As a professional valve manufacturer in industrial applications, we understand the role of control valves in your process. Control valves play a pivotal role in regulating the flow rate, pressure, or level of a fluid in a system. They are the final controlling elements, affecting the system output directly of your overall operation. This means control valve problems can be a significant impediment to your process flow. With our expertise, we’ll guide you through these challenges, outlining material and design complications, and offering comprehensive solutions for control valve problems.
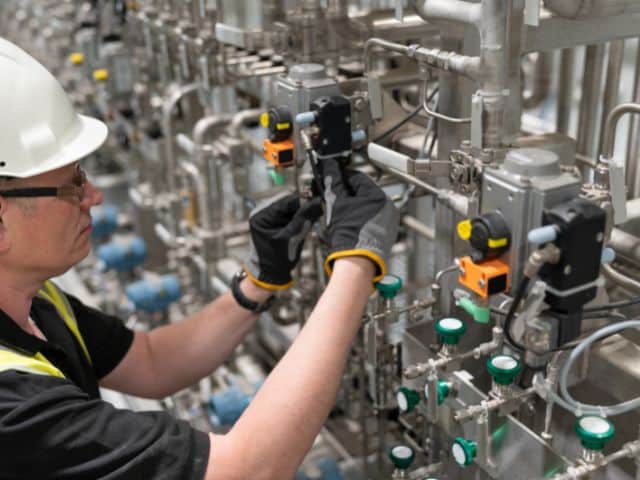
Control Valve Material Challenges: Selection and Considerations
Control valve materials play a vital role in the valve’s performance, durability, and ability to withstand different operating conditions. Selection of these materials is often determined by factors such as fluid characteristics, operating temperature, pressure, and the specific requirements of the application. Here, we discuss some of the most commonly used materials in control valve construction.
Valve Body Materials
The body of a control valve is typically made of robust, corrosion-resistant materials. The most commonly used materials include:
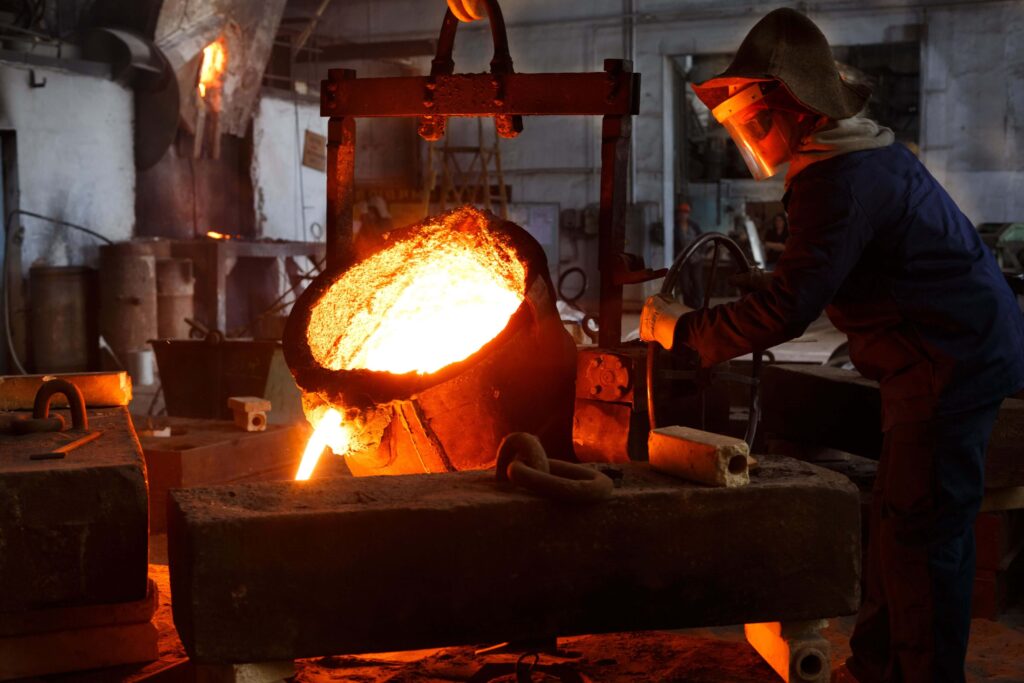
Cast Iron
Cast iron is a cost-effective material often used for control valve bodies. It has good castability, excellent machinability, and high wear resistance. However, it is less suitable for high-pressure and high-temperature applications.
Carbon Steel
Carbon steel is another popular material for valve bodies due to its high tensile strength and durability. It is suitable for high-pressure and high-temperature applications. However, it can be susceptible to corrosion, especially in environments with corrosive fluids.
Stainless Steel
Stainless steel, particularly types 304 and 316, is used in valve body construction for its excellent corrosion resistance. It is particularly suitable for applications involving aggressive fluids or environments.
Trim Materials
The trim of a control valve includes parts such as the stem, plug, and seat. These components are often exposed to high wear and tear, so they’re typically made from durable and corrosion-resistant materials. Common trim materials include:
Stainless Steel
Stainless steel is often used for valve trims due to its good wear resistance and excellent corrosion resistance. It is suitable for many general applications.
Hardened Stainless Steel
Hardened stainless steel, often achieved through processes like nitriding or hard-facing, is used for trim components in more demanding applications. The hardened surface provides increased resistance to wear and erosion.
Bronze
Bronze is used in some trim components, especially in marine and low-pressure applications, due to its good resistance to wear and corrosion.
Sealing Materials
Seals are critical in preventing leakage from the valve. They need to be flexible and durable, and their material selection often depends on the temperature and nature of the fluid. Common sealing materials include:
PTFE (Teflon)
PTFE, or Teflon, is commonly used as a sealing material due to its wide temperature range and excellent chemical resistance. It’s suitable for many corrosive applications.
EPDM
EPDM (Ethylene Propylene Diene Monomer) is a type of synthetic rubber used as a sealing material in many applications due to its good flexibility, heat resistance, and compatibility with a variety of fluids.
Control Valve Design Challenges: Optimal Performance and Flow Control
Understanding the design challenges of control valves is essential to achieving optimal performance. Here, we delve into the key factors.
Control Valve Sizing: Precision is Key
Control valve sizing is paramount in ensuring proper flow control. An undersized valve can restrict flow, causing process inefficiency, while an oversized valve may lead to unstable control and premature wear.
