.
Process Isolation
Valves are used to isolate parts of a process for safe maintenance or repair work. They allow specific sections of a pipeline or process to be shut off without affecting the rest of the operation.
Regulation of Process Conditions
Valves help maintain and regulate process conditions like temperature and pressure within desired limits. This is crucial for processes where specific conditions are required for optimal performance and product quality.
Direction of Flow
Certain types of valves, like check valves, are used to ensure fluid flows in one direction only, preventing backflow that could cause process disruptions or equipment damage.
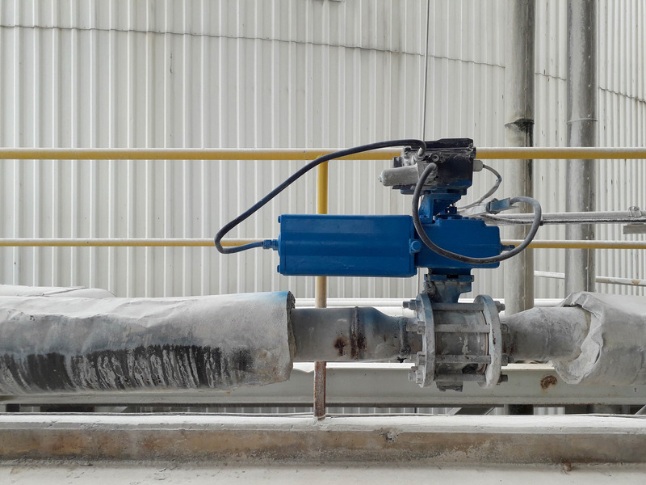
What is a Pneumatically Operated Valve?
A pneumatically operated valve is a type of control valve that uses air pressure to regulate the flow of fluid within a system. It consists of two main components: the valve body and a pneumatic pressure actuator.
The valve body is the part that comes into direct contact with the fluid. It has an opening and closing mechanism, often a disc, gate, or ball, which is moved to control the fluid flow.
The pneumatic actuator is the device that uses air pressure to drive the opening and closing mechanism of the valve. When air pressure is applied to the actuator, it causes a piston or diaphragm within the actuator to move. This movement is then transmitted to the opening and closing mechanism of the valve, causing it to open or close. When the air pressure is removed, a spring or the process fluid within pilot valve itself returns the valve to its original position.
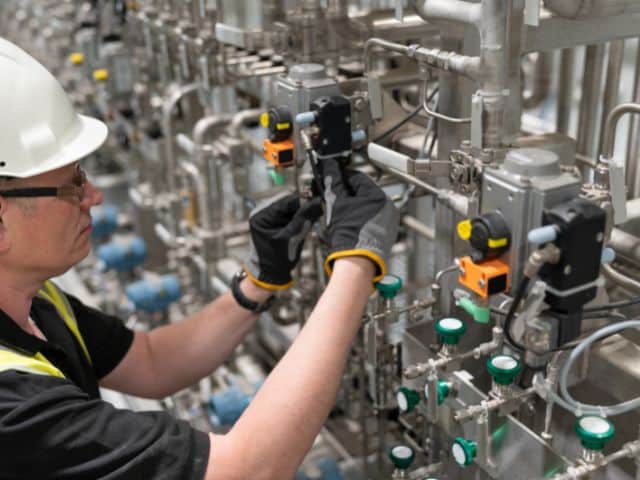
These valves can be designed for various functions, such as on-off control (where the valve is fully open or fully closed), or modulating control (where the valve can be partially opened or closed to regulate the flow rate). The specific design and function depend on the needs of the application.
Pneumatically operated valves are renowned for their reliability, speed, and safety. They are used in a wide range of industrial applications, from oil and gas to water treatment, and are a staple product in the offering of THINKTANK Control Valve.
how pneumatically operated valve works
Pneumatically operated valves function by using the power of compressed air to open, close, or regulate the flow of a fluid within a pipeline or a process.
