This essay will outline the fundamental distinctions between ball valves and gate valves. “THINKTANK,” a leading China-based provider of industrial valves, will explain all you need to know about these valves.
Selecting the correct valve may have a significant impact on the success or failure of a pipeline system. Today, there is a vast selection of valves on the market, and it may be quite challenging to choose the ideal valve for a certain application. Ball and gate valves are the most popular valves used in pipeline systems and industrial applications.
Ball Valves vs. Gate Valves
In the industrial process, ball valves and gate valves can be seen everywhere in the pipeline, they both have the function of closing and opening the flow channel, but the same shut-off function, when to use the ball valve, when to use the gate valve? I know you need some expert advice for your application, and in this post, I will walk you through the expanded definition of ball valves and gate valves, How do they work, what’s pros and cons them, which typical types are they, and what’s the exact application they used for?
Expanded Definition
What Are Ball Valves?
Ball valves use a rotating ball to control the flow of a liquid or gas. The medium travels through a hole (or holes) in the ball, and its location determines whether the valve is open or closed.
Ball valves may have several ports. For typical on/off control, two-way ball valves feature two ports. Multi-port ball valves are also available and are utilized in situations where media must be transmitted in several commands or when more than one media source is required. Ball valves are faster on/off control alternative than gate valves since they need just a 90° dependency on regulating the position of the ball. Ball valves with manual or pneumatic/electric actuators are widely available.
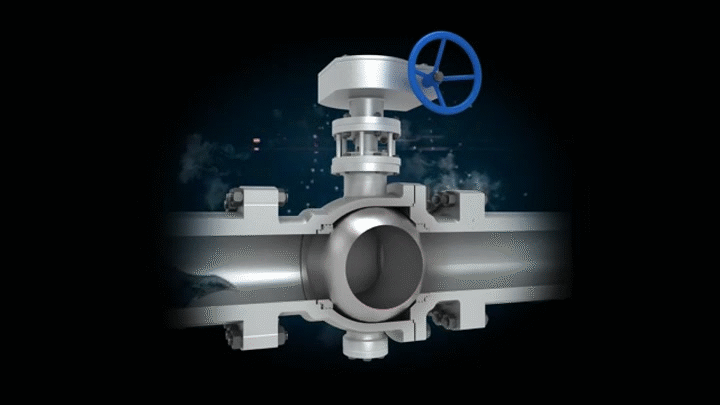
The ball valve belongs to the family of quarter-turn valves. It requires a 90-degree rotation to open or close. The disc of a ball valve is a ball that has been hollowed down to facilitate the passage of media. Ball valves are mostly used for non-slurry applications, although they are also suitable for applications requiring a tight shut-off.
The fast opening and closing of the ball make it essential for some media isolation applications.
What Are Gate Valves?
Gate valves are used to completely start or block the flow of fluid via a pipeline by raising or lowering a solid gate. A valve body, seat, disc, actuator, shaft, and gland are all components of gate valves.
Gate valves are only used to completely open or completely close lines; they are not utilized to manage flow or pressure. These valves require more than 360° of multi-turn motion to change the position of the valve, whereas ball valves only need 90° of action to go from open to closed or from closed to open, which means gate valves are needs more time to shutoff or full open valve. Because of this, gate valves might not be the ideal option for applications requiring frequent operation or quick cycling. Gate valves are most commonly operated with a manual handwheel, but pneumatic and electric actuation options are also available.
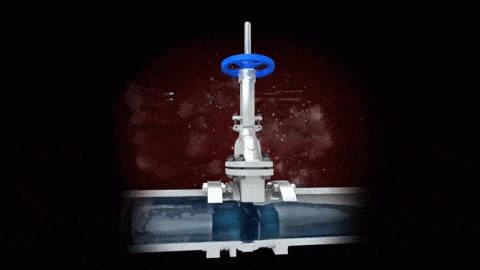
Furthermore, gate valves are a member of the linear motion valve family. The gate valve features a flat or wedge-shaped disc that serves as a gate. The flow of fluid within the valve is controlled by this gate. The gate valve works well when linear media flow with little pressure drop is desired.
