Ball valves are essential components of most industrial liquid and gas control systems. There are a wide variety of ball valves available to meet different industrial requirements, each with its unique set of features and benefits. Understanding the different types of ball valves is critical for anyone working with industrial equipment, as choosing the right type of ball valve can ensure proper function, reduce downtime, and increase the system’s overall performance.
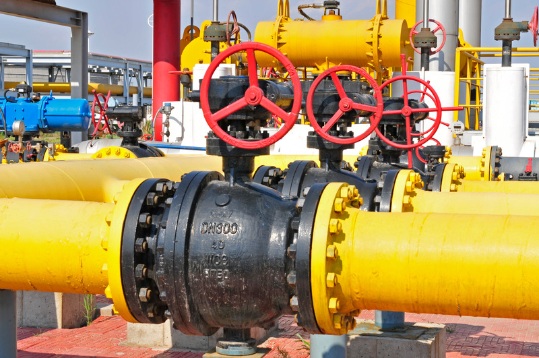
What are ball valves
Ball valves are quarter-turn valves that have a pivoting ball inside the valve body with a hole drilled through the center. The ball’s movements control whether the valve is open or closed, and when the valve is closed, the ball completely blocks fluid or gas flow through the valve. Ball valves are common components of most industrial liquid and gas control systems. They are particularly useful for applications where precise control and shutoff are necessary, as they operate quickly and are relatively easy to automate.
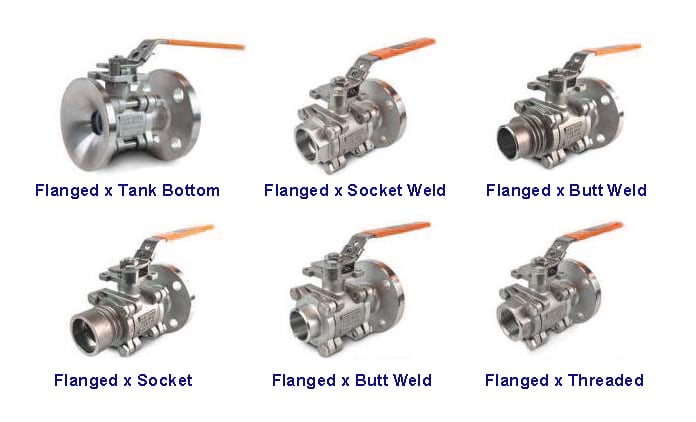
Importance of choosing the right type of ball valve
Choosing the right type of ball valve is crucial for ensuring proper function, reducing downtime, and increasing the overall performance of industrial equipment. Within each type of ball valve, there are different variations that suit different applications. Factors that influence the type of ball valve needed for industrial applications include flow rate, pressure, temperature, corrosion resistance, and fluid or gas type. Selecting the right ball valve ensures that the valve can handle the specific application’s conditions, preventing premature valve failure or malfunction, and maintaining the efficiency of the system. Furthermore, selecting the right ball valve can have an impact on maintenance costs, system safety, and energy consumption.
ball valve components
Ball valves consist of several components that work together to regulate the flow of fluid or gas through the valve. Here are the main components of ball valves:
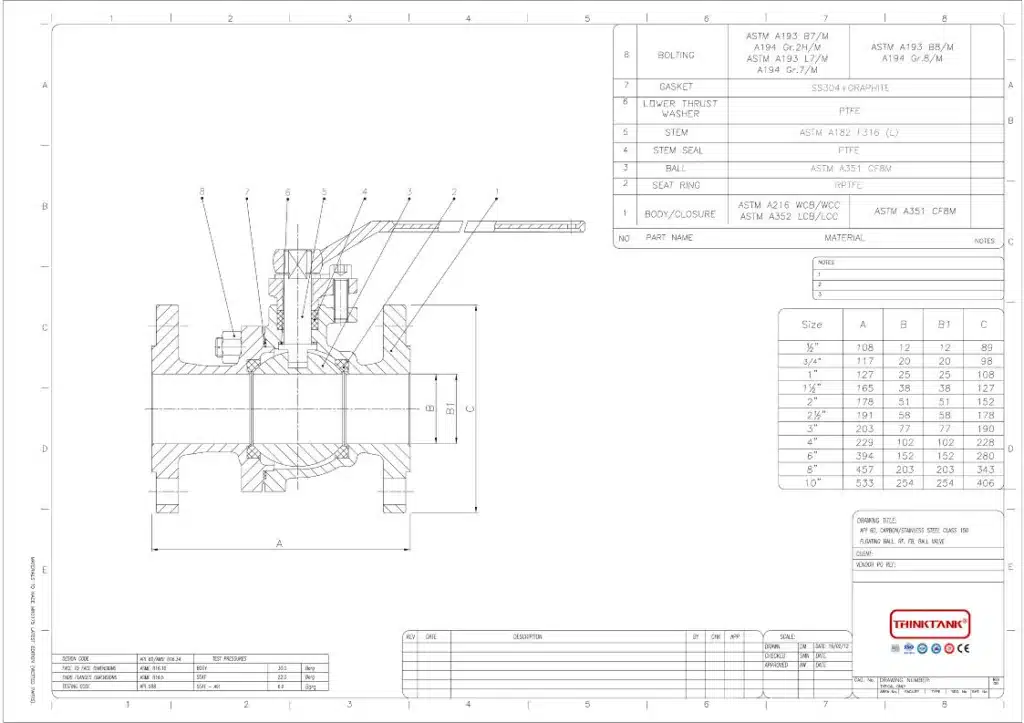
- Body: a valve’s main component that valve housing the ball and stem assembly.