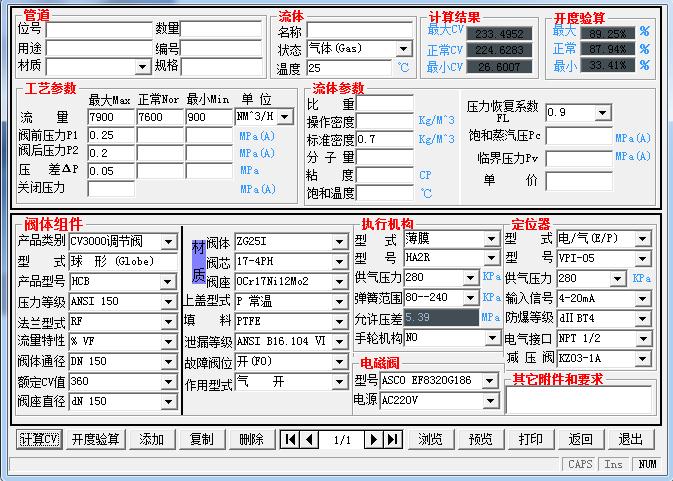
Valve Trim Design: Balancing Flow and Resistance
The design of the valve trim, including the plug, seat, and stem, can also present challenges. A poorly designed trim can result in excessive noise, vibration, and cavitation, which can cause damage over time. It’s a delicate balance between managing flow capacity and resisting the harmful effects of fluid dynamics.
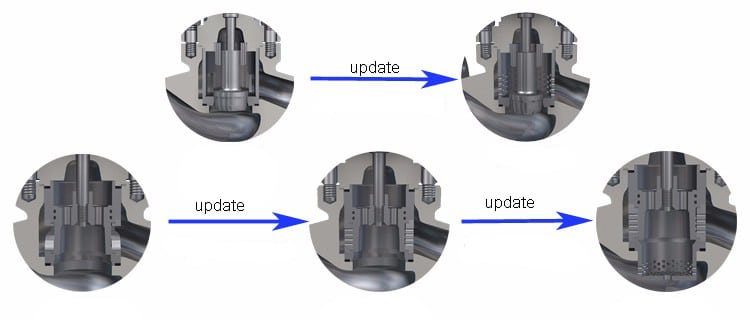
Actuator Selection: Power and Control
Choosing the correct actuator is another critical design challenge. The actuator must be powerful enough to operate the valve under maximum process conditions, yet precise enough to allow for accurate control.
What are the problems with control valves?
Control valves can encounter a variety of problems due to numerous reasons, such as mechanical wear and tear, improper valve selection, or incorrect installation. Here are some common problems with control valves.
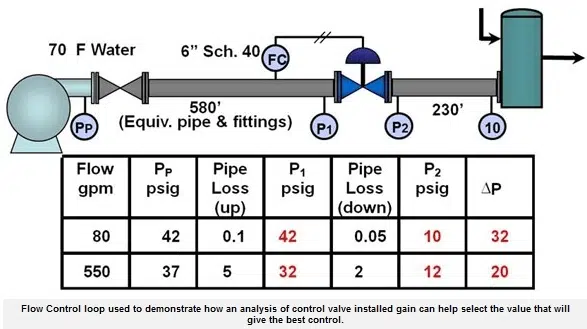
Problem: Valve Leaks
Control valve leaks are a common issue in industrial process control systems. These leaks not only affect the overall efficiency of a system but can also lead to safety concerns, depending on the nature of the fluid involved.
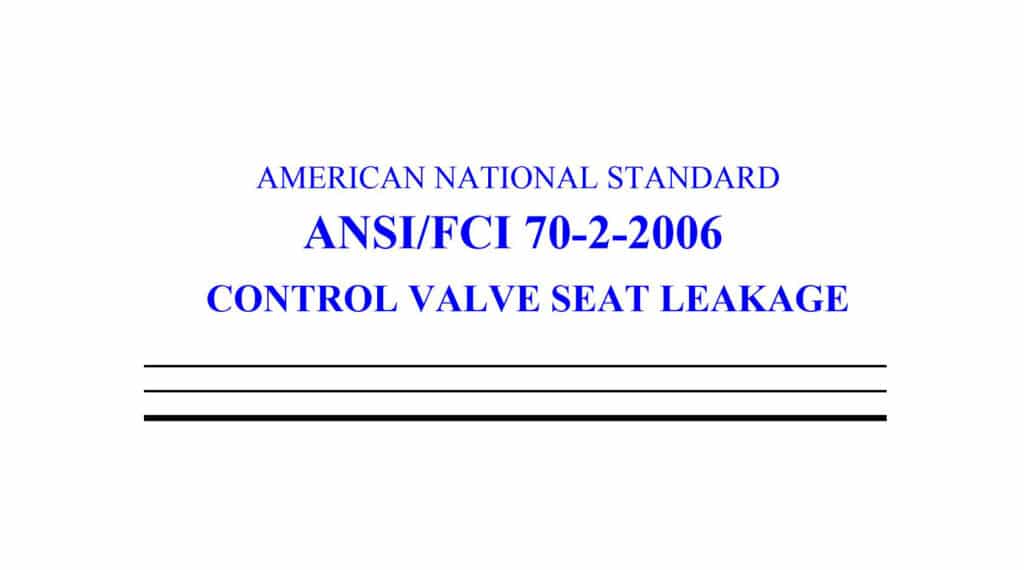
Problem: Valve Noise and Vibration
In the world of process control, noise and vibration from a control valve can be more than just a nuisance-they can be indicative of significant operational issues. This problem should never be overlooked, as it can lead to severe damage and a decrease in overall system efficiency. Excessive noise or vibration from a control valve is often a sign of cavitation or flow turbulence. Resolving this requires a review of the valve trim design or possibly resizing the valve.
The Causes Behind Valve Noise and Vibration
Noise and vibration in control valves primarily stem from the violent energy fluctuations associated with the fluid flow within the system. These fluctuations can be due to:
- Flow Turbulence
Turbulent flow is a complex fluid dynamic phenomenon characterized by chaotic, disordered fluid motion. In control valves, turbulent flow can generate substantial vibration and noise, causing discomfort and potentially damaging the valve or connected piping.
- Cavitation
Cavitation in control valves refers to the formation and collapse of vapor bubbles within the fluid, usually caused by drastic pressure changes. When these bubbles collapse, they cause shock waves that create noise and vibration, eventually leading to physical damage to the valve components.
