A sanitary control valve is a special type of valve designed to meet high standards of hygiene and cleanliness, often used in industries such as pharmaceutical, biotech, food and beverage processing, and cosmetics.
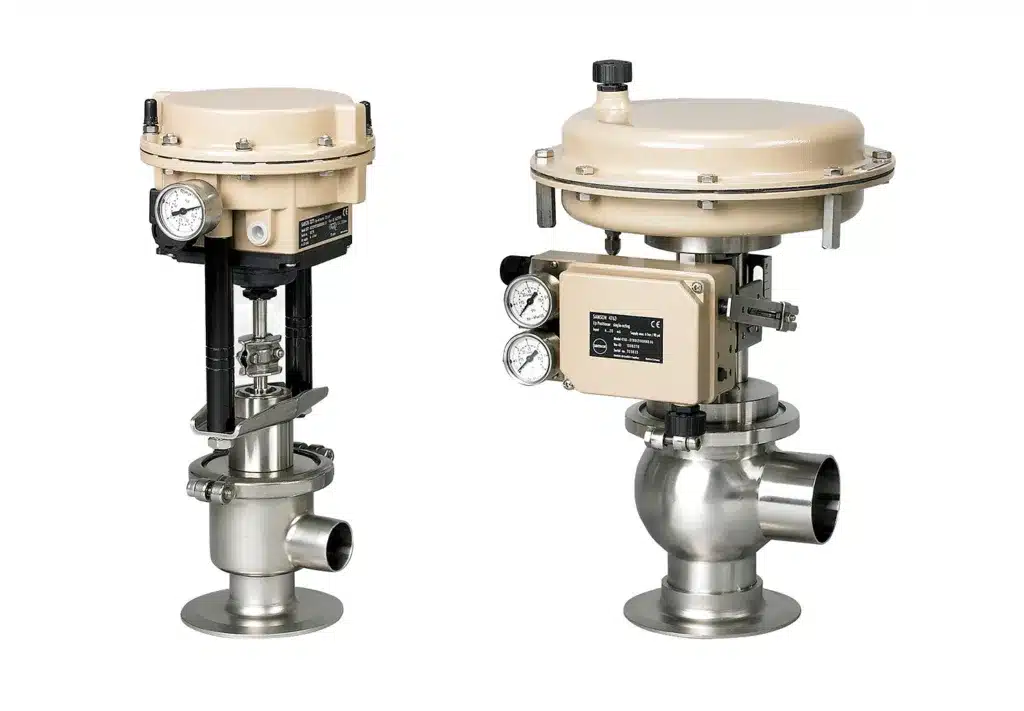
The Fundamentals of Sanitary Control Valves
Sanitary control valves are essential components in hygienic processing applications, where the cleanliness and integrity of the media are essential. They are typically found in the food and beverage, pharmaceutical, biotech, and cosmetics industries, among others. Here are the fundamentals of sanitary control valves:
Purpose
The primary function of a sanitary control valve is to regulate the flow of a liquid or gas through a pipeline, maintaining process conditions within required parameters. They ensure that the media (liquid, gas, or semi-solid) flowing through the system can be safely started, stopped, and regulated without causing contamination.
Design
Sanitary control valves are specifically designed to meet strict hygiene standards. They are typically made of stainless steel or other non-reactive, corrosion-resistant materials that can be easily cleaned and sterilized. Smooth surfaces, elimination of dead-legs, and minimized crevices are also key elements in design to avoid product build-up and bacterial growth.