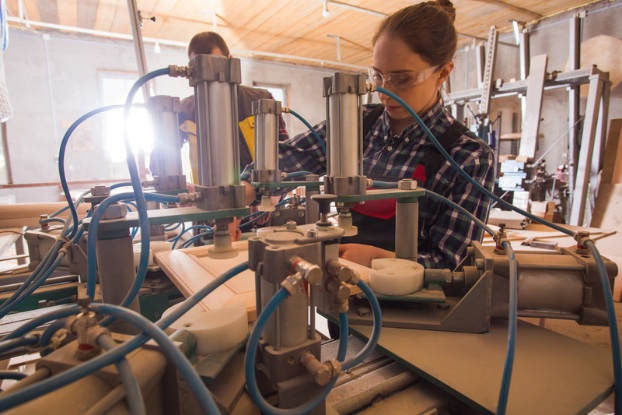
The working of these valves is centered around two main components: the valve body and the pneumatic actuator. The valve body is the component that directly interacts with the fluid, while the pneumatic actuator is responsible for moving the control element within the valve body.
The process begins when compressed air is introduced into the pneumatic system or actuator. The air pressure acts on a piston or a diaphragm within the actuator, causing it to move. This movement is then transferred to the control element within the valve body, typically a disc, a ball, or a gate.
In the case of a two-position actuation, the valve is either fully open or fully closed. When compressed air is applied, the valve opens by moving the control element away from the flow path. When the air supply is cut off, a spring within the actuator pushes the piston or diaphragm back to its original position, moving the control element back to block the air flow through path, thereby closing the valve.
In the case of modulating or throttling valves, the amount of air pressure applied to the actuator can be adjusted to position the control element at different levels within the flow path. This allows for precise directional control of the flow rate.
It’s important to note that the force exerted by the compressed air needs to be sufficient to overcome the process fluid pressure and any friction within the valve. This makes the selection of the appropriate actuator and control element crucial to the proper functioning of the valve.
At THINKTANK Control Valve, our pneumatically operated valves are designed with high-quality materials and engineering precision to ensure optimal performance and longevity.
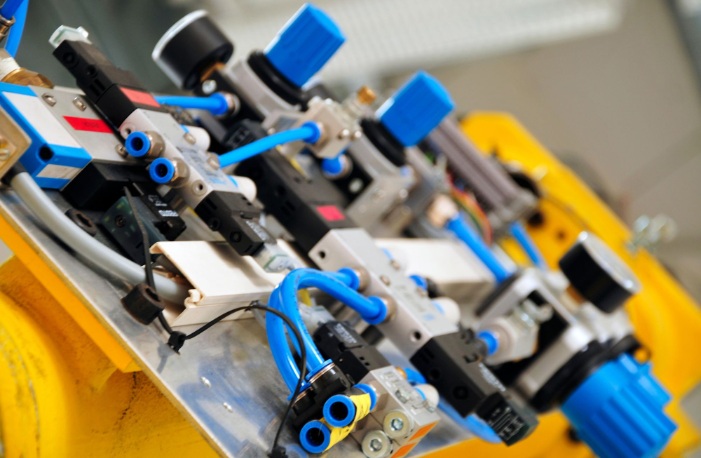
Different types of pneumatically operated valves
Pneumatically operated valves come in several types, each with its own unique design and application. Here are some common types:
Pneumatic Ball Valves: These valves feature a ball with a hole through the center, which rotates to control fluid flow. When the hole aligns with the flow path, the pneumatic valve is open, and when it’s perpendicular, the valve is closed. Pneumatic ball valves are known for their tight sealing and are commonly used for on-off control in applications that require a robust and reliable valve.
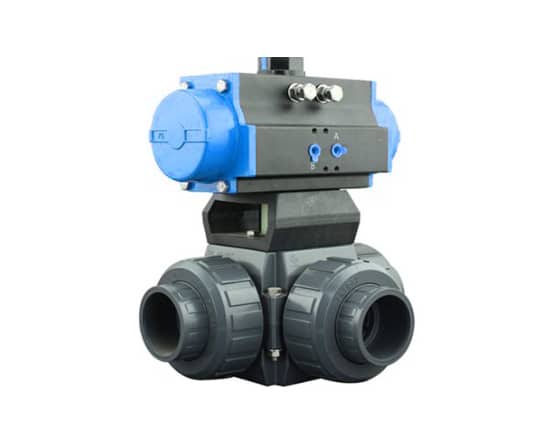
Pneumatic Butterfly Valves: In these valves, the flow of fluid is controlled by a disc that rotates on a shaft. When the disc is parallel to the flow, the valve is open, and when it’s perpendicular, the valve is closed. Butterfly valves are typically used in large-diameter pipelines and are valued for their low cost and light weight.