- Ball: a spherical-shaped component that controls the flow of fluid or gas.
- Seat: a component that provides a seal between the ball and the valve body.
- Stem: a component that connects the actuator to the ball, allowing it to rotate and regulate the flow.
- Actuator: a component that applies the force necessary to open and close the valve.
- Packing: a component that prevents the escape of fluid or gas along the stem.
- Bonnet: a component that covers the stem and contact with the actuator, protecting them from damage.
- Gland: a component that compresses the stem seal, ensuring a tight seal and preventing leaks.
- Stem nut: a component that secures the stem to the actuator, ensuring proper operation.
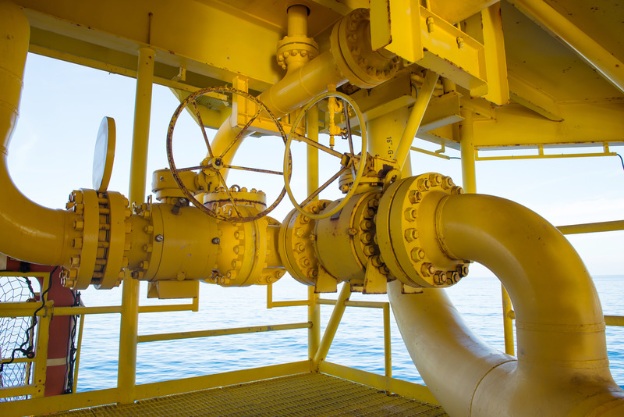
ball valve internal
Ball valve internals refers to the components inside the valve that control, and shut off the flow of fluid or gas. The main internal components of a ball valve include the ball, seat, packing, stem, gasket, and sealings.
uses of ball valve
Ball valves can be used in a wide range of industrial applications due to their high precision flow control and shut-off, low maintenance, and high durability. Some common uses of ball valves include:
Oil and gas industry
Ball valves are commonly used in the oil and gas industry for applications such as wellheads, pipelines, and storage tanks.
Chemical processing industry
Ball valves are frequently used to regulate the flow of chemicals, acids, and other corrosive materials in chemical processing facilities.
Water and wastewater management
Ball valves are commonly used to manage the flow of water and wastewater in treatment plants, distribution systems, and other water storage facilities.
HVAC systems
Ball valves are often used in heating, ventilation, and air conditioning (HVAC) systems to regulate the flow of hot water or chilled water.
Agriculture
Ball valves are commonly used in irrigation systems to control the flow of water.
Marine industry
Ball valves are widely used in the marine industry for applications such as seawater intake and discharge lines, ballast systems, and fire suppression systems.
Pharmaceuticals and food processing
Ball valves are used in pharmaceutical and food processing applications where cleanliness is critical, due to their ease of cleaning and their ability to avoid contamination.
Overall, ball valves are versatile and can be used in a wide range of industries and applications where high-precision flow control and shut-off, low maintenance, and high durability are required.