How Do Ball Valves Work?
The ball valve developed from the plug valve, it has a ball as its opening and closing component and rotates the ball 90 degrees around the stem’s axis to accomplish opening and closing. Ball valves are mostly used in pipelines to distribute media flow, stop, and change its direction.
They are built with an O-type or V-shaped orifice. Ball valves are effective in controlling flow. Ball valves are one of the valve types that have grown the fastest over the past ten years. They have a straightforward structure, good sealing performance, compact design, lightweight, less material consumption, small installation size, and little driving torque. Ball valves are used for a variety of applications including high temperature, high pressure, wide range size, high sealing, long service life, and multi-functional.
Various Ball Valve Types
The ball valve can be categorized in three different ways.
Body Pieces Types
- 1-Piece
- 2-Pieces
- 3-Pieces
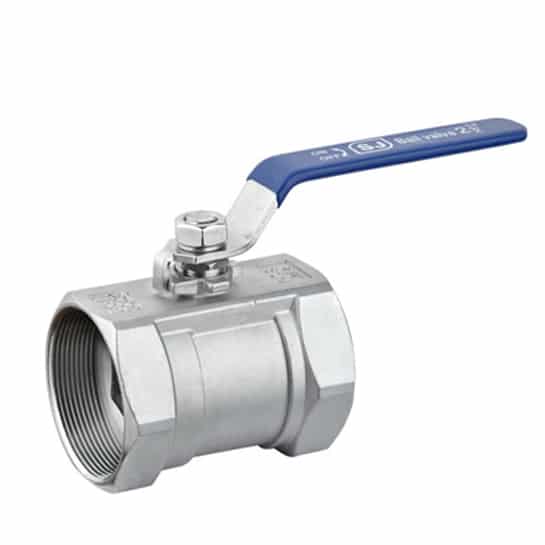
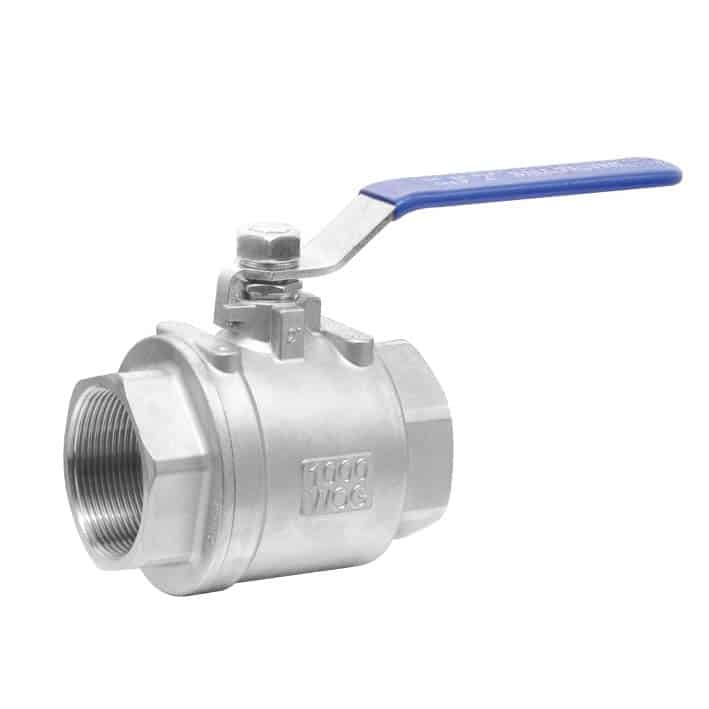
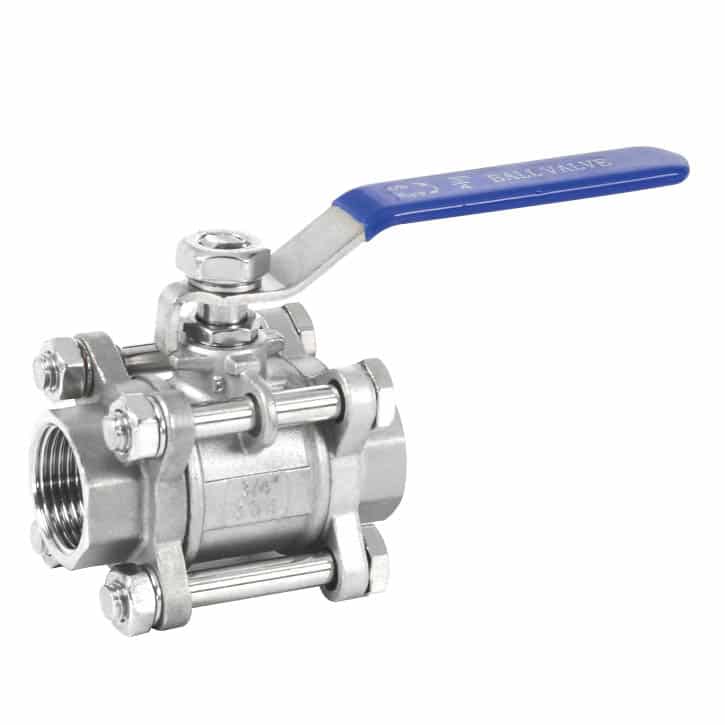
Ball Types
- Float Ball
- Fixed/Trunnion Ball
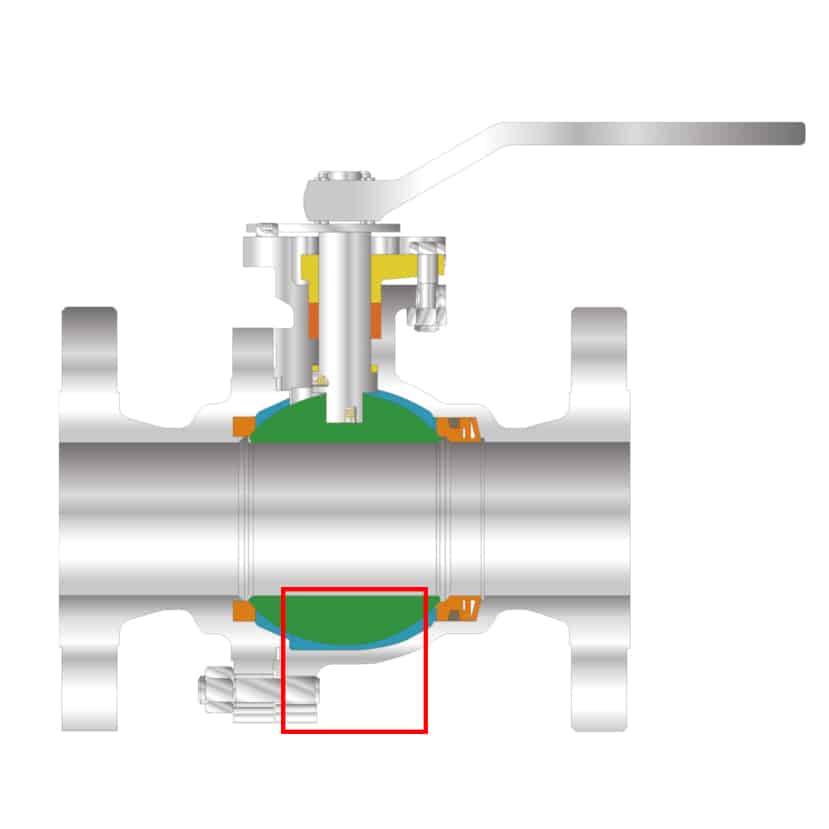
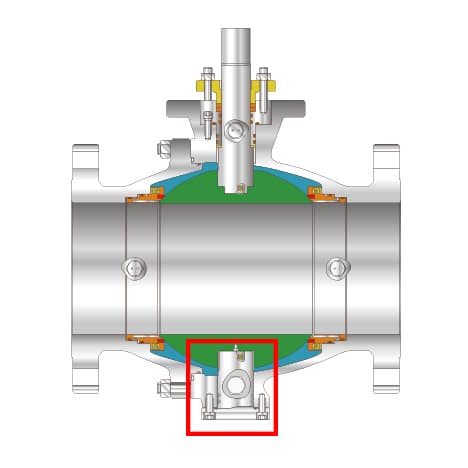
Port Type
- Full Port