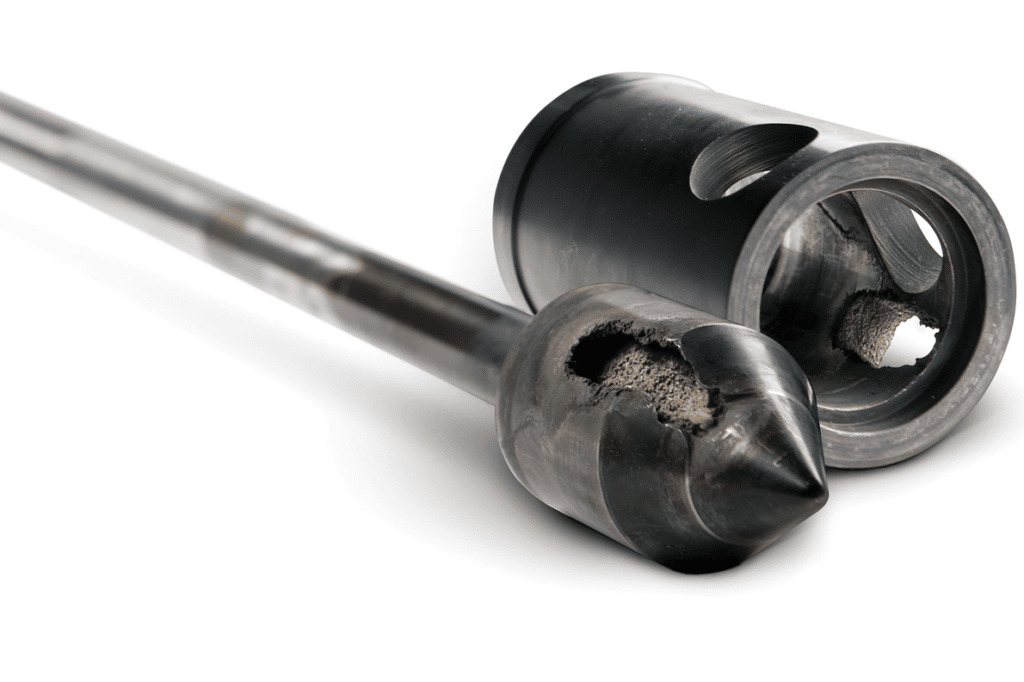
- Mechanical Resonance
Mechanical resonances are situations where an external force driving a mechanical system matches the natural frequency of the system, leading to amplified vibrations in mechanical devices. In control valves, this can happen when the pressure pulsations in the fluid coincide with the natural frequency of the valve or piping.
Problem: Slow Response Time
A slow response time indicates that the valve takes an extended period to reach the operating point or desired position in response to changes in the control signal. This could manifest as a lag in valve operation or a delay in achieving the expected system output.
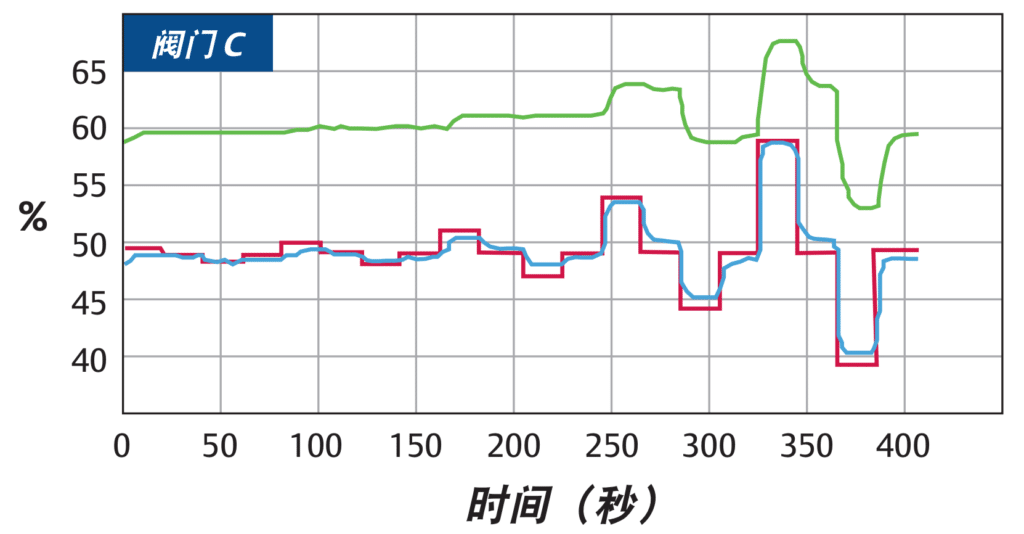
Causes of Slow Response Time
The reasons for slow response time in a control valve can be multifaceted, including but not limited to:
Inadequate Air Supply
The pneumatic actuator of the control valve requires a sufficient air supply to operate correctly. If the supply is inadequate, the actuator may not be able to respond quickly to changes in the control signal, resulting in a slow response time.
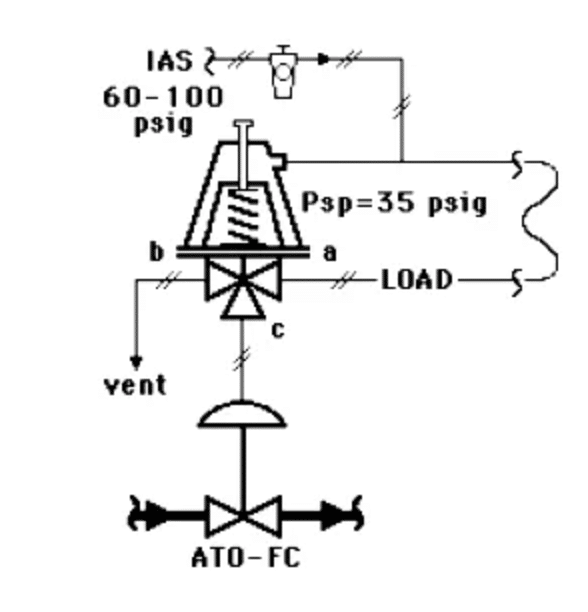
Improperly Sized Actuator
The actuator needs to be appropriately sized to move the valve to the desired position quickly and efficiently. An undersized actuator may lack the necessary force to move the valve stem swiftly, while an oversized one could be sluggish due to its larger moving parts.
