Through years of manufacturing control valves & self-operated regulators, with rich experience in field application and practice, analysis, and summary, we have analyzed and compared the three schemes of steam pressure reduction in the main pipeline of the factory, so as to select the appropriate solution to achieve the best decompression and stabilization effect. Due to the needs of the factory’s production process, steam is an indispensable process medium. Steam needs to be imported from the power plant. Because the distance between the power plant and the factory is relatively large, there are large pressure fluctuations, and the actual flow rate fluctuation range of the factory is large. The pressure of the main steam pipeline entering the factory is reduced and stabilized. To solve the above problems, the following 3 typical solutions are usually adopted.
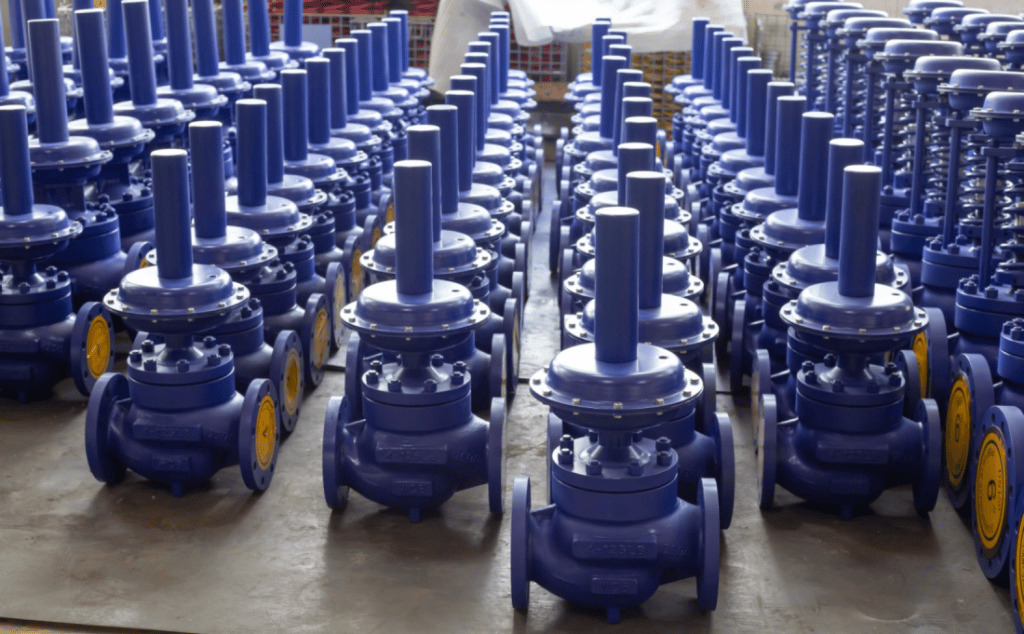
The first option is to use a steam self-operated pressure regulator, the second option is to use a pneumatic or electric globe type control valve to control the process parameters, and the third option is to use two pneumatic or electric globe types control valves in parallel for split-range control.
Three Typical Solutions For Steam Pressure Reducing Station
#1 Using a Steam Self-Operated Pressure Regulator
Using a self-operated steam pressure regulator as a steam prv station is simple and convenient, with little maintenance costs, and is especially suitable for on-site situations where there is no electricity and no air power. Therefore, it has been widely used in steam pressure reduction systems, the following are the advantage of this solution.
