In the world of industrial operations, valves are critical to controlling the flow of fluids and gases, ensuring the safety, efficiency, and reliability of processes across a wide range of industries. However, in severe service environments—where valves are subjected to extreme pressures, high temperatures, abrasive materials, and corrosive chemicals—standard valve materials often don’t cut it. These harsh conditions can lead to rapid wear, frequent maintenance, and even danger failures if not properly prevent these problems.
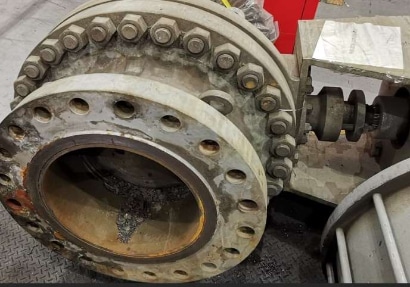
One of the most effective ways to improve the durability and performance of valves in these challenging conditions is through the application of hard coatings. These coatings provide an additional layer of protection, significantly extending the life of the valve and reducing the frequency of maintenance. Hard coating on valve are particularly critical in industries such as oil and gas, chemical processing, power generation, and mining where severe service is the norm rather than the exception.
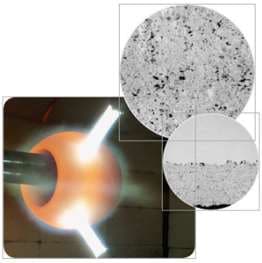
I learned a lot about hard coating in the valve world technical seminar with Flowserve. In this article, I will discuss with you the importance of hard coating for severe service valves, why valves need metal sealing, the common challenges we face in severe service applications, and the solutions provided by professional manufacturers. We will also look at the various coating technologies available in the valve industry and discuss the processes and technologies that ensure the highest performance and reliability.
Why Severe Service Valves Require Metal Sealing
Challenges in Severe Service
Severe service conditions present a unique set of challenges that require specialized solutions. Valves operating in these environments are exposed to a variety of extreme conditions including high-velocity fluids, abrasive slurries, corrosive chemicals, and extreme temperatures and pressures etc,.
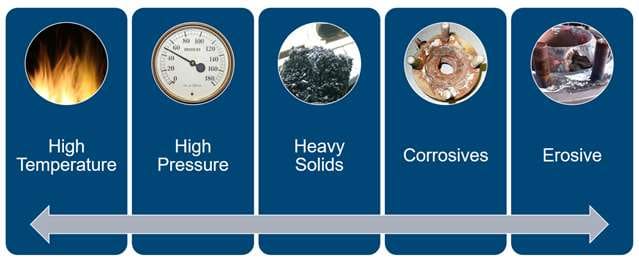
High-Velocity fluids
In many industrial applications, fluids move at high velocities, which can cause significant wear on valve components, especially in areas where turbulence is present. This is especially problematic in applications involving slurries or other abrasive materials.
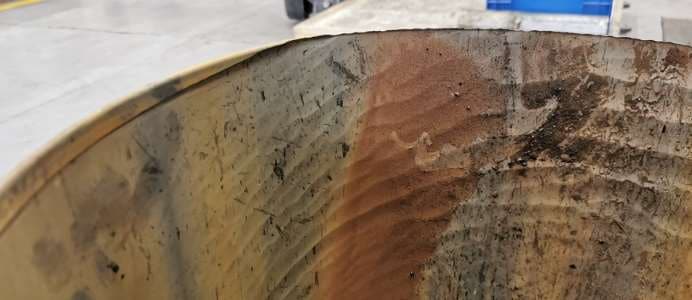
Abrasive Slurries
In industries such as mining and mineral processing, valves are often required to handle abrasive slurries that can quickly wear down unprotected surfaces. The constant impact of hard particles against valve components can lead to rapid degradation and failure.
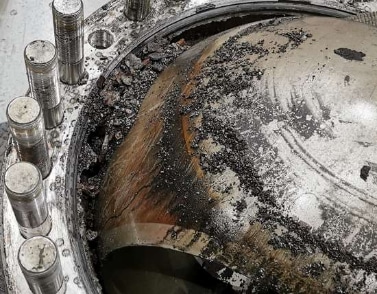
Corrosive Chemicals
Chemical processing and petrochemical industries frequently involve the handling of highly corrosive substances. These chemicals can cause severe corrosion on valve surfaces, leading to leaks and failures if not properly protected.
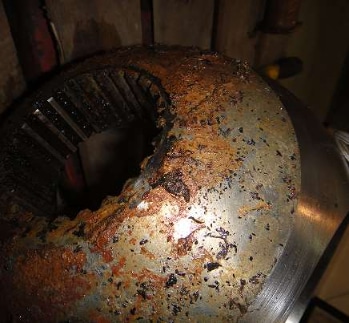
Extreme Temperatures and Pressures
In power generation, oil and gas, and other heavy industries, we often run valves under extreme pressures and temperatures. If we don’t design them to handle these stresses, the materials can weaken, deform, or fail.
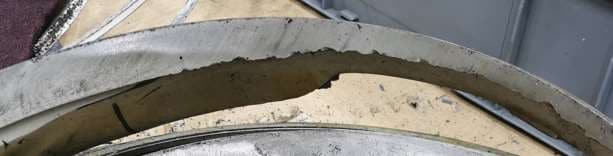
These challenges highlight the need for reliable valve designs that can withstand the harshest conditions without sacrificing performance. This is where metal sealing comes into play.
Flexibility in Severe Service Valve Design
Metal sealing is a critical element in the design of many different types of valves, especially those used in severe service applications. The strength and durability of metal seals make them ideal for valves that must operate in extreme conditions such as high pressures, high temperatures, and exposure to corrosive or abrasive materials. Let’s look at how metal sealing benefits different valve designs, including ball valves, gate valves, and globe valves, and how it makes them more versatile in different operating conditions.
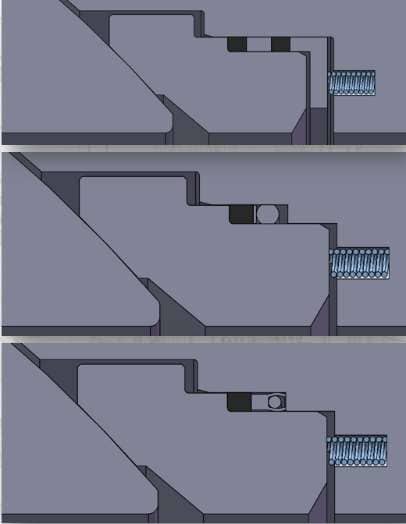
Severe Service Ball Valves
Ball valves are used extensively in industrial applications because they provide tight sealing and low-torque operation. A ball valve controls the flow of fluid or gas through a spherical disc (the “ball”) with a hole through the center. When the ball is rotated, the hole aligns with the flow path, allowing fluid to pass through. Rotate the ball 90 degrees, and the valve closes, stopping the flow.