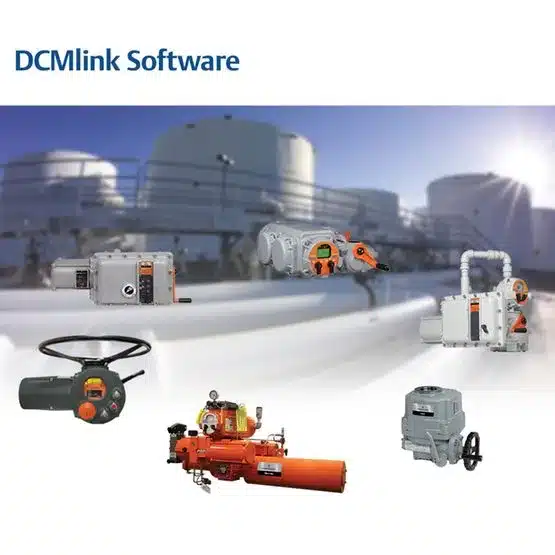
Mechanical Issues
Problems like excessive friction in the valve stem, worn-out or damaged actuator diaphragms, or faulty positioners can lead to a slow response.
Problem: Sticking and Binding
Sticking and binding in control valves refer to the phenomenon where the valve stem or the moving parts within the valve assembly are obstructed, hindering smooth operation. Sticking or binding of the valve stem is a common problem often caused by inadequate lubrication, corrosion, or the presence of foreign materials in the process fluid. This obstruction can lead to sluggish valve response or even total valve failure, significantly affecting the efficiency and control of the industrial process.
The Causes Behind the Issue
Sticking and binding can be traced back to several causes. Let’s dissect these contributors further:
Inadequate Lubrication
The lack of proper lubrication is a common cause of sticking and binding in control valves. With time and continuous operation, the lubrication initially present may degrade, leading to increased friction between moving parts. This can result in the parts ‘sticking’ together, impairing control valve performance further.
Corrosion
Control valves are often exposed to harsh operating conditions, including contact with corrosive substances. These conditions can lead to the corrosion of valve components, causing them to bind together and impede smooth valve operation.
Foreign Materials
The presence of foreign materials in the process fluid is another common cause of sticking and binding. These materials can lodge in the valve, obstructing the movement of the valve stem and other moving parts.
Problem: Cavitation
Cavitation occurs when a liquid’s pressure falls below its vapor pressure, causing vapor bubbles to form and then collapse when pressure rises again. This can cause considerable damage to the valve components and is often a result of an improperly sized valve.

The Effects of Cavitation
Cavitation can have multiple adverse effects on a control valve and the overall operation of the industrial process.
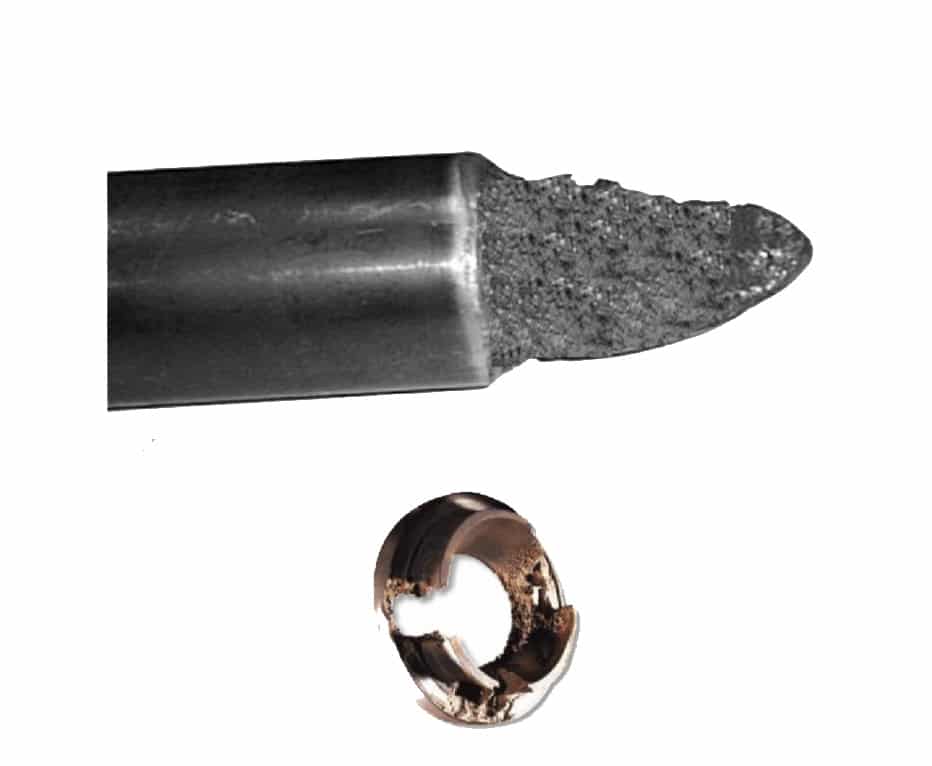
Damage to Valve Components
The most prominent effect of cavitation is the damage it causes to valve components. The energy released from the collapsing vapor bubbles can cause severe erosion and pitting on valve parts, particularly the valve seat and the body. This damage can lead to decreased valve performance, increased leakage, and eventually, valve failure.
Noise and Vibration
Cavitation can cause considerable noise and vibration within the control valve. The repeated formation and collapse of vapor bubbles create pressure waves, which are heard as noise and felt as vibrations. Over time, these vibrations can result in mechanical damage to the valve and associated piping.
Identifying Control Valve Problems
Proper identification of control valve issues is crucial to apply the appropriate corrective measures. This involves understanding the symptoms, and possible causes, and using diagnostic tools effectively.
Detecting Valve Leaks
Detecting a control valve leak promptly can save significant resources and prevent potential safety hazards. Here are some common methods for leak detection:
Visual Inspection
Regular visual inspection of the valve and its surroundings can help identify leaks. Look for signs of fluid accumulation or discolouration around the valve.
Pressure Testing
Pressure tests can reveal leaks that might not be visible to the naked eye. By pressurizing the system and monitoring for pressure drops, you can identify any leaking valves.
