As the Product Marketing Director and a Senior Valve Engineer at THINKTANK, I’m pleased to share insights into the design of Pressure Safety Valves (PSVs). This guide is tailored for valve and instrument engineers, valve company executives, engineering purchase managers, and professionals in related fields.
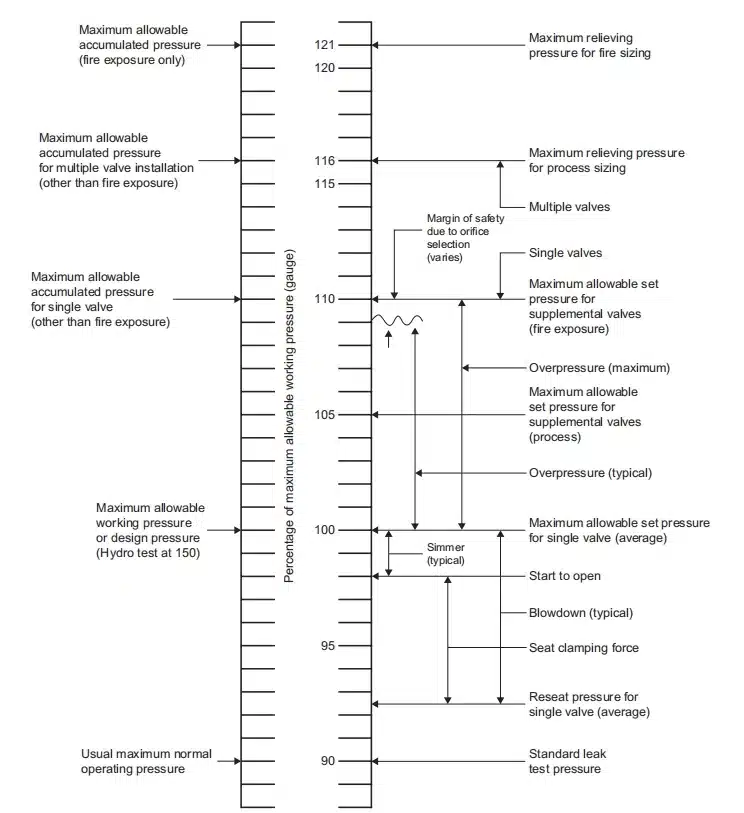
The design of a Pressure Safety Valve (PSV), also known as a Pressure Relief Valve (PRV), is a sophisticated process that incorporates various engineering principles to ensure the valve operates reliably under specific conditions. Here’s an overview of the key design aspects:
1. Purpose and Basic Design of PSV
A PSV is designed to protect equipment from excessive pressure. It automatically opens at a predetermined set pressure to release fluids (gas, steam, or liquid) and then closes when the pressure drops to a safe level.
The most common design for PSVs is the spring-loaded type, which uses a spring to maintain a force keeping the valve closed until the internal pressure exceeds the spring force.
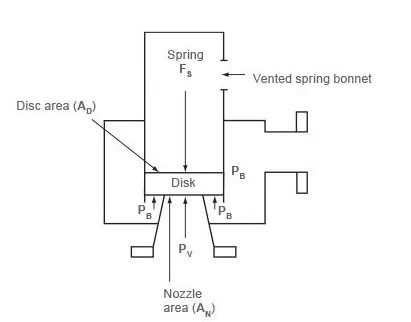
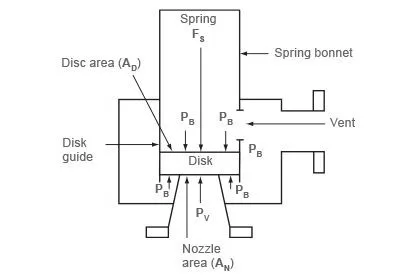
2. Set Pressure
The set pressure is the specific pressure at which the PSV is designed to open. It is determined based on the maximum allowable working pressure (MAWP) of the system the valve is protecting.
The set pressure is usually a percentage above the MAWP to allow for normal operating pressure fluctuations.
