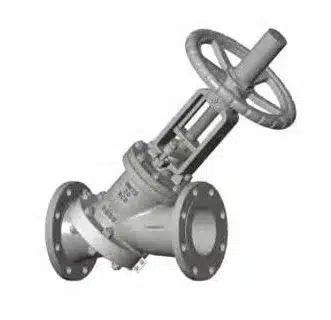
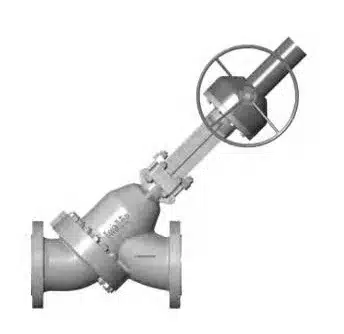
Angle Straight Slurry Valve Class 150LB
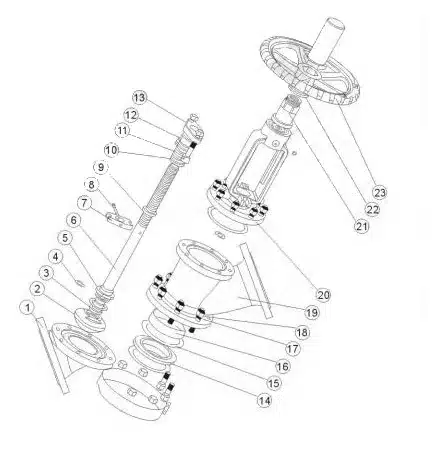
Technical Specification
- Design: ASMEB16.34 Class150
- Flanged Ends: ASME B16.5, GB/T9113.6
- Test and Inspection: API 598
Parts Material of Class 150LB Angle Straight Slurry Valves
1 | Left Side Valve Body | ASTM A216WCB |
2 | Disc | ASTMA105+STL |
3 | Split Ring | ASTM A276-420 |
4 | O-Ring | NBR |
5 | Disc Cover | ASTM A105 |
6 | Stem | ASTM A276-410 |
7 | Move-Proof Plate | Carbon Steel |
8 | Pin | ASTMA193-B7 |
9 | Packing Gasket | ASTMA276-410 |
10 | Packing | Graphite |
11 | Preloaded Screw Bolt | ASTM A193-B7 |
12 | Packing Cover | ASTM A276-410 |
13 | Gland | ASTM A216-WCB |
14 | Seat | ASTM A105+STL |
15 | Gasket | Graphite+Stainless Steel |
16 | Guard Plate | AISI 9260 |
17 | Stud | ASTM A193-B7 |
18 | Nut | ASTM A194-2H |
19 | Body | ASTMA216WCB |
20 | Bonnet | ASTMA216WCB |
21 | Yoke Nut | Copper Alloy |
22 | Bearing Gland | ASTM A105 |
23 | Driving Device | Assembly |
Angle Straight Slurry Valve Class 150LB Dimensions
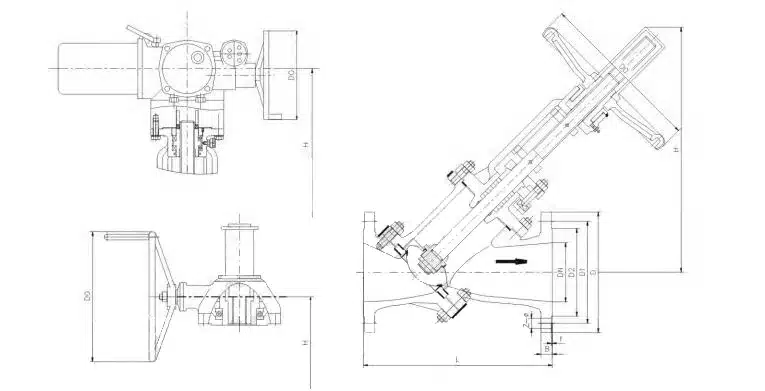
DN(mm) | NPS(in) | Driving Type | L | D | DI | D2 | B | Z-Φ | f | D0 | H |
50 | 2 | Manual | 230 | 150 | 120.5 | 92 | 16 | 4-20 | 2 | 250 | 307 |
80 | 3 | Manual | 310 | 190 | 152.5 | 127 | 19.5 | 4-20 | 2 | 250 | 386 |
100 | 4 | Manual | 350 | 230 | 190.5 | 157 | 24 | 8-20 | 2 | 250 | 448 |
125 | 5 | Manual | 400 | 255 | 216 | 186 | 24 | 8-22 | 2 | 320 | 519 |
150 | 6 | Manual | 480 | 280 | 214.5 | 216 | 25.5 | 8-22 | 2 | 360 | 600 |
200 | 8 | Handwheel Gear Operator | 600 | 345 | 298.5 | 270 | 29 | 8-22 | 2 | 450 | 795 |
250 | 10 | Handwheel Gear Operator | 730 | 405 | 362 | 324 | 30.5 | 12-26 | 2 | 600 | 880 |
