Introduction to Pilot Operated Valves
Pilot operated valves are a critical component of industrial control systems, used to regulate the flow/pressure of fluids in various processes. These valves offer precise control, high capacity, and a wide range of applications, making them an essential choice for many industries.
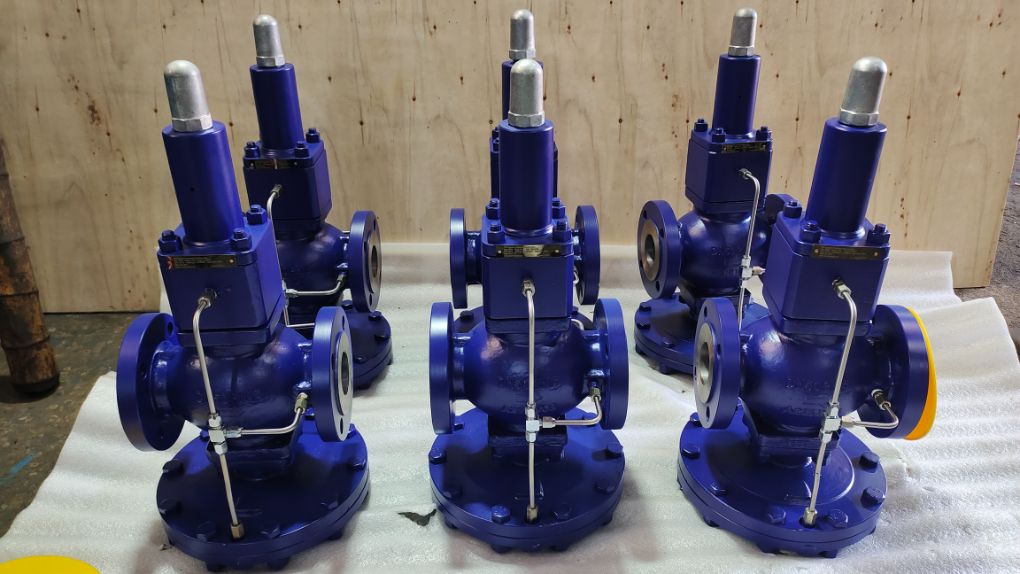
What are Pilot Operated Valves?
Pilot operated valves, also known as pilot valves, are control valves that use a small pilot valve to control the larger main valve. The pilot valve is typically operated by a pressure signal or an electric signal, which in turn controls the flow of fluid through the main control valve.
Components and Working Principles
Pilot operated valves consist of the following key components:
- Main valve: This is the primary valve responsible for controlling the flow of fluid through the system.
- Pilot valve: This smaller valve controls the operation of the main valve, modulating its position based on system requirements.
- Sensing line: This line connects the pilot valve to the system, allowing it to sense changes in pressure or flow and adjust the main valve accordingly.
The working principle of a pilot operated valve is relatively straightforward. When the system requires a change in flow, the pilot valve senses the change and adjusts its position. This change in pilot pressure and position allows fluid to flow into or out of the main valve, causing it to open or close as needed. The result is a highly responsive, accurate control system that can manage complex industrial processes with ease.
Valve model abbreviated description
Abbreviation | Example | Meaning |
L | TD42 L | Left to right flow |
R | TD42 R | Right to left flow |
Z | FT14 Z Sc | Z axis view (for example, the view looking through the centre orifice) |
Fi | ILVA Fi L | Full image |
V or Ver | FT14 V Cover Sc | Vertical flow |
Fl | BPT21 L Fl | Flanged |
Sc | BPT21 L Sc | Screwed |
Bw | AV45 Bw L | Butt weld |
Wd | BTD52 L Wd | Weld |
B/down or Bd | TD42 L Bd+Iso | Blowdown version |
Iso or Isotub | TD42 L Bd+Iso | Isotub option (for Thermodynamic steam traps) |
V or Ver | FT54V* | Vertical version |
H or Hor | FT54H* L | Horizontal version |
SLR | FT14 L SLR Sc | Steam lock release option |
# | BC 3200# | Insert the drawing using a scale factor of 1:1 |
* | BSA1* L | More than one product shares this drawing (for example, the BSA2 & BSA3 look the same as the BSA1 so use the same drawing) |
Types of Pilot-Operated Valves
There are two main types of pilot-operated valves: direct-acting and pilot operated. Direct-acting valves are simple and reliable, but may not be suitable for higher flow rates or more complex systems. Pilot-operated valves, on the other hand, use a small pilot valve to control the flow of fluid through the main valve. This allows for precise control and modulation of flow rates, making them ideal for larger systems or applications that require fine-tuning.