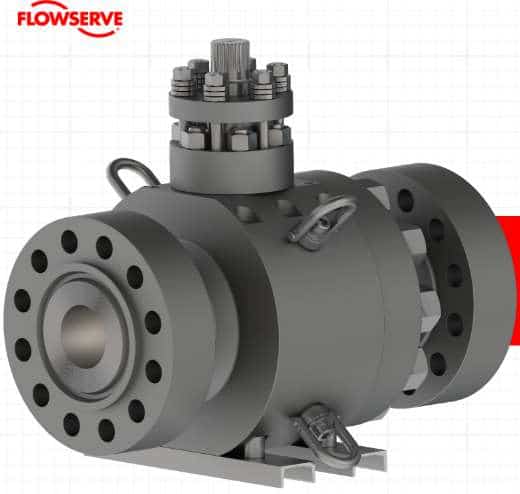
Benefits of Metal Sealing
Increased Durability: In ball valves, metal seals are much more resistant to the wear and tear caused by the constant rotation of the ball against the seal. This is especially important in applications where the valve is cycled open and closed frequently.
High Pressure and Temperature Resistance: Metal seals can handle the high pressures and temperatures often found in industries such as oil and gas, chemical processing, and power generation. This makes ball valves with metal seals perfect for applications where soft seals would break down quickly under these conditions.
Better Corrosion Resistance: In corrosive environments, metal-sealed ball valves are more resistant to chemical attack than their soft-seal counterparts. This means they last longer and require less maintenance.
Application
Tight Shutoff: Metal-sealed ball valves provide a reliable tight shutoff, which is critical in applications where you can’t have any leakage, such as in high-pressure gas lines or critical chemical processes.
Fire-Safe Applications: In environments where fire safety is a concern, metal seals are preferred because they can maintain their sealing integrity even if there is a fire, unlike soft seals that may melt or burn.
High-Cycle Operations: Metal-sealed ball valves are perfect for high-cycle operations where you operate the valve frequently. The durability of metal seals means you can operate the valve many times without significant wear on the seal.
Severe Service Gate Valves
Gate valves are used to start or stop the flow of fluid in a pipeline. They work by lifting a gate (or wedge) out of the path of the fluid. Gate valves are typically used in applications where the valve is either fully open or fully closed, as they are not designed for throttling.
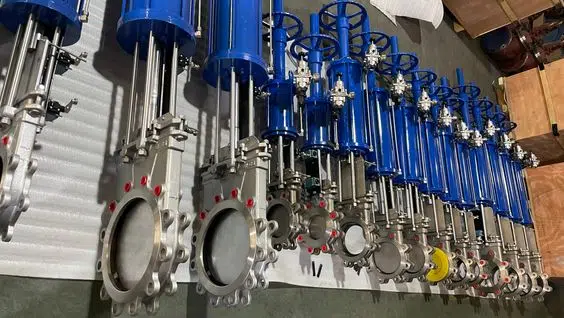
Benefits of Metal Sealing
Long Life in Abrasive Conditions: In gate valves, metal seals are critical to maintaining a tight seal even in abrasive conditions where the valve may come into contact with fluids that have particles in them. The metal seal’s resistance to abrasion ensures the valve will continue to work over time.
High-Pressure Capability: Gate valves are often used in high-pressure applications such as water distribution systems and oil pipelines. Metal seals can handle these pressures without deforming or losing their ability to seal, so the valve works.
Thermal Stability: In applications where temperatures fluctuate, metal-sealed gate valves offer better thermal stability, so the seal remains effective even as the valve expands and contracts.
Application
Critical Shutoff Applications: Metal-sealed gate valves are perfect for applications where you need a good shutoff, such as in isolation services in the oil and gas industry. The robust metal seal ensures the valve can block the flow effectively, even under high pressure.
Erosive Fluid Handling: When you’re dealing with erosive fluids, such as slurries or fluids that contain sand or other particulates, metal-sealed gate valves provide better protection against erosion, so the sealing surfaces remain intact.
High Temperature Services: Gate valves with metal seals are great for high-temperature services, such as in steam systems or industrial furnaces, where soft seals would fail due to thermal degradation.
Severe Service Globe Valves
Globe valves are used primarily to regulate flow in a pipeline. They consist of a movable disk-type element and a stationary ring seat in a generally spherical body. The design of globe valves makes them especially effective for throttling, allowing you to control fluid flow precisely.
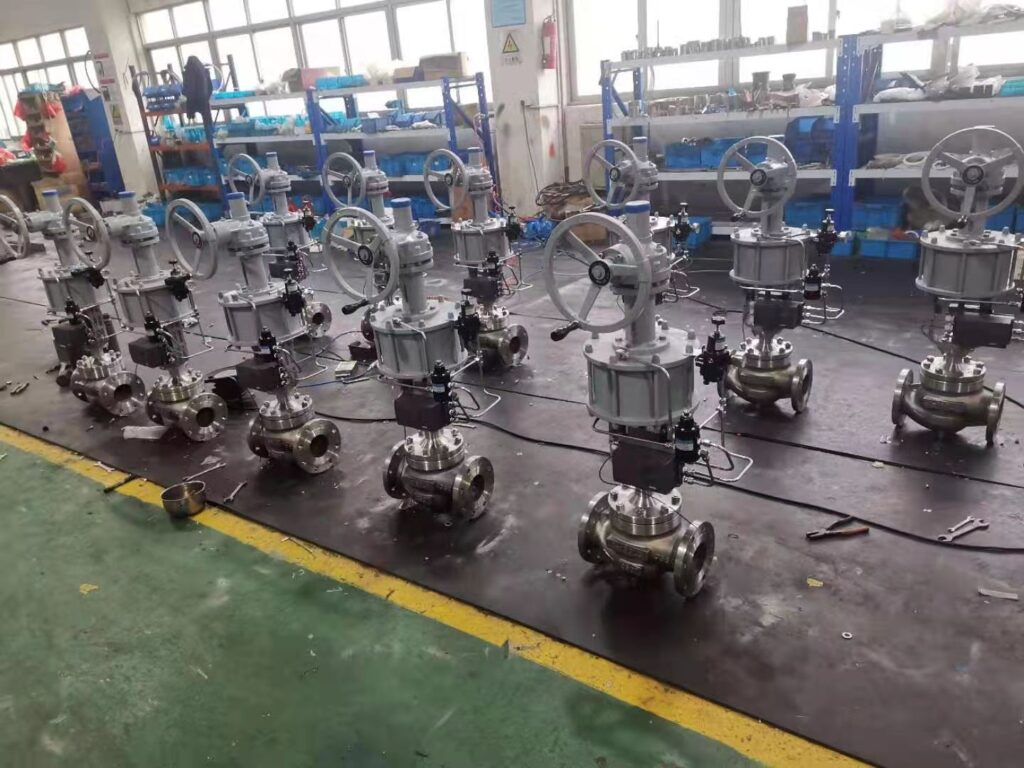
Benefits of Metal Sealing
Throttling Capability: Metal seals in globe valves perform very well in throttling applications, where you open the valve partially to control flow. The durability of metal seals ensures the valve can handle the forces exerted by the fluid as it passes through the partially open valve.