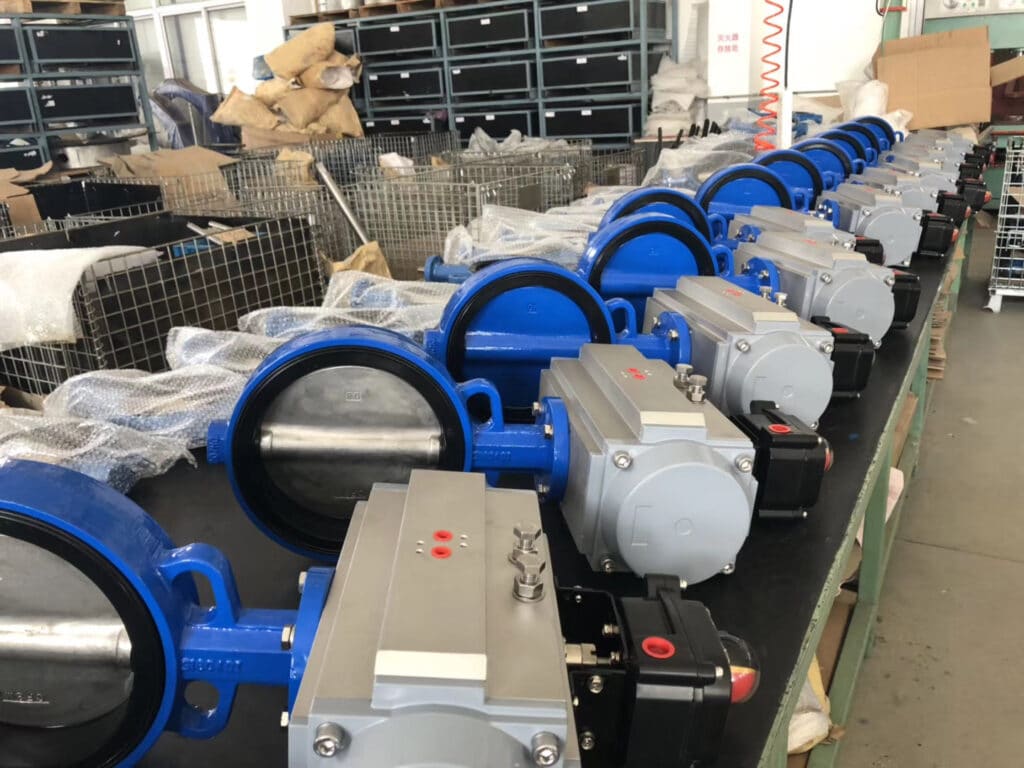
Pneumatic Globe Valves: These valves use a movable plug or disc assembly to regulate fluid flow. The plug is attached to a stem which is moved by the pneumatic actuator. Globe valves offer precise flow regulation, making them ideal for applications that have high flow and require accurate flow control.
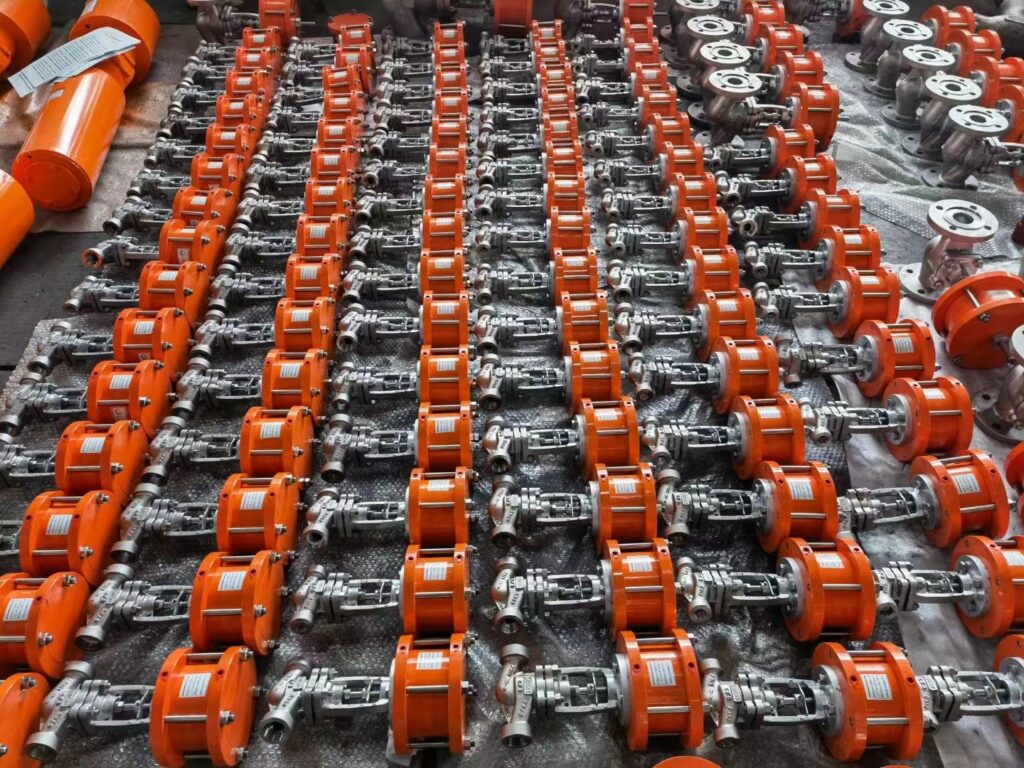
Pneumatic Gate Valves: These valves feature a gate that moves up or down to control fluid flow. When the gate is lifted, the valve is open, and when the gate is lowered, the valve is closed. Gate valves provide a robust seal when closed and are commonly used in applications where the valve is not frequently operated.