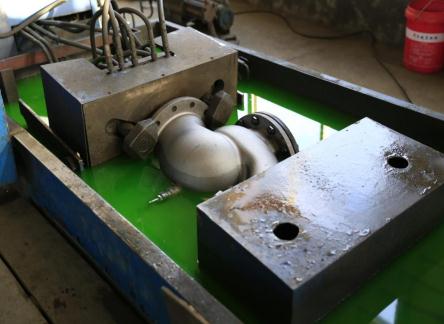
Acoustic Detection
Specialized acoustic equipment can listen for the characteristic sound of a leak, which can be particularly useful for gas or steam systems.
Identifying Noise and Vibration Problems in Control Valves
Diagnosing noise and vibration issues is critical in maintaining efficient system operation. Some common methods include:
Acoustic Analysis
By measuring the noise levels around the valve and analyzing the frequency spectrum of the noise, you can identify possible sources of the problem. Specific patterns can indicate different issues, such as cavitation or flow turbulence.
Vibration Analysis
Vibration analysis uses specialized equipment to measure the vibration levels in the valve and connected piping. Significant deviations from normal levels can indicate potential issues.
Valve Positioner Feedback
Monitoring the valve positioner feedback can provide valuable insights into potential valve problems. An unexpected change in the valve position and feedback signal often indicates issues such as sticking or binding of the valve stem.
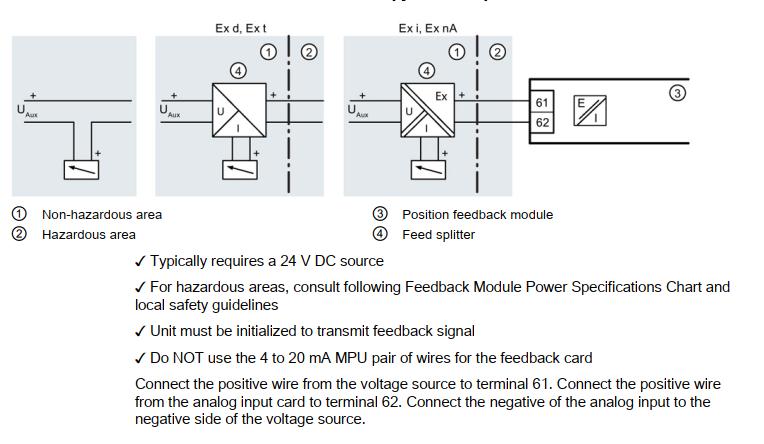
Vibration Analysis
Performing vibration analysis on the control valve can help detect issues such as cavitation or excessive flow turbulence. This can be done using specialized equipment to measure and analyze the vibration levels.
Inspection and Maintenance
Regular inspection and maintenance of control valves can help identify and prevent potential issues. This involves checking the valve components for wear and tear, corrosion, or damage and ensuring that the valve is adequately lubricated.
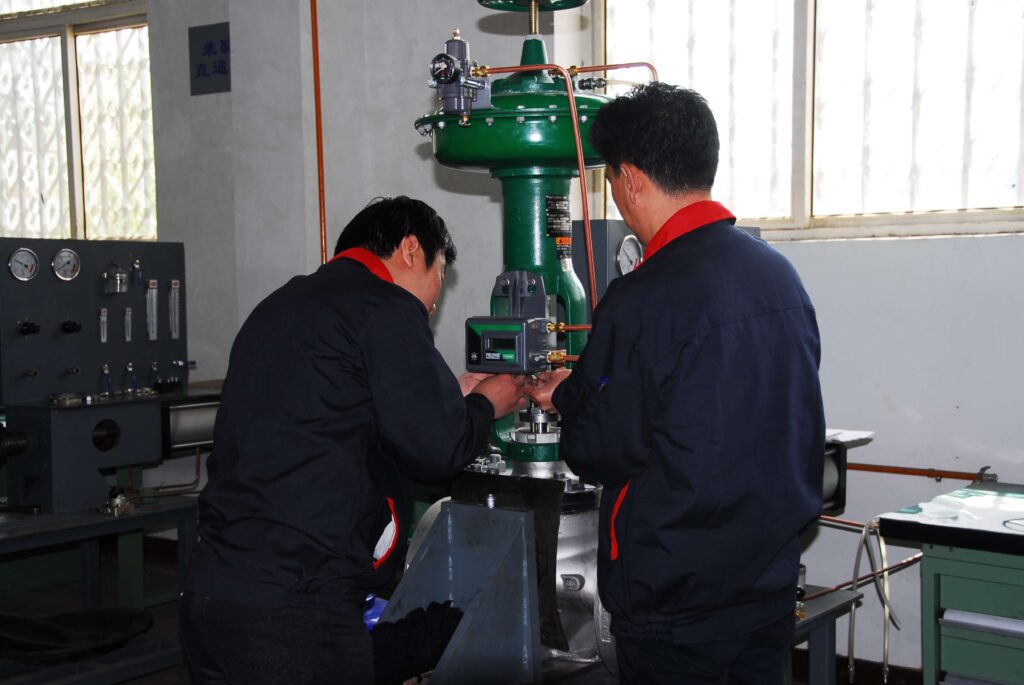
Solutions: Solving Control Valve Problems
Once the problem has been identified, the next step is to implement the correct solution. This can involve adjusting the process conditions, replacing damaged components, or even replacing the valve entirely.
Solve Valve Leaks
If the control valve is leaking, it’s typically due to wear or damage to the seat or seal. Replacement or repair of these components usually resolves the issue.
Valve Repair or Replacement
If the leak is due to degraded seals, damage, or defects, the faulty components need to be repaired or replaced. In some cases, it might be more cost-effective to replace the entire valve.
Re-Installation
If incorrect installation is the cause of the leak, the valve should be re-installed correctly. This involves ensuring proper alignment, seal placement, and component tightening.
Routine Maintenance
Regular maintenance can prevent leaks before they occur. This involves periodic inspections, seal replacements, and pressure tests.
Solve Valve Noise and Vibration
Excessive noise or vibration from a control valve is often a sign of cavitation or flow turbulence. Resolving this requires a review of the valve trim design or possibly resizing the valve.
Once identified, there are several strategies to mitigate noise and vibration issues:
Proper Valve Sizing and Selection
By accurately sizing the valve for the process conditions and selecting the appropriate type of valve, you can prevent conditions that may lead to noise and vibration, such as cavitation.
