Pressure relief valves stand as crucial components in industrial setups when the system reaches maximum pressure, designed to maintain normal operating pressure and avoid the dangers of excess pressure generated by the system. The adjustment of pressure relief valves to the right set pressure is crucial for their proper functioning and preventing the system pressure from reaching its maximum. In cases of pressure relief valve failure or other pressure relief valves malfunctioning, the integrity of the system is compromised posing a serious risk. This article will explore the details of pressure relief valve failure, exploring how regular maintenance and understanding the valve’s set pressure are essential for preventing downtime and sustaining a safe operational environment.
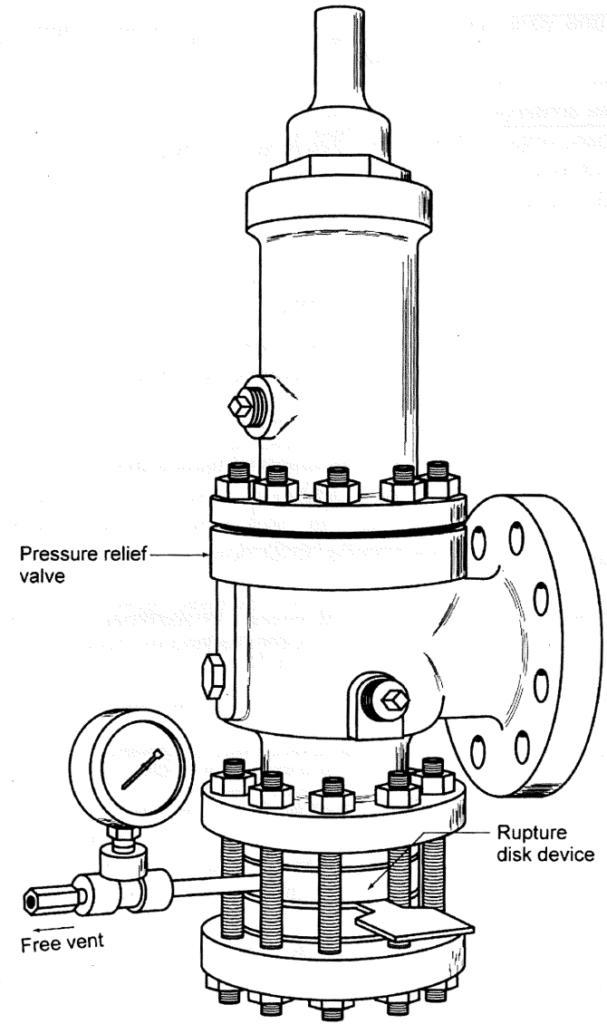
Signs of Pressure Relief Valve Failure
Pressure relief valves play a pivotal role in maintaining the delicate balance of industrial systems, but their failure shows clear signs that require immediate attention attention.
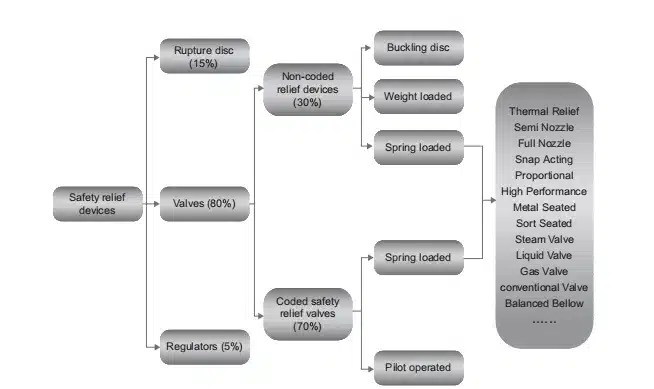
A. System Cannot Reach Pressure
Possible Causes and Solutions
If your system struggles to attain its designed pressure, potential issues with the pressure relief valve may be at play. Adjusting the valve to the correct set pressure should be a primary consideration.
Changes in the plant design without Adjusting the pressure relief valves may lead to early releases. Adjusting the valve’s set pressure is vital to align with the system’s new normal operating pressure.
B. System is Over Maximum Pressure
Causes and Troubleshooting for Overpressure Situations
If your system exceeds the maximum pressure, it indicates a potential functional failure of the pressure relief valves. Recalibrate pressure relief valves and investigate the system’s overall functionality and correct set pressure are key steps in troubleshooting.

C. Pressure Relief Valve is Leaking or Has No Pressure
1. Impact on System Efficiency
pressure relief valve leaking can compromise system efficiency, leading to suboptimal production. Additionally, a pressure relief valve with no pressure may indicate issues like a plugged balance hole, a broken spring, or a loose fit.