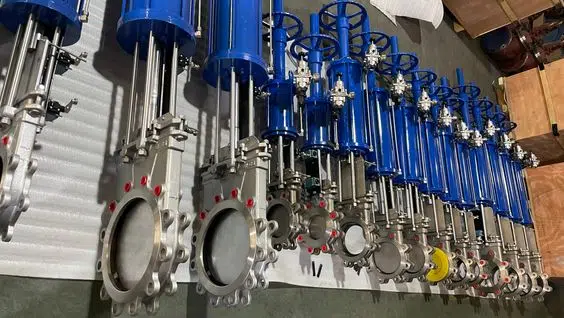
Pneumatic Diaphragm Valves: These valves use a flexible diaphragm that moves up or down to control fluid flow. Diaphragm valves are often used in applications that require a tight seal and are particularly suitable for handling corrosive or dirty fluids.
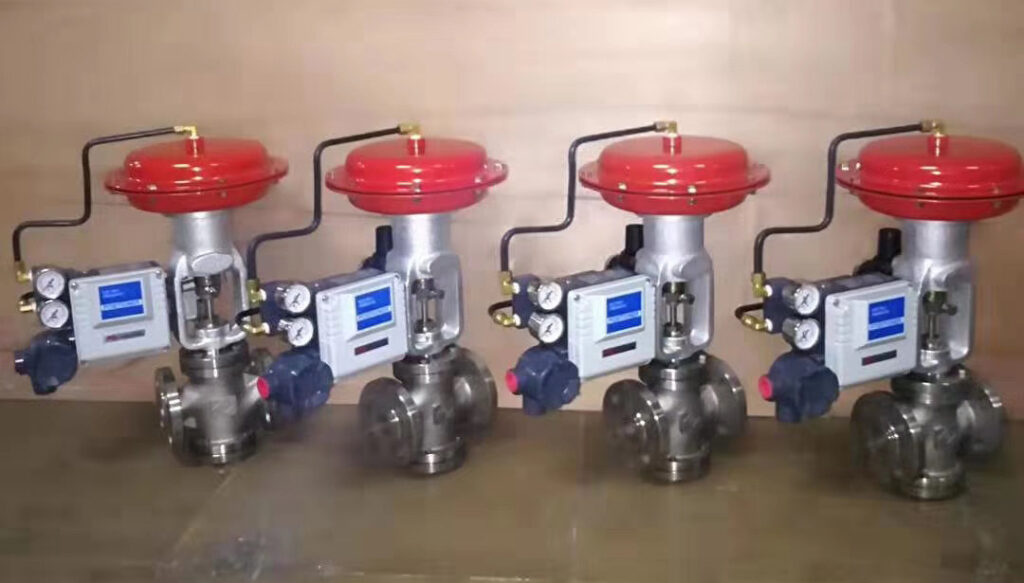
Pneumatic Control Valves: These valves are used in situations where the flow rate needs to be adjusted based on process conditions. They use a pneumatic actuator and a positioner to achieve precise control of the flow rate.
