In this post, we will explore the importance of control valve testing and inspection in ensuring optimal performance in industrial process control systems. By providing a comprehensive overview of the preparation, external and internal inspection, valve testing, and documentation involved in control valve maintenance, we aim to demonstrate the level of professionalism and expertise that valve distributors can offer to their customers. Our goal is to educate and inform industrial valve distributors on the best practices for maintaining control valves and ensuring reliable process control.
Our goal is to educate and inform industrial valve distributors on the best practices for maintaining control valves and ensuring reliable process control. Not only for butterfly valves, steel gate valves, cast iron plug valves, plug valves, and control valves, but also for cast iron plug valves, cast iron gate valves, angle valves, cast iron gate valves, pressure relief valves, cast iron check valves, resilient seated valves, steel valves, alloy valves, and ball valves.
This post will provide valuable information and insights for those looking to enhance their understanding of control valve testing and inspection and its role in maximizing performance and reliability.
The importance of control valve testing and inspection
Control valves are critical components of any process control system, as they regulate the flow of fluids, gases, and other materials. Their performance is essential for maintaining efficient and safe operation of industrial processes, and any malfunction or failure can lead to production downtime, safety hazards, and increased costs.
To ensure optimal control valve performance, regular testing and inspection are necessary. The importance of control valve testing and inspection can be summarized as follows:
- Safety: Control valves play a critical role in maintaining safety in process industries. Any malfunction in a control valve can result in a safety hazard, causing damage to equipment and endangering personnel. Regular testing and inspection can help identify potential safety issues and prevent accidents.
- Performance: The performance of control valves can be affected by various factors such as wear and tear, corrosion, and the build-up of debris. Regular testing and inspection can detect any issues that may impact the performance of control valves, ensuring that they operate efficiently and as designed.
- Efficiency: Control valves are essential for maintaining efficient operations in process industries. Any inefficiency can lead to increased energy consumption and production downtime. Regular testing and inspection can identify any issues that may impact the efficiency of control valves, allowing for timely maintenance and repairs.
- Compliance: Process industries are subject to various regulations and standards, and control valves must meet the required standards. Regular testing and inspection can ensure that control valves comply with regulatory requirements and industry standards.
- Cost savings: Regular testing and inspection can help identify potential issues with control valves early, allowing for timely maintenance and repairs. This can prevent costly production downtime, reduce maintenance costs, and extend the lifespan of control valves.
Control Valve Testing Standards
It’s important to choose control valves that meet the appropriate standards for your specific application to ensure optimal performance and reliability. Additionally, regular testing and inspection can help identify potential problems before they cause serious damage to the system.
Here are some of the most commonly used testing standards for control valves:
- API 598: This is an American Petroleum Institute standard that covers valve inspection and testing.
- ISO 5208: This is an international standard that covers the testing of control valves.
- MSS SP-61: This is a standard developed by the Manufacturer’s Standardization Society (MSS) that covers the testing of control valves.
- NAMUR NE 107: This is a standard developed by the North American Instrument Manufacturers Users’ Roundtable (NAMUR) that covers the interface between control valves and process control systems.
Control Valve Design Standards
The control valve design standards provide guidelines for the materials of construction, dimensions, connections, and performance requirements for control valves.
Here are some of the most commonly used design standards for control valves:
- ISO 5752 Standard
- This is an international standard that defines the dimensions and connection sizes for control valves.
- It provides guidelines for the design of control valves, including the dimensions and connections of the valve body, bonnet, stem, and actuator.
- API 6D Standard
- This is an American Petroleum Institute standard that covers the design and manufacture of pipeline and pipeline valve components.
- It provides guidelines for the design and manufacture of control valves, including the materials of construction, valve body and bonnet design, and actuator design.
- ASME B16.34 Standard
- This is an American Society of Mechanical Engineers standard that covers valve pressure-temperature ratings.
- It provides guidelines for the design of control valves, including the pressure-temperature ratings, materials of construction, and valve body and bonnet design.
- MSS SP-67 Standard
- This is a standard developed by the Manufacturer’s Standardization Society (MSS) that covers the design of control valves.