Direct Acting Valves
Direct-acting valves are the simplest type of pilot operated valve. They operate by using a spring-loaded plunger to control the flow of fluid pressure relief valve. When pressure is applied to the plunger, it opens the valve and allows fluid to flow through. When pressure is removed, the spring returns the plunger to its original position, closing the valve.
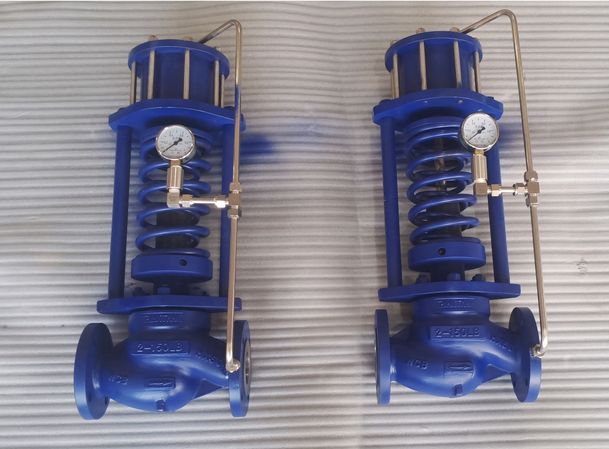
Direct acting valves are typically used in low-flow applications where precise control is not required. They are reliable and easy to maintain, but may not be suitable for larger systems or applications that require more precise control.
Pilot Operated Valves
Pilot operated valves use a small pilot valve to control the flow set pressure of the fluid through the main valve. The pilot valve is typically controlled by a solenoid or other type of actuator, which opens and closes the valve based on the input signal. This allows for precise control of flow rates and modulation of pressure, making them ideal for larger systems or applications that require fine-tuning.
Pilot operated valves can be further categorized into two types: internally piloted and externally piloted. Internally piloted valves have the pilot valve integrated into the main valve body, while externally piloted valves have a separate pilot valve that is connected to the main valve via tubing or piping.
Pilot Operated Valve Drawing
1 | Bottom Cover | A216Gr.WCB |
2 | Bottom Shell | #20 Carbon Steel |
3 | Diaphragm | SS Metal |
4 | Body | A216Gr.WCB |
5 | Stem | SS304 |
6 | Seat | SS304 |
7 | Plug | SS304 |
8 | Main Spring | 50Gr.VA |
9 | Bonnet | A216Gr.WCB |
10 | Cap | A216Gr.WCB |
11 | Adjusting Spring | 60Si2Mn |
12 | Adjusting Screws | #35 Carbon Steel |
DN | L | H1 | H | D | D1 | D2 | f | b | Z-φd |
50 | 230 | 270 | 260 | 160 | 125 | 100 | 3 | 18 | 4-φ18 |
There are several types of pilot operated valves available in the market, including:
1.Direct Acting Pilot Valves: These valves use a direct acting pilot valve to control the main valve. They are typically used in low-pressure applications.