2. Common Causes and Solutions
Causes of pressure relief valve leakage range from contaminants to misalignments. Regular maintenance, including thorough inspections and vigilant testing, is imperative to address these issues and maintain optimal valve performance.
Troubleshooting and Maintenance
A well-executed maintenance routine is the cornerstone of ensuring the longevity and reliability of pressure relief valves. Understanding the complexities of troubleshooting and proactive maintenance is crucial for sustaining optimal system performance.
A. Importance of Regular Maintenance
- Regular maintenance, including recalibrating pressure relief valves to their correct set pressure, is imperative for preventing pressure relief valve failure.
- Systematic checks and adjustments uphold the valves’ ability to function properly, reducing the risk of issues like excess pressure and leaks.
B. Testing and Inspection Procedures
- Complete testing and inspection procedures, including pressure valve leakage checks, are vital components of preventative maintenance.
- Recognizing the importance of safety relief valves, operators should implement testing protocols, ensuring these valves open at the correct set pressure to avert overpressure events.
C. Recognizing Signs of Wear and Issues
- Attentive inspection practices aim to identify signs of wear, such as worn valve stems or malfunctioning valve components, before they escalate.
- Understanding the system pressure and normal operating pressure parameters is crucial for recognizing deviations that may signal potential issues.
D. Addressing Common Problems with Pressure Relief Valves
- Troubleshooting common problems involves a comprehensive approach, including assessing the maximum pressure, recalibrating valves with wrong set pressure, and addressing issues that lead to system overpressure.
- By recognizing pressure relief valve failure as a symptom rather than the problem itself, maintenance efforts can be directed at the root causes, such as misalignments or wear, to prevent unplanned downtime.
Implementing a proactive maintenance strategy, enriched with comprehensive testing and troubleshooting, ensures that pressure relief valves continue to function optimally, upholding the safety and efficiency of industrial systems.
Understanding the Root Causes
Exploring the root causes of pressure relief valve failure unveils the broader context that shapes the reliability and effectiveness of these crucial components within industrial systems. Recognizing the greater problems behind failures provides valuable insights into the longevity and optimal functioning of pressure relief valves.
A. The Greater Problem Behind Pressure Relief Valve Failure
- Pressure relief valve failure is often a symptom rather than the problem itself, necessitating a comprehensive investigation into the underlying issues.
- Exploring causes like wrong set pressures, system overpressure, or valve misalignments allows for targeted solutions that address the core problems impacting valve performance.
B. The Lifespan of Properly Maintained Pressure Relief Valves
- When subjected to regular maintenance, including recalibration to the correct set pressure, pressure relief valves can have a lifespan of up to thirty years.
- Understanding the factors influencing the longevity of these valves underscores the significance of proactive measures to ensure extended, trouble-free service.
C. The Role of Preventative Maintenance in Valve Longevity
- Preventative maintenance emerges as a pivotal factor in prolonging the lifespan of pressure relief valves, safeguarding against common issues such as excess pressure and valve leakage.
- By addressing potential wear and issues before they escalate, preventative maintenance practices contribute significantly to sustaining the reliability and functionality of pressure relief valves.
Appreciating the greater problems behind pressure relief valve failures reveals the path to enhanced valve longevity, highlighting the indispensable role of preventative maintenance in ensuring the continued safety and efficiency of industrial systems.
Common Reasons for Pressure Relief Valve Issues
A. Operating pressure set too close to the valve’s stamped set pressure
- Operating pressure should ideally be 20% lower than the set pressure to ensure superior seat tightness.
- A minimum gap of 10% between operating pressure and set pressure is recommended.
B. System spikes above the allowable safe operating range
- Pressure exceeding the maximum allowable working pressure hinders proper valve function.
- Ensuring system pressures stay within the safe range is critical for optimal valve performance.
C. Improperly supported outlet piping
- Inadequate support for outlet piping places additional stress on the valve, hindering proper seating.
- Properly supporting outlet piping is essential to prevent valve malfunction and potential leakage.
D. Using the wrong valve for the application
- Sizing and selecting the appropriate valve is crucial for effective functionality.
- Mismatched valves can lead to operational issues, emphasizing the importance of selecting the right valve for specific applications.
Recognizing these typical causes sheds light on potential challenges that may undermine the effectiveness of pressure relief valves in preserving the reliability and efficiency of industrial systems.