Leakage Prevention: In applications where you can’t have any leakage, such as in toxic or hazardous fluid handling, metal-sealed globe valves provide a high level of confidence that you will maintain a tight seal.
Resistance to Cavitation: In high-pressure drop applications where cavitation can occur, metal seals are less likely to be damaged by the implosive forces of cavitation bubbles compared to soft seals, making them ideal for these challenging environments.
Application
Flow Control: Metal-sealed globe valves are great for flow control in systems where you need to control the flow rate precisely, such as in steam systems or molten salt condition.
Corrosive Media Handling: In environments where the fluid is corrosive, metal seals give you the resistance to chemical attack you need to ensure the valve will work for a long time.
High Differential Pressure: Globe valves with metal seals can handle high differential pressure without compromising the integrity of the seal, so they work well for critical control applications in power plants and refineries.
Common Problems in Severe Service
Valves in severe service applications face a variety of challenges that can impact their performance and life. Understanding these problems is key to developing effective solutions.
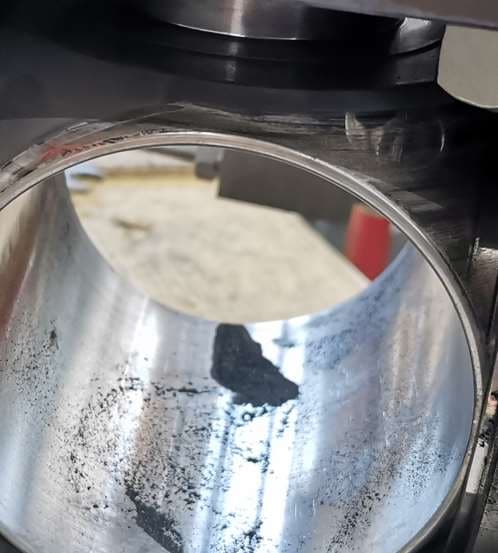
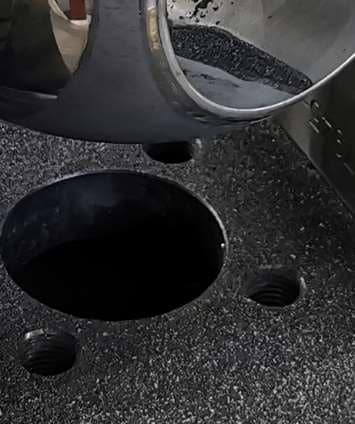
1. Wear Resistance
Wear is one of the most common problems valves face in severe service environments. It occurs when valve components come into contact with abrasive materials, causing material to be removed from the surface. Over time, this can cause significant damage to the valve, impacting its performance and eventually causing it to fail.
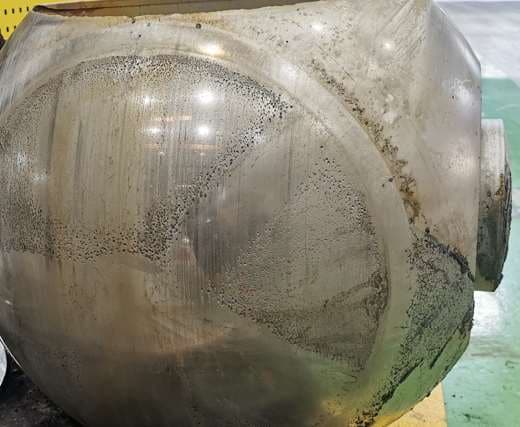
Types of Wear
There are several types of wear that can affect valves, including abrasive wear, adhesive wear, and corrosive wear. Abrasive wear occurs when hard particles in the fluid or gas stream scrape against valve surfaces, causing material to be worn away. Adhesive wear, on the other hand, occurs when two surfaces in contact bond together and then pull apart, removing material in the process. Corrosive wear is caused by chemical reactions between the valve material and the fluid or gas, which gradually deteriorate the surface.
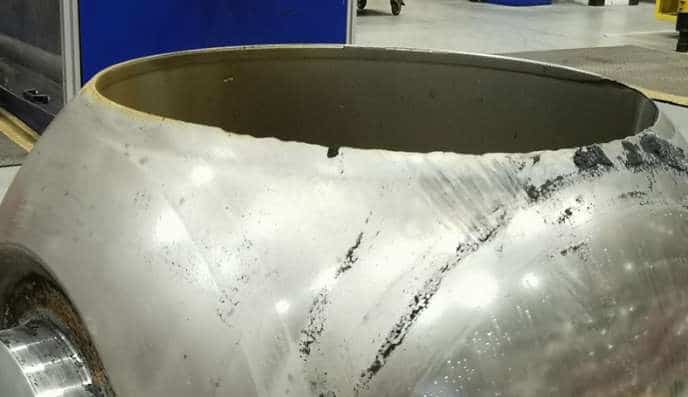
Impact on Valve Performance
Wear can cause a variety of problems, including leakage, reduced flow capacity, and even complete valve failure. In severe cases, worn valve components may no longer be able to seal, allowing fluids or gases to escape and potentially creating safety hazards.