- It provides guidelines for the design of control valves, including the materials of construction, valve body and bonnet design, and actuator design.
- NAMUR NE 107 Standard
- This is a standard developed by the North American Instrument Manufacturers Users’ Roundtable (NAMUR) that covers the interface between control valves and process control systems.
- It provides guidelines for the design of control valves, including the communication between the valve and process control system, response time, and accuracy.
Valve Testing Procedure PDF
It’s important to follow a comprehensive testing procedure to ensure that control valves are functioning properly and provide accurate control of the process. By regularly testing control valves, you can identify potential problems before they cause serious damage to the system.
Here is a comprehensive guide for the control valve test procedure (you can also click here to download the pdf version):
I. Preparation:
- Gather all necessary tools and equipment, such as a multimeter, torque wrench, pressure gauge, and valve position indicator.
- Familiarity with the valve specifications, such as the pressure range, flow rate, and materials of each part.
- Review safety procedures and make sure that the system is properly isolated and depressurized before starting the testing.
II. External Inspection
- Check external inspection, including valve body, bonnet, stem, and actuator.
- Check the signs of damage or wear to look for during the inspection.
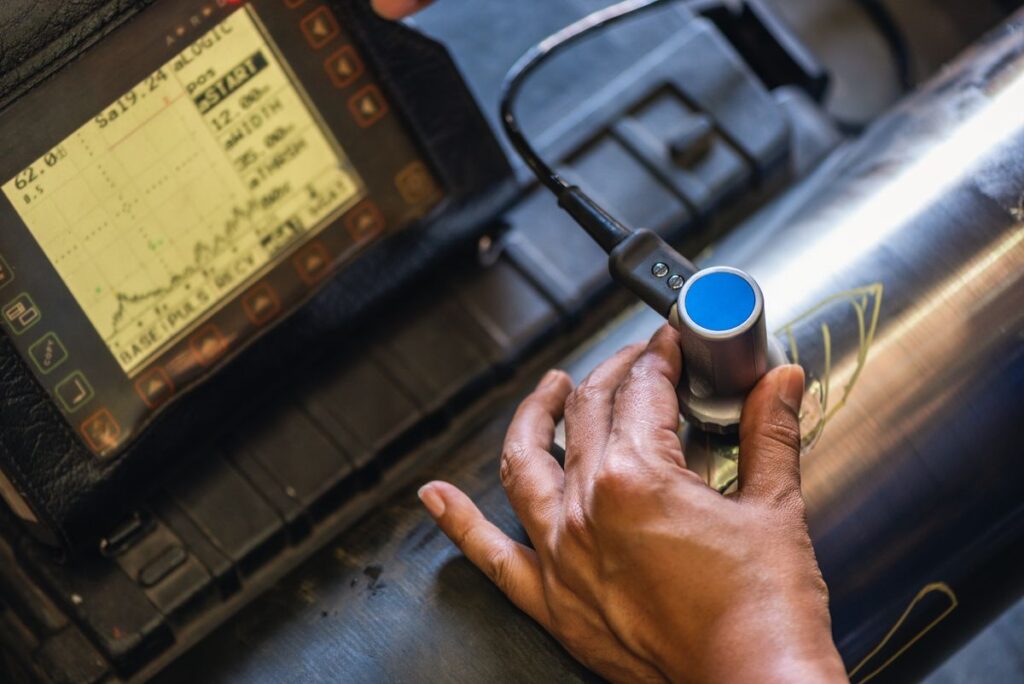
III. Internal Inspection
- Check the steps involved in internal inspection, including removal of the bonnet and inspection of internal components.
- Check the signs of damage or wear to look for during the inspection.
IV. Leak Test
- Close the valve and apply pressure to the system.
- Check for leaks in the body and bonnet using a pressure gauge or leak detection equipment.
- If a leak is detected, repair or replace the valve.
V. Operational Characteristics Test
- Open the valve and measure the pressure drop across the valve.
- Measure the flow rate through the valve.
- Record the response time of the valve to a control signal.
- Compare the results to the specifications and make any necessary adjustments.
VI. Control Signal Test
- Apply a control signal to the valve and verify that it is functioning properly.
