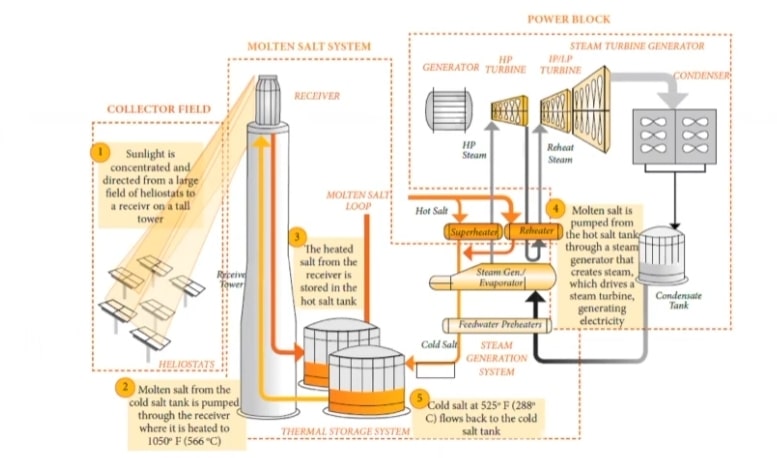
In recent years, as the environmental impact of traditional energy sources such as coal and petrochemicals has become more and more of a concern, there has been a growing search for cleaner and more environmentally friendly energy alternatives. Concentrated Solar Power(CSP) has been widely promoted and applied because of its clean and sustainable characteristics. In Concentrated Solar Power, molten salt control valves are crucial devices, and the selection and application of molten salt control valves are very important for the efficient operation of the entire system.
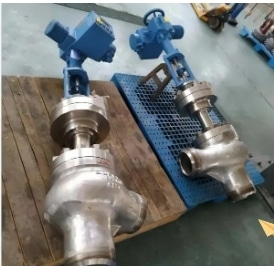
Working Principle and Application of Molten Salt Control Valves
Concentrated solar power uses the heat generated by solar energy to heat the heat transfer material, which then drives the steam turbine to generate electricity. Among the various technologies, tower molten salt power generation is the most mature. The heat transfer material is usually a binary or ternary nitrate molten salt. The tower height can reach over 200 meters, combining high temperature, large differential pressure, crystallization tendency, and strong corrosiveness, which put forward higher requirements for the performance of control valves.
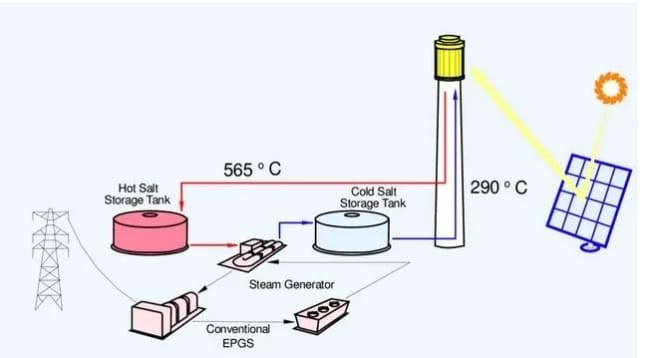
Application Challenges of Molten Salt Control Valves
High Temperature and Large Differential Pressure
The operating temperature range of molten salt is 290-565°C, with wide temperature fluctuations. Pressure differences can be significant, such as in the case of large pressure difference control valves in the lower part of the tower, where the inlet pressure exceeds 5MPa and the outlet pressure is 0.2MPa.
Crystallization and Strong Corrosiveness
Molten salt itself is highly corrosive and prone to crystallization.
Multiple Working Conditions
The valves must meet the requirements of multiple working conditions and have high adjustment performance.
Solutions for Molten Salt Control Valves
Material Selection
Low-Temperature Molten Salt Control Valves (generally 375°C and below)
The valve body and bonnet materials can be WCB, WCC, or A105, the valve plug/trim and seat are made of austenitic stainless steel with Stellite hardfacing, the valve stem is made of high-temperature austenitic stainless steel, and the bolts and nuts are made of high-temperature chromium-molybdenum steel. This material combination is cost-effective and performs well in application.