Hard coatings are a great solution to combat wear. They provide a tough layer that resists the effects of abrasion, adhesion, and corrosion.
2. Abrasion, Erosion, and Corrosion
Abrasion, erosion, and corrosion are closely related problems that can have a significant impact on valve performance in severe service environments.
Abrasion
Abrasion occurs when hard particles in the fluid or gas stream rub against valve surfaces, wearing away the material. This is particularly problematic in applications involving slurries or other abrasive materials, such as in mining or wastewater treatment.
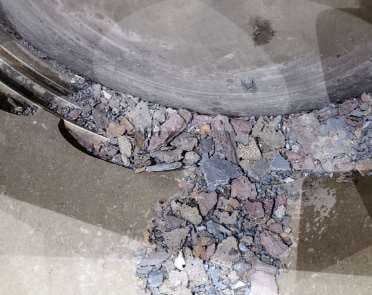
Erosion
Erosion is caused by the impingement of fluid or gas streams against valve surfaces, leading to the removal of material. Erosion is often exacerbated by the presence of solid particles in the fluid, which can cause localized damage to the valve.
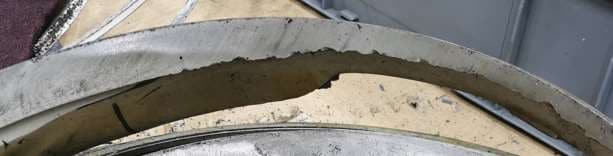
Corrosion
Corrosion occurs when chemical reactions between the valve material and the fluid or gas lead to the degradation of the material. This can be particularly problematic in applications involving corrosive chemicals, such as in the chemical processing or petrochemical industries.
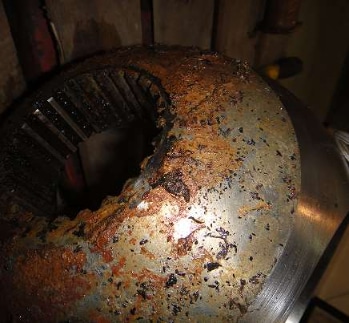
Each of these issues can compromise the integrity of the valve, leading to leaks, reduced performance, and eventual failure. Hard coatings provide a protective barrier that resists the effects of abrasion, erosion, and corrosion, extending the life of the valve and maintaining its performance over time.
3. Extremely High Pressure and Temperature
Valves in severe service applications often operate under extremely high pressures and temperatures, which can put a lot of stress on valve components.
High Pressure: High pressures can cause valve components to bend or distort, which leads to leaks and poor performance. In some cases, the pressure can be so high that it causes the valve body or seat to crack or break.
High Temperature: High temperatures can cause materials to weaken or become brittle, which leads to cracking or distortion. This is especially problematic in applications where valves are exposed to cyclic thermal loads, which cause materials to expand and contract repeatedly.
Hard coatings are designed to withstand these extreme conditions, providing a tough barrier that doesn’t break down even in the worst conditions.
4. Maintaining Tightness After Long-Term Use
One of the big challenges in severe service applications is keeping things sealed up tight over long periods of time, especially in applications where you have a lot of cycling or extreme temperatures.
Seal Degradation: Over time, seals can degrade due to wear, corrosion, or changes in material properties. This can lead to leaks, which can compromise the performance of the valve and potentially cause safety hazards.
Thermal Cycling: In applications where valves are exposed to repeated thermal cycling, the expansion and contraction of materials can cause seals to loosen up or degrade, which leads to leaks.
Hard coatings help maintain tight seals by providing a tough surface that resists wear and corrosion, which means they keep working for a long time even in tough conditions.
5. Durability After Millions of Operations
In many severe service applications, valves are expected to cycle millions of times over the life of the valve. This puts a lot of stress on valve components, which have to be able to cycle over and over without breaking down.
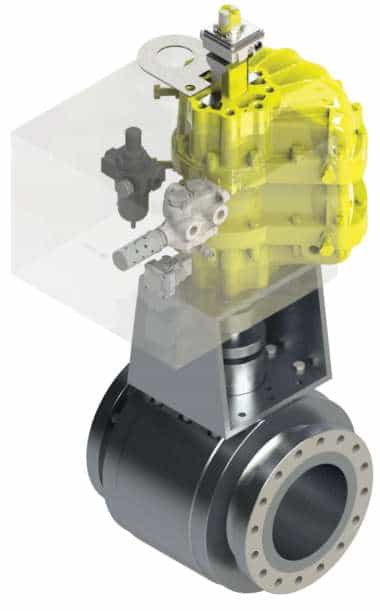
Mechanical Stress: Repeated cycling puts mechanical stress on valve components, which leads to fatigue and eventually failure. This is especially problematic in applications where you have high pressures or high temperatures, which put even more stress on valve components.
Fatigue Resistance: Hard coatings provide a layer of protection that improves the fatigue resistance of valve components, so they can cycle millions of times without breaking down.
6. Powder Accumulation
In some processes, especially those involving fine powders, material can build up on valve surfaces.
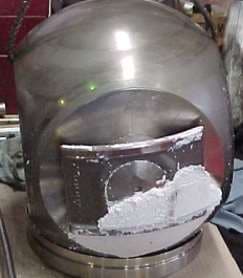
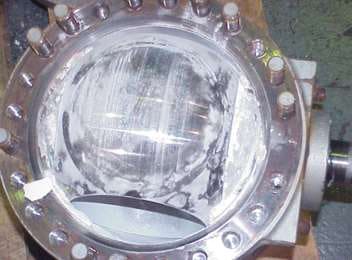
Blockages: When material builds up, it can block the valve, reducing flow capacity and potentially causing the valve to stick or fail.
Poor Performance: Even if you don’t get blockages, having material on valve surfaces can cause the valve to perform poorly by interfering with the smooth operation of the valve components.
Hard coatings help reduce powder accumulation by providing a smooth, non-stick surface that resists the buildup of material.
Hard Coating Solutions from Professional Manufacturers
To address the challenges of severe service applications, you need specialized solutions from people who know what they’re doing. This includes advanced coating technologies, expert product design, and precision manufacturing processes.
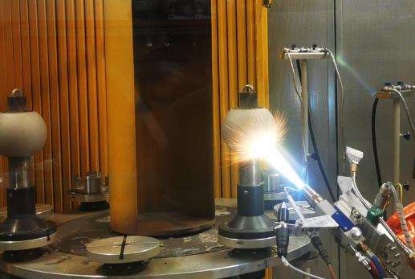
1. Coating Selection and Fabrication
The choice of the right coating material and the fabrication process are two critical factors in making sure valves hold up and perform in severe service environments.