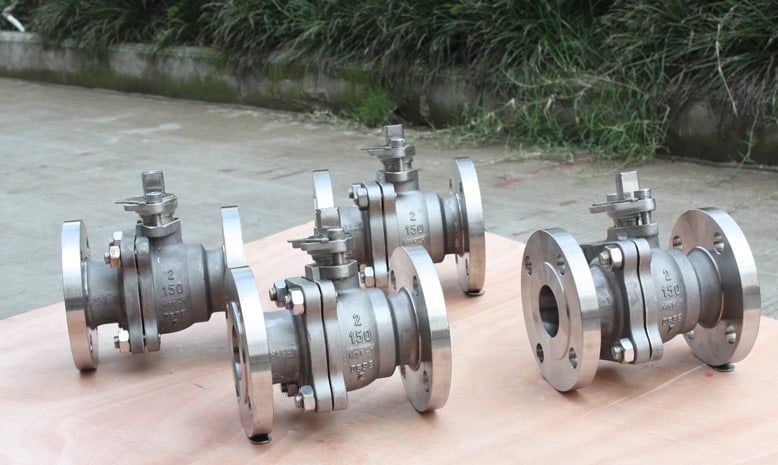
what is a ball valve used for
A ball valve is used to regulate and on/off the flow of fluid or gas through a pipe or tubing. The valve works by rotating a ball inside of the valve body, which either allows or obstructs the flow of fluid or gas. Ball valves are commonly used in industrial applications such as oil and gas, chemical processing, water and wastewater management, and many other industries due to their ability to regulate flow with precision and their durability and reliability. Ball valves are also preferred in many applications because they can be quickly opened and closed, which makes them ideal for emergency shut-off situations. Additionally, because of their design, they do not become clogged easily and can handle high temperatures and pressures. Overall, ball valves are used where high precision flow control and shut-off, low maintenance, and high durability are required.
what does a ball valve look like
A ball valve typically has a spherical-shaped casing that contains a ball with a hole or port in the middle. The ball has a stem on one end, which is connected to an actuator that controls the rotation of the ball. The actuator can either be a manual handle or an electric or pneumatic system, which turns the ball a quarter-turn (90 degrees) to control the flow of fluid or gas through the valve. The valve may also have additional attachments such as a flange or a coupling to connect to pipes or tubing. The specific design and size of a ball valve can vary depending on its intended use and the industry in which it is used.
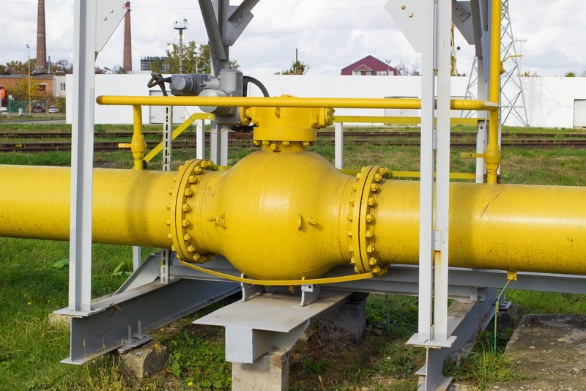
force ball valves
There are several factors that can affect the torque force required to operate a ball valve, including:
Valve size
The larger bore diameter of the valve, the more torque force required to operate it. This is because the ball and stem assembly in larger valves are heavier and require more force to rotate.
Pressure and temperature
The higher the pressure or temperature of the fluid or gas flowing through the valve, the more torque force required to operate it. This is because the pressure and temperature increase the resistance against the ball and stem assembly.
Fluid density
The density of the fluid flowing through the valve can also affect the torque force required to operate it. Fluids with higher densities require more force to move the ball and valve stem in assembly.

Here is a table of approximate torque values for different ball valve sizes operating torque:
Valve Size | Torque Range |
---|---|
1/4″ – 1/2″ | 5-10 Nm |
3/4″ – 1″ | 20-40 Nm |
1 1/4″ – 2″ | 60-100 Nm |
2 1/2″ – 3″ | 150-250 Nm |
4″ – 6″ | 500-800 Nm |
8″ – 10″ | 1000-2000 Nm |
12″ – 14″ | 2500-5000 Nm |
It is important to note that these values are only approximate and may vary depending on the specific factors discussed above. It is always important to refer to the manufacturer‘s recommendations for the specific ball valve being used and to ensure that the valve is properly installed and maintained to ensure safe and efficient operation.