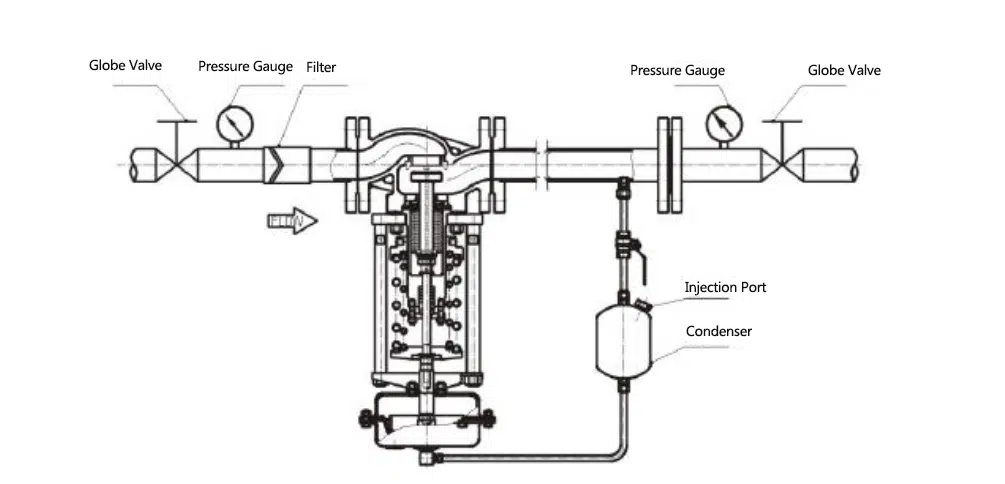
- The pressure setpoint can be adjusted on-site within the pressure adjustment range;
- The valve body and the actuator adopt modular design, and the actuator or spring can be changed according to the site requirements to realize the rapid replacement of the pressure adjustment range within a certain range;
- The self-operated steam pressure reducing valve generally uses bellows as the pressure balance element. The pressure change before and after the valve does not affect the force of the valve core, which greatly accelerates the response speed of the valve, thereby improving the adjustment accuracy of the valve;
- The structure of the cage balance valve adopts a self-balanced and double-sealing surface valve plug as a throttling part. The medium should be clean and free of particles. It is suitable for occasions where the pressure drop is large, the valve diameter is large, and the leakage rate is not high;
- The structure of the double-seat valve adopts a self-balanced & double-seal & double-seated valve plug as the throttling element, which is suitable for occasions with larger valve diameters;
- The diaphragm type actuator adopts the rubber diaphragm as the pressure detection element, which has low rigidity, high sensitivity, rapid response, and high adjustment accuracy, and is suitable for control pressure ≤ 0.6MPa;
- The piston-type actuator adopts the cylinder/piston as the pressure detection element, which is suitable for the application where the control setting value ≥ 0.6MPa pressure;
- The bellows actuator adopts bellows as the pressure detection element, which is suitable for high temperature and other severe working conditions.
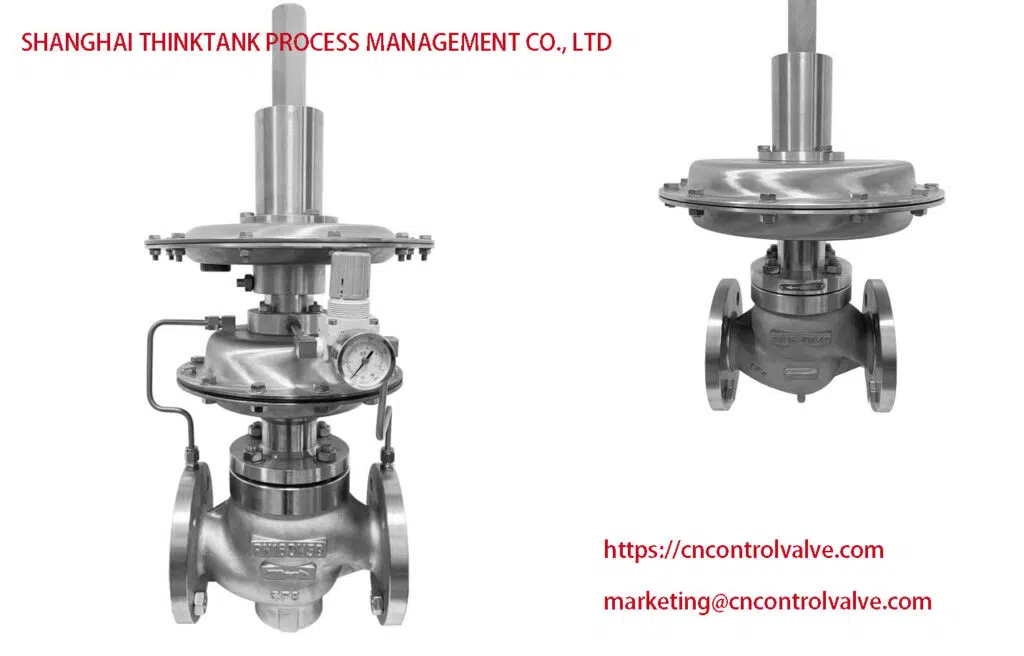