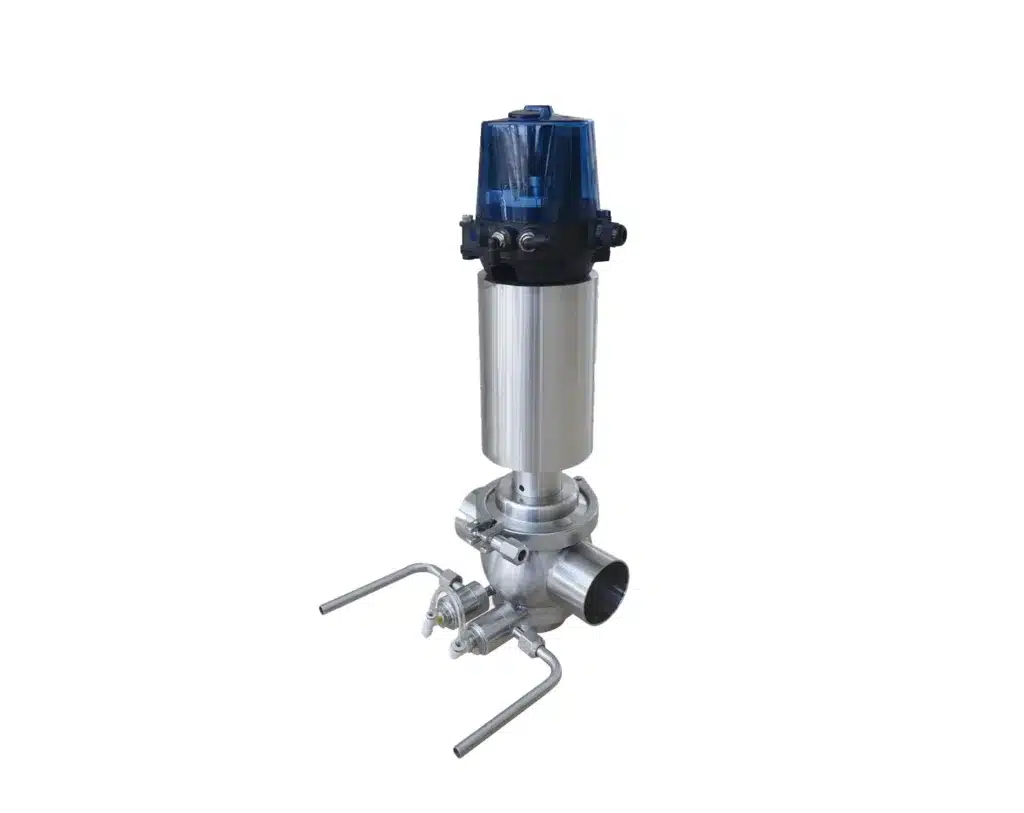
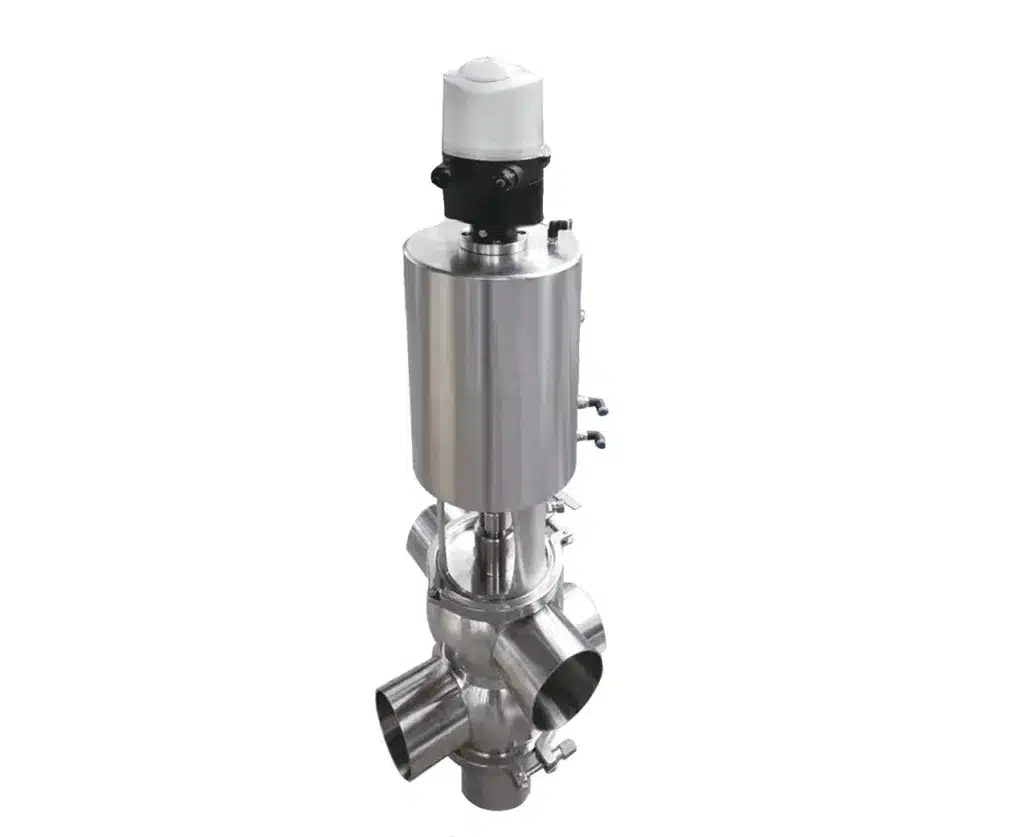
Cleaning and Sterilization
Sanitary control valves are designed for easy cleaning and sterilization. They must be able to withstand processes such as Clean-in-Place (CIP) and Steam-in-Place (SIP) to ensure the entire system remains uncontaminated.