Pressure Drop Management
Managing the pressure drop across the valve can prevent cavitation, significantly reducing noise and vibration. This can be achieved by using pressure-reducing valves or adjusting the pressure gauge to process conditions.
Use of Noise Reduction Trim
Some valves can be fitted with noise reduction trim, designed to reduce the noise produced by turbulent flow and pressure fluctuations.
Noise and vibration in control valves are serious issues that can result in significant damage if not addressed promptly. Through understanding their causes, identifying them early, and taking proper mitigative measures, you can maintain efficient, safe, and quiet operation of your control valve systems.
Slove Slow Response Time
To solve slow response time in control valves, consider the following steps:
Check Air Supply
Ensure that the air supply to the actuator is sufficient and consistent. Investigate and resolve any issues related to the air supply system, such as leaks or blockages.
Review Actuator Sizing
Confirm that the valve movement actuator is correctly sized for the valve. If necessary, consult with a valve specialist or refer to the valve and actuator specifications to verify sizing.
Conduct Regular Maintenance
Regular inspections and preventative maintenance can help identify and address mechanical issues before they severely impact the valve’s response time. Regular lubrication of the valve stem and replacement of worn-out components can significantly improve response times.
Solutions to Valve Sticking and Binding
Addressing the issue of sticking and binding involves both preventative and corrective measures:
Regular Maintenance
Regular maintenance activities, including periodic lubrication and cleaning of the valve, can help prevent the problem of sticking and binding. These activities ensure that the valve parts remain in optimal condition, preventing the onset of sticking and binding.
Corrosion Control
Employing corrosion-resistant materials in valve construction and using corrosion inhibitors can prevent the corrosion of valve components. This can significantly reduce the likelihood of sticking and binding due to corrosion.
Filtration Systems
Integrating filtration systems can remove foreign materials from the process fluid before it passes through the valve. This can prevent these materials from lodging in the valve and causing sticking or binding.
Preventing and Managing Cavitation
Understanding cavitation is one aspect, but effectively managing and preventing it is vital to maintain the longevity and efficiency of control valves.
Correct Valve Sizing
Choosing the right size of control valve can help prevent cavitation. A correctly sized valve will ensure the fluid pressure doesn’t drop below its vapor pressure, thus avoiding bubble formation. Detailed understanding of the process conditions is crucial for proper valve sizing.
Anti-cavitation Trims
Anti-cavitation trims can be utilized in control valves to manage cavitation. These trims work by spreading out the pressure drop over the flow characteristic several stages, preventing the fluid pressure from falling below its vapor pressure at any single point.
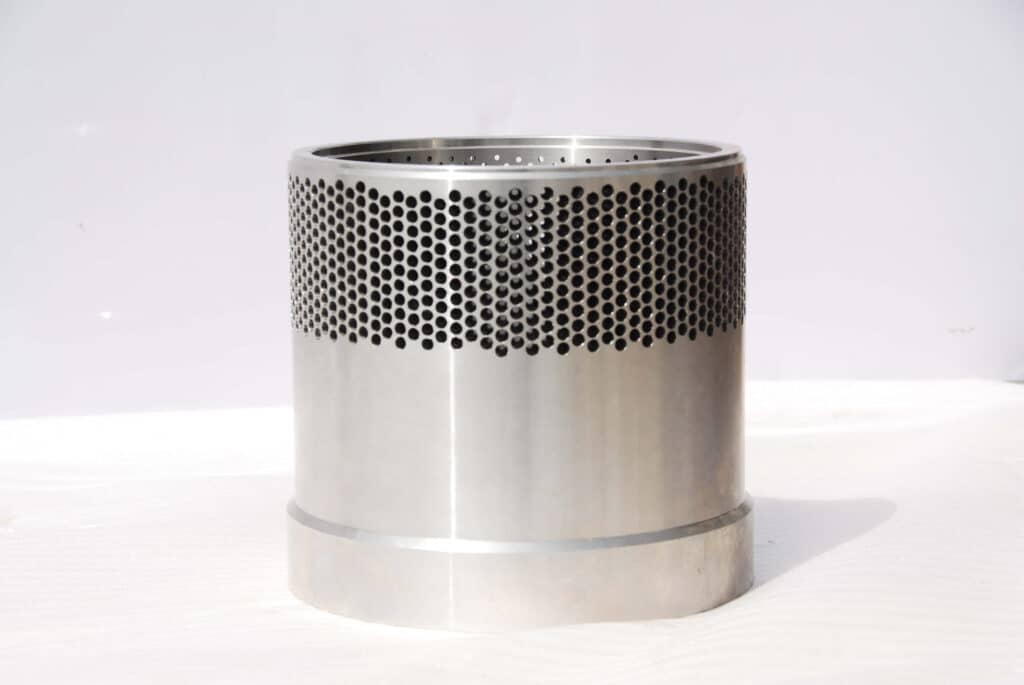
Cavitation-resistant Materials
In cases where cavitation can’t be completely avoided, using cavitation-resistant materials for constructing the valve components can help reduce the damage caused. These materials have higher resistance to the erosive forces produced during cavitation.
Valve Maintenance and Repair
Regular maintenance and repair can significantly enhance the lifespan of a control valve. This involves lubricating moving parts, replacing worn components, and checking for and removing any foreign materials.
System Optimization
Sometimes, solving a control valve problem may involve optimizing the entire system. This could mean adjusting the process conditions, modifying the piping layout, or even changing the type of control valve system being used.
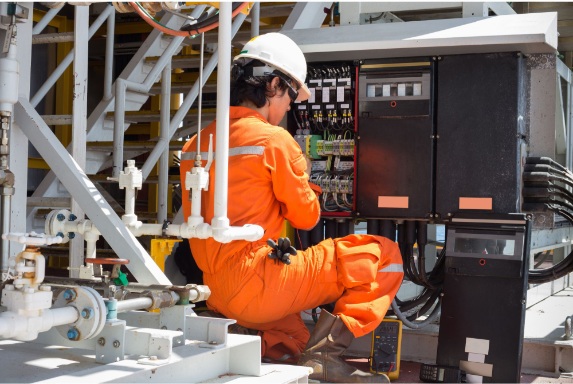
In Conclusion
Control valve challenges may seem complex, but with the right knowledge and strategies, these obstacles can be surmounted. By understanding the material and design challenges and adopting advanced troubleshooting strategies, you can optimize the performance and longevity of your control valves, turning challenges into opportunities for improvement.