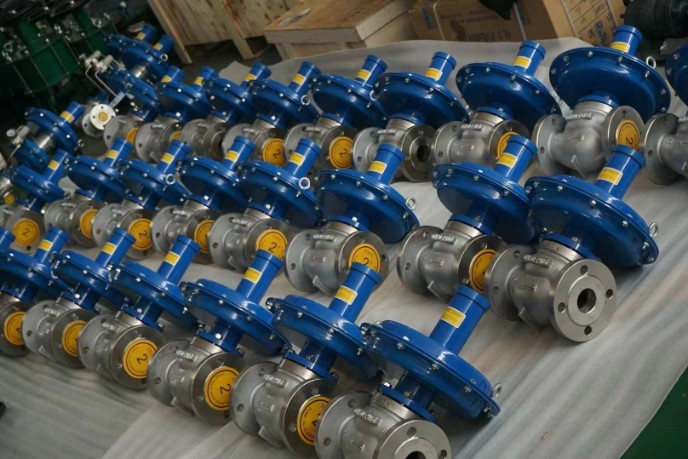
2. Indirect Acting Pilot Valves: These valves use an indirect acting pilot valve to control the main valve. They are typically used in high-pressure applications.
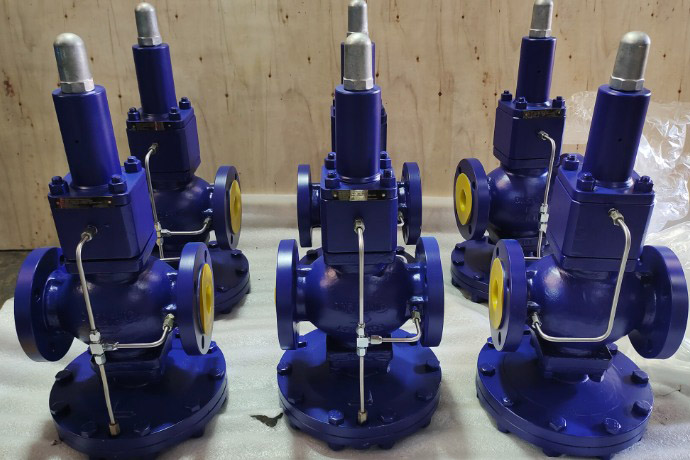
3. Differential Pressure Pilot Valves: These valves use a differential pressure pilot valve to control the main valve. They are typically used in applications where the pressure drop across the valve is high.
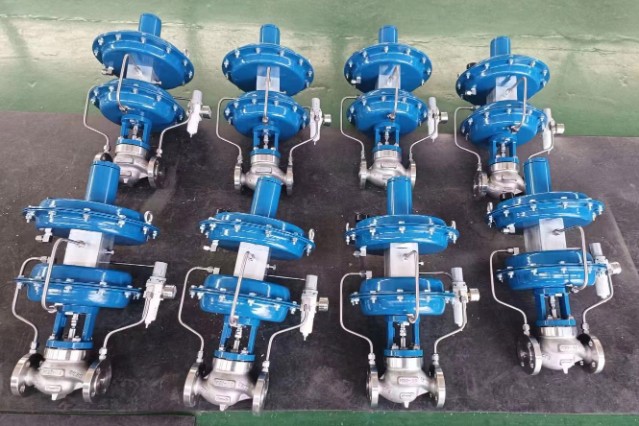
Selecting the Right Pilot Operated Valves
When it comes to selecting the right pilot operated valve for your application, there are a few key factors to consider. Pilot operated valves are an essential component in many hydraulic systems, and selecting the wrong valve can lead to inefficiencies, downtime, and increased costs. In this article, we will cover the different types of pilot operated valves, how to choose the right one for your application, and best practices for installation and maintenance. There are several factors to consider, including:
1. Temperature
Make sure the valve is rated for the pressure and temperature of the fluid in your system.
2. Pressure Range
The pressure range is the range of pressures that the valve is designed to operate within. This includes both the inlet pressure and the outlet pressure. It is important to select a valve that can handle the pressure range required by your system.
3. Flow Rate
The flow rate is the amount of fluid that needs to pass through the valve in a given time period. This is typically measured in gallons per minute (GPM) or liters per minute (LPM). Selecting a valve with the appropriate flow rate is critical to ensuring proper system performance.
4. Valve Size
The size of the valve refers to the diameter of the valve orifice. This is typically measured in inches or millimeters. Selecting the right valve size is critical to ensuring proper flow rates and pressure drop.
5. Material
Make sure the valve is made of the right material for your application.