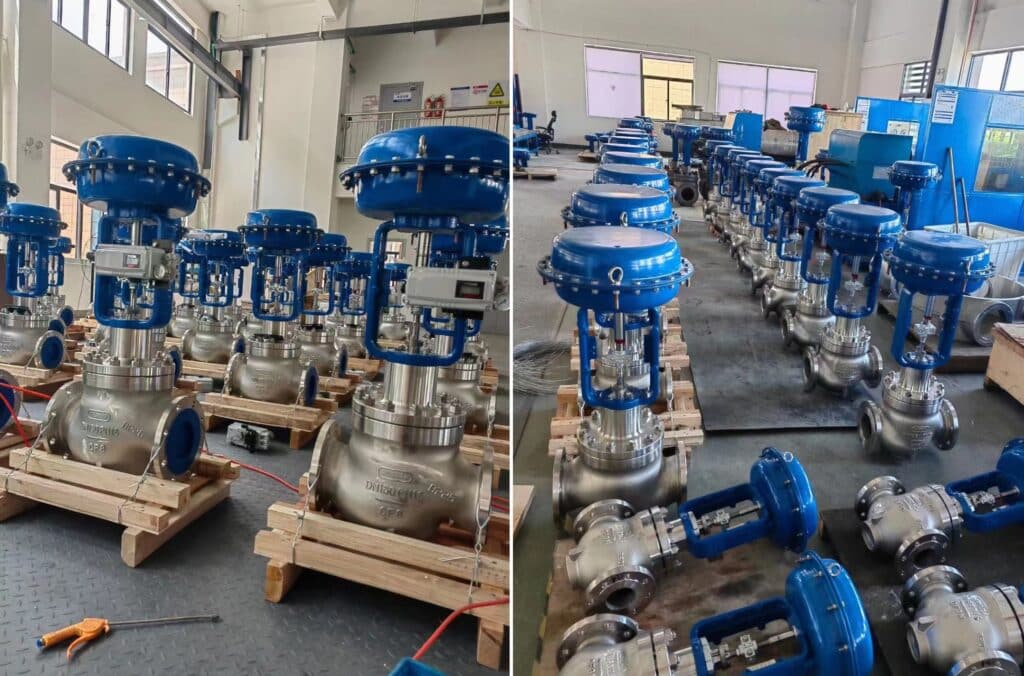
At THINKTANK, we offer a wide variety of configurations of pneumatically operated valves to meet the diverse needs of various industries. We are committed to providing high-quality products that deliver reliability and performance.
Benefits of Using Pneumatically Operated Valves
Energy Efficiency
Pneumatic systems use compressed air, which is abundantly available and can be easily compressed and stored. This makes pneumatically operated valves energy efficient, especially in large industrial operations.
Safety and Reliability
Pneumatically operated valves are inherently safe as they use air, a non-flammable and non-toxic medium. They are reliable and can withstand harsh operating conditions, making them suitable for critical industrial applications.
Speed of Operation
Pneumatic valves offer rapid response times, making them ideal for operations that require quick and frequent opening and closing of valves and ports. Their speed of operation can be easily adjusted by controlling the pressure of the compressed air.
Ease of Maintenance
Pneumatically operated valves have simple designs and are easy to maintain. The actuator components are typically housed in a sealed unit, which protects them from external contaminants. In the event of a malfunction, the faulty components can often be replaced without removing the entire valve from the pipeline.
Cost-Effectiveness
While the initial cost of pneumatically operated valves might be higher than other types of valves, their durability, low maintenance requirements, and energy efficiency can result in lower total cost of ownership over the long term.
Versatility
Pneumatically operated valves can be used with a variety of control options and can easily be integrated into automated systems. They are suitable for a wide range of applications, from simple on-off control to more complex modulating control features.
Applications of Pneumatically Operated Valves
Pneumatically operated valves are used in a wide variety of industries due to their versatility, reliability, and efficiency. Here are some of the key applications:
Oil and Gas Industry:
Pneumatically operated valves are used extensively in the oil and gas industry, controlling the flow of oil and gas in pipelines, refining processes, and storage systems. They are often used in safety systems to provide emergency shut-off in case of abnormal conditions.
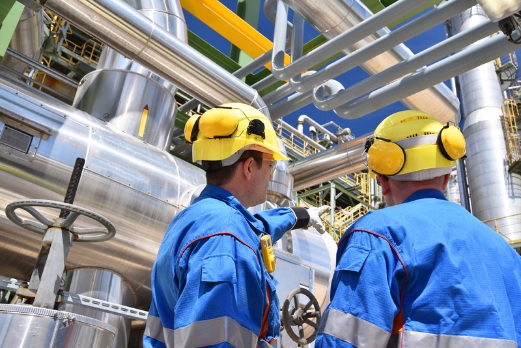
Chemical Processing:
In chemical plants, these stainless steel valves regulate the flow of a wide variety of chemicals. Their ability to withstand harsh conditions and corrosive substances makes them a popular choice.