Remember, the better we understand and manage these challenges, the more efficiently our processes run, translating into better productivity and profitability. As a reputation control valve supplier, THINKTANK not only provides reliable and high-quality control valves and expert knowledge of sizing&selection control valves, but also the perfect service and unique custom solution for valve brands, distributors, engineering companies, EPCs, and instrument companies.
Stay on top of your control valves, and they will keep your processes flowing smoothly.
What is the valve industry forecast?
The control valve industry plays a critical role in an array of sectors, including oil and gas, power generation, water and wastewater treatment, and manufacturing. The industry’s future looks promising, with several key trends and factors poised to drive growth in the coming years.
Market Size and Growth Projections
The global control valve market has seen steady growth over the past few years. According to various market research reports, this upward trend is set to continue. As of 2023, the control valve market was valued at approximately USD 7.9 billion. The industry is projected to grow at a compound annual growth rate (CAGR) of around 5.9%, reaching a valuation of around USD 11.3 billion by 2028.
Driving Factors for Growth
Several factors are contributing to this positive market forecast for control valves.
Industrial Expansion
Increased industrialization, especially in emerging economies, is a significant driver. As industries expand, the demand for control valves, integral components in process control, is expected to rise.
Technological Advancements
Technological advancements are reshaping the control valve industry. Innovations like smart valves and IoT-integrated control valves not only offer better performance and reliability but also provide real-time monitoring and diagnostics capabilities. As industries continue to embrace digital transformation, these next-gen valves are likely to see increased adoption.
Energy Sector Demand
In the energy sector, both traditional and renewable, there’s a continual need for control valves. In traditional energy industries like oil and gas, control valves play a key role in various processes, from extraction to refining. In renewable energy plants, such as wind or solar farms, control valves are critical in managing fluid flows and ensuring optimal performance.
Challenges and Opportunities
Despite the optimistic forecast, the industry faces some challenges. Fluctuations in raw material prices and the need for high initial investment can hamper market growth. However, these challenges also present opportunities. Companies that manage to balance cost-effectiveness with quality and innovation are likely to prosper.
Furthermore, the growing focus on sustainability presents another opportunity. There’s increasing demand for energy-efficient valves that minimize environmental impact. Manufacturers who can deliver on these fronts stand to gain a competitive advantage.
The future of the control valve industry looks bright, driven by industrial expansion, technological advancements, and sustained demand from the energy sector. While challenges exist, they also open up avenues for innovation and development. Therefore, the industry is set to continue its upward trajectory in the foreseeable future, marking an exciting time for all involved stakeholders.
Which control valve is most commonly used in industry?
Control valves are essential components in a variety of industries, managing the flow of fluids to ensure smooth, efficient operations. Of the numerous types of control valves available, one stands out due to its widespread use across sectors – the Globe Valve.
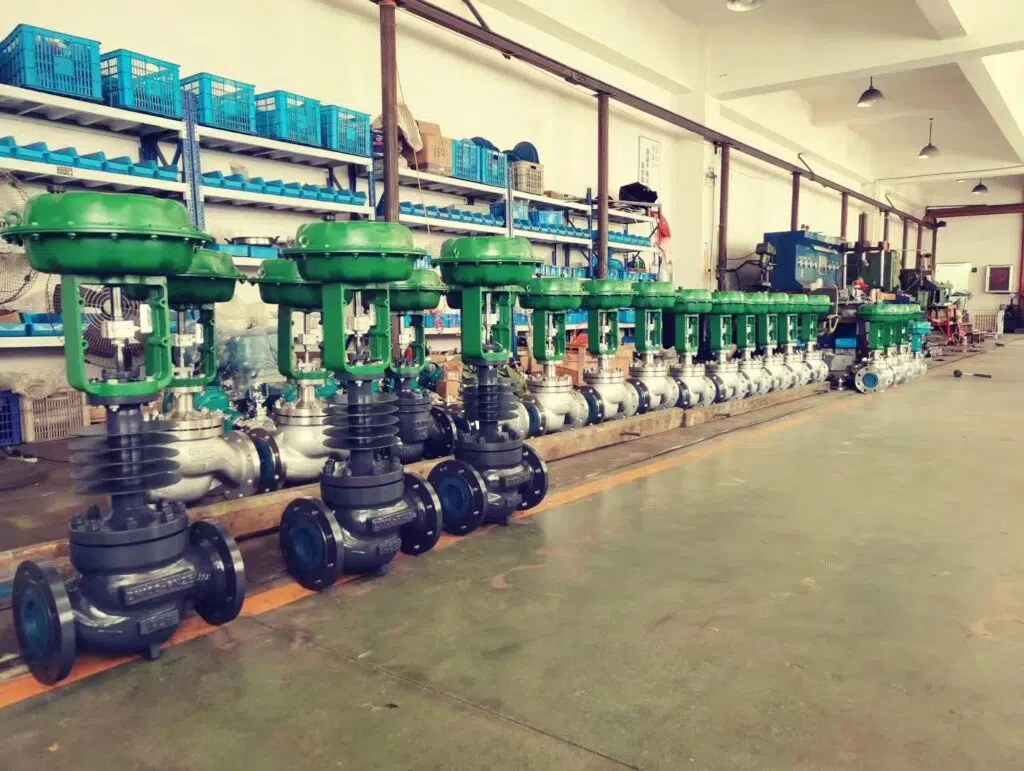
Globe Valve: The Industrial Mainstay
Globe valves, named for their spherical body shape, are one of the most commonly used types of control valves in industries, prized for their durability, versatility, and effective flow control capabilities.
Structure and Functioning
A typical globe valve consists of a movable disc or plug connected to the valve stem, and a stationary ring seat in a generally spherical body. The valve’s operation is straightforward – when the valve handle is turned, it moves the disc against the valve seat, regulating the flow of fluid through the valve.
Versatility
One of the primary reasons for the popularity of globe valves is their versatility. They are suitable for a wide range of applications and can handle various types of fluids, including water, steam, gas, and oil. Globe valves are effective in situations that require throttling, i.e., precise control over fluid flow, and frequent operation.
Durability and Maintenance
Globe valves are known for their durability and can withstand high pressures and temperatures. This makes them suitable for use in demanding industrial environments. Moreover, their design allows for easy maintenance and repair, as the disc and seat are readily accessible for inspection or replacement without removing the entire valve from the pipeline.