6. Fluid Compatibility
The pilot operated valve must be compatible with the type of fluid being used in the system. This includes considerations such as fluid viscosity, temperature, and chemical compatibility.
7. Installation and Maintenance
Proper installation and maintenance are critical to ensuring the long-term performance of the pilot operated valve. This includes considerations such as valve orientation, mounting position, and periodic maintenance such as cleaning and lubrication.
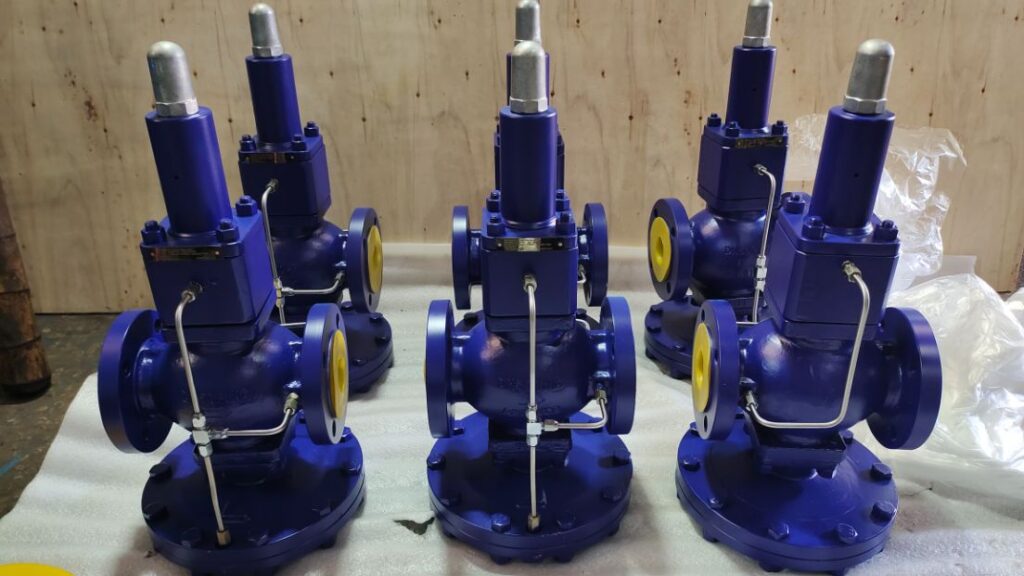
Applications of Pilot Operated Valves
Pilot operated valves are commonly used in a wide range of industries, including oil and gas, chemical, pharmaceutical, and food and beverage. Some of the common applications of pilot operated valves include:
Pressure Control
Pilot operated valves are often used to control the pressure of fluids in pipelines and tanks. By using a pilot valve to control the main valve, the pressure can be maintained at a constant level, even with changes in flow rates.
Temperature Control
Pilot operated valves can also be used to control the temperature of fluids in a system. By using a temperature sensor and a pilot valve, the main valve can be adjusted to maintain the desired temperature.
Flow Control
Pilot operated valves can also be used to control the flow of fluids in a system. By using a flow meter and a pilot valve, the main valve can be adjusted to maintain a specific flow rate.
Pilot operated valves have a wide range of applications in various industries, including:
- Steam systems: These valves are often used in steam systems for boiler feedwater control, steam distribution, and condensate recovery.
- Process control: Pilot operated valves play a crucial role in process control systems, such as chemical, petrochemical, and pharmaceutical plants, where accurate flow regulation is essential.
- Power generation: In power plants, pilot operated valves regulate the flow of steam or other fluids, ensuring optimal performance and safety.
- Oil and gas: These valves control the flow of oil, gas, and other fluids, maintaining consistent pressure and flow rates in pipelines and processing plants.
- Water treatment: Pilot operated valves regulate water flow and pressure in treatment plants, ensuring the consistent delivery of clean water.
- Chemical processing: In chemical plants, these valves control the flow of hazardous or corrosive chemicals, ensuring safe and efficient processing.