300 | 12 | Handwheel Gear Operator | 850 | 485 | 432 | 381 | 32 | 12-26 | 2 | 600 | 935 |
350 | 14 | Handwheel Gear Operator | 980 | 535 | 476 | 413 | 35 | 12-30 | 2 | 600 | 1088 |
200 | 8 | Electric Actuator | 600 | 345 | 298.5 | 270 | 29 | 8-22 | 2 | 305 | 995 |
250 | 10 | Electric Actuator | 730 | 405 | 362 | 324 | 30.5 | 12-26 | 2 | 305 | 1045 |
300 | 12 | Electric Actuator | 850 | 485 | 432 | 381 | 32 | 12-26 | 2 | 305 | 1105 |
350 | 14 | Electric Actuator | 980 | 535 | 476 | 413 | 35 | 12-30 | 2 | 305 | 1250 |
Angle Straight Slurry Valve Class 300LB
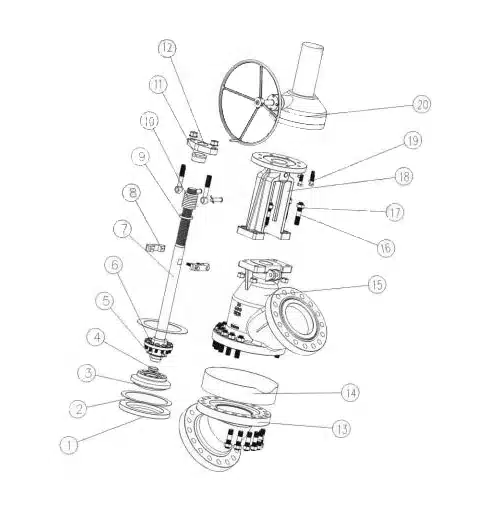
Technical Specification
- Design: ASMEB16.34 Class150
- Flanged Ends: ASME B16.5, GB/T9113.6
- Test and Inspection: API 598
Parts Material of Class 300LB Angle Straight Slurry Valves
1 | Seat | ASTM A105+STL |
2 | Gasket | Graphite+Stainless Steel |
3 | Disc | ASTM A105+STL |
4 | Beam Pad | AISI 5140 |
5 | Split Ring | Carbon Steel |
6 | Disc Cover | ASTM A105 |
7 | Stem | ASTM A276-410 |
8 | Move-Proof Plate | ASTM A105 |
9 | Packing Gasket | ASTM A276-410 |
10 | Packing | Graphite |
11 | Packing Cover | ASTM A276-410 |
12 | Gland | ASTM A216-WCB |
13 | Left Side Valve Body | ASTM A216-WCB |
14 | Guard Plate | AISI 9260 |
15 | Body | ASTM A216WCB |
16 | Stud | ASTM A193-B7 |
17 | Nut | ASTM A194-2H |
18 | Yoke | ASTM A216WCB |
19 | Bolt | ASTM A193-B7 |
20 | Driving Device | Assembly |
Angle Straight Slurry Valve Class 300LB Dimensions
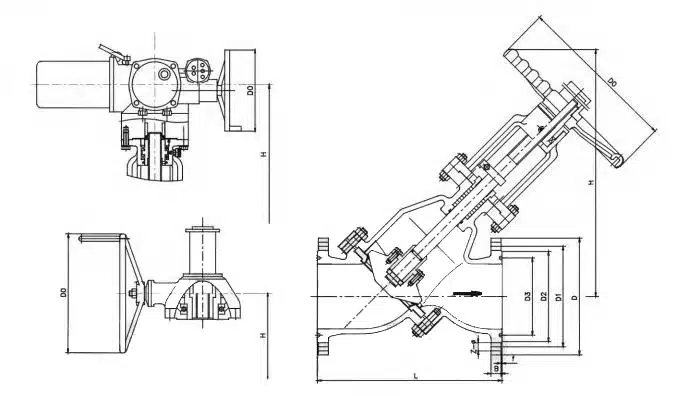
DN(mm) | NPS(in) | Driving Type | L | D | DI | D2 | D3 | B | Z-Φ | f | D0 | H |
50 | 2 | Manual | 372(361)* | 165 | 127 | 108 | 82.55 | 22.5 | 8-20 | 8 | 305 | 426 |
80 | 3 | Manual | 390 | 210 | 168.5 | 146 | 123.82 | 29 | 8-22 | 8 | 400 | 615 |
100 | 4 | Manual | 467(461)* | 255 | 200 | 175 | 149.22 | 32 | 8-22 | 8 | 500 | 730 |