High-Temperature Molten Salt Control Valves (around 565°C)
The valve body and bonnet materials can be CF8C, the valve plug and seat are made of high-temperature stainless steel with Stellite hardfacing, the valve stem is made of high-temperature high-strength stainless steel, and the bolts and nuts are made of high-temperature stainless steel. This material combination has excellent high-temperature oxidation resistance, corrosion resistance, erosion resistance, and fatigue resistance.
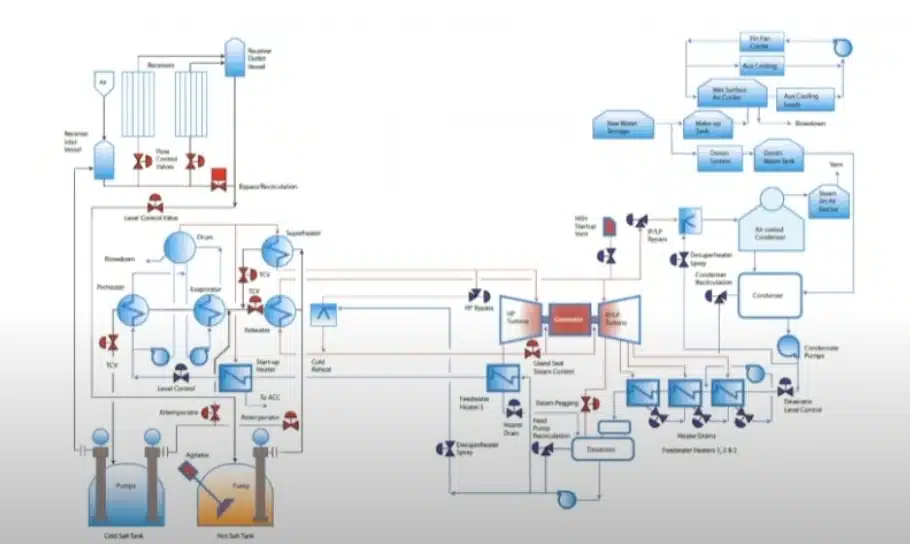
Valve Trim Design
The valve trim design depends on the actual working differential pressure.
- For smaller diameters and differential pressure less than 1MPa, parabolic single-seated valves can be used.
- For larger differential pressure, multi-stage pressure reducing single-seated valves are recommended.
- For larger diameters, cage type control valves are generally used;
- For higher differential pressure, multi-stage or labyrinth control valves are suggested.
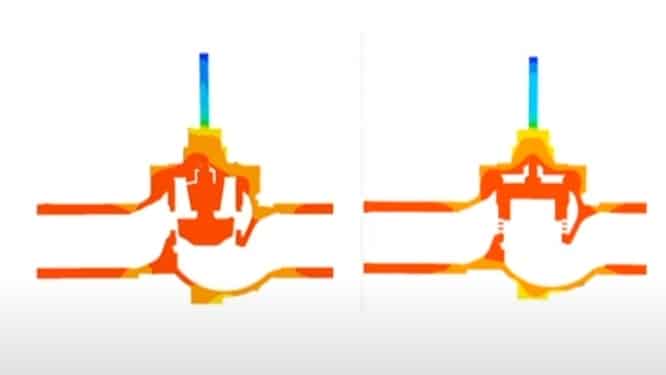
Special Design
Gasket Design
It is generally recommended to use high-temperature austenitic stainless steel metal serrated gaskets, metal octagonal gaskets, metal C-rings, or metal O-rings to ensure high reliability under high temperature and pressure and alternating thermal conditions.
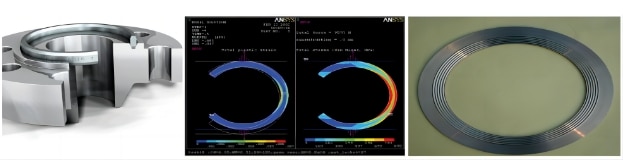
Packing Design
Molten salt control valves use special packing materials and a combination of various high-temperature sealing materials to address the issue of increased leakage pathways caused by the oxidation of conventional graphite packing at high temperatures.