- Reduced Port
- V Port
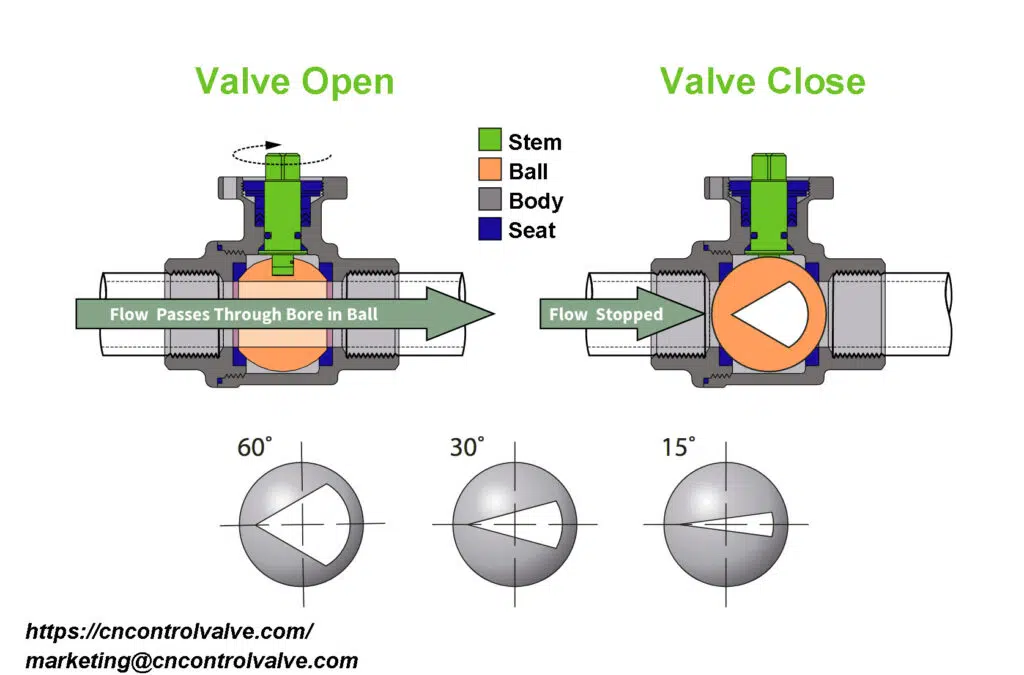
How Do Gate Valves Work?
First, Let’s learn the main components of the gate valve through the following figure.
- Body
- Bonnet
- Solid Wedge
- Body Seat
- Stem
- Back Seat
- Gland Follower
- Gland Flange
- Stem Nut
- Yoke Nut
- Handwheel
- Handwheel Nut
- Stud and Bolts
- Nuts
- Stud Bolts
- Nuts
- Bonnet Gasket
- Lubricator
- Gland Packing
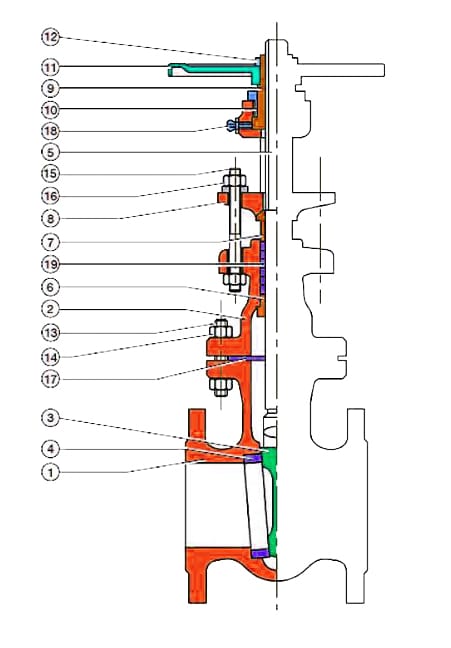
The operation of gate valves involves raising the gate or disc to enable the media to flow through. These valves permit only unidirectional flow with little pressure loss.