125 | 5 | Manual | 546 | 280 | 235 | 210 | 180.98 | 35 | 8-22 | 8 | 500 | 810 |
150 | 6 | Handwheel Gear Operator | 619 | 320 | 270 | 241 | 211.12 | 37 | 12-22 | 8 | 550 | 1320 |
200 | 8 | Handwheel Gear Operator | 743(736)* | 380 | 330 | 302 | 269.88 | 41.5 | 12-26 | 8 | 600 | 1450 |
250 | 10 | Handwheel Gear Operator | 848(840* | 445 | 387.5 | 356 | 323.85 | 48 | 16-30 | 8 | 700 | 1430 |
150 | 6 | Electric Actuator | 619 | 320 | 270 | 241 | 211.12 | 37 | 12-22 | 8 | 550 | 1200 |
200 | 8 | Electric Actuator | 743(736)* | 380 | 330 | 302 | 269.88 | 41.5 | 12-26 | 8 | 305 | 1380 |
250 | 10 | Electric Actuator | 848(841)* | 445 | 387.5 | 356 | 323.85 | 48 | 16-30 | 8 | 457 | 1280 |
Note: If you have a specific dimension required, we can manufacture based on your information. Please do not hesitate to contact us.
What are Angle Straight Slurry Valves
Angle slurry valves are a type of slurry valve that are designed to handle abrasive and corrosive materials in industries such as mining, chemical processing, and wastewater treatment. These valves are named for their angled configuration, which allows for better flow control and reduced wear and tear on the valve stem and seat. They are typically made of materials that are highly resistant to wear and corrosion, such as stainless steel, ceramic, and special alloy steel. Angle slurry valves can have a range of different actuators, including manual, handwheel operation, pneumatic, electric, and hydraulic, depending on the specific requirements of the application.
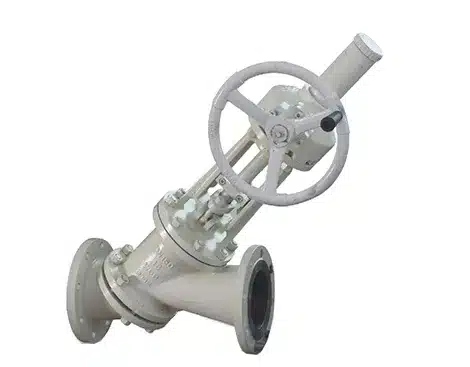
Technical Specification of Angle Slurry Valves
- Size: DN50 to DN500. 2″ to 20″
- Pressure Range: Class 150LB to 600LB
- Design Standard: BS1873, GB/T 12235, ASME B16.34
- Flanged Ends Standard: ASME B16.5, GB/T9113
- Body Material: WCB, WCC, UNS N08031, UNS N08020, CF8M etc.