Special attention should be paid to the following key points in the scheme of adopting self-operated steam pressure regulator, which is also problems that often occur in improper use in practical applications:
NO. | Attentions | Functions | Problems |
1 | A gas tank should be installed after the valve | Has the function of buffering and stabilizing | When the flow rate changes, a large pressure fluctuation phenomenon occurs |
2 | An overpressure protection device should be installed after the pressure reducing valve | Prevent the downstream valve from being broken | (I.e. safety valve), to prevent the self-operated pressure regulator from being damaged due to the pressure rise due to the close to zero flow after the valve. |
3 | The set pressure of the safety valve cannot be close to the working pressure | Prevent frequent take-off of safety valve | If the flow rate is too small, the self-operated pressure regulator tends to close, and the safety valve takes off frequently. |
4 | To minimize the friction at the packing seal of the self-operated steam pressure regulator | Prevent the valve response lag due to excessive friction. | Cause the upstream safety valve to jump frequently or the pressure is too low |
#2 Using a pneumatic or electric globe type control valve to control the process parameters. The characteristic is that the adjustment accuracy is much higher than that of the self-operated steam pressure regulator, but the price and maintenance costs are higher.
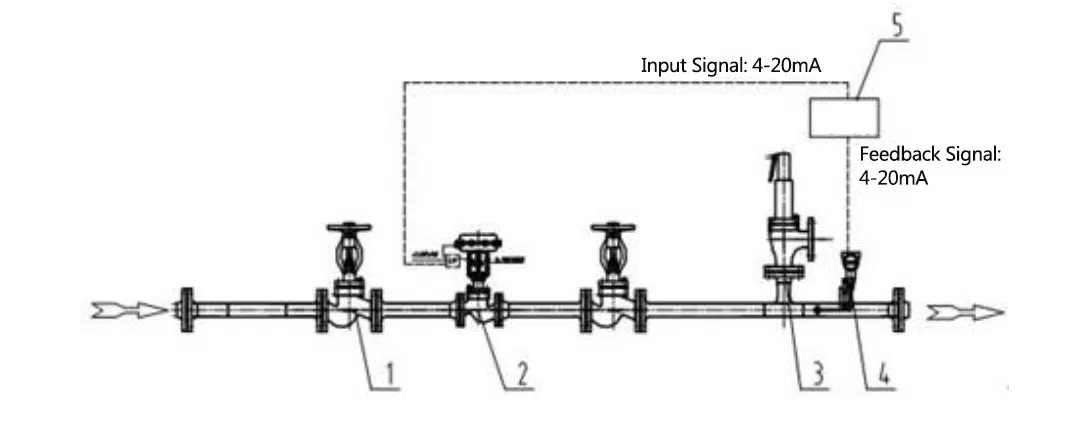
- Globe valve
- Pneumatic control valve (with positioner)
- Safety valve
- Pressure transmitter
- Console (process controller)
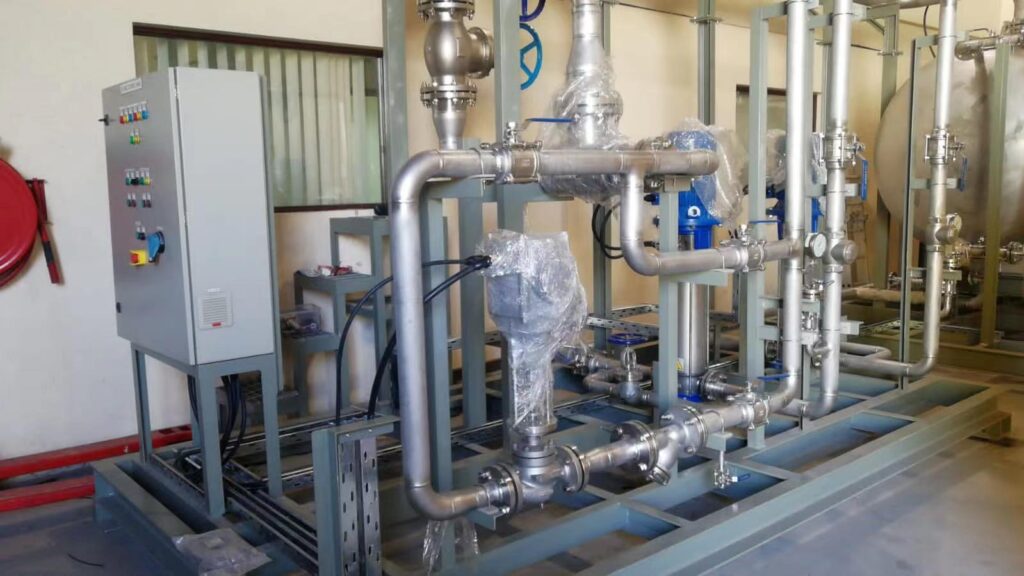