There are two types of stem designs for gate valves. One is the rising stem gate valve, this handwheel raises the stem to the outside environment and simultaneously raises the gate when turned. The second kind of stem is a non-rising gate valve. This is distinguished by a stem that is inserted into the wedge, exposing it to the media.
Rising Stem Gate Valve, OS&Y Bonnet, Outside Stem & York
When you open a gate valve with a rising stem, the stem moves up and the stem will rise above the handwheel, when you close the valve, the stem moves down. It is depicted in the picture. The OS&Y design means outside stem and york, it’s more frequently described as the rising stem gate valve.
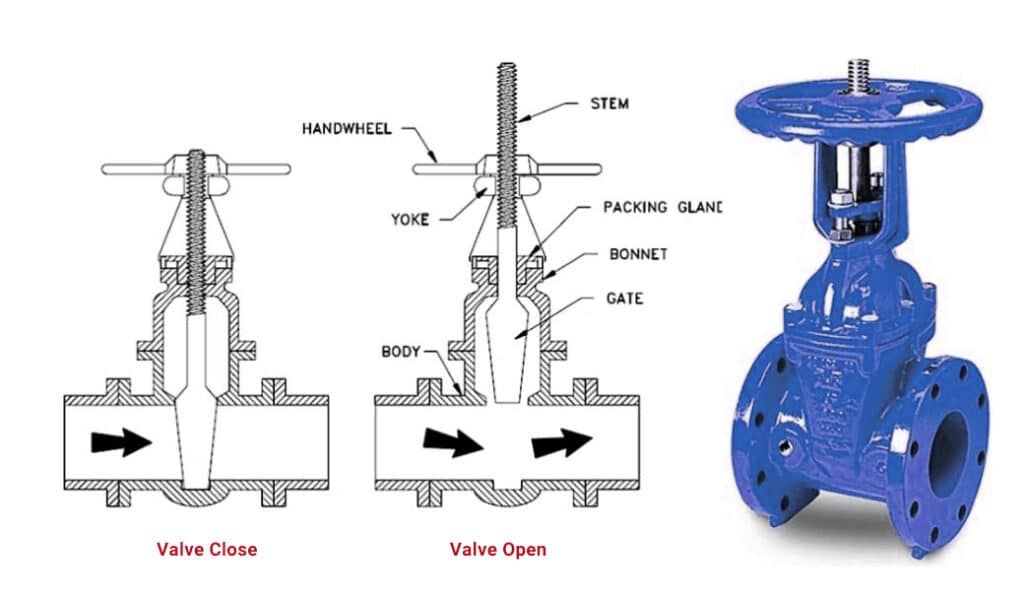
Non-Rising Stem Gate Valve, Inside Screw Stem
The above figure is the non-rising stem gate valve, you can see when the valve is closed or opened, the valve stem is not rising.