- Working Temperature: -29 to +560℃
- Operation: Manual, Handwheel Operation, Pneumatic, Electric, and Hydraulic
- Seat Material: Alloy Steel, Metallic, Stellite
- Pressure test: GB/T13927, API598
- Face to Face: GB/T12221, API609
Application
Mining Industry, Smelter Mill, Mineral Industry, Alumina, Metallurgy, Chemical fertilizer, Pulp and Paper Industry
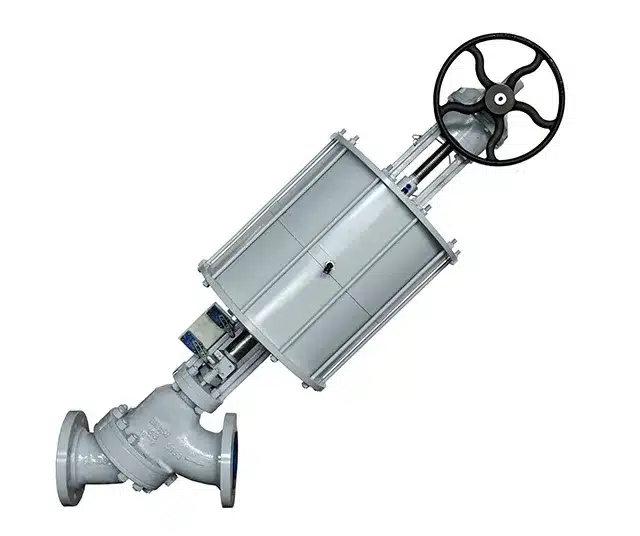
Types of Slurry Valves
Here are some of the most commonly used types of slurry valves:
- Pinch valves: These valves have a flexible elastomer sleeve that is pinched to regulate the flow of slurry. Pinch valves are highly efficient at minimizing abrasive wear and tear.
- Knife gate valves: These valves use a sharp-edged blade to cut through the slurry, allowing it to pass through the valve. Knife gate valves are typically used for applications where the slurry is thick and viscous.
- Diaphragm valves: These valves use a flexible diaphragm to regulate the flow of slurry. Diaphragm valves are easy to operate and maintain, making them a popular choice in a wide range of applications.
- Ball valves: These valves use a ball with a hole in the center to regulate the flow of slurry. Ball valves are highly efficient and offer excellent durability and corrosion resistance.
- Butterfly valves: These valves have a disc that is mounted on a shaft and rotates to regulate flow. Butterfly valves are highly versatile and can be used in a wide range of applications.
- Angle valves: These valves are designed to handle abrasive and corrosive materials in industries such as mining, chemical processing, and wastewater treatment. They are named for their angled configuration, which allows for better flow control and reduced wear and tear on the valve stem and seat.
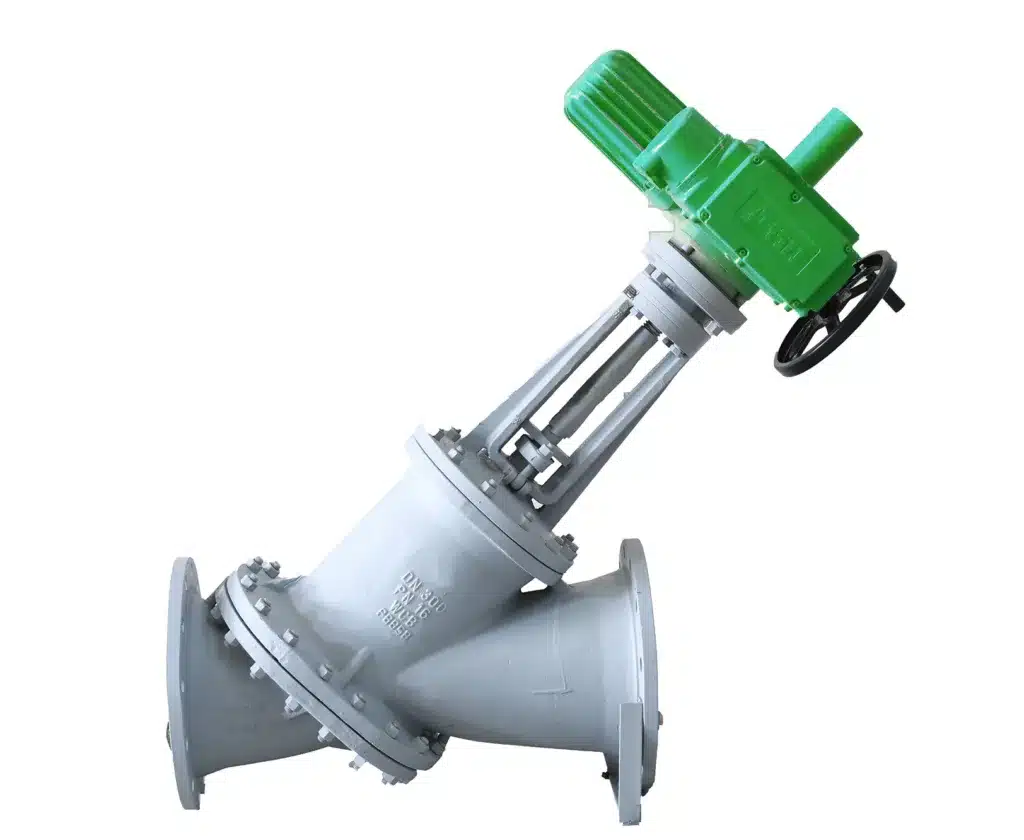
How Angle Straight Slurry Valves Work
Angle straight slurry valves work by controlling the flow of abrasive and corrosive materials like slurry. These valves are designed to be durable and resistant to wear and tear, which is important in applications where the slurry is highly abrasive.