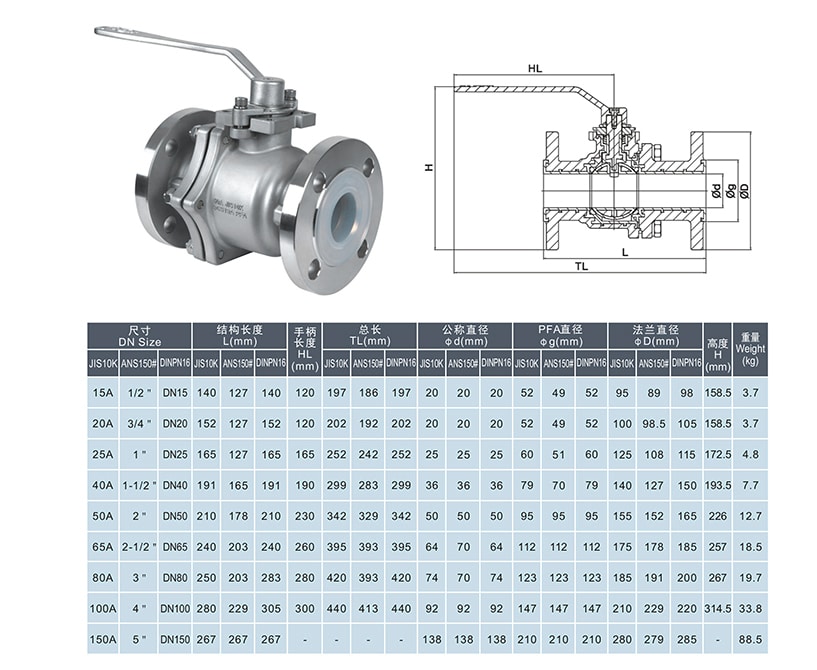
ball valve purpose
The purpose of a ball valve is to regulate the flow of fluid or gas through a pipe or tubing system. It works by rotating a ball that has a hole or port in the middle, which either allows or blocks the flow of fluid or gas. Ball valves are commonly used in a wide range of industrial applications due to their high precision flow control and shut-off, low maintenance, and high durability. They are preferred in many applications due to their ability to quickly open and close, making them useful in emergency shut-off situations. Additionally, because of their design, they do not become clogged easily and can handle high temperatures and pressures. The specific use of the ball valve will depend on the industry and application, but is often used in industries such as oil and gas, chemical processing, water and wastewater management, and many others. Overall, the purpose of a ball valve is to provide efficient and precise fluid flow, control, shut-off, and regulation in various industrial settings.
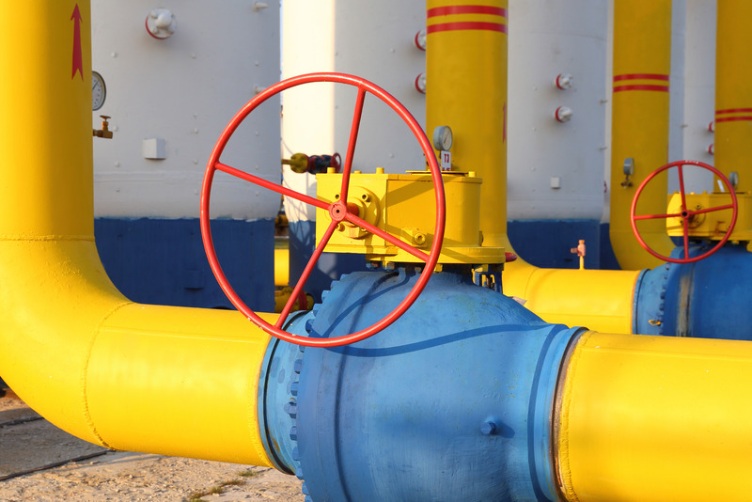
how ball valves work
When the valve is open, the ball is rotated by an actuator, which is typically a manual handle or electric/pneumatic system, and allows the fluid or gas to pass through. As the ball is rotated, the hole or port aligns with the inlet and outlet ports in the valve body, allowing the fluid or gas to flow freely.
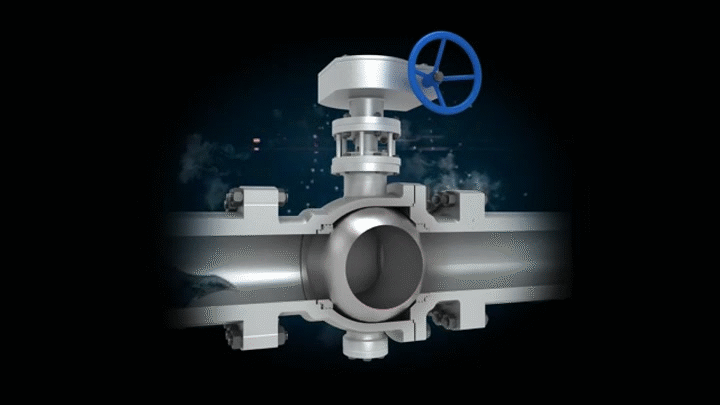
When the valve is closed, the ball is rotated back into a position that blocks the flow of fluid or gas. This is achieved by rotating the ball 90 degrees away from the inlet and outlet ports, which closes off the flow of the fluid or gas. The ball has a seat, which is usually made of a resilient material such as Teflon, that forms a seal against the valve body and prevents the fluid or gas from leaking out.