Operation
Sanitary control valves can be manually operated or automated. Manual operation involves using a handwheel or lever to control the valve, while automated valves use actuators – either electric or pneumatic – which can be controlled remotely and integrated into a process control system.
Sealing
Sanitary control valves typically use high-purity elastomers or plastic seals that prevent leakage and contamination. These seals must be able to withstand regular cleaning and sterilization processes.
Compliance with Standards
Sanitary control valves are subject to rigorous industry and governmental standards to ensure they meet all the necessary requirements for hygiene and safety. This can include 3A sanitary standards, FDA requirements, and European Hygienic Engineering & Design Group (EHEDG) guidelines.
Types
There are different types of sanitary control valves, including ball valves, butterfly valves, diaphragm valves, and check valves. The type chosen depends on the specific application and its requirements.
Understanding these fundamentals can help in the selection, operation, and maintenance of sanitary control valves. Each application will have specific requirements, so it’s important to work with a knowledgeable supplier or engineer like THINKTANK when selecting a sanitary control valve.
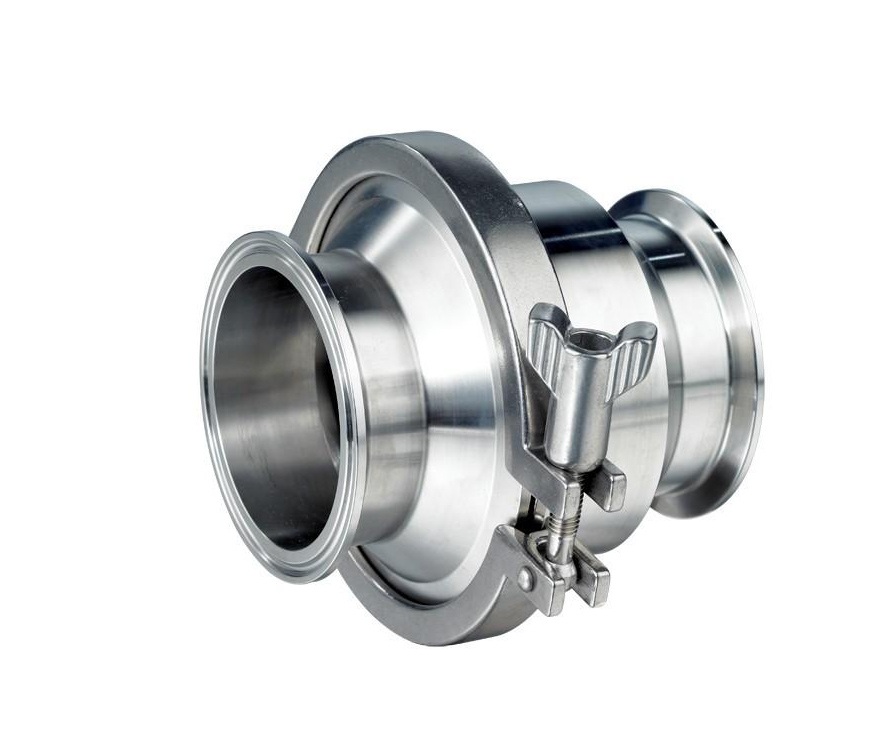
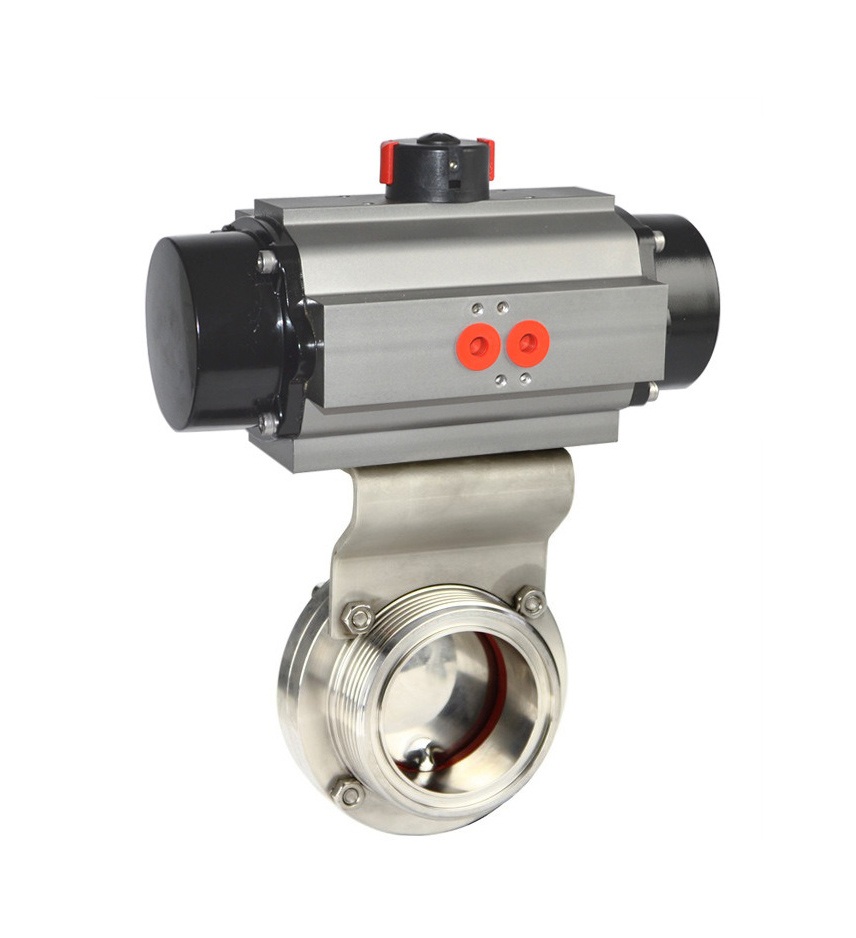
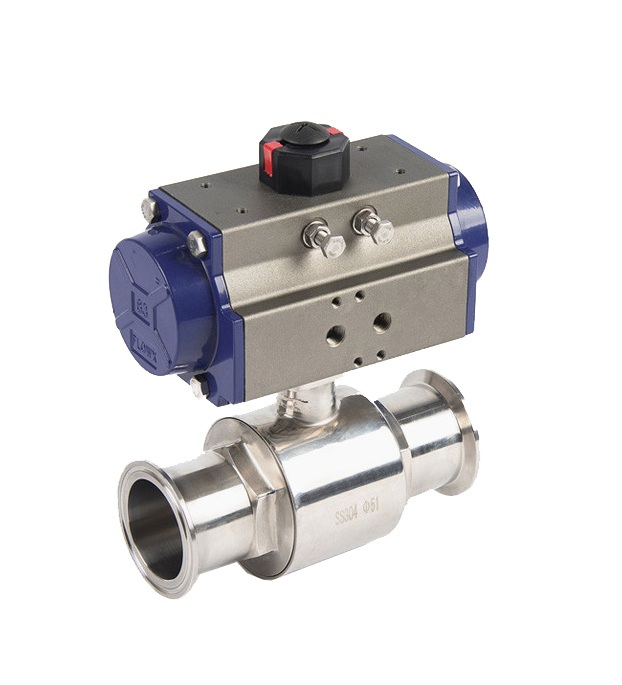
Key Components of a Sanitary Control Valve
Sanitary valves are designed and manufactured to ensure that no contamination of the process media occurs. Here are the key components of a sanitary control valve.
Valve Body
The body of the valve is the outer casing and is typically made from stainless steel or other hygienic materials. It is often designed for easy cleaning and sterilization.
Actuator
This is the component that physically moves or controls the valve. It can be either manual (hand-operated), electric, or pneumatic (air-operated). The actuator is attached to the valve stem, which in turn controls the opening and closing of the valve.