Water Treatment:
Pneumatically operated valves are used in water treatment facilities for controlling the flow of water and other substances during various stages of treatment. Their reliability and ease of automation make them ideal for this application.
Food and Beverage Industry:
These valves are used in various stages of food and beverage production, from ingredient mixing to packaging. They are often chosen for their ability to be cleaned in place (CIP) and sterilized in place (SIP), which are crucial in maintaining hygiene standards.
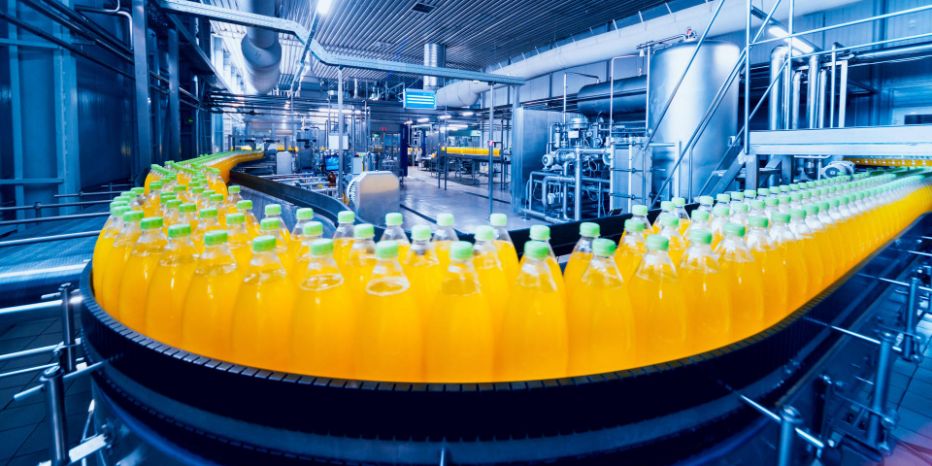
Pharmaceutical Industry:
In pharmaceutical manufacturing, pneumatically operated valves are used to control the flow of ingredients, solutions, and finished products. Their ability to offer precise control and meet stringent hygiene standards makes them suitable for this industry.
Power Generation:
In power plants, these valves are used to control the flow of steam, water, and other fluids. They are often part of safety systems, helping to prevent overpressure situations and ensure the safe operation of the plant.
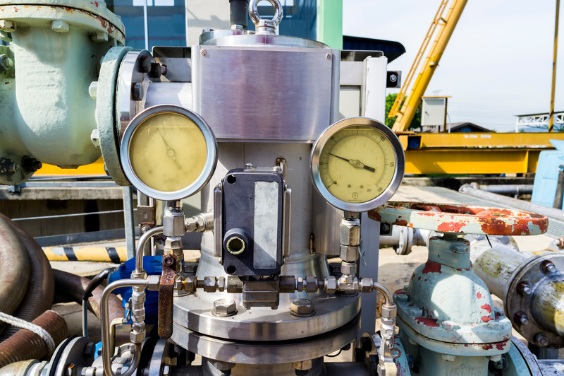
Specific tasks within those industries best suited for pneumatically operated valves
THINKTANK provides pneumatically operated valves are highly versatile and can perform a wide range of tasks within various industries. Here are some specific tasks best suited for these valves:
- Emergency Shutdown Systems in Oil and Gas Industry: These systems are designed to minimize the consequences of emergency situations, such as equipment failures or sudden pressure changes. Pneumatically operated valves are often used in these systems due to their reliability and quick response times.
- Flow Regulation in Chemical Processing: The manufacture of chemicals often involves the careful control of fluid flow rates. Pneumatic control valves, with their precise modulating capabilities, are ideal for this task.
- Wastewater Treatment: In wastewater treatment plants, valves are needed to control the flow of water and sludge through various stages of the treatment process. Pneumatically operated valves are often chosen for their reliability and ease of automation.