function of ball valve
The function of a ball valve is to regulate and on/off the flow of fluid or gas through a piping system with a high degree of precision. Ball valves work by using a ball with a hole or port in the middle that rotates inside a valve body to either allow or block the flow of fluid or gas. The ball is connected to an actuator, which can be a manual lever or an electric or pneumatic system. When the valve is open, the ball is rotated by the actuator and allows the fluid or gas to flow through the hole or port in the ball.
When the valve is closed, the ball is rotated to a position that blocks the flow of the fluid or gas. The ball is in closed position rotated 90 degrees away from the inlet and outlet ports of the valve, which closes the valve and prevents the fluid or gas from flowing through. A seat made of a resilient material such as Teflon forms a seal against the valve body, preventing any leakage of fluid or gas.
Different Types of Ball Valves
Floating Ball Valves
Floating ball valves are one of the most common types of ball valves used in industrial applications. These valves have a simple design in which the ball is suspended in the valve body by two valve seats, one at the upstream end and the other at the downstream end. The rotary ball itself’s movement is controlled by a stem that connects it to the actuator. When the valve is open, the ball rotates to allow fluid or gas to flow through the valve. When the valve is closed, the ball rotates 90 degrees, blocking the flow.
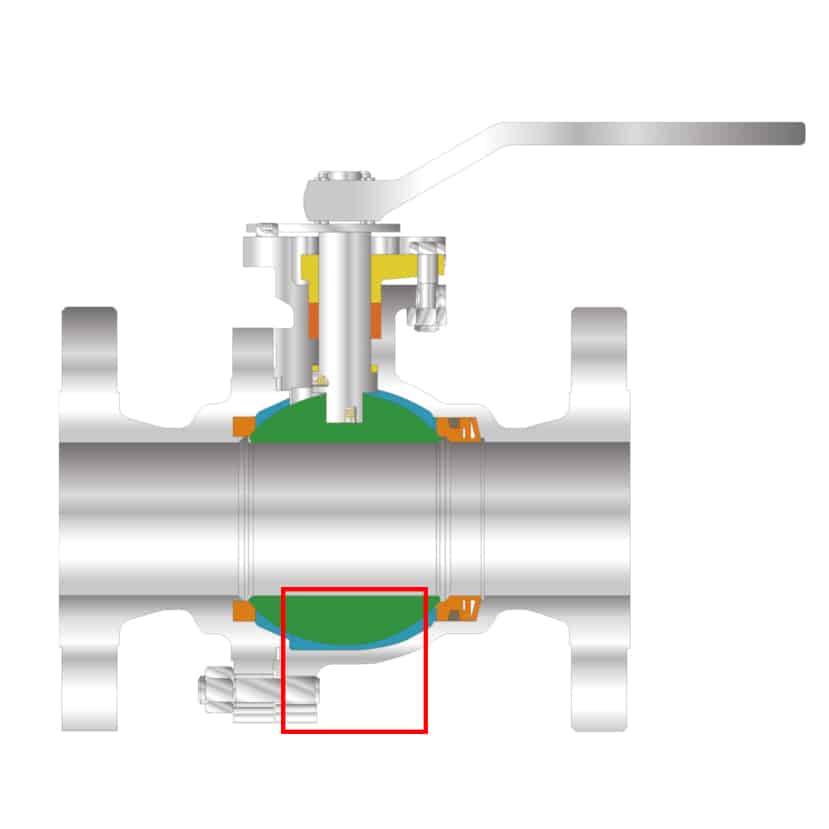
Floating ball valves come in a variety of sizes and materials, making them suitable for use in a wide range of applications. They are relatively inexpensive and easy to maintain, thanks to their simple design. However, they are not ideal for all applications, as they may experience some valve seat’ wear and leakage due to the ball’s movement. Additionally, the seats may become damaged if the valve is not closed gently and can build up debris between the valve seats and the ball leading to a reduction in lifespan.