Overview of Scheme 2: The pressure transmitter feedback 4-20ma.DC current signal according to the measured pressure, and compares it with the set value in the console. When the difference between the two reaches a certain value, the console sends an adjustment signal to the pneumatic control valve. According to this signal, the actuator of the pneumatic control valve causes the valve stem to drive the plug to produce displacement and change the flow through the control valve until the pressure at the test point meets the requirements. So as to achieve the purpose of automatically adjusting the pressure.
The structure of the globe type control valve is basically top-guided single-seat, single-seat cage guided, double-seat, and low-noise trim according to process conditions.
The above two schemes are the two commonly used solutions in factories, but in actual applications, the flow rate of downstream control valve changes greatly, especially when the steam consumption is very small, that is, the valve opening is small, and the valve is not very stable at low valve opening, and it will cause valve oscillation.
Solution: In this case, it is recommended to use solution 3, which uses two pneumatic control valves in parallel.
#3 Using two pneumatic or electric globe-type control valves in parallel for split-range control.
When control valve A receives the signal 4~12.5mA, the valve opening responds from closed to fully open, and when control valve B receives the signal 11.5~20mA, the valve changes from closed to fully open. These two valves are realized by two positioners that lead to action. When the working flow capacity is small, the B valve is in the closed state, which is realized by the change of the opening of the A valve.
When the required flow rate is large, even control valve A is fully opened that still cannot meet the requirements, then control valve B will open to increase the flow capacity of steam. Adopting solution 3 can not only meet the load change requirements during production but also improve the control accuracy and stability.