Valve Disc or Plug
This is the part of the valve that directly regulates the flow of the media. When the actuator moves the stem, the plug or disc either opens or closes the valve, depending on the design.
Stem
The stem connects the actuator and the valve disc. It transmits the actuator movement to the disc, allowing the valve to open or close.
Seat
This is the surface against which the valve disc seals. When the valve is closed, the disc contacts the seat, creating a seal that prevents flow. It’s also designed for easy cleaning and to reduce contamination.
Seals and Gaskets
These are used to ensure a tight fit and prevent leakage between different parts of the valve. They are typically made from high-purity elastomers or plastics that can withstand sterilization processes.
End Connections
These are the parts of the valve that connect to the pipeline or equipment. In sanitary valves, these are often designed to be easy to connect and disconnect for cleaning. Common types of end connections are clamp, weld, thread, and flange.
Bonnet
This part houses the stem, keeping it properly aligned with the actuator and the disc. It’s also responsible for preventing leakage from the space where the stem exits the valve body.
Each of these components plays a crucial role in the operation of a sanitary control valve and can be designed to meet specific hygienic standards, such as 3A, EHEDG, FDA, or others.
How Sanitary Control Valves Operate
Sanitary control valves, much like other control valves, operate by manipulating the flow of media (like liquids, gases, or slurries) through a system, but they do so under strict hygienic conditions. They are designed to meet high standards of cleanliness and sterilization, and their operation involves a combination of manual, automated, or semi-automated components.
Here’s a general overview of how sanitary control valves operate:
Signal Reception
The operation of a sanitary control valve often begins with the reception of a signal from a control system. This system monitors the process conditions, such as flow rate, pressure, or temperature. When the system determines that a change in flow is needed based on these parameters, it sends a signal to the valve actuator.
Actuator Response
Upon receiving the signal, the actuator, which can be either electric or pneumatic, activates. It moves to adjust the position of the valve. The actuator is typically connected to the valve stem, which in turn is connected to the disc or plug of the valve. The movement of the actuator determines whether the valve opens, closes, or partially restricts the flow.
Flow Regulation
The disc or plug inside the valve body is the component that physically interrupts or allows the flow of media. When the actuator is activated, it moves the stem and disc/plug. If the actuator moves the plug to an open position, the flow of media is allowed. If it moves to a closed position, the flow is stopped.
Sealing
When the valve is in the closed position, the disc or plug creates a seal with the valve seat, effectively preventing the flow of media. The seals and gaskets of the valve also play a crucial role in preventing leaks and ensuring the system remains sanitary.
Return to Normal Operation
Once the necessary adjustments have been made and the desired process conditions have been achieved, the control system sends a signal to the actuator to return the valve to its normal operating position, if necessary. This could mean fully opening, fully closing, or adjusting to a particular level of restriction.
Cleaning and Sterilization
Sanitary control valves are typically designed to be easily cleaned and sterilized without needing to be disassembled. This can often be done with Clean-In-Place (CIP) or Steam-In-Place (SIP) procedures, which circulate cleaning and sterilizing agents through the system to ensure it remains free of contamination.
It’s important to note that the specifics of a sanitary control valve’s operation can vary depending on the type of valve (ball, butterfly, diaphragm, etc.), the type of the media being controlled, and the particular requirements of the system in which the valve is installed.