When the valve is closed, a gate or disc is lowered into place across the path of the slurry, stopping the flow completely. When the valve is opened, the gate or disc is moved out of the way, allowing the slurry to flow through the valve.
In an angle straight slurry valve, the gate or disc is placed at an angle to the direction of flow. This angled configuration helps to reduce the amount of wear and tear on the valve stem and valve seat, which can prolong the lifespan of the valve. The angle also helps to reduce the turbulence in the flow of the slurry, making it easier to control the flow rate and reducing the risk of erosion within the valve body.
Angle straight slurry valves are available in a range of materials, from standard metals like cast iron and stainless steel to more specialized materials like ceramic, depending on the specific requirements of the application. They can also be operated using a range of different actuators, including manual, pneumatic, electric, and hydraulic, depending on the type angle valve and the level of automation required.
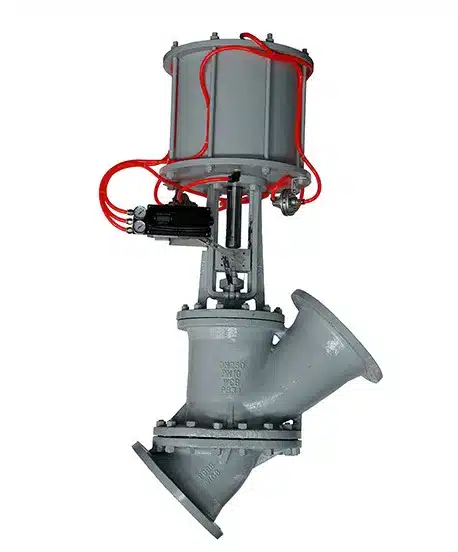
Benefits of Using Slurry Valves
Angle straight slurry valves offer several benefits in the handling of abrasives, corrosives, and thick slurries. By using these valves, you can achieve more precise control over your process flow in severe industrial applications such as mining, chemical processing, and wastewater treatment. Here are some of the key benefits of using an angle valve or straight slurry valves:
- Optimal Slurry Control: Angle straight slurry valves offer better flow control compared to other types of valves, which reduces the risk of slurry overflow, blockages or clogging. These types of slurry valves help to regulate the flow rate of the slurry, reducing turbulence and resistance in the pipework. This helps to minimize water consumption and material loss.
- Corrosion Resistance: Angle straight valves are designed to handle harsh and corrosive conditions. They are manufactured using highly resistant materials such as stainless steel, ceramic or polymer composites that do not easily corrode. This results in a longer lifespan, even in challenging and corrosive environments.
- Extended Lifespan: The angled configuration of the valve body and disc reduces the wear and tear on the stem and seat leading to the extended valve lifespan which can reduce costly downtime for valve replacements. The innovative design contributes to less valve maintenance over time, resulting in cost savings.
We, THINKTANK are a professional valve manufacturer of angle straight slurry valves and have expertise in offering solutions to challenging abrasive and corrosive processes. Our valves are made with high-grade materials to withstand the harsh conditions of heavy industry applications. Trust our professional and experienced team to help you optimize the performance of your slurry system.