Advantages | Disadvantages |
---|---|
Simple design | May Experience Leakage Due to Seat Wear |
Relatively Low Cost | Limited Range of Sizes |
Easy to maintain | Seats May Become Damaged if Valve is Not Closed Gently |
Suitable for a Wide Range of Applications | Buildup of Debris Between Valve Seats and the Ball |
Quick and Easy to Automate | Limited to Applications with High Pressure and Temperature |
Tight Shut-Off When Closed | Not Suitable for Conditions with Particulate Impurities |
Trunnion Mounted Ball Valves
Trunnion Mounted Ball Valves are a type of ball valve that uses additional mechanical anchoring at the ball’s top and bottom to ensure it is held securely within the valve body. These valves have a fixed ball design, where the ball is not suspended in the valve body like the floating ball valve but rather held in place by the trunnion. Trunnion mounted ball valves are designed to handle high pressure and high flow rates and are suitable for use in challenging applications such as the oil and gas industry.
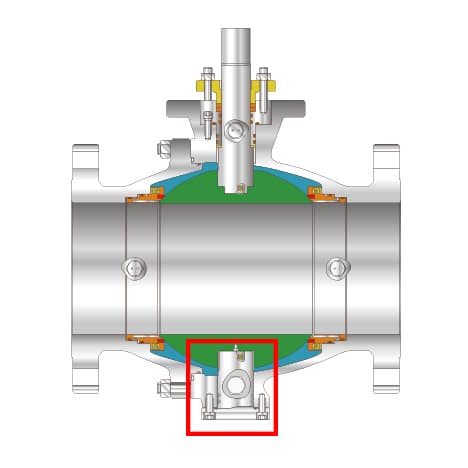
Trunnion-mounted ball valves have several advantages, including being able to handle high flow rates and high pressure. These two piece or three-piece ball valves are ideal for applications in which productivity is critical, and safety must not be compromised. Additionally, trunnion-mounted ball valves provide a reliable seal, reducing the chance of leakage.
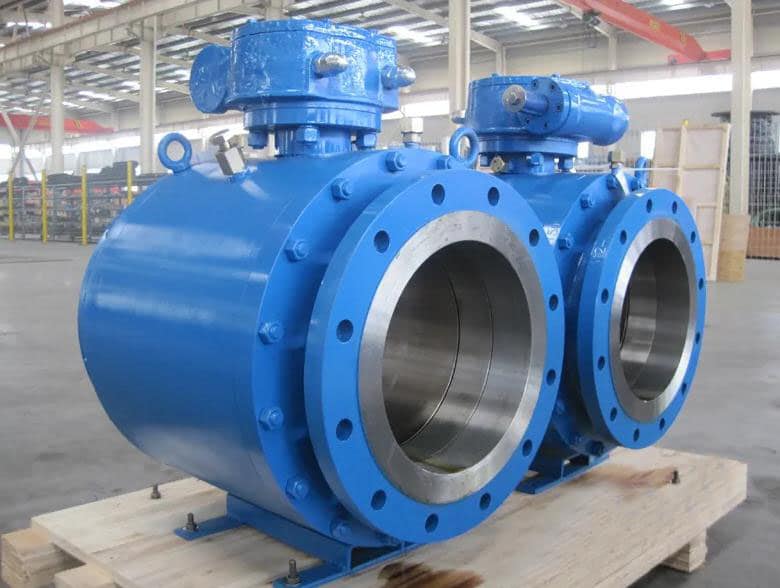
However, there are also some disadvantages to trunnion-mounted ball valves. These types of valves have a more complex design than floating ball valves, which means that they are generally more expensive. Furthermore, they may require more maintenance due to their complexity, which translates into higher costs. Trunnion-mounted ball valves are typically heavier and larger, requiring more space, which may pose space limitations in some applications.
Advantages | Disadvantages |
---|---|
Suitable for high flow rates and high pressure applications | More complex design than floating ball valves |
Reliably seal and reduce the chance of leakage | Generally more expensive compared to floating ball valves |
Ideal for applications in which productivity is critical | Requires more maintenance due to their complexity |
Reliable Performance and Tight Shut-off | Heavier and larger requiring more space for installation |
V-Port Ball Valves
V-Port ball valves are a type of ball valve that is designed to provide a more precise flow control compared to other types of ball valves. In V-Port ball valves, the ball has a V-shaped notch, which allows for accurate flow control by providing variable flow areas that can be easily adjusted to meet application requirements. V-Port ball valves are suitable for use in a wide range of applications that require precise control, such as in the chemical, petrochemical, and oil and gas industries.