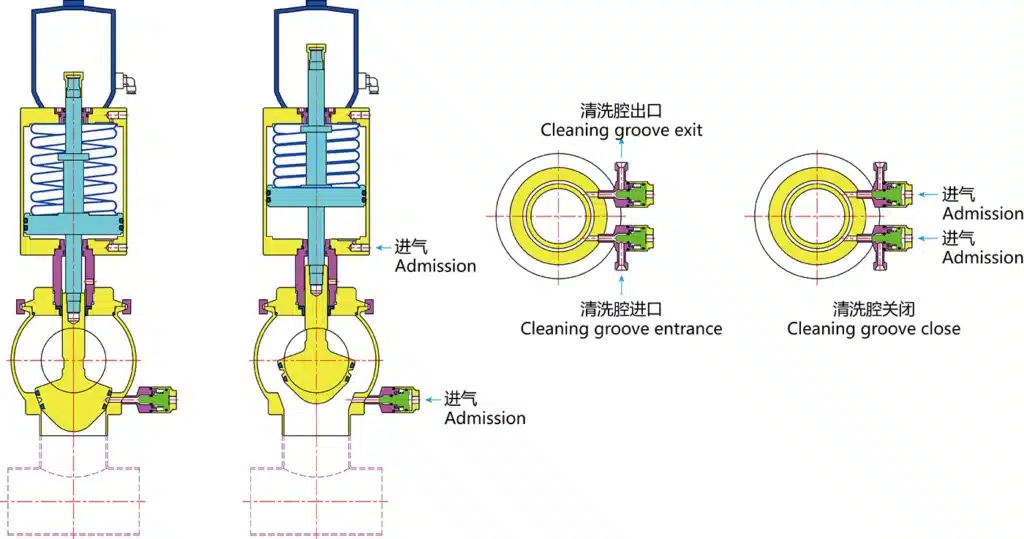
Types of Sanitary Control Valves
Sanitary control valves come in various types, each suited to specific applications and having its own advantages and limitations. Here are some of the most common types of sanitary control valves:
Sanitary Ball Valves
These types of valves use a ball with a hole through it which can be rotated to either block or allow flow. They are often used for on/off applications and can handle high pressure and temperatures. They offer good shut-off capabilities.
Sanitary Butterfly Valves
These are used for flow regulation, as well as for on/off applications. A disc is positioned in the center of the pipe; the disc has a rod passing through it which is connected to an actuator on the outside of the valve. Turning the actuator will rotate the disc either parallel or perpendicular to the flow. They are often chosen for their compactness and low cost.
Sanitary Diaphragm Valves
In these valves, a flexible diaphragm is moved up and down to control the flow of the fluid. When the diaphragm is lowered by the actuator, it blocks the flow. Diaphragm valves offer a high level of cleanliness as the diaphragm can fully seal off the flow, allowing no contaminants to pass.
Sanitary Check Valves
These are self-acting valves that allow media to flow in only one direction, preventing backflow. They are essential in systems where it is critical that substances do not flow back into the system.
Sanitary Plug Valves
A plug valve uses a cylindrical or conical plug with a hole in it to control flow. Rotating the plug allows the media to either pass through the hole or be blocked by the solid part of the plug. These valves are often used in applications where it’s necessary to fully open or close the valve quickly.
Sanitary Pressure Relief Valves
These are safety valves that protect systems from overpressure. When the pressure in the system reaches a preset level, the valve opens to relieve the pressure, preventing potential damage or failure.
Sanitary Control Valves
These valves automatically regulate flow rate, pressure, or temperature, typically in response to signals from a process control system. They can incorporate any of the valve types mentioned above but are fitted with an actuator that can be finely tuned to maintain specific process parameters.
Each of these types of sanitary control valves is designed to meet strict hygiene standards, being easy to clean and resistant to corrosion. The choice between them depends on the specific application, flow characteristics, pressure, and temperature conditions.
Pros and Cons of Various Sanitary Control Valve Designs
Here is a simple table outlining some of the main pros and cons of various sanitary control valve designs:
Valve Type | Pros | Cons |
---|---|---|
Sanitary Ball Valves | High shut-off capabilities, can handle high pressure and temperatures, durable | Not ideal for throttling, potential for cavitation and choked flow |
Sanitary Butterfly Valves | Compact, cost-effective, good for regulating and stopping flow | Not as effective at sealing as other valve types, disc obstructs flow path |
Sanitary Diaphragm Valves | High level of cleanliness, excellent sealing, can be used for throttling | Lower flow rates, not suitable for high-temperature applications |