How to Choose the Right Slurry Valve for Your Application
As industrial valve experts, we can provide useful insight into selecting the appropriate slurry valve for various applications. The key factors that influence the valve selection process include:
Industry Type
The industry in which the slurry valve will operate is a critical factor in selecting the appropriate valve type. Different industry applications have unique requirements for regulating slurry flows, and the type slurry valve selected must withstand the specific demands of that industry. For example, the valve used in mining operations may differ from the valve used in chemical processing industries.
Type of Slurry
The type of slurry being handled significantly influences valve selection. Abrasive and corrosive slurries require valves made of specialized materials such as ceramic or high-performance polymer composites compared to softer slurries, many applications which may use standard metal valves.
Pressure
Understanding the pressure of the slurry flow is critical when choosing the appropriate valve. The pressure determines whether the valve must be manual or actuated and the required pressure rating of the valve. Valve manufacturers supply detailed information about the maximum pressure ratings of their valves.
Temperature
Temperature influences the choice of valve materials. High temperatures can cause some materials to degrade and break down, thus, valves selected must be suitable for the temperature demands of the application.
Flow Rate
Flow rate is the velocity of fluid traveling through a system, and has a huge effect on valve selection. Large flows require high-capacity valves, and high pressure resistance while low flows require smaller valves.
Types of Slurry Valves:
Here is a table showcasing the various types of slurry valves, highlighting their pros and cons, along with use cases and applications where they work best.
Type of Valve | Pros | Cons | Best Use Cases |
Pinch Valves | Low resistance to flow, minimal wear and tear | Less precise than other types of valves | Mining, food industry |
Knife Gate Valves | Able to cut through thick slurry | Risk of jamming and blockage | Refineries, paper industry |
Diaphragm Valves | Easy maintenance, low cost | Limited pressure and temperature ranges | Water treatment, pharmaceuticals |
Ball Valves | High efficiency, durable, good corrosion resistance | Risk of contamination | Chemical processing, petrochemicals |
Butterfly Valves | Quick opening and closing, good for flow control | Susceptible to wear and leakage | Oil and gas, wastewater treatment |
Angle Straight Valves | Extended lifespan, better flow control, reduced wear | Higher cost than other valves | Chemical and mining industries |
Tips for Successful Slurry Valve Installation, Maintenance, and Troubleshooting
- Proper Valve Installation: Follow the manufacturer’s guidelines on installation, calibration, and temperature settings to ensure the valve operates optimally.
- Regular Valve Maintenance: Implement a regular maintenance schedule to keep the valve in good condition, including lubricating the valve regularly and replacing wear components when required.
- Accurate Valve Troubleshooting: Valve troubleshooting requires an intimate knowledge of the valve’s operating system and the slurry system. Refer to the manufacturer’s manual and appropriate experts if necessary.
Selecting the right slurry valve is critical for efficient and safe operation in a range of industrial applications. Consider the industry type, type of slurry, pressure, temperature, and flow rate to choose the appropriate valve type. Deliberate on the pros and cons of each type of valve with useful insights from the table provided, and ensure proper installation, maintenance, and troubleshooting of the valve. With appropriate valve selection and expert maintenance, efficient and safe slurry control is achievable.
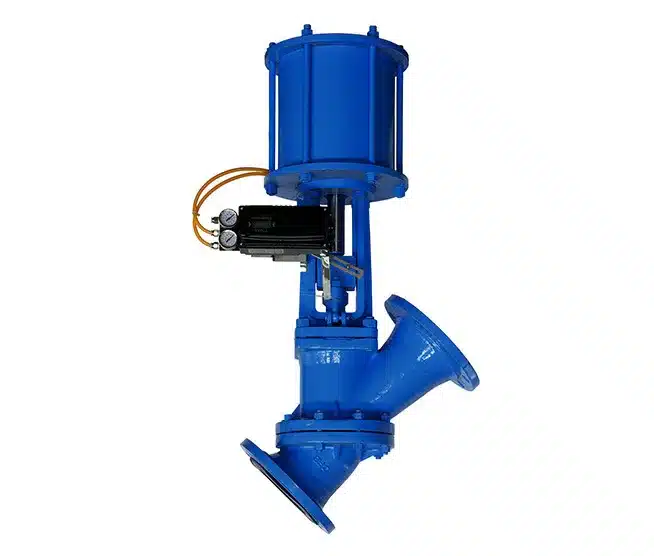
Advantage of THINKTANK’s Angle Straight Slurry Valves
As a valve expert, it is crucial to follow recommended procedures and guidelines to ensure optimal valve performance. The use of THINKTANK valves offers several advantages:
Durability
THINKTANK’s Slurry Valves incorporate natural rubber seats providing excellent longevity against abrasive slurries. These seats provide dual functionality, protecting the metal components within the valve while keeping a tight seal to prevent leakage.