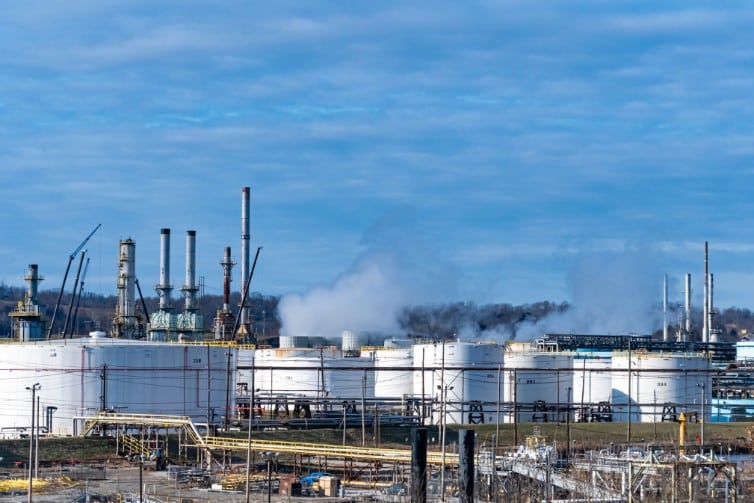
Advantages and Disadvantages
Advantages
- High capacity: Pilot operated valves can handle high flow rates and pressure drops, making them ideal for large-scale industrial applications.
- Precision control: These valves offer excellent control over fluid flow, providing a high degree of accuracy and responsiveness.
- Wide range of applications: Pilot operated valves can be used in a variety of industries and applications, making them a versatile choice.
Disadvantages
- Complexity: The additional components and interconnections required for pilot operated valves can increase their complexity and cost.
- Maintenance requirements: Pilot operated valves may require more frequent maintenance due to the potential for wear and tear on the pilot valve and sensing line.
Maintenance and Troubleshooting for Pilot Operated Valves
Pilot operated valves are essential components in various industrial and commercial systems, providing efficient flow control and regulation. To keep pilot operated relief valves ensure their proper functioning and longevity, regular maintenance and troubleshooting are necessary. Here are some key maintenance and troubleshooting tips for pilot operated valves:
- Regular Inspection: Periodically inspect the valve assembly for any signs of wear, corrosion, or damage. Check for leaks around the valve and look for any unusual noises or vibrations that could indicate an issue.
- Cleanliness: Keep the valve and surrounding area clean and free from debris. Contaminants can cause the valve to malfunction or become blocked. Regularly clean the valve’s strainer or filter to ensure proper flow.
- Lubrication: Lubricate the valve’s moving parts as recommended by the manufacturer. Proper lubrication will ensure smooth operation and reduce wear on components.
- Periodic Testing: Test the valve’s functionality at regular intervals. This will help you identify any issues early on and prevent potential system failures.
Troubleshooting Chart for Pilot Operated Valves
Valve fails to open or close:
a. Check the pilot valve for any blockages or debris. Clean and replace if necessary.
b. Inspect the diaphragm or piston for damage. If damaged, replace the faulty component.
c. Ensure that the pressure differential is within the operating range specified by the manufacturer. If the pressure is too low, the valve may not function properly.
Valve leaks:
a. Inspect the valve seat for damage or debris. Clean or replace the seat if necessary.
b. Check the diaphragm or piston for damage or wear. Replace if needed.
c. Verify that the valve is properly assembled and tightened. If loose, tighten the valve components.
Valve chatters or vibrates:
a. Ensure that the flow rate is within the valve’s specified operating range. If the flow rate is too high or too low, the valve may experience instability.
b. Inspect the pilot valve for blockages or debris. Clean or replace if necessary.
c. Check the valve’s pressure differential. If it is too low or too high, the valve may not function properly. Adjust the system pressure accordingly.
Valve response is slow or sluggish:
a. Inspect the pilot valve for blockages or debris. Clean or replace if necessary.
b. Check the diaphragm or piston for damage or wear. Replace if needed.
c. Verify that the valve’s pressure differential is within the operating range specified by the manufacturer. Adjust the system pressure if necessary.