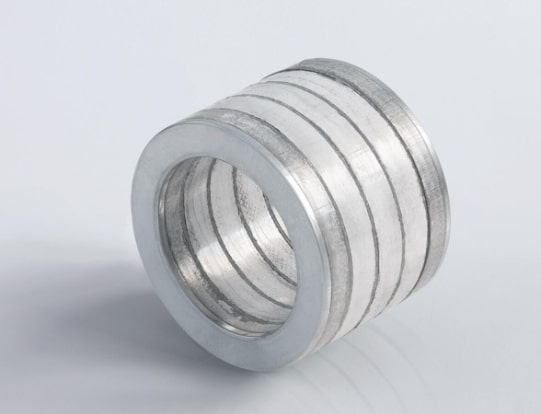
Bonnet Design
Extended bonnets or bellows-sealed bonnets are recommended. Due to the strong permeability of molten salt in its molten state, it is easy to leak from the packing area. Bellows-sealed valve stems are the most effective solution.
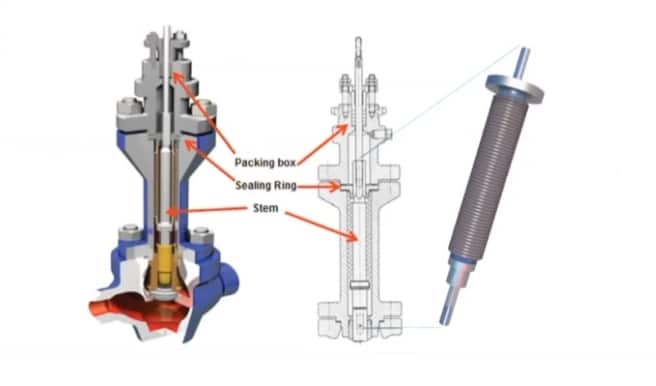
Whether with or without bellows, the bonnet must have heating trace to prevent molten salt crystallization.
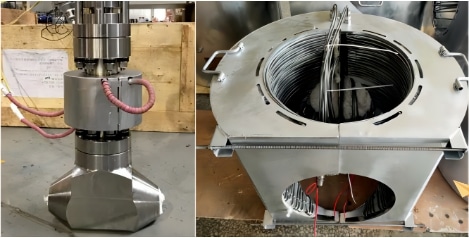
Angle Structure Design
The internal flow path should be smooth and without dead corners to reduce medium wear and deposition.
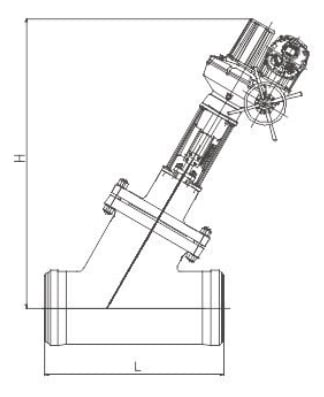
Welded Connection
This design adapts well to pressure and temperature changes, preventing external leakage at pipe connections.
Top Guide Design
Extended bonnets with guides are set to solve stability issues caused by the large slenderness ratio of the valve stem due to the extended bonnet.
High-Temperature Internal Parts Size Control
Accurate size gap control is required to ensure stable operation and prevent jamming of internal parts at high temperatures.
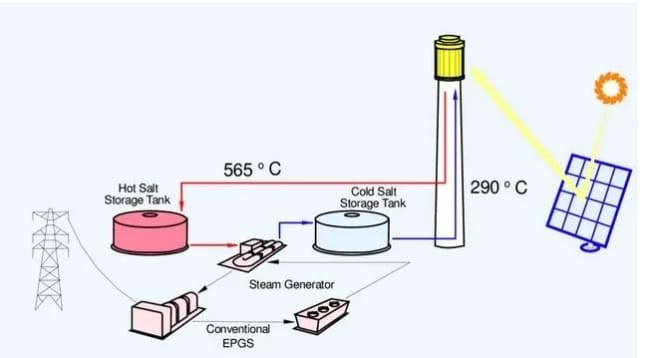
Conclusion
In recent years, THINKTANK’s molten salt control valves have been successfully working well in many CSP projects, accumulating rich design, manufacturing, and operational experience. If you have any needs or questions, please feel free to contact us for free consultation.