- Check the valve’s response to the control signal and make sure that the actuator is properly positioning the valve.
- If the control signal is not functioning properly, repair or replace the valve.
VII. Shutoff Capability Test
- Slowly close the valve and measure the pressure drop across the valve.
- Compare the results to the specifications and make sure that the valve is able to shut off completely.
VIII. Documentation
- Record the results of the testing in a logbook.
- Document any repairs or replacements that were made during the testing.
- Make note of any issues that need to be addressed in the future.
What is the difference between API 598 and ISO 5208?
What does API 598 mean?
API 598 is a standard developed by the American Petroleum Institute (API) that outlines the guidelines for the inspection and testing of valves. The purpose of this standard is to ensure that valves are functioning correctly and provide accurate control of the process. The standard covers various aspects of valve inspection and testing, including visual inspection, pressure testing, and functional testing.
- Visual Inspection: The first step of the valve inspection process is a visual inspection. This includes a thorough examination of the valve body, bonnet, stem, and actuator to identify any signs of damage, wear, or corrosion.
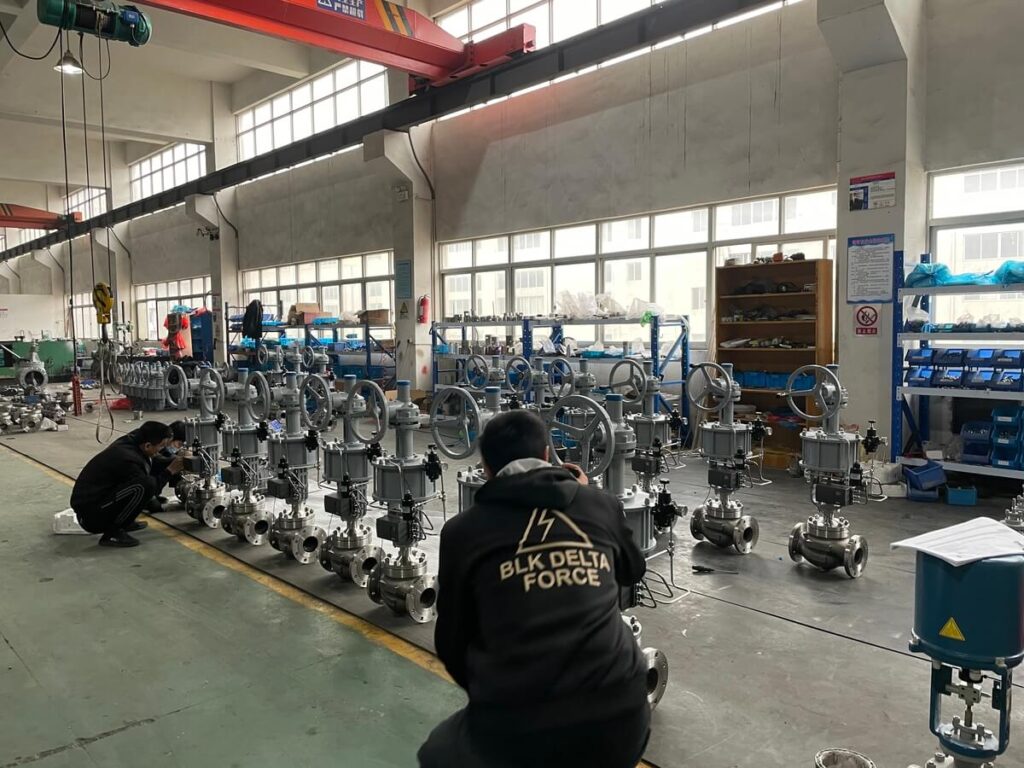
- Pressure Testing: Pressure testing is an important aspect of valve testing to verify the valve’s ability to withstand the pressure required for its intended use. The valve is subjected to air or water pressure at a level of at least 1.5 times the maximum operating pressure of the valve. The test is performed to detect any leaks in the valve body or bonnet.
- Functional Testing: The functional testing aspect of API 598 is performed to verify the valve’s proper operation and control. This includes evaluating the valve’s response time, control signal, and shutoff capability. The goal of this test is to ensure that the valve is functioning correctly and providing accurate control of the process.