Preventive Measures
A. Maintaining a gap between operating pressure and set pressure
- Ensure a substantial gap, ideally 20%, between operating pressure and the valve’s set pressure.
- This practice enhances seat tightness and overall valve performance.
B. Properly supporting outlet piping
- Sufficient support for outlet piping is crucial to prevent undue stress on the valve.
- Proper support ensures the valve functions optimally and minimizes the risk of malfunction.
C. Sizing and selecting the right valve for the application
- Accurate valve selection is essential for optimal system performance.
- Mismatched valves can lead to operational challenges, emphasizing the importance of careful selection.
D. Regular monitoring and condition assessment of all valves
- Implement routine checks and assessments to identify potential issues before they escalate.
- Regular monitoring ensures the longevity and reliability of all valves within the system.
By adopting these preventive measures, industrial operators can proactively safeguard against pressure relief valve issues, contributing to enhanced system efficiency and prolonged valve lifespan.
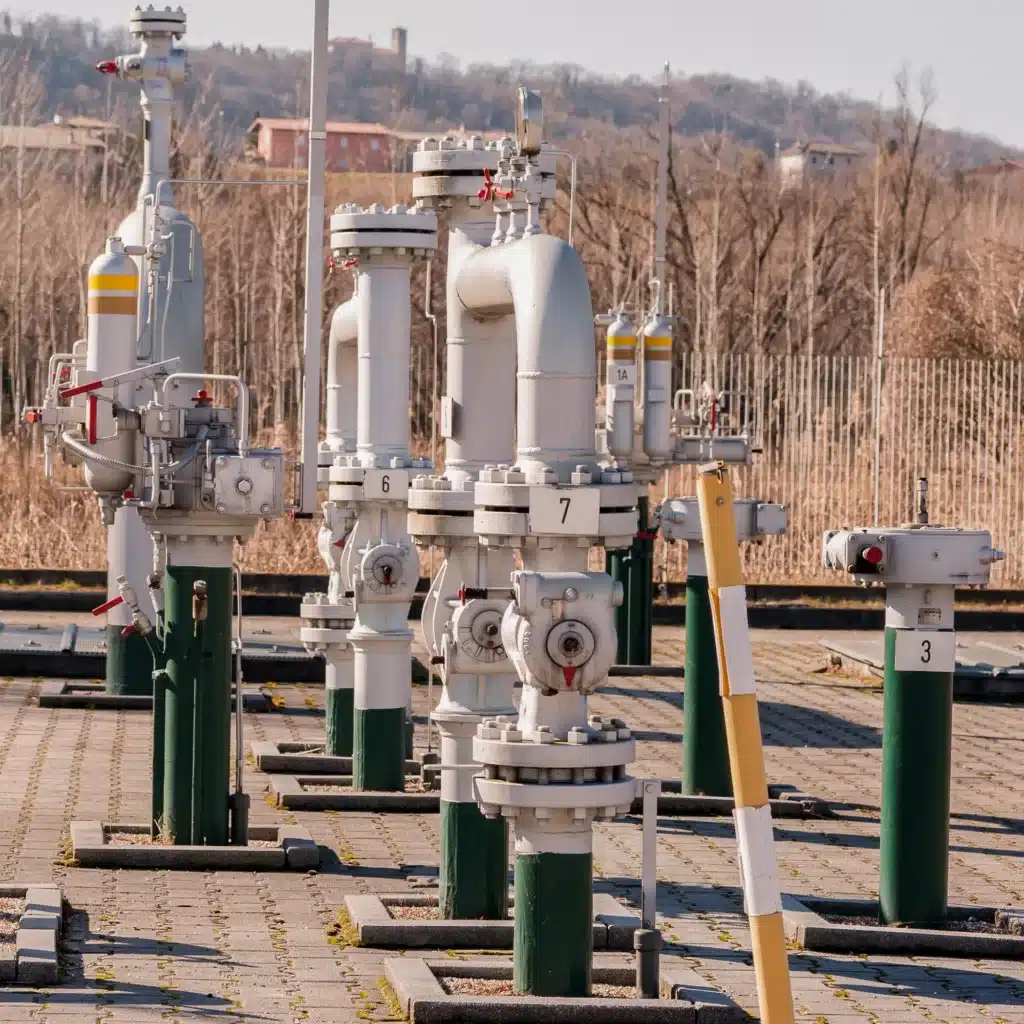
Summary
At THINKTANK, we emphasize the importance of selecting the right PRV for the application, along with proper installation, regular maintenance, and inspections to ensure reliable valve operation and prevent failures.