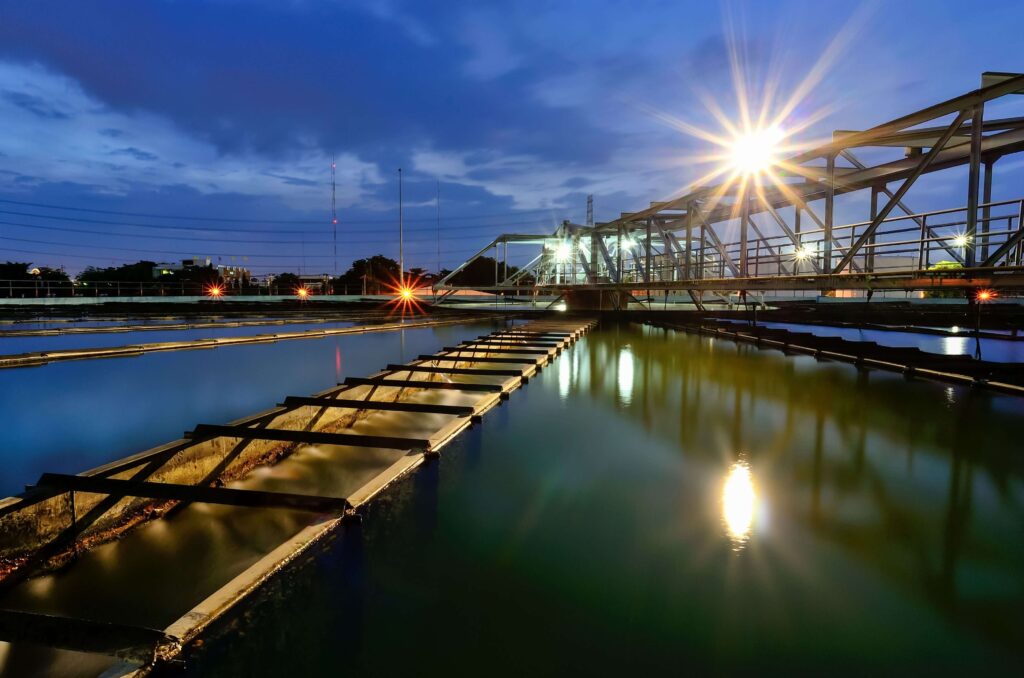
- Clean-in-Place (CIP) Systems in the Food and Beverage Industry: CIP systems are used to clean the interior surfaces of pipes and vessels without disassembly. Pneumatically operated valves are ideal for these systems due to their ability to be easily automated and their compatibility with the cleaning solutions used.
- Fluid Handling in Pharmaceutical Manufacturing: The production of pharmaceuticals often involves the handling of fluids that must be kept sterile. Pneumatically operated diaphragm valves are often used for this task, as they can be thoroughly cleaned and sterilized.
- Steam Control in Power Generation: In power plants, the flow of steam needs to be carefully controlled to ensure efficient power generation. Pneumatic control valves are often used for this task due to their ability to withstand the high temperatures and pressures involved.
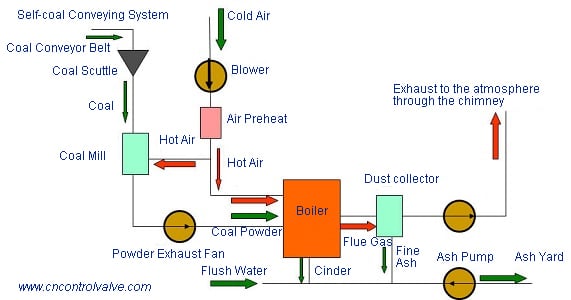
How to Choose the Right Pneumatically Operated Valve
Choosing the right pneumatically operated valve is crucial to ensure the efficient and safe operation of your industrial processes. Here are some key factors to consider:
- Type of Fluid: The nature of the fluid being controlled is an important factor in choosing a valve. Consider properties like viscosity, corrosiveness, temperature, and whether the fluid is a liquid, gas, or slurry. Different valve types and materials are suited to different kinds of fluids.
- Operating Conditions: Consider the operating pressure and temperature. The valve and its components must be able to withstand these conditions without degrading over time.
- Flow Requirements: Think about your flow control needs. Do you need an on-off valve, or do you need to precisely control the flow rate? Different valve types offer different levels of control.
- Actuation Speed: How quickly do you need the valve to open or close? The speed of a pneumatically operated valve can be adjusted by controlling the air pressure, but some types of valves naturally operate faster than others.