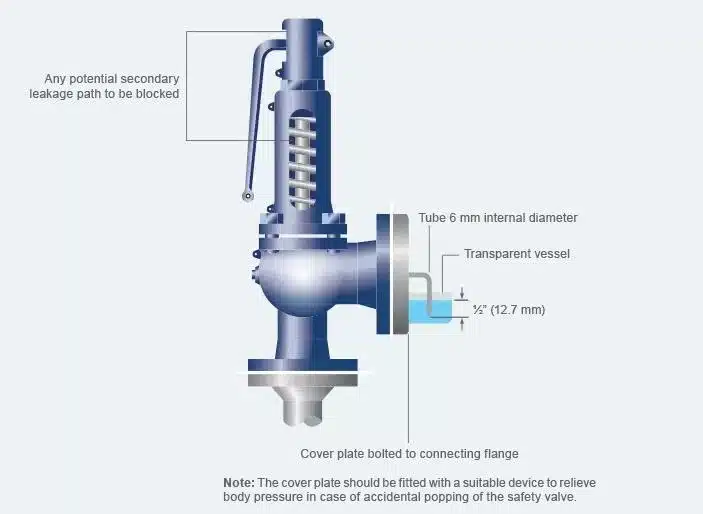
3. Valve Sizing
The size of the PSV is calculated based on the maximum expected flow rate of the fluid it needs to relieve, the properties of the fluid, and the differential pressure across the valve.
Standards such as API (American Petroleum Institute) provide guidelines for sizing calculations.
W, mass flow (kg/h)
V, volumetric fl ow (m 3 /h)
P, pressures (bars) (0.1 Mpa)
T, temperatures ( ° C)
A, areas (cm 2)
ρ, density (kg/m3 )
Z, gas compressibility factor R, constant of the gas (J/kgK)
K, nozzle flow coefficient of the valve M, molar weight of the gas (kg/kmol)
Indices: 1 = inlet; 2 = outlet
Gas flows
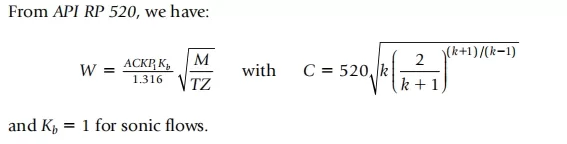
Liquid Flows
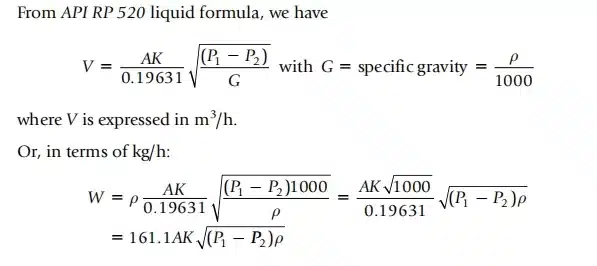
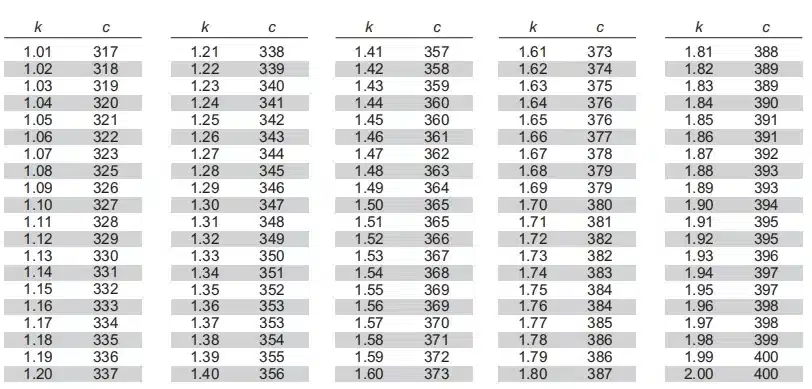
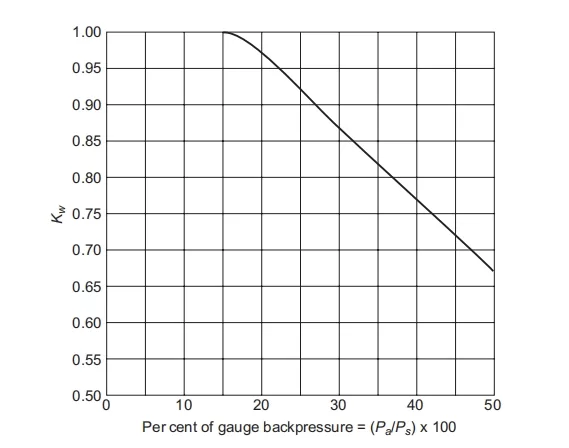
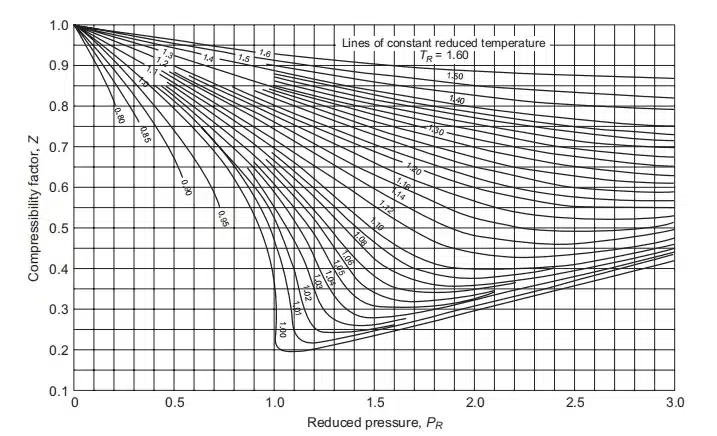
4. Components of PSV
Valve Body: The main structure that contains the internal components.