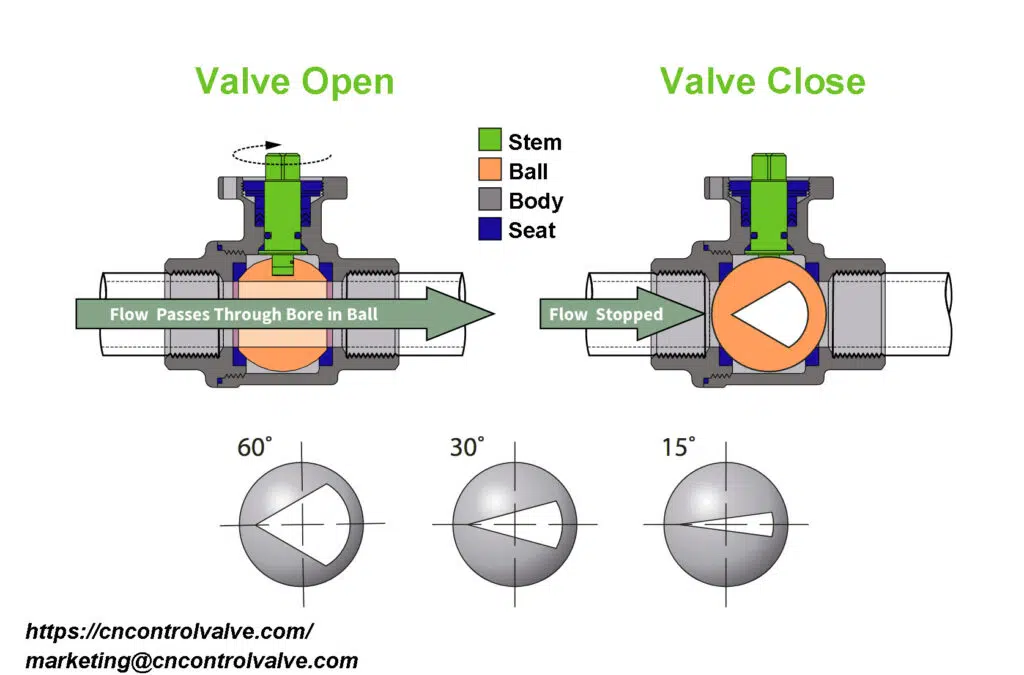
V-Port ball valves have several advantages, including their high degree of accuracy in controlling flow and the ability to maintain a constant flow rate across a wide range of pressures. They also offer high-temperature and high-pressure capabilities, which make them suitable for use in demanding applications. In addition, V-Port ball valves are available in different sizes, materials, and configurations, making them versatile and able to handle different types of media.
However, there are also some disadvantages to V-Port ball valves. Their design is more complex than other ball valves, which can lead to higher maintenance requirements and costs. They are also more expensive than other types of ball valves and may require specialized equipment to install and maintain. V-Port ball valves may also be prone to erosion due to the high velocity of the fluid passing through the valve, which can lead to shorter lifespans.
Advantages | Disadvantages |
---|---|
Precise flow control | More complex design than other ball valves |
Maintain constant flow rate across wide range of pressures | Higher maintenance requirements and costs |
High-temperature and high-pressure capabilities | More expensive than other types of ball valves |
Available in different sizes, materials, and configurations | Prone to erosion due to the high velocity of the fluid passing through |
Cavity Filled Ball Valves
Cavity Filled Ball Valves are designed to prevent fluid from becoming trapped inside the ball valve cavity, which can lead to issues like corrosion, contamination, and damage to the valve body. In these types of ball valves, the space between the ball and the valve body is filled with a cavity filling material, such as PTFE, to prevent buildup of fluid in the valve cavity. Corrosion-resistant materials are typically used to construct the two pieces or three pieces ball valve and body to ensure that the ball valve can withstand harsh chemicals and high temperatures.
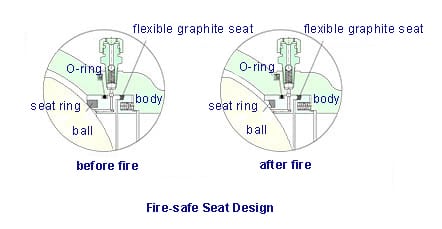
Cavity filled ball valves have several advantages, including their ability to prevent the buildup of corrosive materials inside the valve, reducing the risk of damage to the valve body and ensuring smooth operation. They are suitable for a range of applications, including in chemical and food processing industries. Additionally, they offer good accuracy and regulation of flow control even under high pressure.