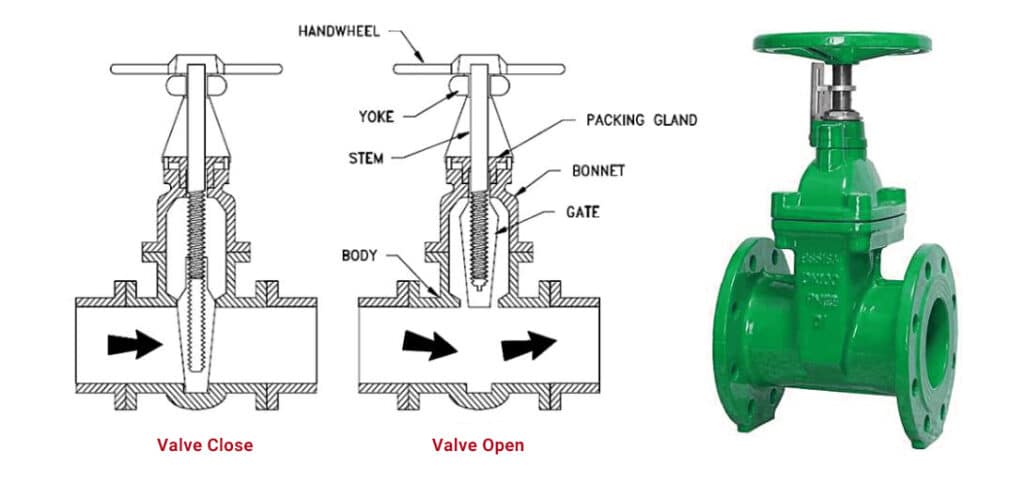
When the gate valve is opened, the passageway expands. As seen in the diagram below, the flow route is not linear in the sense that the medium may fill the vacuum. If the gate valve is employed as a throttle, the flow rate would be inconsistent. This will result in a vibration. These vibrations might cause gate damage.
Various Gate Valve Types
The gate valve can be categorized in three different ways.
Disc Types
- Flexible Wedge Gate Valve
The flexible wedge is a solid, one-piece disk with a perimeter incision. The size, form, and depth of these incisions vary. Less flexibility is provided but strength is maintained via a shallow, thin cut across the wedge’s perimeter. Although it reduces strength, a cast-in recess or a broader and deeper cut on the wedge’s perimeter increases flexibility.
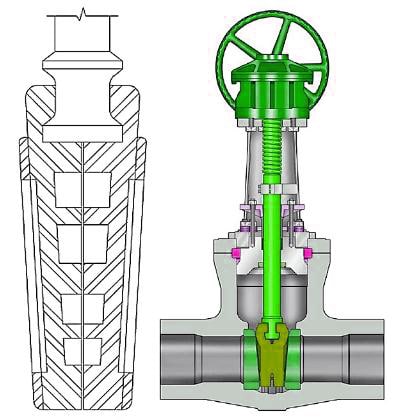
This layout offers improved leak tightness and seat alignment. Additionally, it enhanced performance when heat binding was a possibility. adjustable wedges Steam systems employ gate valves.
The deformation of valve bodies caused by the thermal expansion of the steam line can occasionally result in thermal blindness. The flexible gate eliminates thermal blindness by allowing the gate to stretch as the valve seat contracts as a result of the steam pipeline’s thermal expansion.
Line fluid has a propensity to gather in the disc, which is a drawback of flexible gates. These may cause corrosion, which would degrade the disc in the end.
- Solid Taper Wedge Gate Valve
The most popular and extensively utilized variety of discs is a solid wedge because of its strength and simplicity. A solid wedge valve may be fitted anywhere and is appropriate for practically all fluids. Additionally, it applies to turbulent flow.
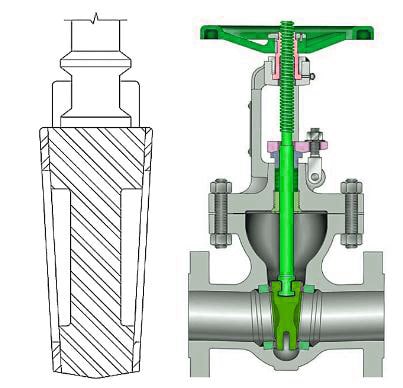
- Split Wedge /Parallel Gate Valve
A split wedge disc is made up of two solid sections that are held together by a unique mechanism. The disk is free to align itself with the sitting surface in the event that one half of the disk is out of alignment. The split disk may have a wedge shape or take the form of a parallel disk.