Temperature and Pressure
THINKTANK advises selecting suitable Slurry Valves based on the type of slurry being transported, taking into account temperature and pressure requirements. The correct elastomers and materials must be selected for the specific process to ensure optimal valve function.
Full Opening
A full port, or pipeline opening, can reduce valve wear and tear on the slurry. THINKTANK valves have options available for a full port configuration, allowing for the maximum flow of slurry through the valve.
Positive Shut Off
THINKTANK’s valves offer a stem that drives the disc against the seat, providing positive shut-off capabilities. This is ideal for situations where the actuator or manual turning of the stem and plug of valve bodies to open and close the valve is required to prevent leaks.
Materials
Slurries can be highly abrasive and corrosive, and it is crucial to use the appropriate materials to ensure valve longevity in the application. THINKTANK valves incorporate hard-facing materials, such as cobalt-chromium alloys, for optimal wear resistance properties.
Draining
Slurries often need to be flushed out of a valve to prevent build-up within the valve and minimize maintenance downtimes. THINKTANK valves include a self-draining feature to ensure optimal function and minimal maintenance requirements.
In conclusion, following recommended procedures and guidelines for slurry applications, such as those provided by THINKTANK, can provide significant advantages in valve operation. Slurry valves must be properly selected based on factors such as temperature, pressure, and the type of slurry being transported. Moreover, incorporating features such as durable materials, positive shut-off, full opening, and self-draining capabilities can provide optimal valve performance, leading to increased efficiency, reduced downtime, and long-term cost savings.
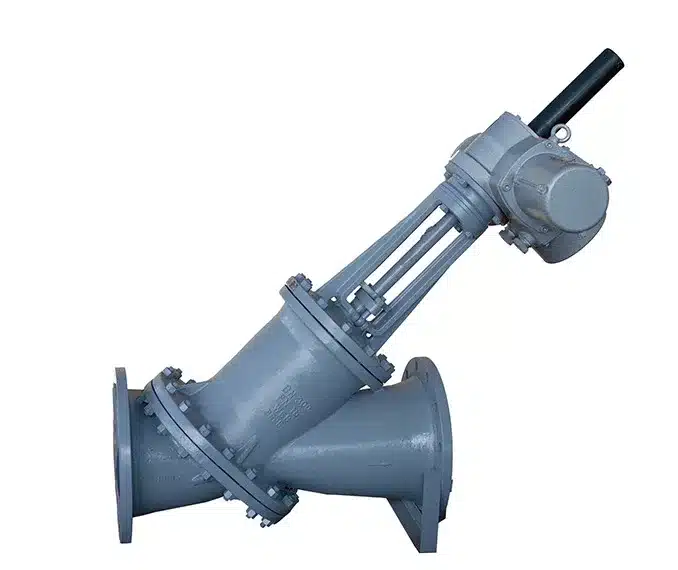
Final Thoughts
Through this post, now we know slurry valves are specifically designed to handle abrasive slurries that other valves may not be able to manage. These abrasive materials can grind against system equipment and wear out internal materials, eventually leading to the wearing down or breaking of valve seals, angle straight slurry valves can completely handle this condition without any worry. THINKTANK, a trusted valve supplier of Angle Slurry Valves, we manufacture high-performance angle slurry valves in a wide range of design types suitable for all applications.
If you are uncertain about which type of Angle Slurry Valve is suitable for your specific application or require further information, our team at THINKTANK is readily available to provide expert guidance and support. Feel free to contact us, and we will gladly discuss the available options with you.