- Safety Requirements: In some applications, safety is a major concern. For example, in an emergency shutdown system, a fail-safe valve that automatically closes (or opens, depending on the application) when the air supply is cut off might be necessary.
- Maintenance and Cost: Consider the maintenance requirements of the valve and the total cost of ownership, including initial cost, operating cost, maintenance cost, and the cost of potential downtime for repairs or replacements.
- Regulatory and Industry Standards: Make sure the valve meets any applicable regulatory or industry standards, especially in industries like food and beverage or pharmaceuticals where hygiene and sterility are crucial.
Importance of quality and durability in valve selection
The quality and durability of a valve are paramount when selecting a valve for any industrial process. Here’s why:
- Operational Efficiency: High-quality valves operate efficiently and consistently, providing accurate control over fluid flows. This ensures that processes run smoothly and effectively, with minimal interruptions.
- Longevity and Cost Savings: Durable valves that can withstand the rigors of industrial use can operate effectively for many years, reducing the need for frequent replacements. This results in significant cost savings over the life of the valve.
- Safety: Valves are often integral parts of safety systems in industrial processes. High-quality, reliable valves are necessary to ensure these safety systems function correctly when needed, protecting both personnel and equipment.
- Reduced Downtime: Quality valves are less likely to fail or require maintenance, leading to reduced downtime and more continuous operation. This can significantly improve the productivity and profitability of an industrial operation.
- Compliance: In many industries, valves need to comply with specific standards or regulations. High-quality valves are designed and manufactured to meet these requirements.
- Environmental Impact: Durable valves that last longer help to reduce waste and the use of resources associated with manufacturing and disposing of valves. This can contribute to a company’s environmental sustainability goals.
Why Choose THINKTANK Control Valve for Your Pneumatically Operated Valve Needs
Here are some reasons you Choosing THINKTANK (cncontrolvalve.com) for your pneumatically operated valve needs comes with a host of advantages.
- High-Quality Products: At THINKTANK, we prioritize quality above all else. Our pneumatically operated valves are designed and manufactured to the highest standards, ensuring that they perform reliably and effectively in your processes.
- Broad Product Range: We offer a wide variety of pneumatically operated valves to meet the diverse needs of various industries. Whether you need a simple on-off valve or a complex control valve, we have the right product for you.
- Expertise and Experience: With years of experience in the industry, our team of experts understands the technical intricacies of pneumatically operated valves. We can provide valuable advice and assistance in selecting the right valve for your specific application.
- Customer Service: We are committed to providing exceptional customer service. Our team is always ready to answer your questions and resolve any issues that may arise.
- Innovation: At THINKTANK, we continually strive to innovate and improve our products. We invest in research and development to ensure that we stay at the forefront of valve technology.
- Value for Money: While we never compromise on quality, we also strive to offer our products at competitive prices. This ensures that you get great value for your investment.
Customer testimonials
Conclusion
In conclusion, pneumatically operated valves play a crucial role in a wide variety of industries, offering benefits like energy efficiency, safety, speed of operation, ease of maintenance, cost-effectiveness, and versatility. Understanding the different types of pneumatically operated valves, their benefits, applications, and how to select the right valve for your specific needs can significantly enhance your industrial processes.
Whether you’re in the oil and gas industry, chemical processing, water treatment, food and beverage, pharmaceutical, or power generation industry, these valves are a critical component to ensure smooth, efficient, and safe operations.
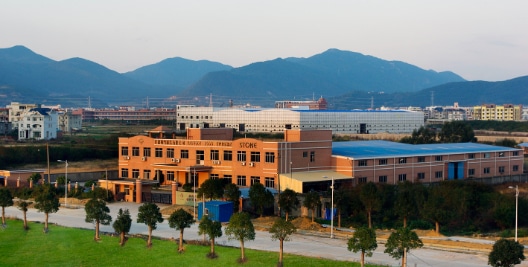
At THINKTANK (China Control Valve), we offer a broad range of high-quality, durable pneumatically operated valves tailored to meet the diverse needs of these industries. Our team of experts is committed to providing you with the best possible solutions for your specific application, coupled with exceptional customer service.
If you have any questions about pneumatically operated valves, or if you need assistance in selecting the right valve for your needs, please don’t hesitate to contact us. We invite you to visit our website at https://cncontrolvalve.com to learn more about our offerings and how we can help you optimize your industrial processes. Trust THINKTANK for all your pneumatically operated valve needs!