We know all control valves should be sizing and selected before ordering, to make sure it meets our condition.
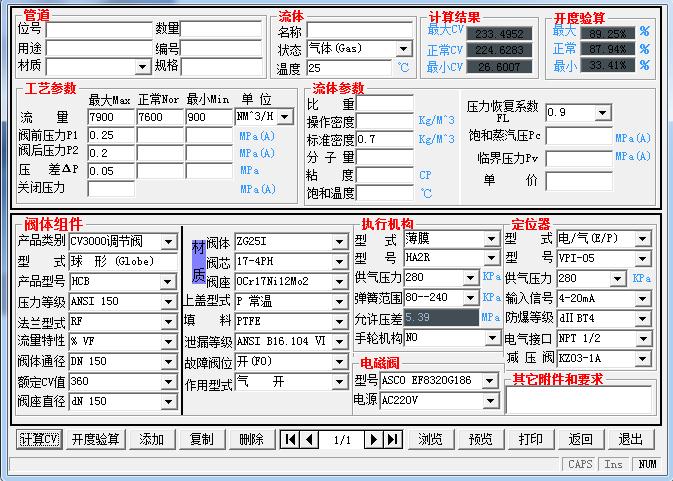
Because if oversizing the control valves will hurt the process variability in two ways. First, the oversized valve cost too much, and the flow capacity range is wide. It makes less flexibility in adjusting the controller, especially controlling the valve opening around 25% travel. And this will create a risk of increased process variability. Secondly, the oversized control valves hurt process variability because an oversized valve is caused to operate more frequently at lower valve travel. Lower valve opening makes seal friction greater, particularly in rotary valves. Because oversized control valves supply a disproportionately large flow change for a given increment of valve travel, this phenomenon greatly exaggerates the process variability associated with friction-induced dead zones.
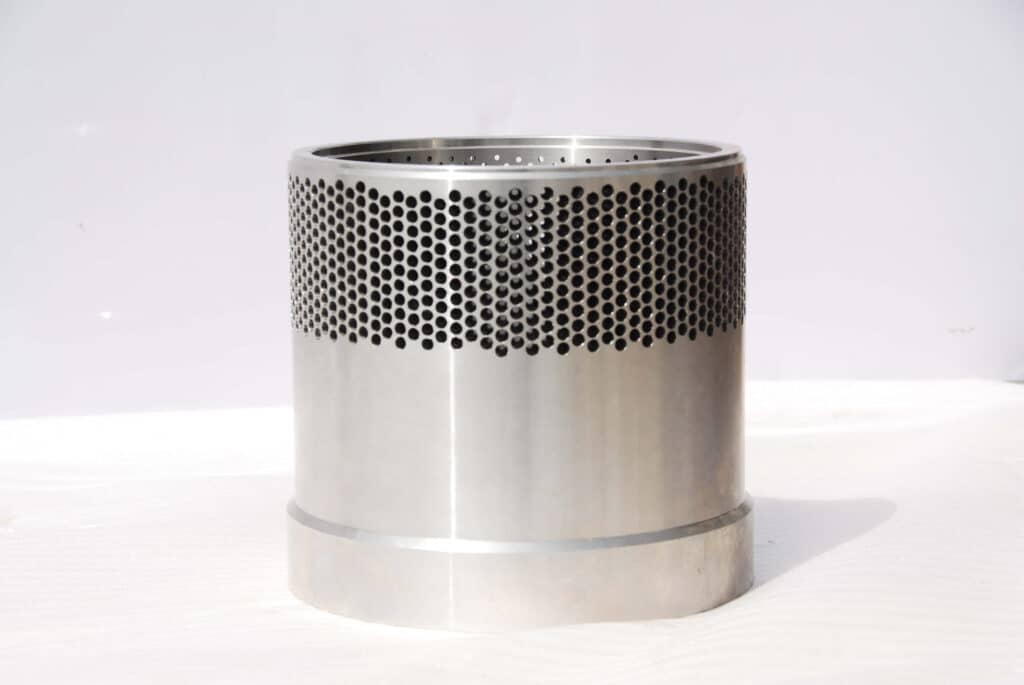
Regardless of its actual inherent flow characteristic of the control valve, an oversized control valve act more likely as a quick-opening valve, which results in high installed process gain in the lower lift regions.
Meanwhile, when the control valve is oversized, the valve tends to reach system capacity at relatively low travel, making the flow curve flatten out at higher valve travels. For valve travel over about 50%, the valve has become completely ineffective for control purposes because the process gain is close to zero and the valve travel has to vary greatly with little change.
So it is very important to consider the valve type, inherent characteristic, valve size when we are on selecting a control valve.
In this way, no matter from the economic point of view, the process management accuracy can reach the maximum benefit.
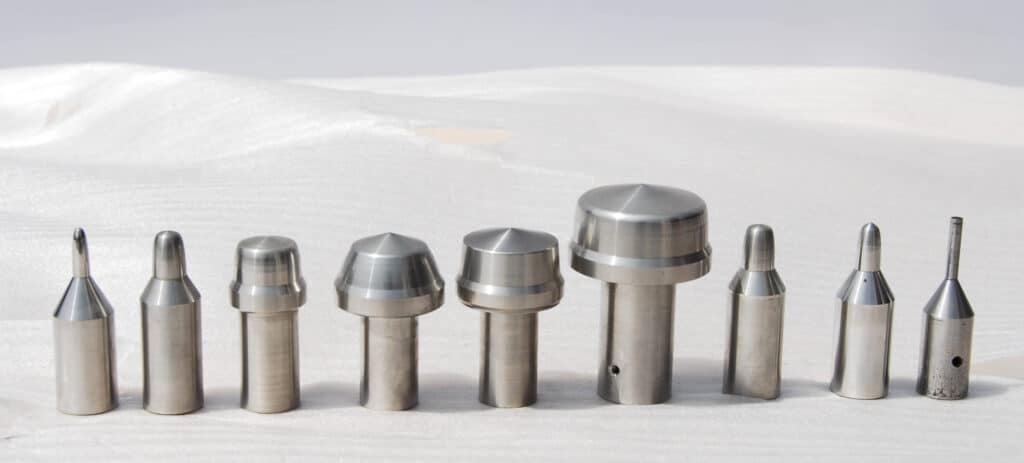