Material Selection: Choosing the right coating material is critical to achieving the desired level of wear, corrosion, and temperature resistance. Common materials used for hard coatings include tungsten carbide, chromium carbide, and nickel-based alloys. Each of these materials has different properties that make them suitable for specific applications.
Fabrication Process: The fabrication process consists of several steps, including surface preparation, coating application, and heat treatment. Surface preparation is critical to ensure that the coating adheres properly to the base material, while the coating application process must be carefully controlled to achieve the desired thickness and uniformity. Heat treatment is often used to improve the bond between the coating and the base material, which increases the overall durability of the valve.
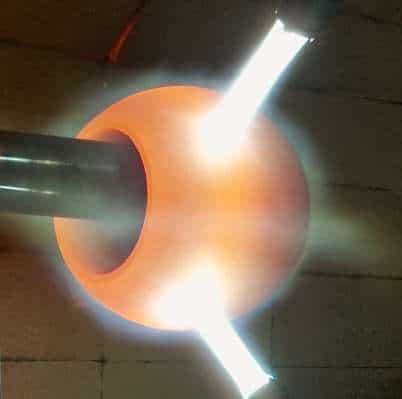
2. Experienced Product Design
Designing valves for severe service applications requires a deep understanding of the specific challenges posed by these environments. Experienced engineers use advanced tools and techniques to create valve designs that can handle the rigors of severe service.
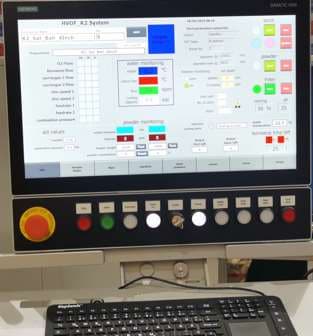
Design Simulations
Finite element analysis (FEA) and computational fluid dynamics (CFD) are commonly used to simulate the behavior of valves under different operating conditions. These simulations allow engineers to see where the design might be weak and make changes to improve performance.
Material Selection
In addition to selecting the right coating material, you also need to choose the right base materials for the valve components. Materials such as stainless steel, Inconel, and Hastelloy are commonly used because they resist corrosion and high temperatures well.
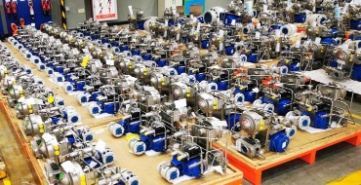
Custom Designs
In some cases, standard valve designs may not be enough to meet the demands of a particular application. In these situations, you may need to have a valve custom designed to give you the performance and reliability you need.
3. Specialized Equipment
Applying hard coatings and manufacturing valves for severe service require specialized equipment that can deliver precise and consistent results.
Thermal Spray Equipment
Thermal spray equipment, such as high-velocity oxygen fuel (HVOF) and plasma spray systems, is used to apply hard coatings to valve components. These systems have to be set up correctly to make sure the coating goes on evenly and at the right thickness.
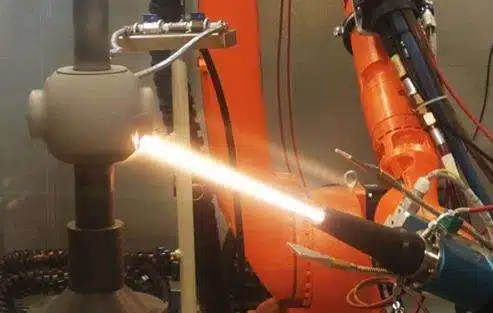
Spray & Fuse Machine
In the case of Spray & Fuse coatings, fusion machines are used to heat the coating material to its melting point so it fuses with the base material. This creates a strong, metallurgical bond that makes the coating last longer.
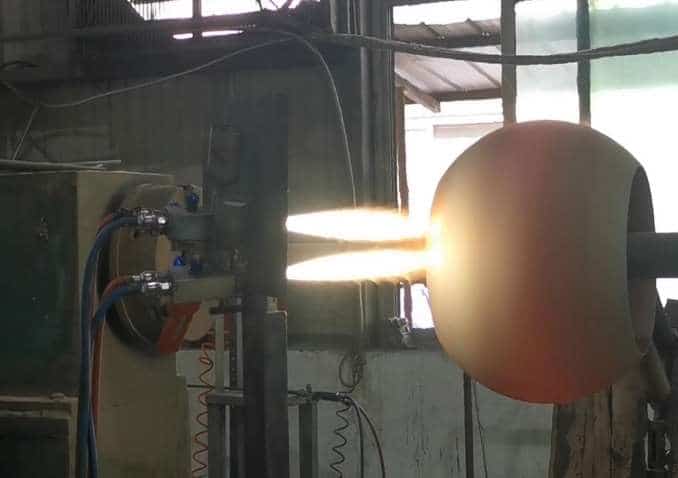
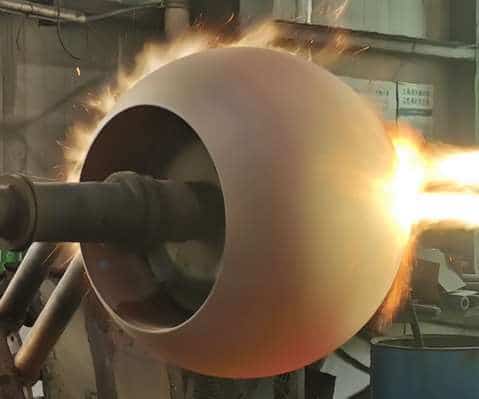
Lapping Equipment
Lapping is a critical finishing process that makes sure the sealing surfaces of the valve are perfectly round and have an even thickness. You use precision lapping equipment to get the right surface finish and tight tolerances you need for the valve to seal properly.