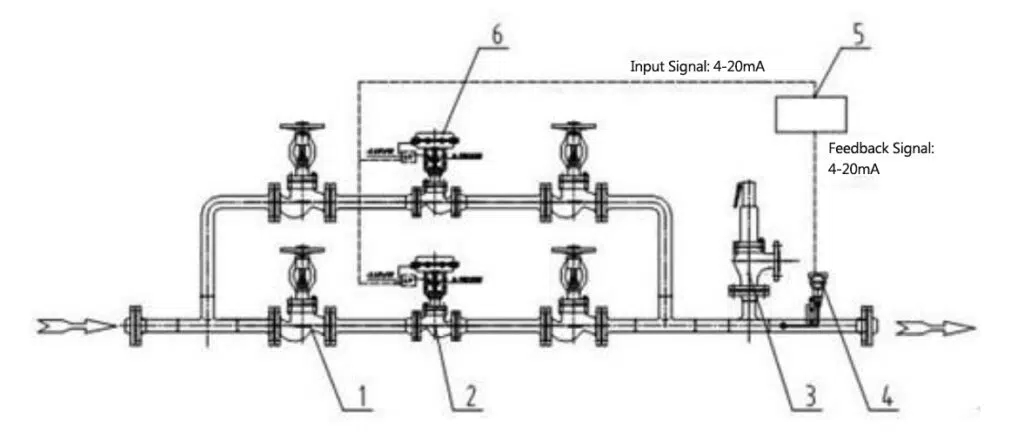
- Globe valve
- Control valve A (pneumatic control valve with positioner and air filter pressure reducer)
- Safety valve
- Pressure Transmitter
- Console (process controller)
- Control valve B (pneumatic control valve with positioner and air filter pressure reducer)
Feature Comparison Valve Type | Cost | Precision & Stability | Suitable Application | Application Examples |
Option 1 (One self-operated Pressure Regulator) | Cost-Effective | Low | -No power supply or air source -When the flow rate changes relatively little -The set pressure of the safety valve cannot be close to the working pressure | Upstream Pressure: 8~10kg/cm2 Downstream Pressure: 5 kg/cm2 Flow Rate: 6~10t/h Selection Valve Size: DN100 (Direct Response From the Pipeline) |
Option 2 (A Pneumatic Control Valve) | More Expensive | Good | -Have power supply or air source -Can be remotely set and displayed -Generally used in self-operated steam pressure regulator can not meet the requirements, especially when the flow rate changes relatively large and Where precise control is required | Upstream Pressure: 8~12kg/cm2 Downstream Pressure: 5 kg/cm2 Flow Rate: 2~10t/h Requirement: Precise/accuracy control Select Valve Size: DN100 (Input Signal: 4~20mA ) |
Option 3 (Using two pneumatic or electric globe type control valves in parallel) | Quite Expensive | Excellent | -Have power supply or air source -Can be remotely set and displayed -Generally used in self-operated steam pressure reducing valves or occasions that cannot be met by a pneumatic control valve, suitable for occasions where the flow rate changes greatly. | Upstream Pressure: 8~14kg/cm2 Downstream Pressure: 5 kg/cm2 Flow Rate: 0.5~10t/h Requirement: Precise/accuracy control Control Valve A Select Valve Size: DN40 (Input Signal: 4~12.55mA) Control Valve B Select Valve Size: DN100 (Input Signal: 11.5~20mA) |
The parameters of the steam pressure regulator should be indicated when ordering
- Model
- Nominal diameter × seat diameter
- Nominal pressure
- Connection type
- The material and surface hardening treatment requirements of the valve body and internal components
- Medium name
- Medium working temperature
- The inlet pressure and adjusting range
- Pressure setting point and adjustment range at the outlet (if for control upstream pressure, only required in items 7 and 8)
- The maximum, normal, and minimum flow values per hour of the equipment
- Special requirements, free oil, free bronze etc.
The above is the selection of three different types of steam pressure reducing valves summarized by our company’s technicians through years of selection and application experience. THINKTANK, as a professional manufacturer in the field of high-end control valves and pressure regulators. The brand’s partners and after-sales rapid response center, through years of experience in design, assembly, transformation, maintenance, and debugging, absorb innovation in the field of control valves and provide customers with a full range of fluid control solutions. Products are widely used in petroleum, chemical, power power, shipbuilding, food, medicine, building, machinery supporting industries. The main products include globe control valves, pressure reducing valves, safety valves, self-operated pressure regulators, etc. We can provide carbon steel, alloy steel, stainless steel, super duplex stainless steel, and special alloys such as MONEL and other materials. The product temperature ranges from -196℃ to 650℃.