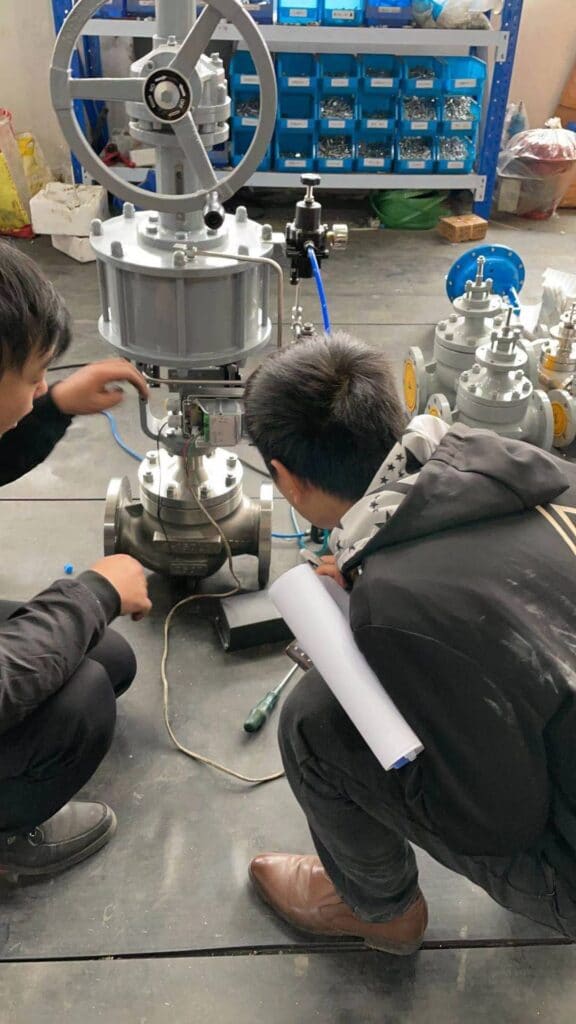
It is crucial to follow the guidelines set forth in API 598 to ensure that valves are functioning correctly and providing accurate control of the process. The results of the inspection and testing should be documented and kept on file for future reference. By following the standard, valve manufacturers, distributors, and users can be confident that the valves they use meet the highest quality standards.
What does ISO 5208 Valve Test Standard mean?
ISO 5208 is an international standard that provides guidelines for the testing of control valves. The purpose of this standard is to ensure that control valves are functioning correctly and provide accurate control of the process. The standard covers various aspects of control valve testing, including performance testing, functional testing, and high-pressure testing.
- Performance Testing: Performance testing is an important aspect of control valve testing to verify the valve’s ability to perform its intended function. The test is performed to evaluate the valve’s flow characteristics, such as flow rate, pressure drop, and accuracy of control. The results of the performance testing are compared to the valve’s specifications to verify its compliance.
- Functional Testing: The functional testing aspect of ISO 5208 is performed to verify the valve’s proper operation and control. This includes evaluating the valve’s response time, control signal, and shutoff capability. The goal of this test is to ensure that the valve is functioning correctly and providing accurate control of the process.
- High-Pressure Testing: High-pressure testing is performed to verify the valve’s ability to withstand the pressure required for its intended use. The valve is subjected to a specified high pressure and held for a specified time to verify its ability to withstand the pressure without leaking.
How are Valves Tested?
Valves are tested to ensure that they are functioning properly and providing accurate control of the process.
The testing process typically includes a combination of visual inspection, pressure testing, and functional testing. During the visual inspection, the valve is examined for signs of damage, wear, or corrosion.
Pressure testing is performed to verify the valve’s ability to withstand the pressure required for its intended use.
Functional testing is performed to verify the valve’s proper operation and control, including evaluating the valve’s response time, control signal, and shutoff capability.
The results of the testing are documented and used to identify any necessary repairs or replacements to ensure optimal valve performance.
What are the API, ISO, MSS Codes and Standards for Valve Inspection and Testing
There are several codes and standards that outline the guidelines for valve inspection and testing, including:
- American Petroleum Institute (API) Standards: API standards, such as API 598 for control valves and API 6D for pipeline valves, provide guidelines for the inspection and testing of valves. These standards cover aspects such as visual inspection, pressure testing, and functional testing.