Sanitary Check Valves | Self-acting, prevent backflow, simple design | Depend on flow velocity, potential for water hammer effect, may not seal properly at low flow rates |
Sanitary Plug Valves | Quick to open and close, good sealing, suitable for slurry applications | More difficult to clean, potential for leakage over time |
Sanitary Pressure Relief Valves | Provide safety by relieving overpressure, self-acting | Not for flow regulation, require regular maintenance and testing |
Sanitary Control Valves | Fine regulation of process parameters, can be automated, flexible design options | Complexity can lead to higher cost, require regular maintenance |
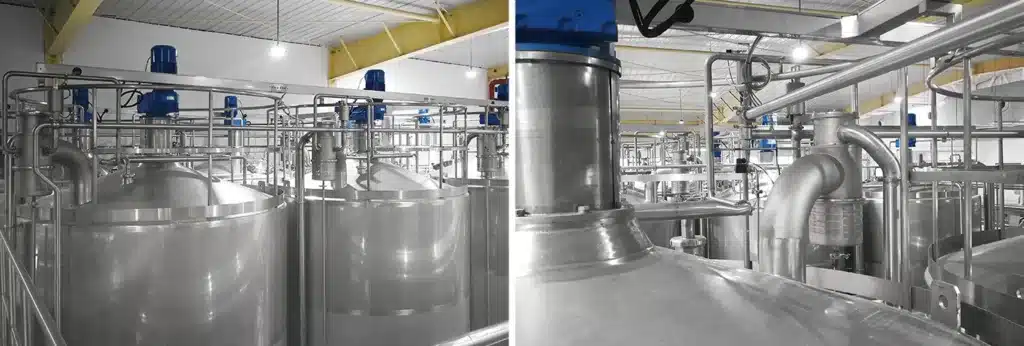
Selecting the Right Sanitary Control Valve for Your Needs
Choosing the right sanitary control valve for your needs depends on a variety of factors. Understanding these parameters can help ensure that your valve operates effectively and maintains the required level of sanitation. Here are some considerations to help guide your selection:
Type of the Media
The type of media that will be flowing through the valve, whether liquid, gas, or semi-solid, will greatly influence your choice of valve. Also consider the characteristics of the media, such as its viscosity, temperature, corrosiveness, and whether it contains particulate matter.
Flow Control Needs
If you need to be able to finely adjust the flow rate, you’ll want a valve designed for throttling, such as a butterfly or diaphragm valve. If you only need to fully open or close the flow, a ball or plug valve may be more suitable.
Pressure and Temperature
The operating pressure and temperature in the system are also important considerations. Some valves are better suited to high pressure or high temperature environments than others.
Hygiene Requirements
If you’re in an industry that requires very high hygiene standards, such as food and beverage, biotech, or pharmaceuticals, make sure the valve meets all relevant standards. Consider the ease of cleaning and whether the valve can withstand Clean-in-Place (CIP) or Steam-in-Place (SIP) procedures.
Actuation
Consider how you want the valve to be actuated. Manual valves are simple and cost-effective, but require personnel to physically adjust them. Automated valves can be controlled remotely and integrated into your process control system, providing greater precision and freeing up personnel for other tasks.
Installation and Maintenance
Check if the valve can be easily installed in your current system. Some designs are more compact, making them more suitable for systems where space is limited. Also, consider the ease of maintenance and the availability of spare parts.
Budget
Of course, cost is always a factor. Try to find a balance between upfront costs and ongoing maintenance costs. A more expensive valve might last longer and require less maintenance, ultimately saving money in the long run.
Supplier/Manufacturer Support
Finally, consider the level of support provided by the supplier or manufacturer. They should be able to provide technical information, help with installation and maintenance, and provide timely and effective customer service when needed.
Always consult with a valve specialist or engineer to ensure that the sanitary control valve you select is the best fit for your particular application. We can provide expert advice and guide you through the selection process.
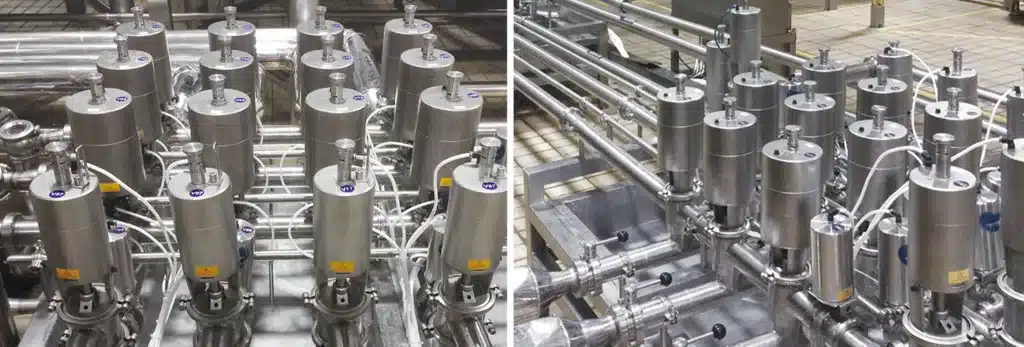