Disc: The part that seals against the seat to close the valve.
Seat: The surface against which the disc seals.
Spring: Applies a force to keep the valve closed until overpressure occurs.
Bonnet: Houses the adjusting mechanism and spring.
Lift Mechanism: Allows manual testing of the valve.
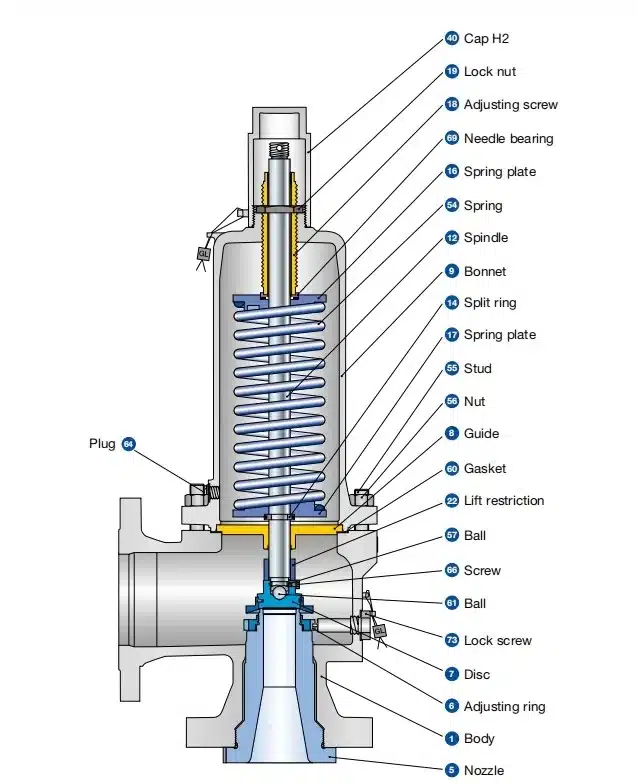
5. Materials
The material selection for PSVs is crucial and depends on the type of fluid, operating temperatures, and environmental conditions.
Common materials include carbon steel, stainless steel, and alloys for high-temperature or corrosive environments.
6. Overpressure and Blowdown:
Overpressure is the pressure increase over the set pressure at which the valve fully opens.
Blowdown is the pressure decrease required to reseat the valve after it has opened. It’s defined as a percentage of the set pressure.
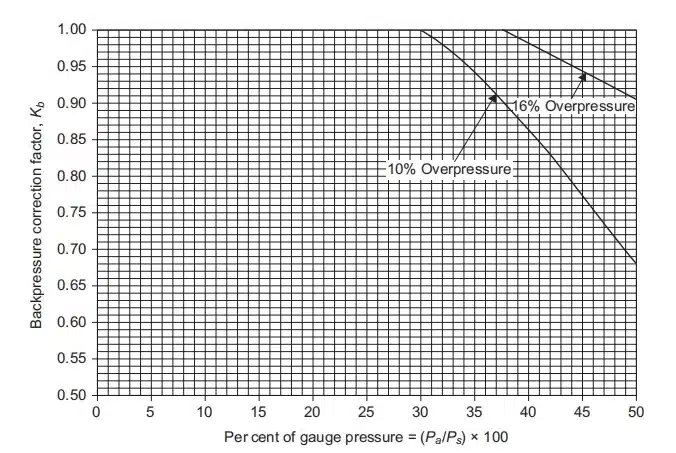
7. Types of PSVs
Conventional PSVs: Affected by back pressure, used in systems with relatively stable back pressure.

Balanced PSVs: Uses a bellows or piston to minimize the effect of back pressure.