2. International Organization for Standardization (ISO) Standards: ISO standards, such as ISO 5208 for control valves, provide international guidelines for the testing of valves. These standards cover aspects such as performance testing, functional testing, and high-pressure testing.
3. Manufacturers Standardization Society (MSS) Standards: MSS standards, such as MSS SP80 for bronze gate, globe, angle, and check valves, provide guidelines for the testing and inspection of specific types of valves. These standards cover aspects such as visual inspection, pressure testing, and functional testing.
Valve Inspection Checklist PDF
Valve inspection is an important aspect of ensuring the safe and reliable operation of industrial valves. A thorough inspection of the valve can identify potential issues before they cause serious damage to the system and help to ensure the valve is functioning properly. This checklist provides a comprehensive overview of the items that should be considered when performing a valve inspection.
- Physical Inspection: A visual inspection of the valve should be performed to check for any physical damage, corrosion, or other issues. The valve body, stem, and other components should be inspected for any signs of wear or damage.
2. Testing: The valve should be tested to verify its proper operation and control. This may include pressure testing, functional testing, and other types of tests as specified by the relevant standards.
3. Calibration: The valve should be calibrated to ensure that it is providing accurate control of the process. This may include adjusting the valve’s settings or using specialized equipment to calibrate the valve’s operation.
4. Documentation: The results of the valve inspection, testing, and calibration should be documented and kept on file for future reference. This documentation can be used to track the valve’s performance over time and to identify any potential issues that need to be addressed.
5. Maintenance: Any maintenance or repair work that is required as a result of the valve inspection should be performed in a timely manner. This may include replacing worn or damaged components, adjusting the valve’s settings, or performing other types of maintenance as needed.
Third Party Inspection(TPI) for Valves
- Preparation:
- TPI will review the valve specifications and requirements to ensure that the inspection is performed in accordance with the customer’s needs.
- TPI will gather all necessary tools and equipment, such as a multimeter, torque wrench, pressure gauge, and valve position indicator.
- TPI will review the safety procedures and make sure that the system is properly isolated and depressurized before starting the inspection.
- Visual Inspection:
- TPI will perform a visual inspection of the valve to identify any signs of damage, wear, or corrosion.
- TPI will include a review of the valve body, bonnet, stem, and actuator.
- TPI will document any issues identified during the visual inspection.
- Pressure Testing:
- TPI will perform a pressure test to verify the valve’s ability to withstand the pressure required for its intended use.
- The valve will be subjected to air or water pressure at a level of at least 1.5 times the maximum operating pressure of the valve.
- TPI will check for leaks in the valve body and bonnet using a pressure gauge or leak detection equipment.
- TPI will document the results of the pressure test.
- Functional Testing:
- TPI will perform a functional test to verify the valve’s proper operation and control.
- The test will include a review of the valve’s response time, control signal, and shutoff capability.
- TPI will compare the results of the functional test to the valve’s specifications.
- TPI will document the results of the functional test.
- Documentation:
- TPI will provide a detailed report of the inspection results, including any issues identified during the inspection.
- The report will include recommendations for any repairs or replacements that may be necessary to bring the valve into compliance with the specifications.
- TPI will provide a certificate of inspection, indicating that the valve has been inspected in accordance with the customer’s requirements.
This is a comprehensive guide to Third Party Inspection for valves. By having a third-party inspection company perform an inspection, valve brands, distributors, agents, EPCs, and end-users can be confident that the valves they purchase meet the highest quality standards.
In conclusion, professional control valve testing and inspection are essential for maintaining optimal performance and safety in process industries. Regular testing and inspection can help identify potential issues early, prevent accidents, improve efficiency, and ensure compliance with regulatory requirements and industry standards. By investing in professional testing and inspection, companies can reduce maintenance costs, extend the lifespan of control valves, and minimize the risk of production downtime. Overall, control valve testing and inspection are critical components of any process control system, and companies should prioritize these activities to ensure the long-term success of their operations. Should you have any questions, welcome to contact THINKTANK for a free consultation.