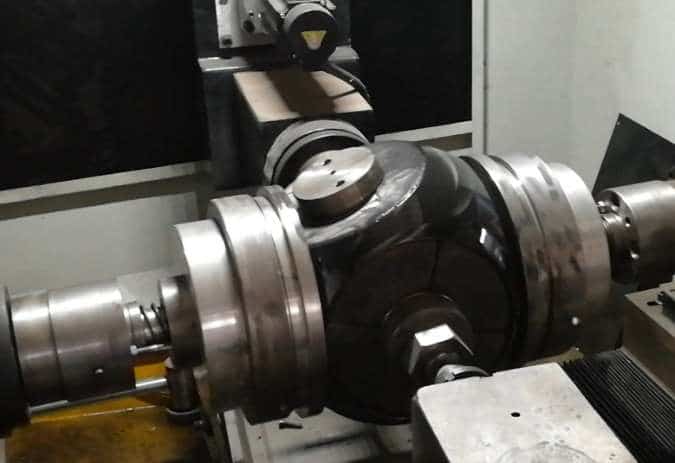
Coating Technologies in the Valve Industry
The success of hard coatings in severe service valves depends on selecting the right coating technology and applying it correctly. There are several coating technologies commonly used in the valve industry, each with its own advantages.
I. Pre-Processing
The foundation of any high-quality coating lies in the preparation of the base material. Proper pre-processing ensures that the coating adheres well and performs effectively.
Surface Preparation
Surface preparation is critical to getting a good bond between the coating and the base material. Common surface preparation techniques include sandblasting, chemical cleaning, and mechanical polishing. Sandblasting removes contaminants and creates a rough surface that helps the coating stick, while chemical cleaning removes oils, greases, and other residues that could interfere with the coating process.
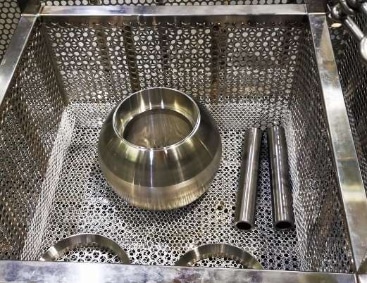
Surface Roughness
The surface roughness of the base material is an important factor in how well the coating sticks and performs. A rougher surface gives the coating more places to “anchor” to, which can make it last longer. However, you have to be careful not to make the surface too rough because you can create stress concentrations that can cause the coating to fail.
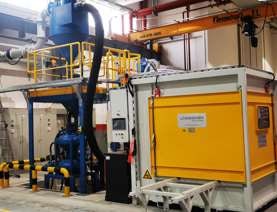

Cleanliness
Making sure the surface is clean and free of contaminants is critical to getting a good bond between the coating and the base material. If there is oil, grease, or dust on the surface, it can create weak spots in the coating that will cause it to fail early.
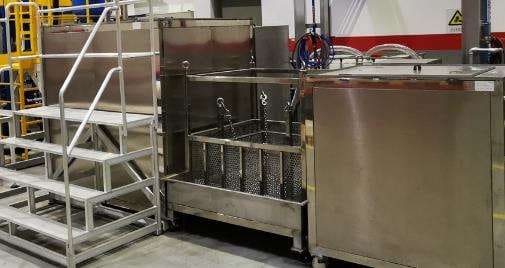
II. Coating Process
The actual application of the coating is the core of its quality. Several different coating technologies are commonly used in the valve industry, each with its own advantages and disadvantages.
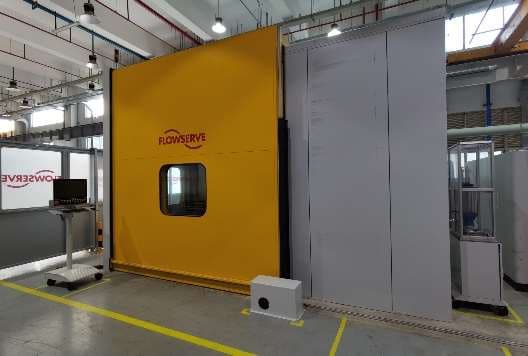
High-Velocity Oxygen Fuel (HVOF) Coating
HVOF is a thermal spray process that produces coatings that are extremely hard and dense. In this process, a mixture of fuel gas and oxygen is ignited to create a high-velocity flame. The coating material, in the form of a powder, is fed into the flame where it melts and is accelerated onto the surface of the valve component. The high velocity of the particles results in a dense, tightly bonded coating with excellent wear and corrosion resistance.
HVOF Coating | Spray &Fuse Coating | |
Advantages | ·Applicable on any metallic base material | ·Closed porosity and metallurgical bond ·High impact resistant |
·Highest hardness and wear resistance | ·Corrosion resistance against variety of liquids and gaseous medias especially against bases and oxidizing acids,even at highertemperatures | |
Applications | ·Severe service | ·Severe service(Abrasion,Erosion,Corrosion) |
·General service,moderate operating cycles | ·High pressure Oxygen,Hydrogen and Critical Gases ·Demandinglowleakage classes | |
·High pressure,High temperature | ·Thermal cycling/shock ·High and ultimate operating cycles |
Plasma Spray Coating
Plasma spray is another thermal spray process that uses a high-temperature plasma to melt the coating material and propel it onto the surface of the valve component. Plasma spray coatings have excellent adhesion and can be used to apply a wide range of materials, including ceramics and metals. This makes plasma spray a versatile option for a wide range of severe service applications.
Spray & Fuse Coating
Spray & Fuse is a two-step process that involves spraying a coating material onto the surface of the valve component and then heating it to fuse it with the base material. This process creates a metallurgical bond between the coating and the base material, resulting in a very durable and wear-resistant surface. Spray & Fuse coatings are particularly effective in applications where you need high impact resistance and corrosion resistance.
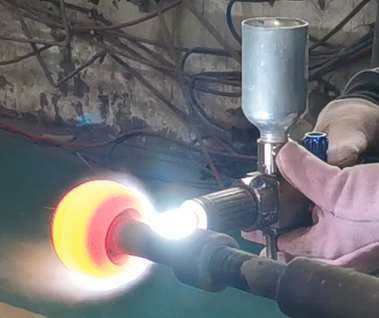
III. Heat Treatment
Heat treatment is a critical step in the coating process that ensures the coating bonds well with the base material. This step is essential for creating a surface that will last a long time.