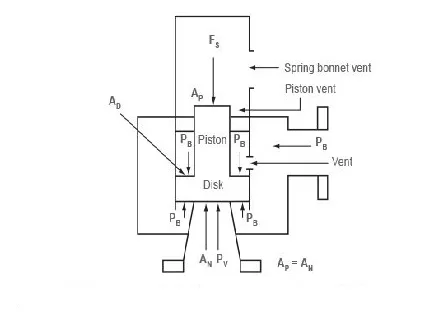
Pilot-Operated PSVs: Uses system pressure to aid in opening the valve.
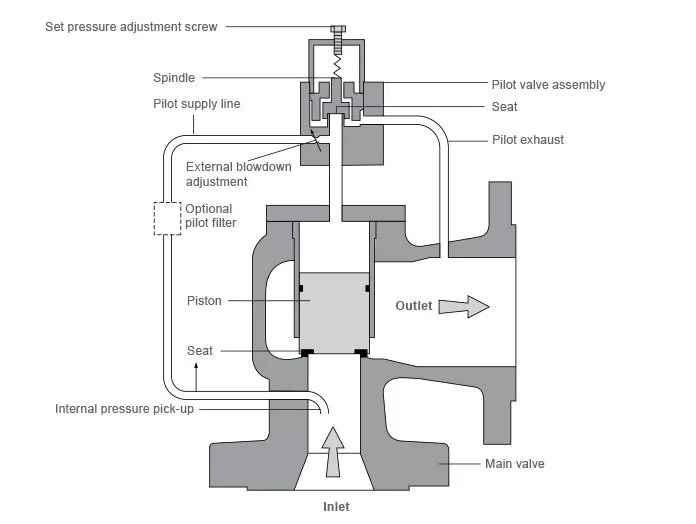
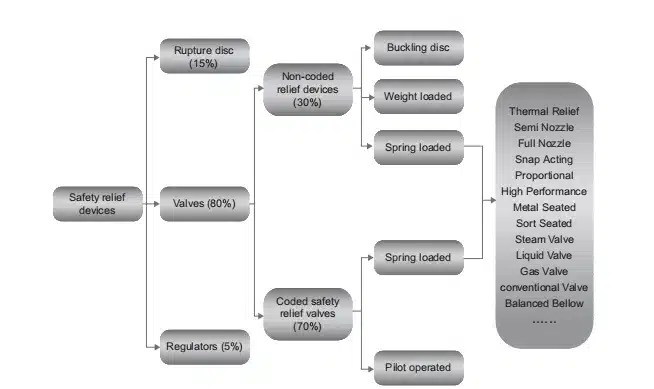
8. Design Codes and Standards
PSVs are designed according to international standards and codes, such as ASME (American Society of Mechanical Engineers), API, and ISO (International Organization for Standardization).
Organization | Publications |
American Petroleum InstituteWashingtonwww.api.org | API Recommended Practice 520 Part 1 – Sizing and SelectionAPI Recommended Practice 520 Part 2 – Installation API Recommended Practice 521 – Guide for PressureRelief and Depressurizing SystemsAPI Standard 526 – Flanged Steel Pressure Relief ValvesAPI Standard 527 – Seat Tightness of Pressure Relief ValvesAPI Recommended Practice 576 – Inspection of Pressure Relieving Devices |
ASME InternationalNew Yorkwww.asme.org | ASMEPTC 25 – Pressure Relief DevicesASME B16.34 – Valves – Flanged, Threaded and Welding EndASME B31.1 – Power PipingASME B31.3 – Process PipingASME B31.8 – Gas Transmission and DistributionPiping SystemsASME Boiler and Pressure Vessel CodeSection I – Power BoilersSection II – MaterialsSection III – Nuclear Power StationsSection IV – Heating boilersSection V – Non-destructive ExaminationSection VIII – Pressure VesselsSection IX – Welding and Brazing Qualifications |
ISO – International Organization for StandardizationGenevawww.iso.org | EN/ISO 4126 – Safety Devices for Protection Against Excessive PressurePart 1 – Safety ValvesPart 2 – Bursting Disc Safety DevicesPart 3 – Safety Valves and Bursting Disc Safety Devices in CombinationPart 4 – Pilot Operated Safety ValvesPart 5 – Controlled Safety Pressure Relief Systems Part 6 – Application, Selection and Installation ofBursting Disc Safety DevicesPart 7 – Common DataPart 9 – Application and Installation of Safety Devices Excluding Standalone Bursting Disc Safety DevicesISO 9001 – 2000 – Quality Management System |
Organization | Publications |
CEN – European Committee for StandardizationBrusselswww.cenorm.be | EN/ISO 4126 – Safety Devices for Protection Against Excessive PressurePart 1 – Safety ValvesPart 2 – Bursting Disc Safety DevicesPart 3 – Safety Valves and Bursting Disc Safety Devices in CombinationPart 4 – Pilot Operated Safety ValvesPart 5 – Controlled Safety Pressure Relief Systems Part 6 – Application, Selection and Installation ofBursting Disc Safety DevicesPart 7 – Common Data |