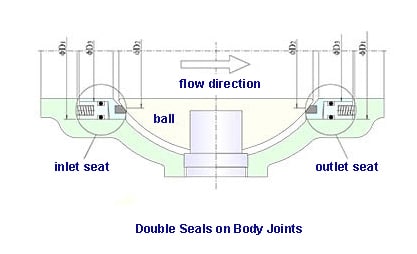
However, there are also some disadvantages to cavity filled ball valves. They can be more expensive than other types of ball valves due to their specialized design. Furthermore, they may require more maintenance than other types of ball valves, requiring the replacement of the cavity filling material to ensure continued proper function long service life. Cavities valves are also more prone to leakage, therefore regular maintenance is important in extending their lifespan.
Advantages | Disadvantages |
---|---|
Prevents fluid buildup in the valve cavity | More expensive than other types of ball valves |
Suitable for a range of applications, including corrosive materials | Requires routine maintenance, including cavity filling material replacement |
Ensures smooth operation of the valve | More prone to leakage compared to other types of ball valves |
Offers good accuracy and regulation of flow control |
Conclusion of Different Types of Ball Valves
Now we know the common types of ball valves used in industrial applications. Each type of ball valve has its advantages and disadvantages, and choosing the appropriate one depends on the specific application’s requirements, pressures, temperatures, and fluid or gas types.
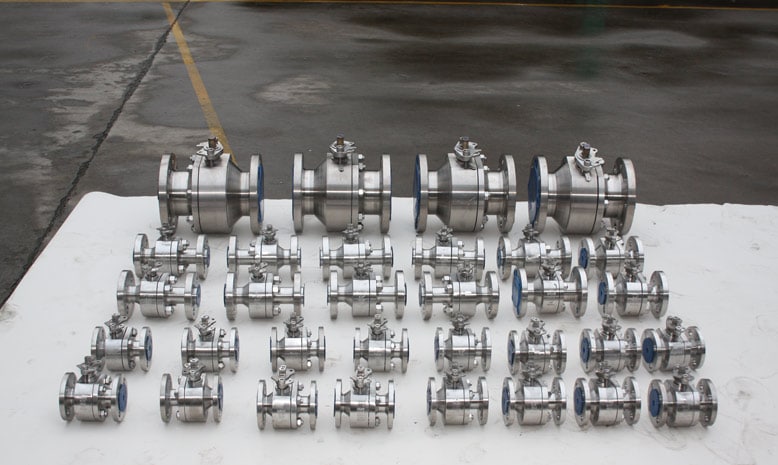
THINKTANK is a professional ball valve manufacturer based in Taiwan and mainland China. With three decades of experience in the industry, THINKTANK has become a trusted and reliable source of high-quality ball valves. We offer a wide range of ball valves in various sizes and configurations, including full port, reduced port, two-way, three-way, and multi-port valves. All ball valves are made with high-quality materials such as stainless steel, special alloy, carbon steel, and brass, and are designed to provide precise flow control, shut-off, and regulation in various industrial applications. THINKTANK is dedicated to providing exceptional customer service and support and is committed to delivering innovative products that meet the evolving needs of our customers. Welcome to contact us at any time.
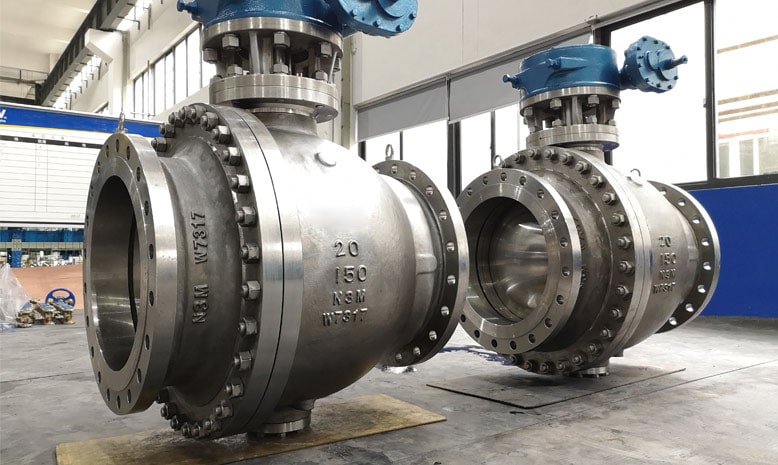