For more details, please contact us or log in to the company’s official website for consultation <https://cncontrolvalve.com>
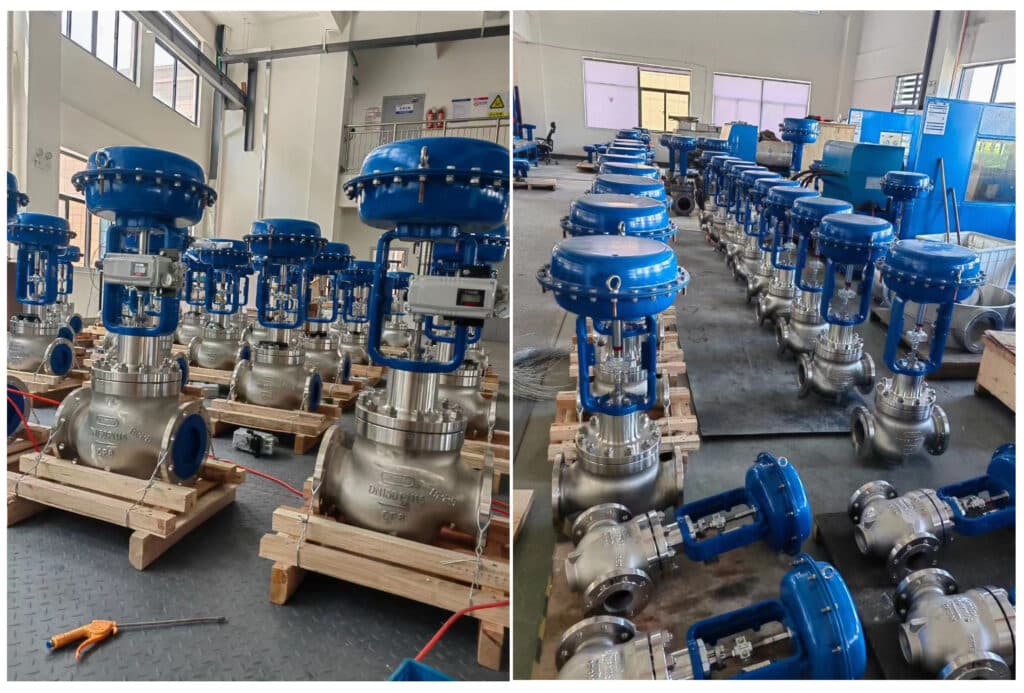
Final Thoughts of PRV Station
In this post, you have learned the most typical solutions for steam pressure reducing, and how to install the split range control valve for your application. If you are interested in more knowledge about control valves and regulators, please just click the following posts.
Learn All About Pressure Control Valves
Pressure control valves are more and more popular used for a natural gas applications, THINKTANK has participated in more than 10 large natural gas plant projects, not only has rich experience in type selection but also provides end-users with more cost-effective pressure control valves while controlling costs.
Self-operated pressure regulators
Nowadays, there are two types of self-operated pressure regulators, direct-acting self-operated pressure regulators, and pilot-operated pressure regulators.
Self-operated temperature regulators
Self-acting temperature control valves also known as self-operated temperature regulators, it doesn’t need any external power sources to regulate the temperature of process streams, tanks, and various systems. THINKTANK’s self-operated temperature regulators are often used for boiler temperature adjustment. It can maintain a linear functional relationship between temperature and valve opening.
Self-operated differential flow control valves
ZZC, ZZV self-operated differential (micro) pressure regulator is not needed to require external energy, and differential (micro) pressure can be adjusted in sections, ranging from 50mm.w.c to 0.1MPa. It has a wide range of uses and can be used in industrial combustion furnace systems to control the ratio of two materials, such as gas and air, to achieve ideal combustion.
For more information, you can refer to this post. Everything knowledge you can learn for your project.