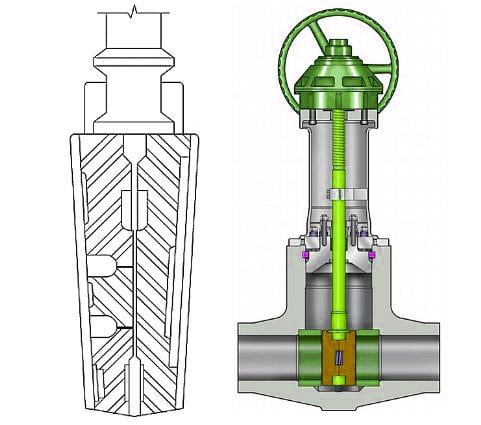
Since parallel discs are spring-loaded, they always make contact with the seats and provide sealing in both directions. At both normal and high temperatures, the split wedge can handle noncondensing gases and liquids.
Even if the valve was closed when the line was cold, the disc’s freedom of movement avoids thermal binding. This indicates that when a line is heated by a fluid and expands, thermal blindness is not produced.
Bonnet Types
- Bolted Bonnet
This is the most widely used design and is seen in many gate valves. The bonnet and body must be sealed with a gasket.
- Screwed Bonnet
This is the most basic design that is utilized for low-cost valves.
- Welded Bonnet
This is a common design that doesn’t need disassembly, and compared to the bolted-bonnet gate valve, the welded-bonnet gate valve is lighter than theirs.
- Pressure Seal Bonnet
The pressure seal bonnet gate valves are widely used for high-pressure and high-temperature applications. The force on the gasket of a pressure seal gate valve increases with the body cavity pressure.
But it doesn’t make up for changes in the alignment of the seat caused by pipe loads or thermal expansion. As a result, this kind of disk design is most prone to leakage. Thermal locking occurs when a solid wedge is applied in high-temperature conditions.
If it’s used for high temperatures, it will cause the metal expansion, and that thermal locking makes a wedge stuck between the seat. So the solid wedge gate valve is commonly serviced for low-pressure and moderate-temperature conditions.
Stem Types
- Rising Stem Gate Valve(OS&Y)
- Non-Rising Stem Gate Valve
Ball Valve vs. Gate Valve Difference Points
Difference Points | Ball Valve | Gate Valve |
---|---|---|
Cost | Higher costs | Lower costs |
Operation | 90 Degree operation to open and close the valve. | 360 Degree multi-turn to shut off or open the valve. |
Application | High-frequency cycle action, tightly closed, no impurities in gas&oil, water, steam, air, etc. | Better suitable for non-frequent operation applications, slurries, and media that are viscous or with particles. |
Size | 1/4” to 20” | 2” to 40″ (suitable for large pipeline systems) |
Ports | Two ports, three ports, and multi-ports | Two ports. |
Installation Space | More face-to-face distance than gate valve, and require quarter turn handle design for operation. | Compact installation space. |
Leakage | Excellent tight shutoff | Prone to leaks more often than a ball valve |
Reliability | High performance and reliable quality. | Less resilient and vulnerable to damage |
Maintenance | Readily maintainable and repairable | Less maintenance and repair tasks |
Ball Valve vs. Gate Valve: Pros and Cons
Name | Pros | Cons |
Ball Valve | ☑ Reliable tight off performance ☑ Quick cycle speed ☑ High-pressure and high-temperature condition ☑ Long service lifetime ☑ Wide range of material options | × Not ideal for regulating the flow × Fast cycle time can lead to a water hammer × For the large size, the cost of the ball valve is much higher than the gate valve |
Gate Valve | ☑ Economical option for isolation condition ☑ Bi-directional Large size Little resistance to the media flow ☑ Excellent shutoff | × Definitely can not control the flow × A large differential drop pressure will cause the water hammer × Prone to leaks means less durable than ball valves × Need more time to fully open and shut off the valve × If at a partially open position, it will cause vibration and noise More difficult to repair than the ball valve |
Summarize
The kind of fluid running through your pipeline will determine whether you select a ball valve or a gate valve. We also take into account the cost budget. Careful evaluation of the advantages and disadvantages will help you choose the best valve for your circumstance. If you have any other questions, just feel free to contact us for a free consultation.