Other Noteworthy Control Valves
While globe valves are an industry favorite, it’s worth noting a few other types of control valves that are also commonly used:
Ball Valves: Known for their quick operation and durability, ball valves are commonly used in applications requiring on-off control of fluid flow.
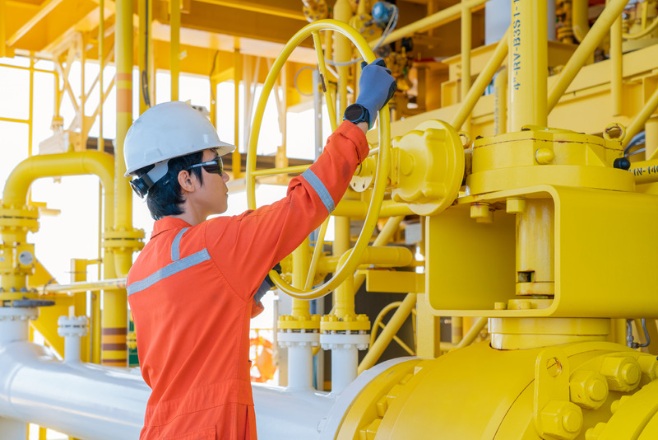
Butterfly Valves: Lightweight and compact, butterfly valves are often used in large-diameter pipelines. They are suitable for applications that require the throttling of fluid flow and low-pressure drop.
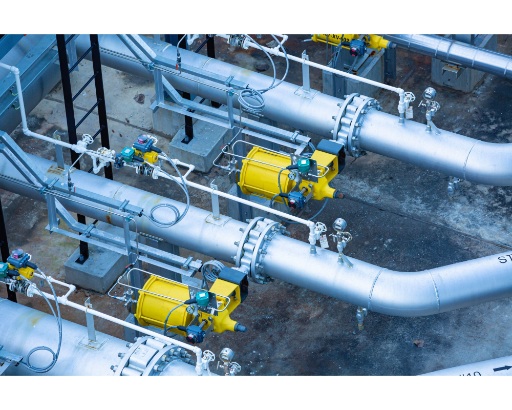
Gate Valves: Best suited for on-off control rather than throttling, gate valves are often used when minimal flow restriction is desired.
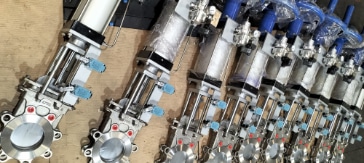
What are the three basic types of control valves?
What is the reason for control valve hunting?
Control valve hunting, also known as oscillation, is a common issue where the control valve continuously cycles open and closed rather than settling at a stable position. This erratic behavior can result in inefficient system performance and potential damage to the valve and associated equipment. Several factors can lead to control valve hunting.
Improper Tuning of the Control Loop
One of the main reasons for control valve hunting is improper tuning of the control loop. If the controller is set too aggressively (high gain), it might cause the control valve to react too quickly to changes in the process variable, leading to oscillations around the set point.
Valve Stiction
Valve stiction, a portmanteau of static and friction, is another common cause of control valve hunting. Stiction refers to the extra force required to initiate movement in the valve stem from a stationary position. This can lead to an overshoot when the valve begins to move, causing the valve to oscillate.
Mismatched Valve and Actuator
If the valve and actuator are not properly matched in terms of size and performance characteristics, it can lead to control valve hunting. An oversized actuator may cause the valve to react too quickly, while an undersized actuator may not provide the necessary force to move the valve, both resulting in oscillations.
Inadequate Air Supply
Inadequate or fluctuating air supply to the pneumatic actuator can also result in control valve hunting. If the air supply pressure is too low, it may not provide the necessary force for the actuator to control the valve effectively, leading to oscillations.
Incorrectly Sized Valve
An incorrectly sized valve can also lead to control valve hunting. If the valve is too large for the application, small changes in the control signal can result in significant changes in the flow rate, causing the valve to oscillate.
What is the major cause of valve failure?
The most significant cause of control valve failure is improper installation and maintenance. While several other factors contribute to valve failure, improper installation and maintenance are often the root causes leading to several downstream problems.
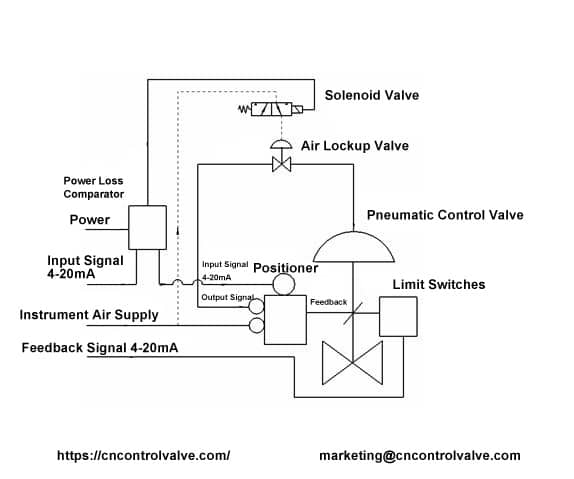
Misalignment and Incorrect Sizing
Incorrect installation can lead to various issues. For instance, if a valve is installed misaligned with the piping, it can cause undue stress on the valve body, leading to leakage or failure. Incorrect sizing of the valve for its application can also lead to overloading or underloading of the valve, causing premature wear and tear and eventual failure.
Inadequate Maintenance
Inadequate or improper maintenance can cause several problems, such as:
Lack of Lubrication: Lack of regular lubrication can lead to increased friction in the moving parts of the valve, leading to wear and potential failure.
Untreated Corrosion: Corrosion, if not treated in its early stages, can cause significant damage to the valve body and internal components, leading to leaks and valve failure.
Seal Deterioration: Over time, seals can deteriorate and lose their ability to prevent fluid leaks. If not replaced in time, leaking fluid can damage other valve components and lead to valve failure.
Other Causes of Control Valve Failure
While improper installation and maintenance are the most significant causes, other factors can also contribute to control valve failure:
Cavitation and Flashing: These phenomena can cause erosion of the valve components, leading to leakage and eventual failure.
High Pressure and Temperature: Control valves exposed to conditions beyond their pressure and temperature ratings can suffer from deformation or cracking, leading to failure.
Foreign Particles: Debris or foreign particles in the fluid can cause damage to the internal components of the valve, leading to failure.