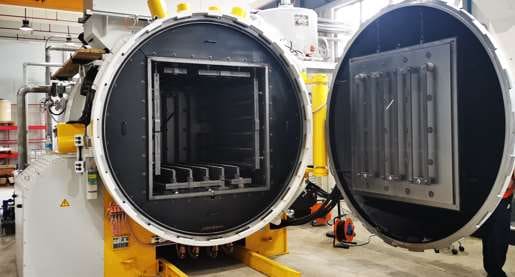
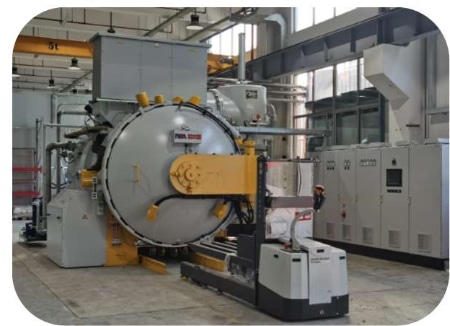
Annealing
Annealing is a heat treatment process that involves heating the coated valve component to a specific temperature and then allowing it to cool slowly. This process relieves internal stresses in the coating and the base material, which makes the coating tougher and more durable.
Tempering
Tempering is a heat treatment process that involves heating the coated valve component to a temperature below its critical point and then cooling it in air. This process makes the coating tougher and reduces the risk of cracking or chipping during operation.
Quenching
Quenching is a heat treatment process that involves heating the coated valve component to a high temperature and then rapidly cooling it in water or oil. This process makes the coating and the base material harder, which makes them more resistant to wear and impact.
IV. Lapping
Lapping is a finishing process that ensures the valve’s sealing surfaces are perfectly round and have an even thickness. This is important because it helps the valve make a tight seal and prevents leaks.
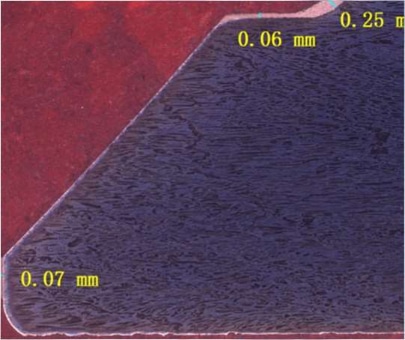
Abrasive Materials
Lapping uses abrasive materials like diamond or silicon carbide to remove a small amount of material from the surface of the valve component. The abrasive material is applied using a lapping machine that rotates the valve component against a lapping plate.
Precision
Lapping is a very precise process that requires careful control of the pressure, speed, and duration of the lapping operation. The goal is to achieve a surface finish that is smooth and uniform, with a high degree of roundness and thickness evenness.
Sealing Performance
The quality of the lapping process has a direct impact on the sealing performance of the valve. A well-lapped surface ensures that the valve seats properly, which creates a tight seal that prevents leaks. This is especially important in severe service applications where even small leaks can cause big problems.
Testing & Verification
Testing and verification are critical steps in the production of severe service valves to make sure the hard coatings we apply meet the stringent demands of the application. These processes help us confirm that the coatings will perform as expected under extreme conditions, giving you the durability, wear resistance, and corrosion protection you need.
Standard Testing Methods
Hardness Testing
Hardness is a key indicator of a coating’s ability to resist wear and abrasion. Hardness testing usually involves using an indenter to press into the coating material and measure its resistance to deformation. Common methods include Rockwell, Vickers, and Knoop hardness tests. The results give you a number that tells you how well the coating can handle mechanical stress.

Porosity Testing
Porosity in a coating can create weak spots where corrosion and wear can start, which will ruin the coating’s effectiveness. Porosity testing involves looking at the coating under a microscope or using techniques like gas permeability testing to find and measure the size and distribution of pores in the coating. The lower the porosity, the better the coating will protect.
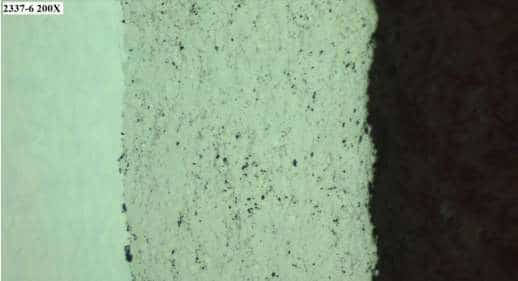
Bond Strength Testing
The strength of the bond between the coating and the base material is critical to how long the coating will last. Bond strength testing measures the force it takes to pull the coating off the substrate. You usually do this with tensile or shear testing. The higher the bond strength, the better the coating will stay on the valve, even under severe service conditions.
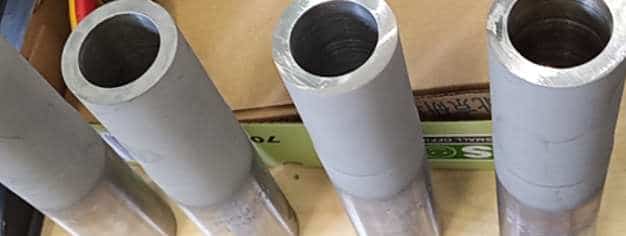
Bend Testing
Bend testing evaluates the coating’s flexibility and ability to withstand deformation without cracking or delaminating. In this test, the coated valve component is bent to a specific angle, and the coating is inspected for signs of cracking or peeling. This test is particularly important for coatings applied to components that may experience mechanical stress or deformation during operation.
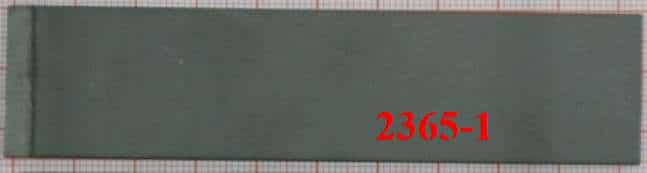
Destructive Testing Methods
While standard testing methods give you a good idea of how good the coating is, destructive testing lets you dig deeper by looking at the actual material properties of the coating and the substrate. These tests involve cutting out sections of the coated valve and doing different analyses to see what’s going on with the coating.
Thickness Measurement
Coating thickness is a critical parameter that affects how well the valve will work and how long it will last. Destructive testing lets you measure the coating thickness very accurately using techniques like cross-sectional analysis under a microscope. It’s important to have the same thickness all over the valve to get the same protection and performance.
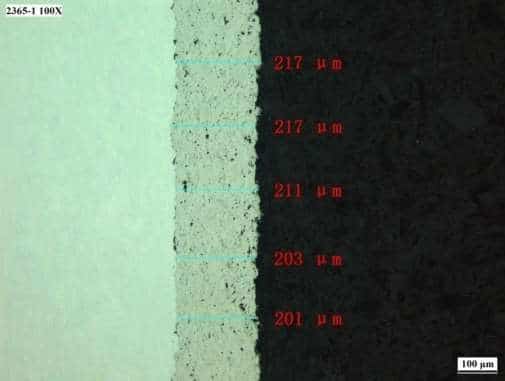
Hardness Evaluation
In addition to the standard hardness tests, destructive methods can include microhardness testing, which measures the hardness of the coating at a microscopic level. This can give you information about how the hardness is distributed in the coating and if there are any variations that could affect how it works.