Issue | Possible Cause | Solution |
Valve fails to open or close | • Blockages or debris in pilot valve • Damaged diaphragm or piston • Pressure differential outside operating range | • Clean or replace pilot valve • Replace damaged component •Adjust system pressure |
Valve leaks | • Valve leaks,Damaged or dirty valve seat • Damaged diaphragm or piston • Loose valve assembly | • Clean or replace valve seat • Replace damaged component • Tighten valve components |
Valve chatters or vibrates | • Flow rate outside operating range • Blockages or debris in pilot valve • Pressure differential outside operating range | • Adjust flow rate • Clean or replace pilot valve • Adjust system pressure |
Slow or sluggish valve response | • Blockages or debris in pilot valve • Damaged diaphragm or piston • Pressure differential outside operating range | • Clean or replace pilot valve • Replace damaged component • Adjust system pressure |
Remember, regular maintenance and prompt troubleshooting are essential to ensure the longevity and efficient operation of pilot operated valves. Always consult the manufacturer’s guidelines and seek professional assistance if needed.
Conclusion
Pilot operated valves are an essential component in many industrial processes, and choosing the right valve can have a significant impact on the efficiency and reliability of your system. By understanding the functionality, applications, and types of pilot operated valves, as well as the factors to consider when choosing a valve, you can make an informed decision and ensure that your system operates at peak performance. If you need help choosing the right pilot operated relief valve for your application, contact our experts, and we’ll be happy to assist you.
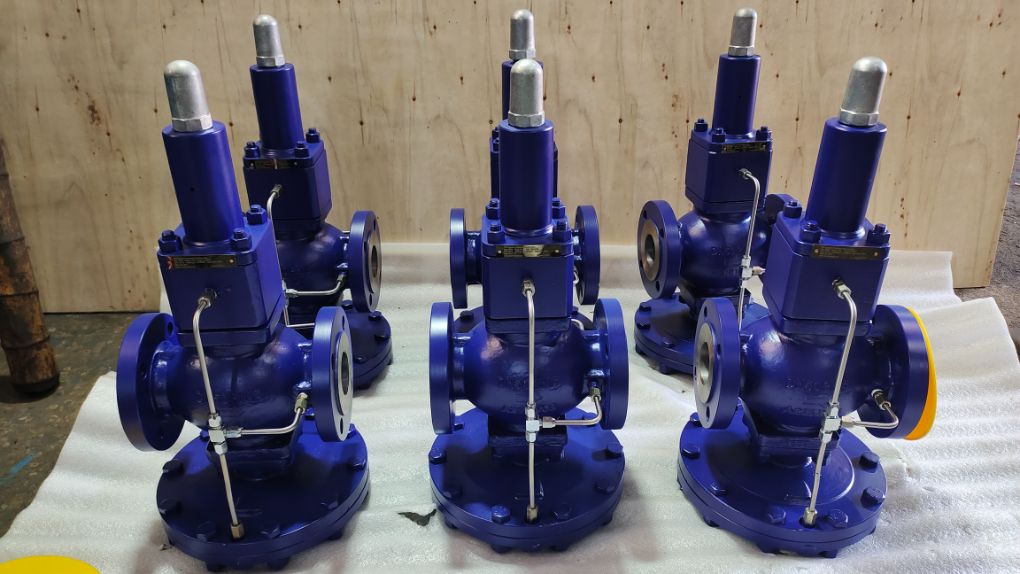
Additional Information on Pilot Operated Valves
Pilot operated valves can also be categorized based on their function. Some of the common types of pilot operated valves based on their function are:
- Relief Valve: These valves are designed to release pressure in a system when it exceeds a certain level. They are often used in safety applications to protect equipment and personnel from overpressure.
- Pressure Reducing Valve: These valves are designed to reduce the pressure of a fluid in a system to a desired level. They are commonly used in applications where high pressure can damage equipment or cause safety concerns.
- Solenoid Valve: These valves are operated by an electric signal and are commonly used in automation applications. They are often used in applications where quick and precise control of fluid flow is required.
- Proportional Valve: These valves are designed to provide precise control of fluid flow based on an electrical input signal. They are commonly used in applications where accurate control of flow rate is critical.