NACE – National Association of Corrosion EngineersHoustonwww.nace.org | NACE MR0175-2002 – Sulphide stress cracking resistant metallic materials for oilfield equipment NACE MR0175-2003 – Metals for sulphide stresscracking and stress corrosion cracking resistance in sour oilfield environmentsNACE MR0175/ISO15156-2003 Parts 1, 2 and 3– Petroleum and natural gas industries materials for use in H2S containing environments in oil and gas productionNACE MR0103-2003 – Materials resistant to sulphide stress cracking in corrosive petroleum environments |
National Board of Boiler and Pressure Vessel InspectionsColumbuswww.nationalboard.org | NB-18 – National Board Pressure Relief Device CertificationsNB-23 – National Board Inspection Code (NBIC) |
9. Testing and Certification
PSVs undergo rigorous testing for opening pressure, reseating pressure, and flow capacity. They are often certified by regulatory agencies or third-party organizations.
10. Safety and Environmental Considerations
Design also considers safety aspects, such as preventing leakages and ensuring safe discharge of the relieved fluid.
THINKTANK’s Approach to PSV Design
At THINKTANK, we prioritize precision and reliability in our PSV designs. Our approach involves:
1. Customization
We understand that one size does not fit all. Our team works closely with clients to develop tailored PSV solutions that meet specific industry requirements.
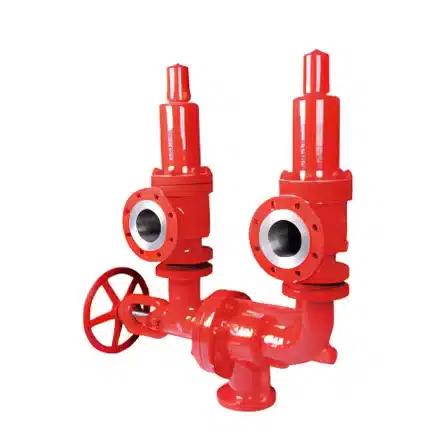
2. Innovation
Leveraging the latest in technology and materials, our PSVs are designed to deliver superior performance and reliability.
3. Quality Assurance
Each PSV undergoes rigorous testing to ensure it meets our high standards and those of the industry.
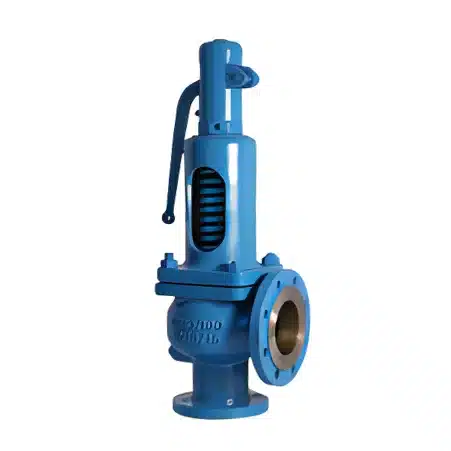
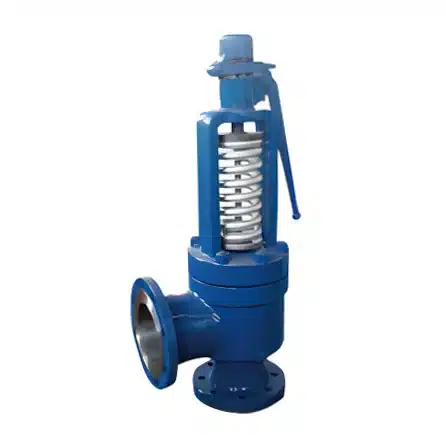
Concluding Thoughts
Thank you for taking the time to read this post. We at THINKTANK are committed to providing top-notch valve solutions and sharing our expertise in the field. Should you have any further questions or require detailed information, please feel free to reach out to us at [email protected]. We’re here to assist with all your valve-related needs and look forward to any opportunity to collaborate and contribute to your projects.