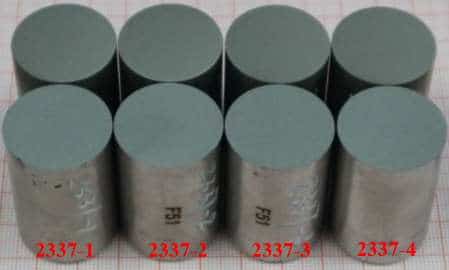
Porosity Analysis
Destructive porosity analysis involves cutting the coated valve part in half and looking at the cross-section under a microscope to find and measure the pores. This gives you a better idea of how the porosity is distributed in the coating, so you can make specific improvements to your coating process if you need to.
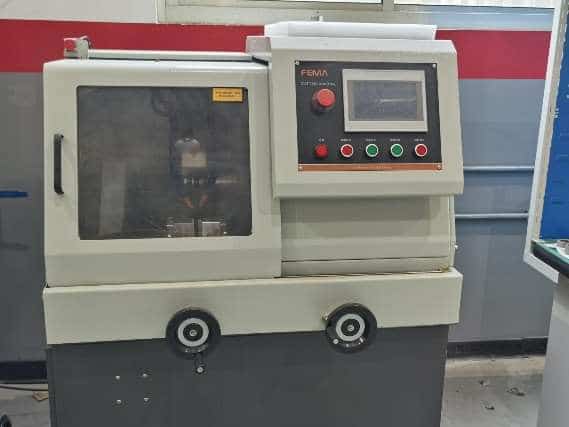
Metallographic Examination
Metallographic analysis involves cutting the coated valve part in half, preparing a cross-section, and looking at it under a microscope to see the microstructure of the coating and the substrate. This analysis can tell you about the quality of the coating’s adhesion, if there are any defects or inclusions, and how well the coating is bonded to the substrate.
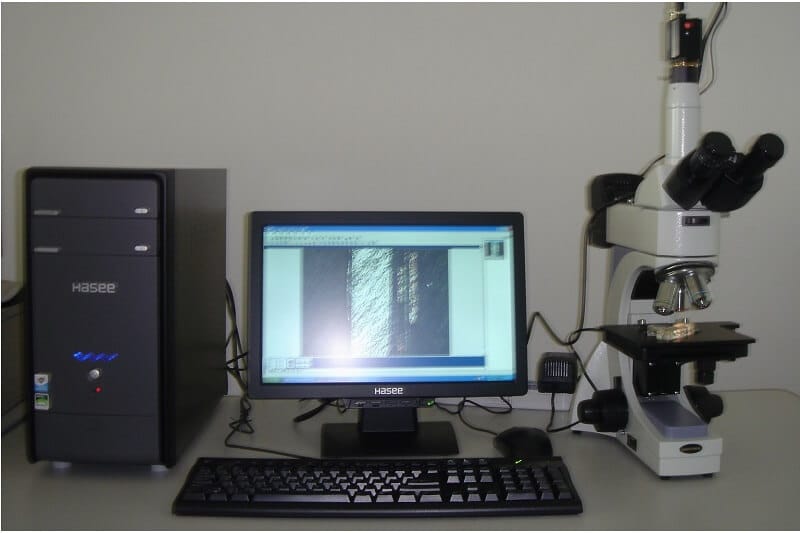
These testing and verification methods are critical to making sure the hard coatings you put on your severe service valves are the best they can be. By testing and verifying every aspect of the coating, you can be confident that you’re delivering valves that will work in the toughest conditions.
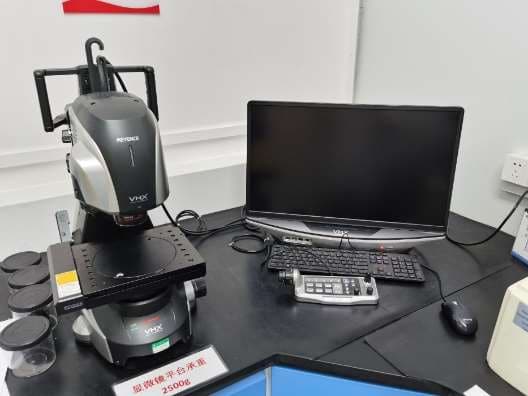
Conclusion
Metal seat valves with high-quality hard coatings are critical to severe service across many industries. These valves are designed to work in extreme conditions, including high pressures, high temperatures, and exposure to abrasive and corrosive media. The key to the success of these valves is the application of advanced coating technologies that protect the valve and allow it to work reliably for a long time.
In this article, we’ve talked about the problems valves have in severe service, including wear, abrasion, erosion, corrosion, and the need to maintain tight seals over long periods of time. We’ve also talked about the solutions that professional manufacturers provide, including using the right coating materials, advanced fabrication processes, and testing and verifying the coatings.
Future Trends
In the future, we can expect to see more advances in coating technologies in the valve industry, including the development of nano-coatings, advanced ceramic materials, and other new solutions. These new technologies will help improve the performance and durability of severe service valves, so they can handle the increasing demands of today’s industrial applications.
Final thoughts
For valve engineers, engineering companies, and instrument engineers, it’s important to understand the importance of hard coatings and work with manufacturers who know what they’re doing to get the best performance in severe service. By understanding the latest advances in coating technology and choosing the right solution for their needs, professional manufacturers can help severe service valves operate better in special conditions, ensuring long-lasting and stable working capabilities. If you have more questions about hard coating, please feel free to contact us. THINTANK’s valve experts are always available to provide you with free consultation services.
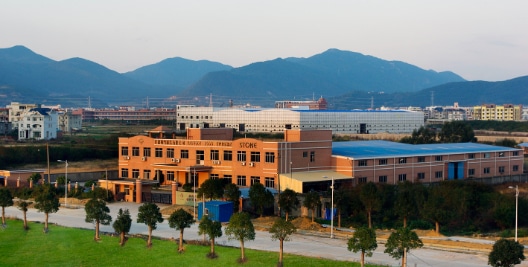